The Aseptic Pharma Processing Market size was estimated at USD 47.88 billion in 2024 and expected to reach USD 50.86 billion in 2025, at a CAGR 5.93% to reach USD 67.68 billion by 2030.

Revolutionizing Sterility with Advanced Aseptic Processing
In an era where patient safety and product integrity define competitive advantage, aseptic pharmaceutical processing stands at the intersection of engineering precision and regulatory rigor. Encompassing the sterile filling of liquid injectables and syrups, the careful handling of creams and gels, and the encapsulation of solid-dose therapies, aseptic techniques have evolved from manual cleanroom operations into advanced isolator systems and single-use assemblies. These innovations address rising demands for contamination control, process efficiency, and accelerated time-to-market.
Recent global health challenges have underscored both the strategic importance and the vulnerabilities of ensuring uninterrupted sterile production. Disruptions to raw material flows and surges in vaccine demand have exposed supply chain fragilities, prompting a renewed focus on resilient manufacturing platforms. Advanced digital twins and real-time process analytical technology have emerged as pivotal tools to detect minute deviations before they escalate into batch failures. Meanwhile, updates to global guidelines, including revisions to Annex 1 and the FDA’s latest process validation framework, have raised the bar for sterile production controls.
This executive summary synthesizes the transformative trends, policy shifts, and competitive dynamics shaping aseptic processing today. Drawing on segmentation analyses, regional overviews, and insights from leading equipment and service providers, the ensuing sections illuminate opportunities for innovation and risk mitigation. By integrating actionable recommendations, this document equips decision makers with the strategic framework needed to navigate an increasingly complex sterile manufacturing landscape.
Emerging Dynamics Reshaping Aseptic Manufacturing
In the past five years, the aseptic processing landscape has witnessed an unprecedented wave of digital and automation-driven innovations. Single-use assemblies and disposable bag-in-box systems have supplanted traditional stainless steel vessels in many fill-finish operations, reducing cleaning validation burdens and accelerating product changeovers. Simultaneously, the integration of continuous manufacturing platforms and process analytical technology has enabled real-time monitoring of critical quality attributes, enhancing consistency and yield. Artificial intelligence and machine learning algorithms now sift through terabytes of sensor data to predict contamination events and optimize equipment uptime.
Regulatory authorities worldwide have responded to these technological advances by refining guidelines and streamlining approval pathways. The European Union’s Annex 1 revisions emphasize closed systems, while the U.S. Food and Drug Administration’s guidance underscores lifecycle management and risk-based validation. Emerging harmonization efforts across Asia, the Middle East, and Latin America signal a gradual convergence toward unified sterility standards, reducing complexity for multinational manufacturers.
These transformative shifts are also reshaping competitive dynamics, as established equipment suppliers expand service portfolios to include digital twins, maintenance-as-a-service, and remote monitoring solutions. New entrants specializing in modular, plug-and-play platforms are challenging incumbents with agile deployment and lower capital intensity. In parallel, strategic alliances between pharmaceutical developers and technology vendors are accelerating the co-development of tailored aseptic suites for high-value biologics and vaccines. The result is a marketplace defined by rapid innovation cycles, heightened regulatory expectations, and an uncompromising drive for operational excellence.
Assessing the Ripple Effects of US Tariffs on Aseptic Operations
Building on the Section 301 measures introduced earlier in the decade, the United States implemented a new round of tariffs on critical raw materials and manufacturing equipment destined for aseptic processing in 2025. Stainless steel components, precision pumps, isolator modules, single-use piping assemblies, and fill-finish machinery now attract duties ranging from 10 to 25 percent. These levies have been applied not only to final equipment imported from major Asian and European hubs but also to key feedstocks and ancillary parts sourced from global suppliers. As a result, capital expenditures for new aseptic lines have surged, prompting capital planners to revisit return-on-investment assumptions and phased implementation schedules.
The tariff escalation has triggered a multifaceted response across the industry. Some manufacturers are accelerating efforts to localize supply chains, forging partnerships with domestic fabricators and equipment assemblers to mitigate exposure to cross-border levies. Others are renegotiating long-term contracts with original equipment manufacturers to secure preferential pricing or expanded service packages. Meanwhile, contract development and manufacturing organizations are exploring off-site prefabrication and standardized skid-based solutions to optimize duty classification. Despite these adaptive strategies, the increased cost base has pressured profit margins and elevated scrutiny of total cost of ownership, ultimately rewarding players who can deliver compelling value through integrated equipment-as-a-service offerings.
Looking ahead, tariff volatility remains a key risk factor, with negotiations between major trading partners creating uncertainty around trade policy continuity. Manufacturers that embed dynamic scenario planning and agile procurement practices are best positioned to navigate future fluctuations. As tariff frameworks evolve, the ability to quantify end-to-end supply chain costs and deploy modular, upgradable platforms will serve as a critical hedge against regulatory and economic turbulence.
