The Power Tools Market size was estimated at USD 40.58 billion in 2024 and expected to reach USD 42.35 billion in 2025, at a CAGR 4.42% to reach USD 52.60 billion by 2030.

Unveiling the Power Tools Market Landscape
The power tools industry has undergone a period of dynamic evolution, propelled by rapid technological innovation and shifting market demands. In recent years, advancements in battery technology, digital connectivity, and materials have converged to redefine the capabilities and expectations of both professional and residential users. This executive summary distills the critical developments, challenges, and opportunities that are shaping the global power tools arena as we move into 2025.
By examining the latest industry trends, regulatory pressures, and competitive dynamics, this overview equips decision-makers with a clear understanding of the forces at play. From established leaders to emerging disruptors, stakeholders across the value chain will find valuable insights that inform product development, investment strategies, and market positioning. In this introduction, we establish the context for subsequent sections that delve into transformative shifts, tariff implications, segmentation analysis, regional variations, competitive intelligence, strategic recommendations, and methodological rigor.
Emerging Forces Reshaping Power Tools Industry
The power tools sector is experiencing transformative shifts driven by converging technological and market forces. The integration of smart sensors and Internet of Things connectivity is enabling predictive maintenance, remote diagnostics, and enhanced user safety, fundamentally altering how tools are designed, deployed, and serviced. Such digital capabilities are fostering new business models, including subscription-based offerings and data-driven service contracts that extend value beyond the point of sale.
Simultaneously, advancements in battery chemistry and pack design are delivering unprecedented power density, reduced charge times, and longer runtimes. Manufacturers are racing to introduce high-voltage platforms that rival corded performance while maintaining the mobility benefits of cordless tools. Alongside energy efficiency, sustainability considerations are rising to prominence, with stakeholders prioritizing recyclable materials, reduced lifecycle emissions, and adherence to stringent environmental regulations.
Safety innovations, driven by regulatory bodies and end-user demand, are leading to ergonomic designs, active kickback protection, and automated shutoff features. These developments not only enhance operator well-being but also reduce liability for distributors and contractors. Together, these shifts underscore a broader trend toward smarter, greener, and safer power tools that cater to an increasingly sophisticated global customer base.
Assessing the Impact of US Tariffs in 2025
In 2025, cumulative tariffs imposed by the United States have significantly influenced the power tools supply chain and cost structures. These levies on key components and finished products imported from major manufacturing hubs have elevated landed costs, compelling original equipment manufacturers and distributors to reevaluate sourcing strategies. As a result, some players have sought alternative production locales in Southeast Asia and Latin America to mitigate tariff exposure and maintain margin integrity.
The ripple effects extend to pricing strategies, where increased input costs have been partially passed through to end-users in the form of higher retail prices. This dynamic has heightened sensitivity among price-conscious residential buyers and put pressure on professional contractors operating within tight project budgets. To preserve competitiveness, several firms have intensified their focus on value-added services, bundling extended warranties, on-site training, and consumables with core product offerings.
Beyond cost implications, tariffs have accelerated strategic alliances and joint ventures across borders, fostering collaborative manufacturing models that optimize duty structures and logistical efficiency. Companies that proactively engaged in tariff mitigation measures have strengthened their resilience, whereas those unable to adapt swiftly have faced supply delays and margin erosion. The ongoing tariff landscape underscores the importance of agile operations and diversified sourcing in sustaining long-term growth.
Deep Dive into Market Segmentation Dynamics
A nuanced understanding of product categories reveals distinct growth trajectories. Breaker tools have gained traction in infrastructure projects, while cutting and sawing solutions are favored for renovation work. Drilling instruments continue to see steady demand across both heavy construction and light-duty applications, and fastening devices remain indispensable for assembly operations. Each product group demands tailored innovation in power delivery, ergonomics, and durability to meet evolving performance expectations.
From a power source perspective, electric platforms dominate professional and residential segments thanks to their convenience and improving runtime. Gas-powered systems retain relevance in remote or high-intensity environments where battery life poses limitations, whereas hydraulic and pneumatic tools sustain niche roles in specialized industrial settings, such as shipbuilding and heavy machinery maintenance, where extreme force and reliability are paramount.
Application-based distinctions further refine market focus. Construction and demolition benefit from high-torque solutions, while metalworking and woodworking demand precision and minimal vibration. Shipbuilding imposes rigorous safety standards and corrosion resistance, driving bespoke tool configurations. Distribution channels have also diversified; brick-and-mortar retailers remain critical touchpoints for hands-on evaluation, even as e-commerce platforms expand reach and personalization capabilities. End-user segmentation underscores divergent priorities: commercial enterprises emphasize total cost of ownership and service support, industrial entities prioritize uptime and durability, and residential consumers seek ease of use and aesthetic appeal.
