[180 Pages Report] The Aseptic Pharma Processing Market size was estimated at USD 49.02 billion in 2023 and expected to reach USD 51.83 billion in 2024, at a CAGR 5.92% to reach USD 73.34 billion by 2030.
Aseptic pharma processing, crucial in the pharmaceutical industry, ensures sterile production environments for medications and biologics to maintain safety and efficacy. This technique is essential for formulating, filling, and packaging injectable drugs, vaccines, and other sterile products. Its necessity stems from its ability to guarantee high sterility assurance, mitigating contamination risks that could lead to recalls and regulatory non-compliance. Primary end-users widely applied to injectable medications, biologics, vaccines, and IV fluids include pharmaceutical manufacturers, biotech companies, contract manufacturing organizations (CMOs), and healthcare facilities. The market growth is influenced by rising demands for biologics, stringent regulatory standards from agencies such as FDA and EMA, advancements in aseptic technologies, and an expanding pharmaceutical sector. Key opportunities lie in investing in advanced technologies, tapping emerging markets, developing sustainable processes, and enhancing workforce training. However, challenges include high initial capital investment, technical complexities, compliance requirements, supply chain disruptions, contamination risks, and evolving regulations. The best innovation areas for business growth comprise digitalization, single-use systems, enhanced sterilization methods, and real-time monitoring systems. The aseptic pharma processing market remains highly dynamic, necessitating continuous innovation and investment in new technologies.
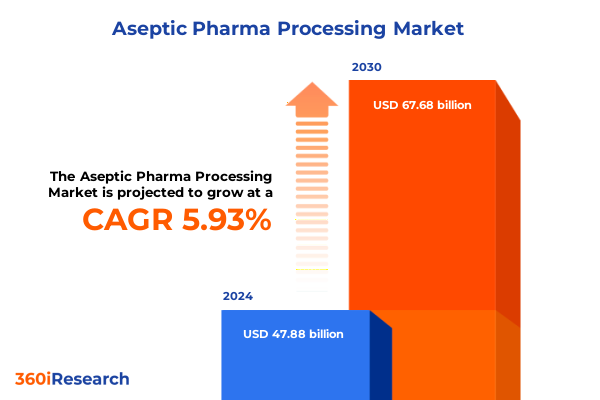
The market dynamics represent an ever-changing landscape of the Aseptic Pharma Processing Market by providing actionable insights into factors, including supply and demand levels. Accounting for these factors helps design strategies, make investments, and formulate developments to capitalize on future opportunities. In addition, these factors assist in avoiding potential pitfalls related to political, geographical, technical, social, and economic conditions, highlighting consumer behaviors and influencing manufacturing costs and purchasing decisions.
- Market Drivers
- Expanding usage of aseptic processing in the biotechnology industry
- Increasing demand for sterile packaging solutions in the pharmaceutical industry
- Market Restraints
- High initial investment and operational costs
- Market Opportunities
- Ongoing advancements in aseptic processing technologies
- Increasing need for large-scale vaccine production
- Market Challenges
- Concerns associated with strict regulations and standards
The market disruption analysis delves into the core elements associated with market-influencing changes, including breakthrough technological advancements that introduce novel features, integration capabilities, regulatory shifts that could drive or restrain market growth, and the emergence of innovative market players challenging traditional paradigms. This analysis facilitates a competitive advantage by preparing players in the Aseptic Pharma Processing Market to pre-emptively adapt to these market-influencing changes, enhances risk management by early identification of threats, informs calculated investment decisions, and drives innovation toward areas with the highest demand in the Aseptic Pharma Processing Market.
The porter's five forces analysis offers a simple and powerful tool for understanding, identifying, and analyzing the position, situation, and power of the businesses in the Aseptic Pharma Processing Market. This model is helpful for companies to understand the strength of their current competitive position and the position they are considering repositioning into. With a clear understanding of where power lies, businesses can take advantage of a situation of strength, improve weaknesses, and avoid taking wrong steps. The tool identifies whether new products, services, or companies have the potential to be profitable. In addition, it can be very informative when used to understand the balance of power in exceptional use cases.