Nuanced Views Across Segmentation Dimensions
When analyzing the market based on product type, liquid pharmaceuticals command a significant share, driven by both high-value biologics requiring injectables and patient-friendly oral syrups for ambulatory therapies. Within the liquid domain, aseptic processing lines for injectables must adhere to the strictest particulate and microbial control standards, while syrup filling operations emphasize viscosity management and container compatibility. Semi-solid formulations such as creams, gels, and ointments present unique challenges in maintaining uniform active pharmaceutical ingredient distribution under sterile conditions. The gels segment further bifurcates into oral gels, where taste masking and dosing precision are critical, and topical gels, which demand consistent rheology for correct application. Solid pharmaceuticals, encompassing capsules and tablets, rely on advanced encapsulation technology; hard gelatin capsules must balance shell integrity with dissolution profiles, whereas soft gelatin variants offer enhanced bioavailability for lipid-soluble compounds.
On the packaging material front, traditional glass remains the benchmark for parenteral therapies, with pipettes supplying diagnostic assays and vials serving as primary containers for high-value injectables. Metal tubes have secured a niche in semi-solid dressings and ointment products due to their barrier properties and consumer familiarity. Plastic ampoules and bottles are gaining traction for liquid formulations where breakage risk and weight considerations take precedence. From an equipment perspective, capping machines-available in multi-head configurations for large-scale throughput and single-head variants for batch flexibility-play a pivotal role in ensuring closure integrity. Filling machines vary between liquid and powder modules, each optimized for volumetric precision or mass dosing, respectively. Sterilization equipment such as autoclaves remains indispensable for steam-based decontamination, while tunnel sterilizers offer continuous pass-through solutions ideal for high-volume production.
The end user landscape comprises hospital pharmacies, pharmaceutical companies, and research institutes. Hospital pharmacies often prioritize compact, high-speed fill-finish units to manage on-demand compounding under strict sterility protocols. Pharmaceutical companies, including large enterprises and small & medium enterprises, seek scalable aseptic suites that can transition seamlessly from pilot to commercial capacity. Research institutes-spanning private labs and university labs-focus on flexible, modular platforms that facilitate rapid experimentation during both preclinical and clinical trial phases. In the clinical development phase, precise dosing and stringent documentation are paramount, whereas the production phase emphasizes sustained uptime and supply consistency.
When viewed through the lens of application, cardiology and infectious disease therapies maintain stable demand curves, driven by chronic treatment regimens and vaccination programs. Oncology and vaccine production are at the forefront of capital investment, reflecting the clinical urgency and high-value nature of these segments. Within neurology, Alzheimer’s and Parkinson’s candidates impose distinct aseptic requirements due to sensitive biologic modalities and narrow therapeutic indices. The component tier reveals a dichotomy between services and software: installation and maintenance services form the backbone of sustained operational excellence, ensuring equipment calibration and regulatory compliance over the lifecycle. Concurrently, software solutions for data analysis and process control provide real-time insights, predictive maintenance alerts, and automated batch documentation-elements that collectively enhance sterility assurance and drive continuous improvement.
This comprehensive research report categorizes the Aseptic Pharma Processing market into clearly defined segments, providing a detailed analysis of emerging trends and precise revenue forecasts to support strategic decision-making.
- Product Type
- Packaging Material
- Equipment Type
- End User
- Phase Of Use
- Application
- Component
Regional Landscapes Illuminating Global Aseptic Trends
The Americas region benefits from robust regulatory frameworks and deep capital markets that underwrite the rapid adoption of advanced aseptic processing technologies. The United States, in particular, leads with a dense concentration of bio-manufacturing hubs and stringent FDA oversight, which collectively drive demand for state-of-the-art isolator systems, robotic filling lines, and sophisticated sterility testing platforms. Canada’s emphasis on life sciences innovation has catalyzed investments in modular fill-finish suites, while Latin American markets, including Brazil and Chile, exhibit growing interest in local vaccine production, necessitating cost-effective glass vial filling and sterility assurance services.
Europe, the Middle East, and Africa present a tapestry of regulatory environments and market maturities. Western Europe’s harmonized directive under the European Medicines Agency fosters cross-border sourcing and standardization of sterile manufacturing practices. Emerging markets in the Middle East are expanding biosimilar capacity, supported by government incentives, leading to increased imports of capping and labeling equipment. In Africa, resource limitations and infrastructural constraints drive demand for turnkey, service-inclusive aseptic solutions that can operate under variable power and water quality conditions.