This comprehensive research report categorizes the Power Tools market into clearly defined segments, providing a detailed analysis of emerging trends and precise revenue forecasts to support strategic decision-making.
- Product
- Power Source
- Application
- Distribution Channel
- End-User
Regional Variations Driving Market Growth
Regional analysis highlights marked differences in growth drivers and market maturity. In the Americas, robust infrastructure spending and residential renovation trends underpin sustained demand. Contractors and DIY enthusiasts alike benefit from well-established distribution networks, although economic headwinds can introduce cyclical fluctuations. North America leads in the adoption of cordless technologies, while Latin America presents untapped potential in mining and energy sectors.
Europe, the Middle East & Africa exhibit a diverse landscape shaped by regulatory frameworks and varied economic conditions. Stringent emissions and noise regulations in Western Europe accelerate investments in electric and low-vibration models, whereas emerging economies in the Middle East leverage power tools for large-scale construction initiatives. In Africa, infrastructure development and urbanization create new entry points for cost-effective, durable equipment, albeit tempered by logistical challenges.
Asia-Pacific remains the fastest-growing region, driven by rapid urban expansion, industrial modernization, and a burgeoning manufacturing base. China and India contribute substantially to global consumption, supported by competitive local production and an expanding e-commerce ecosystem. Southeast Asian markets are also gaining prominence as manufacturing hubs and distribution centers, reflecting a broader shift toward supply chain diversification.
This comprehensive research report examines key regions that drive the evolution of the Power Tools market, offering deep insights into regional trends, growth factors, and industry developments that are influencing market performance.
- Americas
- Europe, Middle East & Africa
- Asia-Pacific
Competitive Landscape and Leading Innovators
The competitive landscape is marked by a blend of legacy players and agile newcomers. Leading power tool manufacturers have doubled down on platform consolidation, creating interoperable battery systems that appeal to professional users invested in ecosystem compatibility. Strategic acquisitions have bolstered portfolios, enabling incumbents to expand their reach into adjacent categories and specialized segments.
Innovation is a critical differentiator: companies investing heavily in research and development are introducing tools with predictive maintenance algorithms, advanced brushless motors, and integrated safety sensors. Partnerships with technology firms and academic institutions facilitate the rapid prototyping and validation of novel materials and electronic architectures. Meanwhile, regionally focused players leverage local supply chains and distribution partnerships to deliver cost-competitive offerings tailored to specific market requirements.
Market entrants are carving niches by emphasizing sustainability credentials, such as low-carbon manufacturing processes and take-back recycling programs. Others are capitalizing on digital engagement, offering seamless online configurators and virtual demonstrations that streamline the buying experience. Overall, the sector’s leading innovators balance technological prowess with operational excellence to maintain their positions in a fiercely contested market.
This comprehensive research report delivers an in-depth overview of the principal market players in the Power Tools market, evaluating their market share, strategic initiatives, and competitive positioning to illuminate the factors shaping the competitive landscape.
- Apex Tool Group, LLC
- Atlas Copco AB
- Dynabrade, Inc.
- Emerson Electric Co.
- Enerpac Tool Group
- Fortive Corporation
- Hilti Corporation
- Husqvarna Group
- IDEAL INDUSTRIES, INC.
- Illinois Tool Works Inc.
- Ingersoll-Rand Inc.
- Klein Tools, Inc
- KNIPEX-WERK C. Gustav Putsch KG
- Koki Holdings Co., Ltd.
- Makita Corporation
- OLFA Corporation
- Panasonic Corporation
- Positec Tool Corporation
- Robert Bosch GmbH
- Sandvik AB
- SNA Europe Group
- Snap-on Incorporated
- Stanley Black & Decker, Inc.
- Taizhou Dingba Power Tools Co., Ltd
- Techtronic Industries Company Limited
- United Pacific Industries Ltd.
- Uryu Seisaku, Ltd.
- WUYI CHUANGFENG TOOLS MANUFACTURE CO., LTD.
- Yamabiko Corporation
Strategic Recommendations for Market Leadership
Industry leaders should prioritize investments in next-generation battery systems to stay ahead of cordless adoption curves. By accelerating research into fast-charging chemistry and energy-dense cells, companies can deliver cord-replacing performance while enhancing user productivity. Equally important is the development of digital platforms that aggregate tool usage data, enabling tailored maintenance services and fostering recurring revenue streams.