The value chain of the Aseptic Pharma Processing Market encompasses all intermediate value addition activities, including raw materials used, product inception, and final delivery, aiding in identifying competitive advantages and improvement areas. Critical path analysis of the <> market identifies task sequences crucial for timely project completion, aiding resource allocation and bottleneck identification. Value chain and critical path analysis methods optimize efficiency, improve quality, enhance competitiveness, and increase profitability. Value chain analysis targets production inefficiencies, and critical path analysis ensures project timeliness. These analyses facilitate businesses in making informed decisions, responding to market demands swiftly, and achieving sustainable growth by optimizing operations and maximizing resource utilization.
The pricing analysis comprehensively evaluates how a product or service is priced within the Aseptic Pharma Processing Market. This evaluation encompasses various factors that impact the price of a product, including production costs, competition, demand, customer value perception, and changing margins. An essential aspect of this analysis is understanding price elasticity, which measures how sensitive the market for a product is to its price change. It provides insight into competitive pricing strategies, enabling businesses to position their products advantageously in the Aseptic Pharma Processing Market.
The technology analysis involves evaluating the current and emerging technologies relevant to a specific industry or market. This analysis includes breakthrough trends across the value chain that directly define the future course of long-term profitability and overall advancement in the Aseptic Pharma Processing Market.
The patent analysis involves evaluating patent filing trends, assessing patent ownership, analyzing the legal status and compliance, and collecting competitive intelligence from patents within the Aseptic Pharma Processing Market and its parent industry. Analyzing the ownership of patents, assessing their legal status, and interpreting the patents to gather insights into competitors' technology strategies assist businesses in strategizing and optimizing product positioning and investment decisions.
The trade analysis of the Aseptic Pharma Processing Market explores the complex interplay of import and export activities, emphasizing the critical role played by key trading nations. This analysis identifies geographical discrepancies in trade flows, offering a deep insight into regional disparities to identify geographic areas suitable for market expansion. A detailed analysis of the regulatory landscape focuses on tariffs, taxes, and customs procedures that significantly determine international trade flows. This analysis is crucial for understanding the overarching legal framework that businesses must navigate.
The regulatory framework analysis for the Aseptic Pharma Processing Market is essential for ensuring legal compliance, managing risks, shaping business strategies, fostering innovation, protecting consumers, accessing markets, maintaining reputation, and managing stakeholder relations. Regulatory frameworks shape business strategies and expansion initiatives, guiding informed decision-making processes. Furthermore, this analysis uncovers avenues for innovation within existing regulations or by advocating for regulatory changes to foster innovation.
The FPNV positioning matrix is essential in evaluating the market positioning of the vendors in the Aseptic Pharma Processing Market. This matrix offers a comprehensive assessment of vendors, examining critical metrics related to business strategy and product satisfaction. This in-depth assessment empowers users to make well-informed decisions aligned with their requirements. Based on the evaluation, the vendors are then categorized into four distinct quadrants representing varying levels of success, namely Forefront (F), Pathfinder (P), Niche (N), or Vital (V).
The market share analysis is a comprehensive tool that provides an insightful and in-depth assessment of the current state of vendors in the Aseptic Pharma Processing Market. By meticulously comparing and analyzing vendor contributions, companies are offered a greater understanding of their performance and the challenges they face when competing for market share. These contributions include overall revenue, customer base, and other vital metrics. Additionally, this analysis provides valuable insights into the competitive nature of the sector, including factors such as accumulation, fragmentation dominance, and amalgamation traits observed over the base year period studied. With these illustrative details, vendors can make more informed decisions and devise effective strategies to gain a competitive edge in the market.
The strategic analysis is essential for organizations seeking a solid foothold in the global marketplace. Companies are better positioned to make informed decisions that align with their long-term aspirations by thoroughly evaluating their current standing in the Aseptic Pharma Processing Market. This critical assessment involves a thorough analysis of the organization’s resources, capabilities, and overall performance to identify its core strengths and areas for improvement.
