The Aluminum Welding Wires Market size was estimated at USD 10.46 billion in 2024 and expected to reach USD 11.61 billion in 2025, at a CAGR 10.91% to reach USD 19.48 billion by 2030.
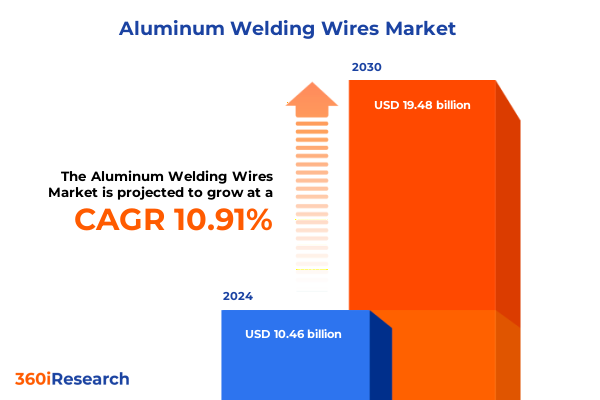
Introduction to the Aluminum Welding Wires Market
The aluminum welding wires market is at a critical juncture, driven by evolving industrial requirements and technological breakthroughs. As global manufacturing pivots towards lighter, stronger materials, aluminum alloys have become indispensable across sectors ranging from aerospace to automotive. Welding wires tailored for aluminum substrates deliver essential benefits: enhanced corrosion resistance, optimal electrical conductivity and reduced weight. These attributes align with industry mandates for fuel efficiency, structural performance and sustainability. Furthermore, advancements in alloy engineering and automated welding platforms are reshaping how fabricators approach joint integrity and productivity. Yet, this dynamic environment also presents challenges-supply chain realignments, material shortages and rising trade barriers demand agile strategies.
Against this backdrop, companies and decision–makers require a thorough understanding of the forces molding the aluminum welding wires landscape. This introduction establishes the market’s core dynamics, spotlighting key drivers and constraints that will echo throughout subsequent sections. By weaving together technological, regulatory and economic threads, readers gain a cohesive overview that sets the stage for deeper insights.
Transformative Shifts in the Aluminum Welding Landscape
The aluminum welding wires sector is experiencing transformative shifts, propelled by next–generation technologies and changing end–user priorities. Robotics and artificial intelligence–enabled welding cells now deliver consistent bead geometry and minimal porosity, reducing rework and boosting throughput. Concurrently, the rise of high-performance alloys-particularly aluminum–silicon blends with enhanced fluidity-permits welding at lower heat inputs, preserving base–metal integrity and minimizing distortion.
Sustainability goals have catalyzed a pivot toward low-emission welding processes. Manufacturers are adopting flux-cored wires with proprietary chemistries that stabilize arc characteristics while reducing spatter and fume generation. This trend not only addresses stringent workplace safety regulations but also aligns with corporate net-zero pledges. On the supply side, raw material digitalization enables real-time tracking of alloy batches, elevating quality control and ensuring traceability from smelter to shop floor.
Meanwhile, the proliferation of additive manufacturing in aluminum components has sparked research into hybrid fusion–brazing wires, further blurring traditional process boundaries. Taken together, these technological and sustainability imperatives are remapping competitive benchmarks and redefining value propositions in the aluminum welding wires market.
Cumulative Impact of United States Tariffs 2025
With the United States implementing a fresh round of tariffs on imported aluminum welding wires in early 2025, manufacturers and end–users are reassessing procurement strategies. The cumulative impact amplifies landed costs by up to 15%, compelling fabricators to diversify sourcing. Several have already negotiated longer-term supply agreements with domestic mills, while others are exploring alternative origins in Southeast Asia to mitigate price volatility. These tariff shifts also accelerate near-shoring initiatives, particularly for automakers and aerospace suppliers seeking supply chain resilience.
On the domestic front, tariff revenues are being reinvested into downstream capacity expansions, bolstering local alloy production and generating economies of scale. In parallel, research grants are fueling innovation in low-cost alloying elements that maintain weldability under tariff-constrained budgets. However, smaller welding shops face margin pressure, as cost inflations are difficult to pass along to end customers. To remain competitive, many SMEs are streamlining operations through advanced welding management software and targeting higher-value niche applications.
Ultimately, the 2025 tariff environment is sharpening the focus on supply chain agility and cost engineering. Organizations that proactively reconfigure logistics, secure diversified raw material channels and leverage domestic incentives will be best positioned to thrive under these new trade parameters.
Key Segmentation Insights
Segmentation analysis reveals nuanced opportunities and constraints across the aluminum welding wires market. By type, brazing wires excel in aerospace fittings while fusion welding wires dominate automotive assembly lines; hardfacing wires extend service life in heavy machinery and thermal spray wires fortify protective coatings for marine and infrastructure projects. Material composition delineates distinct performance tiers: aluminum-manganese alloys strike an optimal balance of strength and formability, aluminum-silicon blends ease weld flow and reduce hot cracking, and pure aluminum wires ensure maximum conductivity for electrical and heat exchanger assemblies.