Supply chain resilience must be fortified through geographic diversification and strategic inventory planning. Establishing production partnerships in low-tariff regions and implementing predictive demand analytics will mitigate the risk of cost volatility and component shortages. Enhancing sustainability practices across manufacturing and packaging not only meets regulatory expectations but also resonates with environmentally conscious end-users.
Finally, strengthening omnichannel capabilities is essential. Integrating seamless customer journeys from online research to in-store pickup enhances brand loyalty and upsell potential. Training programs and technical support services should be expanded to ensure professional contractors can fully leverage advanced tool features. By aligning product innovation with customer-centric service models, industry leaders can secure lasting competitive advantage.
Robust Research Methodology for Reliable Insights
This report’s findings derive from a comprehensive research methodology that triangulates primary and secondary data sources to ensure robustness and reliability. Primary research included in-depth interviews with industry stakeholders spanning manufacturers, distributors, contractors, and end-users. Quantitative surveys captured usage patterns, purchasing criteria, and satisfaction drivers across multiple regions and segments.
Secondary research encompassed analysis of corporate filings, trade association publications, regulatory documents, and reputable news outlets. Historical trend analysis and case study examinations provided context for recent developments, while comparative benchmarking against adjacent industries enriched the framework for evaluating best practices.
Data validation processes involved cross-referencing interview feedback with market intelligence databases and third-party analytics. Quality checks and iterative hypothesis testing were conducted to refine insights, ensuring that conclusions accurately reflect market realities. The result is a multi-faceted perspective that balances depth and breadth across product categories, power sources, applications, distribution channels, and end-user segments.
Explore AI-driven insights for the Power Tools market with ResearchAI on our online platform, providing deeper, data-backed market analysis.
Ask ResearchAI anything
World's First Innovative Al for Market Research
Concluding Perspectives on Market Evolution
The power tools market in 2025 stands at the intersection of rapid technological progress and evolving market dynamics. As innovation accelerates, companies that adeptly integrate digital connectivity, sustainability initiatives, and ergonomic design will command leadership positions. Meanwhile, geopolitical influences such as tariffs underscore the imperative for agile operations and diversified sourcing.
Granular segmentation analysis and regional insights highlight where growth opportunities truly lie-whether in mature markets optimizing premium cordless platforms or emerging economies prioritizing cost-effective solutions. Competitive intelligence reveals that technological differentiation, operational resilience, and customer-centric services are the hallmarks of market outperformance.
This executive summary distills these critical dimensions to guide strategic decision-making. By heeding the insights and recommendations presented, stakeholders can navigate complexity, capitalize on emerging trends, and chart a path toward sustained market success.
This section provides a structured overview of the report, outlining key chapters and topics covered for easy reference in our Power Tools market comprehensive research report.
- Preface
- Research Methodology
- Executive Summary
- Market Overview
- Market Dynamics
- Market Insights
- Cumulative Impact of United States Tariffs 2025
- Power Tools Market, by Product
- Power Tools Market, by Power Source
- Power Tools Market, by Application
- Power Tools Market, by Distribution Channel
- Power Tools Market, by End-User
- Americas Power Tools Market
- Europe, Middle East & Africa Power Tools Market
- Asia-Pacific Power Tools Market
- Competitive Landscape
- ResearchAI
- ResearchStatistics
- ResearchContacts
- ResearchArticles
- Appendix
- List of Figures [Total: 26]
- List of Tables [Total: 239 ]
Connect with Ketan Rohom to Secure Full Report
If you are ready to gain a competitive edge by accessing in-depth market intelligence and actionable insights on the power tools sector, reach out to Ketan Rohom, Associate Director of Sales & Marketing. Ketan can guide you through the full report’s comprehensive findings, offering tailored support to help your organization capitalize on emerging opportunities and navigate industry challenges with confidence. Connect today to unlock the strategic knowledge necessary for driving growth, optimizing investments, and staying ahead of the curve in the evolving power tools marketplace.
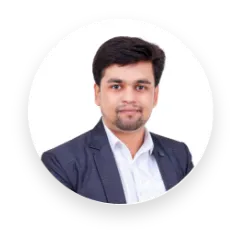
- How big is the Power Tools Market?
- What is the Power Tools Market growth?
- When do I get the report?
- In what format does this report get delivered to me?
- How long has 360iResearch been around?
- What if I have a question about your reports?
- Can I share this report with my team?
- Can I use your research in my presentation?