[189 Pages Report] The Aluminum Welding Wires Market size was estimated at USD 9.47 billion in 2023 and expected to reach USD 10.46 billion in 2024, at a CAGR 10.82% to reach USD 19.46 billion by 2030.
Aluminum welding wires are thin, flexible rods made predominantly from aluminum alloys. They serve as a consumable material in the welding process, where they help join aluminum parts together by melting and fusing them. The welding wires are often used in various industries, including automotive, aerospace, construction, and manufacturing, due to their ability to create strong, corrosion-resistant joints. Aluminum welding wires are increasingly used in the automotive and aerospace sectors due to aluminum's lightweight and strong properties. With ongoing infrastructure projects worldwide, there's a rising need for welding materials. Aluminum's properties make it suitable for use in bridges, buildings, and other large-scale construction efforts. However, welding aluminum requires specific skills and expertise, limiting its use to trained professionals. Furthermore, performance issues, such as high thermal conductivity and the formation of an oxide layer when exposed to air, can reduce the reliability of aluminum welding wires. Future developments in welding technologies could simplify the aluminum welding process, making it more efficient and accessible. Increased focus on recycling and sustainability could enhance aluminum's attractiveness as a material, boosting demand for welding wires.
In the Americas region, particularly in the United States and Canada, the demand for aluminum welding wires is robust due to a strong manufacturing base, extensive infrastructure projects, and significant advancements in the automotive sector. The focus on lighter materials to improve fuel efficiency drives this market further. The region also experiences heightened demand from the aerospace sector, given its substantial number of aerospace manufacturers. The European Union represents a diversified market where high standards for automotive and aerospace industries support steady demand for aluminum welding wires. Countries such as Germany, France, and Italy are notable economies due to their strong manufacturing sectors and stringent regulations that favor lightweight and eco-friendly materials. In the Middle East, the construction and oil & gas sectors serve as primary consumers of aluminum welding wires. Countries such as UAE and Saudi Arabia are investing heavily in infrastructure and industrial projects, boosting market growth. APAC's strategic position in the manufacturing industry and rapid urbanization make it a substantial landscape for aluminum welding wires. The region's initiatives in expanding its electric vehicle sector and large-scale infrastructure projects influence market dynamics. Government policies support industrial growth and further propel market expansion.
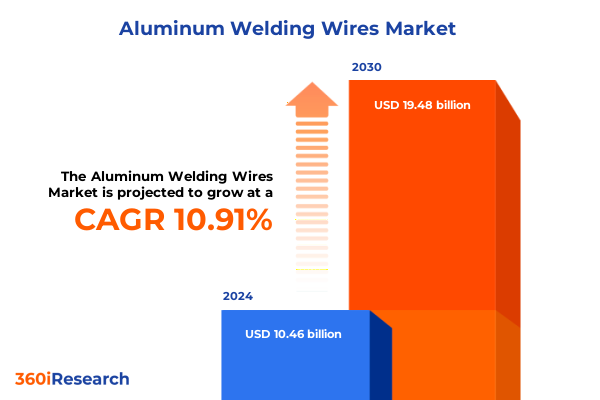
The market dynamics represent an ever-changing landscape of the Aluminum Welding Wires Market by providing actionable insights into factors, including supply and demand levels. Accounting for these factors helps design strategies, make investments, and formulate developments to capitalize on future opportunities. In addition, these factors assist in avoiding potential pitfalls related to political, geographical, technical, social, and economic conditions, highlighting consumer behaviors and influencing manufacturing costs and purchasing decisions.