Product form segmentation underscores divergent application profiles: flux-cored wires enable high deposition rates for automated workflows, while solid wires remain a reliable choice for manual welding environments. In application segments, aerospace and automotive sectors demand stringent certification and repeatability, construction and general manufacturing prioritize cost efficiency, and shipbuilding confronts unique corrosion challenges. End-user segmentation mirrors these trends, with aerospace and defense, automotive components, building and infrastructure and consumer electronics each commanding tailored alloy chemistries and quality control protocols.
Dimensional characteristics such as thickness range drive process selection: wires under 1 mm facilitate precision joining for consumer electronics, 1 mm to 5 mm grades are standard in automotive panels, 5 mm to 10 mm wires reinforce heavy-duty structures, and above 10 mm feedstocks target thick-section repairs. Tensile strength grades bifurcate into low, medium and high strength classes, guiding material engineers in selecting wires that meet fatigue and impact requirements. Similarly, melting temperature tiers-low, medium and high-dictate heat input strategies. Coating types, from nickel-coated for corrosion mitigation to zinc-coated for sacrificial protection and non-coated for pure alloy characteristics, further refine selection. Finally, technology and process type segmentation ties everything together, as automatic and manual welding platforms leverage flux-cored arc welding, gas metal arc welding, submerged arc welding and tungsten inert gas welding to achieve diverse production objectives.
This comprehensive research report categorizes the Aluminum Welding Wires market into clearly defined segments, providing a detailed analysis of emerging trends and precise revenue forecasts to support strategic decision-making.
- Type
- Material Composition
- Product Form
- Application
- End-User Industry
- Thickness Range
- Tensile Strength Grade
- Melting Temperature
- Coating Type
- Technology
- Process Type
Key Regional Insights
Regional dynamics shape market behavior in distinct ways. In the Americas, growing reshoring efforts and robust automotive and aerospace sectors drive demand for high-performance aluminum welding wires. Domestic policy incentives and infrastructure spending foster investments in local alloy refiners and welding consumable manufacturers. Across Europe, Middle East & Africa, stringent environmental regulations and ambitious renewable energy projects underscore the necessity of low-emission welding wires, while the shipbuilding industry in the Gulf and Mediterranean remains a significant consumer of corrosion-resistant alloys.
In Asia-Pacific, rapid industrialization and urbanization fuel the largest share of consumption. China’s expanding electric vehicle and high-speed rail programs rely heavily on aluminum structures, elevating demand for specialized flux-cored and solid wires. Japan and South Korea, home to major electronics and automotive OEMs, maintain rigorous quality standards that drive continuous innovation. Southeast Asian nations are emerging as key manufacturing hubs, offering competitive labor and supportive trade agreements that attract welding wire producers looking to optimize cost structures and regional reach.
This comprehensive research report examines key regions that drive the evolution of the Aluminum Welding Wires market, offering deep insights into regional trends, growth factors, and industry developments that are influencing market performance.
- Americas
- Asia-Pacific
- Europe, Middle East & Africa
Key Company Insights Driving Competitive Differentiation
Leading enterprises are leveraging scale, technological expertise and strategic partnerships to strengthen their market positions. Ador Welding Limited and ESAB Corporation capitalize on broad product portfolios and service networks to address complex industrial welding requirements, while The Lincoln Electric Company and Illinois Tool Works Inc. differentiate through integrated equipment and consumables solutions. Kobe Steel Ltd. and Sumitomo Electric Industries, Ltd. invest heavily in alloy R&D to maintain high-margin specialty wires, whereas Kiswel Ltd. and Capilla Schweissmaterialien GmbH pursue regional expansion to capture underserved markets.
Players such as ChangZhou Changjiang Welding Materials Co. Ltd. and Changzhou Huatong Welding Industry Co., Ltd. scale production of flux-cored arc welding wires for automotive OEMs, while Drahtwerk Elisental W. Erdmann GmbH and Berkenhoff GmbH emphasize sustainability certifications to win contracts in Europe. Safra SPA and Sahara Enterprises specialize in high-strength tensile grade wires for defense applications, and Novametal SA deploys advanced melting technologies for premium aluminum-silicon alloys. Fusionteck Corporation and Welding Alloys Group focus on thermal spray and hardfacing segments. Meanwhile, Anand ARC Ltd., Bullion Pipe, Chanzhou Aozhong Special Welding Wire Co., Ltd., P. K. Engineers, MIGAL.CO GmbH, ZULFI WELDING ELECTRODES FACTORY CO. LTD. and Fuseteck Corporation collectively expand regional footprints by forging alliances with local distributors and service providers.
This comprehensive research report delivers an in-depth overview of the principal market players in the Aluminum Welding Wires market, evaluating their market share, strategic initiatives, and competitive positioning to illuminate the factors shaping the competitive landscape.
- Ador Welding Limited
- Anand ARC Ltd.
- Berkenhoff GmbH
- Bullion Pipe
- Capilla Schweissmaterialien GmbH
- ChangZhou Changjiang Welding materials Co. Ltd.