Asia-Pacific stands as a dynamic growth frontier, anchored by manufacturing giants in China and India that supply both domestic and global markets. Regulatory reforms in these nations have streamlined approval processes for sterile injectables, bolstering investments in stainless steel autoclaves and single-use production lines. Meanwhile, Japan and Australia maintain high sterility benchmarks, promoting the integration of line clearance automation and process analytical tools. Southeast Asian nations, including Malaysia and Vietnam, are emerging clinical trial centers, generating demand for ambulatory syringe fill-finish systems and real-time environmental monitoring services.
This comprehensive research report examines key regions that drive the evolution of the Aseptic Pharma Processing market, offering deep insights into regional trends, growth factors, and industry developments that are influencing market performance.
- Americas
- Europe, Middle East & Africa
- Asia-Pacific
Competitive Landscape and Company Strategies Unveiled
Leading equipment manufacturers and service providers are consolidating their positions through targeted acquisitions and strategic partnerships that broaden product portfolios and geographic reach. Companies with deep expertise in cleanroom assemblies are expanding into modular aseptic isolator systems, while traditional fill-finish machinery vendors are incorporating single-use technologies to address client demands for reduced validation cycles. The competitive landscape is further defined by niche suppliers specializing in specialized components, such as high-precision peristaltic pumps and micro-filtration units, which often command premium pricing due to stringent quality requirements.
Digitalization has emerged as a pivotal differentiator, with top-tier players offering integrated software platforms that unite data from sterilization cycles, filling operations, and quality analytics. These offerings enable remote monitoring, predictive maintenance scheduling, and automated batch release protocols, thereby minimizing downtime and accelerating compliance reporting. Service models are evolving to include equipment-as-a-service and performance-based contracts, shifting capital expenditure burdens toward operational expense structures and fostering long-term client relationships.
Innovation is also being driven by cross-sector collaboration. Partnerships between equipment vendors, software developers, and pharmaceutical sponsors are co-authoring best-practice standards for implementing digital twins and continuous manufacturing in sterile environments. Collaborative R&D initiatives with academic institutions and research institutes are yielding cutting-edge membrane technologies and closed-loop systems that promise to redefine sterility assurance paradigms. As next-generation biologics and personalized therapies gain traction, companies that can seamlessly integrate mechanical hardware, advanced services, and data-driven software will hold a competitive edge.
This comprehensive research report delivers an in-depth overview of the principal market players in the Aseptic Pharma Processing market, evaluating their market share, strategic initiatives, and competitive positioning to illuminate the factors shaping the competitive landscape.
- AbbVie Inc.
- Ajinomoto Bio-Pharma
- AST, Inc.
- Baxter Pharmaceutical Solutions LLC
- Boehringer Ingelheim International GmbH
- Catalent, Inc.
- Dara Pharma
- Dietrich Engineering Consultants
- Evonik Industries AG
- Grand River Aseptic Manufacturing
- IMA S.p.A.
- JBT Corporation
- Klenzaids Contamination Controls Pvt. Ltd.
- Körber AG
- Lonza Group Ltd.
- Micron HVAC Pvt. Ltd.
- Mycoscience Labs
- OPTIMA Packaging Group
- PCI Pharma Services
- Pfizer Inc.
- SAE Media Group
- Steriline S.r.l.
- Syntegon Technology GmbH
- Thermo Fisher Scientific Inc.
- TriRx Pharmaceutical Services
- Vetter Pharma
Strategic Actions Guiding Future-Proof Aseptic Operations
Industry leaders should prioritize a phased roadmap for adopting single-use and continuous manufacturing technologies, beginning with pilot-scale installations that validate process performance and cost-effectiveness. By integrating real-time analytics and digital twin frameworks early in the transformation, organizations can capture critical quality attribute data and establish predictive maintenance protocols that reduce unplanned downtime. Complementing automation investments with robust process analytical technology enhances batch-to-batch consistency and streamlines regulatory submissions through comprehensive data traceability.
Given ongoing tariff volatility and supply chain disruptions, firms must diversify their supplier base and explore nearshore or onshore sourcing strategies for critical components and consumables. Establishing long-term strategic partnerships with domestic fabricators and equipment assemblers can mitigate duty exposures and accelerate lead times. Simultaneously, aligning cross-functional teams to actively monitor policy changes and maintain agile procurement practices will ensure rapid adaptation to evolving trade environments and cost structures.
Workforce development remains integral to sustaining high-performance aseptic operations. Organizations should invest in targeted training programs that blend cleanroom practices with digital literacy, equipping technicians to operate automated filling lines and interpret analytical data outputs. Embracing sustainability goals by optimizing water and energy usage within sterilization and environmental control systems can yield both cost savings and regulatory goodwill. Finally, fostering collaborative ecosystems with software and service providers will enable the co-creation of tailored solutions, ensuring that aseptic processing platforms remain flexible, compliant, and technologically relevant.