- Market Drivers
- Growing demand for lightweight automobiles and aerospace components
- Rising private and public construction industry
- Increasing oil and gas production units across economies
- Market Restraints
- Technical limitations and product performance Cconcerns
- Market Opportunities
- Growing expansion of aluminum welding production facilities
- Government investments in renewable energy sector
- Market Challenges
- Complexities associated with aluminum welding wire manufacturing process
Technology: Wide applicability of Al-Si (aluminum-silicon) alloy welding wire owing to its corrosion resistance and thermal stability
Al-Si (aluminum-silicon) alloy welding wire consists primarily of aluminum with silicon additions. This technology is typically used for welding applications that require good mechanical properties and a smooth finish. Automotive and aerospace industries often prefer Al-Si alloy welding wire due to its excellent corrosion resistance and good thermal stability. It provides good weldability and less cracking tendency, making it suitable for complex geometries. Aluminum magnesium alloy welding wire contains magnesium as the primary alloying element. These wires are well-regarded for their strength and marine corrosion resistance. It is commonly used in the shipbuilding and marine industry due to its high strength and excellent corrosion resistance in saltwater environments. The technology also offers good ductility, making it easier to form and weld even in difficult positions, making it suitable for marine structures, pipelines, storage tanks, and other high-strength aluminum applications. Pure aluminum welding wire primarily consists of 99.0% or higher aluminum content. It is typically used for welding applications that require a clean, high-quality weld with minimal contamination. It is utilized in industries requiring high-purity welds, such as food and beverage, pharmaceuticals, and certain electrical applications. It is used for the welding of pure aluminum components, electrical busbars, and ultra-high purity equipment.
End-Use Industry: Emerging need for aluminum welding wires owing to the industry’s push towards lighter, more fuel-efficient vehicles
The aerospace industry heavily relies on aluminum welding wires for the construction and repair of aircraft. Aluminum is favored due to its high strength-to-weight ratio and resistance to corrosion. Components such as fuselage panels, wings, and various structural parts are welded using aluminum wires to ensure durability and performance. In the automotive sector, aluminum welding wires are used to join parts of a vehicle's body, engine components, and other structural elements. Aluminum's light weight helps improve fuel efficiency, making it a preferred material in this industry. The shift towards electric vehicles (EVs) further boosts the demand for aluminum welding due to the need for lightweight and conductive materials. Aluminum welding wires are used in the construction industry for building frameworks, roofing, and various structural applications. Aluminum's resistance to corrosion makes it a popular choice for outdoor structures and buildings in coastal or industrial environments. In the manufacturing industry, aluminum welding wires are utilized for fabricating machinery, equipment, and consumer goods. The versatility and adaptability of aluminum make it ideal for a wide range of products, from household items to industrial machinery. The marine industry uses aluminum welding wires extensively due to aluminum's corrosion resistance, especially in saltwater environments. Applications include shipbuilding, boat manufacturing, and offshore structures. Aluminum helps in reducing the weight of marine vessels, thereby enhancing fuel efficiency and performance.
The market disruption analysis delves into the core elements associated with market-influencing changes, including breakthrough technological advancements that introduce novel features, integration capabilities, regulatory shifts that could drive or restrain market growth, and the emergence of innovative market players challenging traditional paradigms. This analysis facilitates a competitive advantage by preparing players in the Aluminum Welding Wires Market to pre-emptively adapt to these market-influencing changes, enhances risk management by early identification of threats, informs calculated investment decisions, and drives innovation toward areas with the highest demand in the Aluminum Welding Wires Market.
The porter's five forces analysis offers a simple and powerful tool for understanding, identifying, and analyzing the position, situation, and power of the businesses in the Aluminum Welding Wires Market. This model is helpful for companies to understand the strength of their current competitive position and the position they are considering repositioning into. With a clear understanding of where power lies, businesses can take advantage of a situation of strength, improve weaknesses, and avoid taking wrong steps. The tool identifies whether new products, services, or companies have the potential to be profitable. In addition, it can be very informative when used to understand the balance of power in exceptional use cases.
The value chain of the Aluminum Welding Wires Market encompasses all intermediate value addition activities, including raw materials used, product inception, and final delivery, aiding in identifying competitive advantages and improvement areas. Critical path analysis of the <> market identifies task sequences crucial for timely project completion, aiding resource allocation and bottleneck identification. Value chain and critical path analysis methods optimize efficiency, improve quality, enhance competitiveness, and increase profitability. Value chain analysis targets production inefficiencies, and critical path analysis ensures project timeliness. These analyses facilitate businesses in making informed decisions, responding to market demands swiftly, and achieving sustainable growth by optimizing operations and maximizing resource utilization.
