The Metal Forging Market size was estimated at USD 92.70 billion in 2024 and expected to reach USD 102.44 billion in 2025, at a CAGR 10.02% to reach USD 164.48 billion by 2030.

Exploring the Dynamic Metal Forging Industry Through Contextual Overview of Technological Advances Supply Chain Challenges and Market Demand Drivers
Metal forging stands at the heart of modern manufacturing, underpinning critical sectors from aerospace and defense to automotive and industrial machinery. In an era defined by rapid technological progress and evolving customer demands, forging processes have transcended traditional boundaries to deliver components with unrivaled strength, precision, and reliability. This executive summary presents a concise yet comprehensive overview of the metal forging landscape, capturing pivotal trends, transformative shifts, and strategic insights essential for decision-makers.
The introduction lays the groundwork by framing metal forging not merely as a fabrication technique but as a strategic driver of innovation and competitive differentiation. Within this context, forging’s capacity to optimize material properties, reduce waste, and enhance component longevity aligns with global imperatives toward sustainability and resource efficiency. By synthesizing qualitative and quantitative research findings, this summary equips industry leaders with the context needed to navigate supply chain complexities, regulatory environments, and emerging market opportunities.
Understanding How Technological Disruptions Digital Transformation and Sustainable Practices Are Redefining Metal Forging Processes and Competitive Dynamics Industrywide
The metal forging sector is experiencing a wave of transformative shifts, propelled by the integration of digital technologies, advanced materials, and heightened sustainability imperatives. Digital twins, real-time monitoring systems, and predictive maintenance algorithms are redefining operational efficiency, enabling manufacturers to optimize die life and reduce downtime through data-driven decision-making. These innovations usher in a new paradigm where process variability is minimized and quality consistency reaches unprecedented levels.
Concurrently, the push toward lightweight alloys and high-performance materials is reshaping product design parameters. Aluminum and titanium components are increasingly favored in aerospace and automotive applications due to their high strength-to-weight ratios, compelling forging operations to adapt equipment capabilities and process controls. Moreover, environmental regulations and corporate sustainability goals are driving investments in energy-efficient furnaces and low-emission hydraulic systems, signaling a broader shift toward greener forging practices. Together, these dynamics underscore a fundamental realignment of competitive landscapes, where agility, technological adoption, and environmental stewardship converge.
Evaluating the Aggregate Consequences of Recent Trade Measures on Domestic Metal Forging Operations Supply Chains and Strategic Sourcing Decisions in the United States
The cumulative impact of recent United States tariffs implemented in 2025 has reverberated across domestic forging operations, supply chains, and sourcing strategies. Import levies on key materials such as aluminum, steel, and titanium have elevated input costs, compelling manufacturers to recalibrate their supplier networks and reevaluate contract terms. As a result, many forging shops have intensified collaboration with domestic mills, seeking to secure preferential pricing and mitigate tariff-induced cost inflation.
In parallel, end-use industries facing elevated component prices are scrutinizing product specifications and exploring design-for-forging initiatives to optimize material usage. While this trend enhances technical collaboration between forging suppliers and OEMs, it also heightens competitive pressures among fabricators. Mid-tier companies with flexible production lines have gained traction by offering rapid prototyping services and design consultancy aimed at minimizing waste. Ultimately, the tariff landscape has accelerated strategic localization efforts, reinforcing the importance of vertical integration and agile procurement strategies within the U.S. metal forging ecosystem.
Unveiling Market Segment Perspectives by Material Equipment Configuration Process Variation and Die Design to Illuminate Growth and Competitive Opportunities
A comprehensive analysis of market segments reveals nuanced opportunities across material types, equipment modalities, process variations, and die configurations. In the realm of material, carbon steel remains the backbone of heavy machinery components due to its exceptional load-bearing capacity, while stainless steel continues to expand within consumer and medical device applications for its corrosion resistance. Aluminum’s lightweight characteristics drive expansion in electric vehicle and aerospace sectors, and titanium’s high-temperature resilience caters to specialized engine and defense requirements.
Equipment type segmentation highlights the resurgence of drop hammers, especially mechanical variants, where high-impact energy meets precision hammering for large-scale forgings. Hydraulic presses have gained traction for crafting complex geometries and closed-die products, whereas three-roll and four-roll forging machines support seamless tubular forms and rotational symmetry. Process type delineations underscore a shift toward warm forging, offering a hybrid advantage of cold forging’s dimensional accuracy and hot forging’s formability, with warm extrusion processes unlocking refined grain structures and superior surface finish. Die type choices further dictate production outcomes; multi-stage closed dies enable progressive forming sequences, flashless die designs minimize material loss, and impression dies facilitate intricate profile creation with coining and trimming attachments.