Robust Research Methodology Underpinning Insights
This research employs a comprehensive approach that begins with an extensive review of publicly available literature, regulatory filings, industry white papers, and patent databases to map prevailing aseptic processing technologies and market dynamics. Secondary data sources are complemented by structured interviews with subject matter experts spanning pharmaceutical manufacturers, equipment OEMs, and regulatory consultants. These conversations yield qualitative insights into operational challenges, emerging trends, and strategic priorities.
Quantitative data is sourced from proprietary transaction databases, equipment shipment records, and published financial reports, enabling triangulation of market activity across regions and segments. Data validation is achieved through cross-referencing multiple sources and through follow-up expert consultations to resolve discrepancies. A rigorous classification framework ensures consistency in segment definitions, such as distinguishing between multi-head and single-head capping machines or parsing clinical development versus production phase requirements.
Analytical methodologies include comparative trend analysis, scenario planning, and sensitivity testing to assess the impact of variables such as tariff fluctuations and regulatory changes. The findings are synthesized into actionable insights, vetted through peer review by independent consultants, and presented in a structured format encompassing segmentation breakdowns, competitive intelligence, and regional overviews. This methodological rigor underpins the reliability of the recommendations and the strategic relevance of the report.
Explore AI-driven insights for the Aseptic Pharma Processing market with ResearchAI on our online platform, providing deeper, data-backed market analysis.
Ask ResearchAI anything
World's First Innovative Al for Market Research
Synthesis and Path Forward for Aseptic Processing
In summary, the aseptic pharmaceutical processing sector is undergoing a period of accelerated transformation driven by technological innovation, stricter regulatory scrutiny, and trade policy shifts. Advanced manufacturing paradigms-from single-use systems to continuous operations and digital twin integration-are redefining the parameters of sterility assurance and process efficiency. Market segmentation analyses reveal diverse requirements across product types, packaging materials, equipment categories, end users, development phases, therapeutic applications, and service‐software components. Regionally, the Americas lead in capital investments and regulatory rigor, Europe, the Middle East, and Africa present varied maturity levels, and Asia-Pacific stands out for its manufacturing scale and approval reforms.
Competitive pressures are intensifying as equipment suppliers, software developers, and service providers converge to deliver integrated, value-added solutions. Against a backdrop of tariff volatility and supply chain uncertainties, organizations that emphasize flexibility, data-driven decision making, and strategic partnerships will establish robust aseptic platforms. This executive summary has distilled the key insights and actionable recommendations necessary to guide investment decisions and operational strategies. Stakeholders equipped with this intelligence can confidently navigate the evolving sterile processing landscape and capture sustainable performance gains.
This section provides a structured overview of the report, outlining key chapters and topics covered for easy reference in our Aseptic Pharma Processing market comprehensive research report.
- Preface
- Research Methodology
- Executive Summary
- Market Overview
- Market Dynamics
- Market Insights
- Cumulative Impact of United States Tariffs 2025
- Aseptic Pharma Processing Market, by Product Type
- Aseptic Pharma Processing Market, by Packaging Material
- Aseptic Pharma Processing Market, by Equipment Type
- Aseptic Pharma Processing Market, by End User
- Aseptic Pharma Processing Market, by Phase Of Use
- Aseptic Pharma Processing Market, by Application
- Aseptic Pharma Processing Market, by Component
- Americas Aseptic Pharma Processing Market
- Europe, Middle East & Africa Aseptic Pharma Processing Market
- Asia-Pacific Aseptic Pharma Processing Market
- Competitive Landscape
- ResearchAI
- ResearchStatistics
- ResearchContacts
- ResearchArticles
- Appendix
- List of Figures [Total: 30]
- List of Tables [Total: 1120 ]
Engage with Ketan Rohom to Access the Full Market Report
To gain comprehensive access to the full market research report and unlock detailed data visualizations, proprietary analyses, and bespoke scenario modeling, connect with Ketan Rohom (Associate Director, Sales & Marketing at 360iResearch). His expertise will guide you through the report’s rich content and help identify the sections most relevant to your strategic priorities.
Act now to secure timely insights that will inform capital planning, regulatory planning, and technology roadmaps in advance of critical fiscal and policy milestones. Reach out today to explore tailored purchasing options and begin translating these findings into competitive advantage.
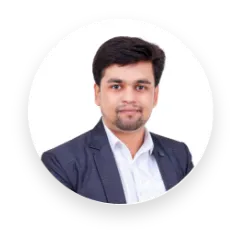
- How big is the Aseptic Pharma Processing Market?
- What is the Aseptic Pharma Processing Market growth?
- When do I get the report?
- In what format does this report get delivered to me?
- How long has 360iResearch been around?
- What if I have a question about your reports?
- Can I share this report with my team?
- Can I use your research in my presentation?