The pricing analysis comprehensively evaluates how a product or service is priced within the Aluminum Welding Wires Market. This evaluation encompasses various factors that impact the price of a product, including production costs, competition, demand, customer value perception, and changing margins. An essential aspect of this analysis is understanding price elasticity, which measures how sensitive the market for a product is to its price change. It provides insight into competitive pricing strategies, enabling businesses to position their products advantageously in the Aluminum Welding Wires Market.
The technology analysis involves evaluating the current and emerging technologies relevant to a specific industry or market. This analysis includes breakthrough trends across the value chain that directly define the future course of long-term profitability and overall advancement in the Aluminum Welding Wires Market.
The patent analysis involves evaluating patent filing trends, assessing patent ownership, analyzing the legal status and compliance, and collecting competitive intelligence from patents within the Aluminum Welding Wires Market and its parent industry. Analyzing the ownership of patents, assessing their legal status, and interpreting the patents to gather insights into competitors' technology strategies assist businesses in strategizing and optimizing product positioning and investment decisions.
The trade analysis of the Aluminum Welding Wires Market explores the complex interplay of import and export activities, emphasizing the critical role played by key trading nations. This analysis identifies geographical discrepancies in trade flows, offering a deep insight into regional disparities to identify geographic areas suitable for market expansion. A detailed analysis of the regulatory landscape focuses on tariffs, taxes, and customs procedures that significantly determine international trade flows. This analysis is crucial for understanding the overarching legal framework that businesses must navigate.
The regulatory framework analysis for the Aluminum Welding Wires Market is essential for ensuring legal compliance, managing risks, shaping business strategies, fostering innovation, protecting consumers, accessing markets, maintaining reputation, and managing stakeholder relations. Regulatory frameworks shape business strategies and expansion initiatives, guiding informed decision-making processes. Furthermore, this analysis uncovers avenues for innovation within existing regulations or by advocating for regulatory changes to foster innovation.
The FPNV positioning matrix is essential in evaluating the market positioning of the vendors in the Aluminum Welding Wires Market. This matrix offers a comprehensive assessment of vendors, examining critical metrics related to business strategy and product satisfaction. This in-depth assessment empowers users to make well-informed decisions aligned with their requirements. Based on the evaluation, the vendors are then categorized into four distinct quadrants representing varying levels of success, namely Forefront (F), Pathfinder (P), Niche (N), or Vital (V).
The market share analysis is a comprehensive tool that provides an insightful and in-depth assessment of the current state of vendors in the Aluminum Welding Wires Market. By meticulously comparing and analyzing vendor contributions, companies are offered a greater understanding of their performance and the challenges they face when competing for market share. These contributions include overall revenue, customer base, and other vital metrics. Additionally, this analysis provides valuable insights into the competitive nature of the sector, including factors such as accumulation, fragmentation dominance, and amalgamation traits observed over the base year period studied. With these illustrative details, vendors can make more informed decisions and devise effective strategies to gain a competitive edge in the market.
Alfiniti Inc. Acquires Alabama Tube Corporation to Boost Production and Expand Market Reach in Aluminum Welding Products
Alfiniti Inc. has acquired Alabama Tube Corporation, strengthens Alfiniti's market position and expands its production capabilities in aluminum welding products. By incorporating Alabama Tube Corporation, Alfiniti aims to enhance its product offerings and meet the growing demand for aluminum welded tubes across various industries. [Published On: 2024-05-07]
AlcoTec Introduces Enhanced 4043 and 4047 Aluminum Welding Wires for Improved Performance and Versatility
AlcoTec, an ESAB brand, has upgraded its 4043 and 4047 aluminum MIG welding wire products using a proprietary and patented surface treatment technology. This enhancement leads to smoother feeding performance and fewer tangles. Widely used in the manufacture of EV battery trays, bumper assemblies, bicycles, and general fabrication. [Published On: 2024-04-25]
Ador Welding and Hindalco Join Forces to Boost Aluminum Welding Wire Quality and Performance
Ador Welding and Hindalco entered into a strategic partnership aimed at enhancing welding performance through the development of superior aluminum welding wires. This collaboration leverages Ador Welding's expertise in welding equipment and consumables alongside Hindalco's leadership in aluminum production. The partnership is expected to result in high-quality welding wires that offer improved performance, catering to the evolving demands of various industries. [Published On: 2024-03-29]
The strategic analysis is essential for organizations seeking a solid foothold in the global marketplace. Companies are better positioned to make informed decisions that align with their long-term aspirations by thoroughly evaluating their current standing in the Aluminum Welding Wires Market. This critical assessment involves a thorough analysis of the organization’s resources, capabilities, and overall performance to identify its core strengths and areas for improvement.