This comprehensive research report categorizes the Metal Forging market into clearly defined segments, providing a detailed analysis of emerging trends and precise revenue forecasts to support strategic decision-making.
- Material
- Equipment Type
- Process Type
- Die Type
- End-Use Industry
Delineating Regional Market Characteristics Across the Americas Europe Middle East Africa and Asia Pacific to Uncover Growth Patterns and Strategic Positioning
Regionally, the Americas maintain a robust forging footprint driven by the aerospace hubs in the United States and Canada, where stringent certification standards and high-value contract opportunities sustain demand for critical rotating and structural components. Brazil and Mexico contribute through expansion in automotive manufacturing and heavy equipment, leveraging lower labor costs and favorable trade agreements.
In Europe, Middle East, and Africa, the forging market is spurred by a diverse mix of industries. Germany and Italy lead in precision engineering and high-end industrial machinery, whereas emerging Middle Eastern economies invest in oil and gas infrastructure requiring large open-die forgings. Meanwhile, African markets are gradually embracing forging for mining machinery applications, supported by regional partnerships and infrastructure growth initiatives. Across the Asia-Pacific region, China’s expansive steel industry underpins large-scale operations, while Japan and South Korea focus on advanced equipment and high-quality stainless steel and titanium forgings. Southeast Asian nations are increasingly attracting forging investments through competitive manufacturing ecosystems and special economic zones.
This comprehensive research report examines key regions that drive the evolution of the Metal Forging market, offering deep insights into regional trends, growth factors, and industry developments that are influencing market performance.
- Americas
- Europe, Middle East & Africa
- Asia-Pacific
Highlighting Key Industry Players Innovating Through Strategic Collaborations Technological Advancements and Operational Agility in the Metal Forging Market
Key players in the metal forging industry are distinguished by their commitment to technological innovation, strategic partnerships, and operational excellence. Major global forgers leverage integrated manufacturing networks, combining in-house material processing with advanced finishing capabilities to offer end-to-end solutions. Their investments in Industry 4.0 platforms facilitate real-time collaboration with suppliers and customers, enhancing responsiveness and quality assurance.
At the same time, mid-market specialists focus on niche segments, delivering bespoke forging solutions with rapid turnaround times. These companies often cultivate deep technical expertise in forging complex alloys or producing high-tolerance components, carving out competitive advantages through agility and customization. Collaborative ventures between forging houses and machine tool providers are also on the rise, enabling co-development of tailored equipment configurations that optimize energy consumption and die life. As competitive dynamics intensify, forgers that balance scale with specialization are poised to capture incremental market share by addressing specialized material requirements and stringent regulatory standards.
This comprehensive research report delivers an in-depth overview of the principal market players in the Metal Forging market, evaluating their market share, strategic initiatives, and competitive positioning to illuminate the factors shaping the competitive landscape.
- Bharat Forge Limited
- Thyssenkrupp AG
- Georg Fischer AG
- Alcoa Corporation
- Janesville Forge LLC
- Fagor Arrasate S. Coop.
- Siegfried Holding GmbH & Co. KG
- Carpenter Technology Corporation
- Shanghai Forging Co., Ltd.
- AIC Steel, Ltd.
Crafting Strategic Action Plans for Industry Leaders to Capitalize on Emerging Forging Technologies Trade Landscape Shifts and Evolving End User Expectations
Industry leaders must adopt a multi-pronged approach to harness emerging opportunities and mitigate evolving risks within the forging sector. First, investing in digital infrastructure that spans from shop-floor sensors to cloud-based analytics will be critical for optimizing throughput and reducing unplanned downtime. By establishing cross-functional teams that integrate data scientists with metallurgical experts, organizations can develop predictive models to fine-tune process parameters.
Second, forging firms should explore strategic partnerships along the value chain, collaborating with upstream material suppliers to secure preferential pricing and with downstream OEMs to co-create application-specific solutions. Such alliances can unlock design-for-forging initiatives that reduce material waste and accelerate time to market. Third, diversifying regional manufacturing footprints can mitigate trade uncertainties and tariff volatility, ensuring capacity flexibility and supply chain resilience. Finally, embedding sustainability imperatives into forging operations-through electrification of furnaces and closed-loop water systems-will meet customer expectations and adhere to tightening environmental regulations, reinforcing brand reputation and operational efficiency.