The report delves into recent significant developments in the Aseptic Pharma Processing Market, highlighting leading vendors and their innovative profiles. These include AST, Inc., Lonza Group Ltd, Klenzaids Contamination Controls Pvt. Ltd., Dara Pharma, Pfizer Inc., Grand River Aseptic Manufacturing, PCI Pharma Services, OPTIMA Packaging Group, Boehringer Ingelheim International GmbH, IMA S.p.A., JBT Corporation, Mycoscience Labs, Baxter Pharmaceutical Solutions LLC, TriRx Pharmaceutical Services, Ajinomoto Bio-Pharma, Catalent, Inc., Micron HVAC Pvt. Ltd., Thermo Fisher Scientific Inc., Dietrich Engineering Consultants, Syntegon Technology GmbH, Steriline S.r.l., Vetter Pharma, Körber AG, SAE Media Group, AbbVie Inc., and Evonik Industries AG.
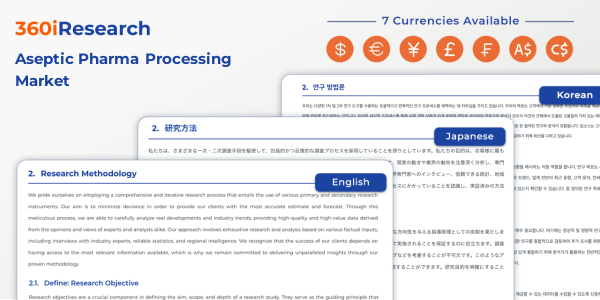
This research report categorizes the Aseptic Pharma Processing Market to forecast the revenues and analyze trends in each of the following sub-markets:
- Type
- Packaging
- Bags & Pouches
- Bottles & Cans
- Cartons
- Pre-filled Syringes
- Vials & Ampoules
- Processing
- Centrifuges & Separation Equipment
- Heat Exchangers
- Homogenizers
- Spray Dryers
- Ultra High-Temperature Treatment
- Packaging
- Material
- Glass
- Metal
- Paper & Paperboard
- Plastic
- Application
- Aqueous-based Aerosols for Inhalation
- Ophthalmic Suspensions
- Reconstituted Lyophilized Powders for Injection
- Sterile Injectables
- Region
- Americas
- Argentina
- Brazil
- Canada
- Mexico
- United States
- California
- Florida
- Illinois
- New York
- Ohio
- Pennsylvania
- Texas
- Asia-Pacific
- Australia
- China
- India
- Indonesia
- Japan
- Malaysia
- Philippines
- Singapore
- South Korea
- Taiwan
- Thailand
- Vietnam
- Europe, Middle East & Africa
- Denmark
- Egypt
- Finland
- France
- Germany
- Israel
- Italy
- Netherlands
- Nigeria
- Norway
- Poland
- Qatar
- Russia
- Saudi Arabia
- South Africa
- Spain
- Sweden
- Switzerland
- Turkey
- United Arab Emirates
- United Kingdom
- Americas
- Market Penetration: This section thoroughly overviews the current market landscape, incorporating detailed data from key industry players.
- Market Development: The report examines potential growth prospects in emerging markets and assesses expansion opportunities in mature segments.
- Market Diversification: This includes detailed information on recent product launches, untapped geographic regions, recent industry developments, and strategic investments.
- Competitive Assessment & Intelligence: An in-depth analysis of the competitive landscape is conducted, covering market share, strategic approaches, product range, certifications, regulatory approvals, patent analysis, technology developments, and advancements in the manufacturing capabilities of leading market players.
- Product Development & Innovation: This section offers insights into upcoming technologies, research and development efforts, and notable advancements in product innovation.
- What is the current market size and projected growth?
- Which products, segments, applications, and regions offer promising investment opportunities?
- What are the prevailing technology trends and regulatory frameworks?
- What is the market share and positioning of the leading vendors?
- What revenue sources and strategic opportunities do vendors in the market consider when deciding to enter or exit?