The report delves into recent significant developments in the Aluminum Welding Wires Market, highlighting leading vendors and their innovative profiles. These include ChangZhou Changjiang Welding materials Co. Ltd., Sahara Enterprises, Novametal SA, Kiswel Ltd., ZULFI WELDING ELECTRODES FACTORY CO. LTD, Gedik ART, Sumitomo Electric Industries, Ltd., ESAB Corporation, Safra SPA, Chanzhou Aozhong Special Welding Wire Co., Ltd., Anand ARC Ltd., Kunshan Gintune Welding Co., Ltd., Bullion Pipe, MIGAL.CO GmbH, Berkenhoff GmbH, Illinois Tool Works Inc., The Lincoln Electric Company, P. K. Engineers, Capilla Schweissmaterialien GmbH, Kobe Steel Ltd., Ador Welding Limited, Drahtwerk Elisental W. Erdmann GmbH, Welding Alloys Group, Changzhou Huatong Welding Industry Co.,Ltd., and Fuseteck Corporation.
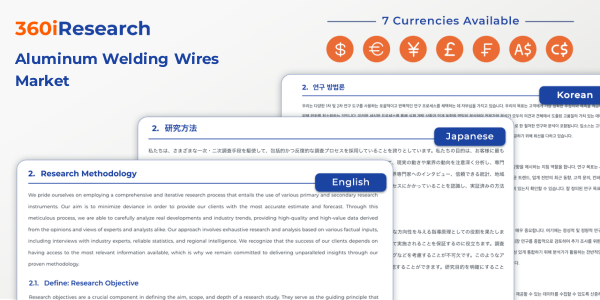
This research report categorizes the Aluminum Welding Wires Market to forecast the revenues and analyze trends in each of the following sub-markets:
- Product
- Flux-Cored Wires
- Solid Wires
- Technology
- Al-Si Alloy Welding Wire
- Aluminum Magnesium Alloy Welding Wire
- Pure Aluminum Welding Wire
- Distribution Channel
- Direct Sales
- Distributors
- Online Retail
- End-Use Industry
- Aerospace
- Automotive
- Construction
- Manufacturing
- Marine
- Application
- Cladding
- Fabrication
- Repair & Maintenance
- Region
- Americas
- Argentina
- Brazil
- Canada
- Mexico
- United States
- California
- Florida
- Illinois
- New York
- Ohio
- Pennsylvania
- Texas
- Asia-Pacific
- Australia
- China
- India
- Indonesia
- Japan
- Malaysia
- Philippines
- Singapore
- South Korea
- Taiwan
- Thailand
- Vietnam
- Europe, Middle East & Africa
- Denmark
- Egypt
- Finland
- France
- Germany
- Israel
- Italy
- Netherlands
- Nigeria
- Norway
- Poland
- Qatar
- Russia
- Saudi Arabia
- South Africa
- Spain
- Sweden
- Switzerland
- Turkey
- United Arab Emirates
- United Kingdom
- Americas
- Market Penetration: This section thoroughly overviews the current market landscape, incorporating detailed data from key industry players.
- Market Development: The report examines potential growth prospects in emerging markets and assesses expansion opportunities in mature segments.
- Market Diversification: This includes detailed information on recent product launches, untapped geographic regions, recent industry developments, and strategic investments.
- Competitive Assessment & Intelligence: An in-depth analysis of the competitive landscape is conducted, covering market share, strategic approaches, product range, certifications, regulatory approvals, patent analysis, technology developments, and advancements in the manufacturing capabilities of leading market players.
- Product Development & Innovation: This section offers insights into upcoming technologies, research and development efforts, and notable advancements in product innovation.
- What is the current market size and projected growth?