- Changzhou Huatong Welding Industry Co.,Ltd.
- Chanzhou Aozhong Special Welding Wire Co., Ltd.
- Drahtwerk Elisental W. Erdmann GmbH
- ESAB Corporation
- Fuseteck Corporation
- Gedik ART
- Illinois Tool Works Inc.
- Kiswel Ltd.
- Kobe Steel Ltd.
- Kunshan Gintune Welding Co., Ltd.
- MIGAL.CO GmbH
- Novametal SA
- P. K. Engineers
- Safra SPA
- Sahara Enterprises
- Sumitomo Electric Industries, Ltd.
- The Lincoln Electric Company
- Welding Alloys Group
- ZULFI WELDING ELECTRODES FACTORY CO. LTD
Actionable Recommendations for Industry Leaders
To navigate rising trade barriers, technological disruption and sustainability mandates, industry leaders should pursue multifaceted strategies. First, integrate advanced welding analytics platforms to monitor arc stability and deposition efficiency in real time, enabling rapid process optimization. Second, cultivate agile supply chains by qualifying secondary suppliers in low-tariff jurisdictions and negotiating volume-discount contracts that absorb price fluctuations. Third, invest in R&D collaborations with research institutions to develop low-fume, high-flow alloys that meet upcoming emission standards without sacrificing deposition rate.
Moreover, diversify value propositions through bundled service models that combine welding equipment, consumables and training. This approach enhances customer lock-in and opens revenue streams in aftermarket support. Simultaneously, align sustainability roadmaps with circular economy initiatives, implementing alloy recycling programs and certified eco-labeling. Finally, strengthen digital marketing and thought leadership efforts to position your organization as a trusted advisor in critical verticals such as aerospace, automotive and infrastructure.
Explore AI-driven insights for the Aluminum Welding Wires market with ResearchAI on our online platform, providing deeper, data-backed market analysis.
Ask ResearchAI anything
World's First Innovative Al for Market Research
Conclusion: Reinforcing Future Resilience and Growth
The aluminum welding wires market stands poised for continued evolution under the influence of technology, regulation and trade policy. Organizations that proactively embrace automation, develop next-generation alloys and reinforce supply chain robustness will differentiate themselves in an increasingly competitive environment. Segmentation insights reveal targeted growth corridors, while regional analysis underscores the importance of localized strategies. Company profiles illustrate that sustained differentiation derives from integrated solutions, persistent R&D investment and strategic partnerships. As 2025 unfolds, the interplay between tariff regimes and innovation priorities will determine which market participants thrive.
In sum, the ability to adapt to shifting cost structures, comply with heightened environmental standards and deliver consistent quality will define leadership in this market. Those that balance operational excellence with forward-looking product development will capture the lion’s share of growth opportunities and cement long-term customer relationships.
This section provides a structured overview of the report, outlining key chapters and topics covered for easy reference in our Aluminum Welding Wires market comprehensive research report.
- Preface
- Research Methodology
- Executive Summary
- Market Overview
- Market Dynamics
- Market Insights
- Cumulative Impact of United States Tariffs 2025
- Aluminum Welding Wires Market, by Type
- Aluminum Welding Wires Market, by Material Composition
- Aluminum Welding Wires Market, by Product Form
- Aluminum Welding Wires Market, by Application
- Aluminum Welding Wires Market, by End-User Industry
- Aluminum Welding Wires Market, by Thickness Range
- Aluminum Welding Wires Market, by Tensile Strength Grade
- Aluminum Welding Wires Market, by Melting Temperature
- Aluminum Welding Wires Market, by Coating Type
- Aluminum Welding Wires Market, by Technology
- Aluminum Welding Wires Market, by Process Type
- Americas Aluminum Welding Wires Market
- Asia-Pacific Aluminum Welding Wires Market
- Europe, Middle East & Africa Aluminum Welding Wires Market
- Competitive Landscape
- ResearchAI
- ResearchStatistics
- ResearchContacts
- ResearchArticles
- Appendix
- List of Figures [Total: 38]
- List of Tables [Total: 510 ]
Call-To-Action: Partner with Ketan Rohom to Unlock Deeper Market Intelligence
Ready to transform your strategic approach? Engage with Ketan Rohom (Associate Director, Sales & Marketing) to secure the comprehensive aluminum welding wires market research report. Gain exclusive access to in-depth analyses, tailored scenario planning and actionable insights designed to elevate your competitive advantage. Reach out today to unlock the data-driven strategies you need to navigate the evolving landscape and lead with confidence.
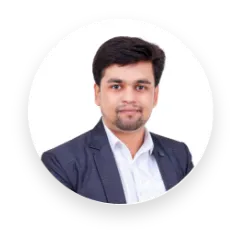
- How big is the Aluminum Welding Wires Market?
- What is the Aluminum Welding Wires Market growth?
- When do I get the report?
- In what format does this report get delivered to me?
- How long has 360iResearch been around?
- What if I have a question about your reports?
- Can I share this report with my team?
- Can I use your research in my presentation?