Articulating the Rigorous Research Methodology Employing Primary Stakeholder Interviews Secondary Data Synthesis and Data Triangulation for Insight Validity
The research methodology underpinning this analysis combines rigorous qualitative and quantitative techniques to ensure data integrity and actionable insights. Primary research comprised in-depth interviews with forging operations managers, procurement directors, and R&D specialists, capturing firsthand perspectives on process innovation, material selection, and regulatory compliance.
Secondary research leveraged publicly available industry publications, technical journals, patent filings, and tariff announcements to contextualize interview findings within broader market trends. Data triangulation was employed to cross-verify inputs across multiple sources, ensuring that narrative conclusions accurately reflect prevailing market dynamics. In addition, a structured framework for segment mapping was utilized to analyze the interactions between material types, equipment configurations, process variations, and regional factors. This robust approach guarantees that strategic recommendations are grounded in comprehensive evidence and industry-best practices.
Explore AI-driven insights for the Metal Forging market with ResearchAI on our online platform, providing deeper, data-backed market analysis.
Ask ResearchAI anything
World's First Innovative Al for Market Research
Synthesizing Critical Findings to Reinforce Strategic Imperatives Foster Innovation and Guide Decision Making in the Evolving Metal Forging Landscape
The synthesis of key findings reveals a metal forging industry at the confluence of technological innovation, trade policy evolution, and shifting end-market demands. Forging houses that successfully integrate digital capabilities and prioritize sustainable operations will shape the competitive frontier, delivering high-performance components with reduced environmental footprints. Tariff-driven strategic realignments underscore the importance of flexible procurement strategies and regional diversification to navigate cost pressures.
Furthermore, segmentation-driven insights demonstrate that material choice, equipment technology, process selection, and die design collectively define competitive positioning. Hence, forging firms must invest selectively in capabilities that align with their target end-use industries, whether that be lightweight aluminum parts for electric vehicles or high-strength titanium components for aerospace. Ultimately, informed decision-making predicated on this multifaceted analysis will empower industry stakeholders to spearhead innovation, bolster resilience, and capture emerging market opportunities.
This section provides a structured overview of the report, outlining key chapters and topics covered for easy reference in our Metal Forging market comprehensive research report.
- Preface
- Research Methodology
- Executive Summary
- Market Overview
- Market Dynamics
- Market Insights
- Cumulative Impact of United States Tariffs 2025
- Metal Forging Market, by Material
- Metal Forging Market, by Equipment Type
- Metal Forging Market, by Process Type
- Metal Forging Market, by Die Type
- Metal Forging Market, by End-Use Industry
- Americas Metal Forging Market
- Europe, Middle East & Africa Metal Forging Market
- Asia-Pacific Metal Forging Market
- Competitive Landscape
- ResearchAI
- ResearchStatistics
- ResearchContacts
- ResearchArticles
- Appendix
- List of Figures [Total: 28]
- List of Tables [Total: 1628 ]
Engage with Ketan Rohom to Access the Full Metal Forging Market Report Obtain Exclusive Insights and Empower Your Strategic Growth Decisions Today
Engage directly with Ketan Rohom, Associate Director of Sales & Marketing, to secure comprehensive access to the full metal forging market research report. By collaborating with Ketan, stakeholders will gain exclusive insights into industry dynamics, emerging technologies, and competitive strategies that can catalyze growth. His expertise in translating complex data into actionable narratives ensures that your organization can swiftly implement informed decisions and outpace competitors.
Partnering with Ketan also unlocks tailored briefing sessions, enabling teams to explore customized scenarios and identify high-impact opportunities within specific material segments, equipment configurations, or regional markets. Reach out today to schedule a consultation and transform empirical analysis into strategic advantage, driving innovation and resilience in your forging operations.
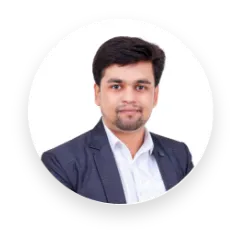
- How big is the Metal Forging Market?
- What is the Metal Forging Market growth?
- When do I get the report?
- In what format does this report get delivered to me?
- How long has 360iResearch been around?
- What if I have a question about your reports?
- Can I share this report with my team?
- Can I use your research in my presentation?