- Which products, segments, applications, and regions offer promising investment opportunities?
- What are the prevailing technology trends and regulatory frameworks?
- What is the market share and positioning of the leading vendors?
- What revenue sources and strategic opportunities do vendors in the market consider when deciding to enter or exit?
- Preface
- Research Methodology
- Executive Summary
- Market Overview
- Market Insights
- Aluminum Welding Wires Market, by Product
- Aluminum Welding Wires Market, by Technology
- Aluminum Welding Wires Market, by Distribution Channel
- Aluminum Welding Wires Market, by End-Use Industry
- Aluminum Welding Wires Market, by Application
- Americas Aluminum Welding Wires Market
- Asia-Pacific Aluminum Welding Wires Market
- Europe, Middle East & Africa Aluminum Welding Wires Market
- Competitive Landscape
- Competitive Portfolio
- List of Figures [Total: 26]
- List of Tables [Total: 468]
- List of Companies Mentioned [Total: 25]
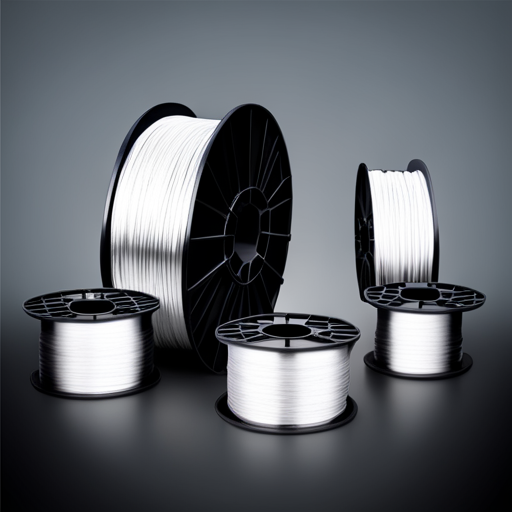
Key Features of Aluminum Welding Wires:
Aluminum welding wires are unique from other cables as they have outstanding corrosion resistance and provide superb electrical conductivity. Welding operations that employ aluminum welding wires are known for their aesthetic appeal as they produce clean and precise welds. This property is advantageous in manufacturing products such as heat exchangers, automotive components, and the aerospace industry.
Rising Use of Aluminum Welding Wires:
The increase in demand for aluminum welding wires is primarily a result of their low-density characteristics. The weight of aluminum is much lower than other metals, making it ideal for lightweight applications. Transportation, automotive, and aerospace industries require lightweight components to improve fuel efficiency and performance. Therefore, the need for aluminum welding wires has surged due to their versatility in various sectors.
Availability of Different Grades of Aluminum Welding Wires:
Different grades of aluminum welding wires are available depending on the final product's application. They range from pure aluminum to aluminum alloys that contain silicon, copper, magnesium, and manganese, among other elements. The grading helps match the desired properties of the weld to those of the end product.
Compatibility with various welding processes:
Aluminum welding wires are highly compatible with various welding processes, including MIG and TIG technologies. MIG welding utilizes consumables that melt and mix with the welded components, creating a stronger bond. TIG welding uses non-consumable tungsten to create the arc that melts the base materials together. So, whether it is TIG, MIG, or other welding technologies, aluminum welding wires offer superior compatibility.
Regulatory standards:
Welding is a specialized field that requires adherence to various standards and operational protocols to produce quality products. Therefore, aluminum welding wires must comply with regulatory standards. These standards ensure the final product is safe and of the required quality.
The increasing expansion of welding production facilities is a primary driver for the growing demand for aluminum welding wires. This metal's low-density quality makes it ideal for various applications, including the aerospace and transportation sectors. Additionally, the availability of different grades of aluminum welding wires makes them suitable for a diverse scope of welding applications. Finally, aluminum welding wires are compatible with various technologies, making them ideal for different welding processes.
- How big is the Aluminum Welding Wires Market?
- What is the Aluminum Welding Wires Market growth?
- When do I get the report?
- In what format does this report get delivered to me?
- How long has 360iResearch been around?
- What if I have a question about your reports?
- Can I share this report with my team?
- Can I use your research in my presentation?