- Preface
- Research Methodology
- Executive Summary
- Market Overview
- Market Insights
- Aseptic Pharma Processing Market, by Type
- Aseptic Pharma Processing Market, by Material
- Aseptic Pharma Processing Market, by Application
- Americas Aseptic Pharma Processing Market
- Asia-Pacific Aseptic Pharma Processing Market
- Europe, Middle East & Africa Aseptic Pharma Processing Market
- Competitive Landscape
- Competitive Portfolio
- List of Figures [Total: 22]
- List of Tables [Total: 476]
- List of Companies Mentioned [Total: 26]
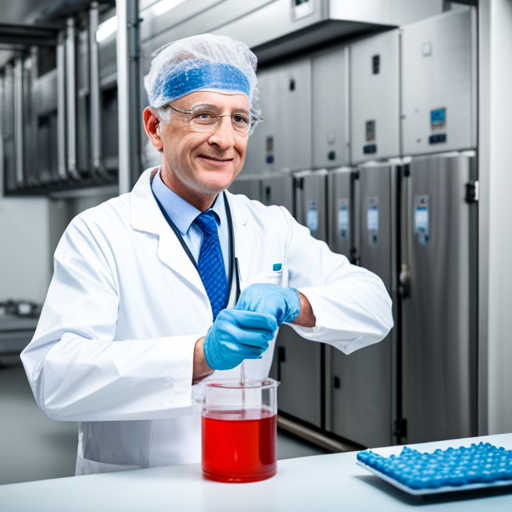
Disposable Systems:
One of the most significant technological advancements in aseptic processing is the use of disposable systems. Disposable manufacturing is a rapidly developing alternative to traditional stainless-steel manufacturing, which has several benefits. Firstly, disposable systems offer flexibility and provide an ease of changeover between different products, reducing contamination risks. Secondly, they facilitate modular and scalable production, enabling manufacturers to meet changing demands with minimal capital investment. Thirdly, disposable systems eliminate cleaning and sterilization, saving time and cost.
Barrier Isolators:
Barrier isolators protect the product from contamination by providing an airtight enclosure. They also enable improved operational safety and increase the productivity of the production line. Besides, barrier isolators require less space, leading to lower financial requirements and faster ramp-up times.
Protective Film Technologies:
Protective film technologies are used to create an isolated, clean environment in pharmaceutical filling lines by selectively covering different surfaces with cleanable film materials. Protective film technologies have transformed the industry in recent years with developments in automated machine applications. These films protect the products from airborne contamination and improve the efficiency of cleaning and decontamination protocols.
Robotics Automation:
Introducing robotics automation to aseptic processing minimizes the need for human intervention and reduces the risk of human error, which can cause contamination. Robotics automation enhances optimization, training, and control capabilities, improving quality. Additionally, robotics automation eliminates tedious and repetitive work, freeing up staff for more demanding tasks.
Reducing Water Utilization:
Another critical issue facing pharmaceutical companies is the water requirements necessary to run aseptic environments. Companies strive to reduce water consumption due to sustainability goals, regulations, and cost savings. Modern technologies limit water utilization and offer other techniques, such as dry heat and vapor phase decontamination, saving up to 99% of water consumption and providing a viable option to existing methods.
The growing demand for safety, quality, and accessibility has driven the development of aseptic processing technology in recent years. Advancements in disposable systems, barrier isolators, protective film technologies, robotics automation, and reducing water utilization are key to pharma manufacturing growth and success. These innovative techniques enable better-quality products, improve process efficiency, reduce production costs, and minimize the risk of contamination. Thus, pharmaceutical companies can leverage these technological advancements to increase manufacturing efficiency, meet regulatory requirements, and assure patient safety.
- How big is the Aseptic Pharma Processing Market?
- What is the Aseptic Pharma Processing Market growth?
- When do I get the report?
- In what format does this report get delivered to me?
- How long has 360iResearch been around?
- What if I have a question about your reports?
- Can I share this report with my team?
- Can I use your research in my presentation?