The Shredder Blades Market size was estimated at USD 344.41 million in 2024 and expected to reach USD 363.89 million in 2025, at a CAGR 5.60% to reach USD 477.86 million by 2030.

Shredder Blades Market in Focus
The shredder blades industry stands at a pivotal juncture, reflecting both enduring demand for document and material destruction technologies and evolving requirements driven by data security, sustainability, and efficiency. As businesses and consumers alike seek robust solutions to manage increasingly sensitive information and recyclable materials, shredder blades have become indispensable components in maintaining operational integrity and environmental responsibility. The introduction sets the stage by articulating the critical intersection of security regulations, waste management imperatives, and cost pressures that shape the competitive landscape for blade manufacturers and distributors.
In recent years, regulatory bodies across multiple sectors have tightened standards for data privacy and material disposal, prompting organizations to upgrade their shredding equipment to comply with newly enacted rules. These shifts have spurred innovation in blade geometry and materials engineering, with an emphasis on enhancing cutting performance while reducing energy consumption. Concurrently, the growing focus on circular economy principles has elevated the significance of recyclable and reusable componentry in blade manufacturing. Together, these dynamics underscore the strategic importance of understanding market drivers and constraints in order to anticipate future opportunities.
This introduction establishes the foundational context for stakeholders seeking to navigate market complexities. By outlining the convergence of regulatory mandates, sustainability goals, and operational efficiency demands, it underscores the need for informed decision-making grounded in comprehensive market insights. Readers will gain clarity on why shredder blade solutions remain at the forefront of organizational strategies targeting secure and sustainable material processing.
Cutting-Edge Forces Reshaping the Market
The landscape of shredder blades is undergoing transformative shifts, as technological advancements, supply chain realignments, and evolving customer expectations redefine competitive dynamics. Digital integration has emerged as a centerpiece of this transformation, with smart sensors and predictive maintenance platforms enabling real-time performance monitoring and proactive wear management. This move toward the Industrial Internet of Things heralds a new era of operational transparency and cost optimization, allowing manufacturers to offer value-added services beyond traditional product delivery.
Parallel to digitalization, supply chains are being reconfigured to address resilience and sustainability imperatives. Raw material sourcing strategies are shifting toward regional suppliers to mitigate global logistics disruptions and reduce carbon footprints. The growing emphasis on eco-friendly manufacturing practices has also prompted the adoption of low-emission heat treatments and closed-loop recycling systems for blade waste. These green initiatives resonate with end users striving to meet corporate social responsibility targets.
Customer expectations have likewise evolved, with users demanding customizable blade profiles that cater to specific shredding applications, from high-security document disposal to heavy-duty industrial material processing. As a result, modular design philosophies and rapid prototyping capabilities have become key differentiators. In combination, these transformative shifts underscore a market in flux, where agility, technological prowess, and sustainability credentials are fundamental to competitive advantage.
Navigating Tariff Pressures through Strategic Adaptation
The imposition of revised tariffs on imported steel and aluminum has exerted a cumulative impact on the shredder blade sector, affecting material costs, supply chain strategies, and pricing structures. Companies reliant on international suppliers faced upward pressure on production expenses, prompting a reevaluation of sourcing models and negotiations with domestic mills. This recalibration has generated both challenges and opportunities, as manufacturers explore alternative alloys and treatment processes to maintain performance while preserving margin profiles.
With tariffs influencing raw material procurement, firms have accelerated efforts to optimize blade lifespan through advanced coatings and proprietary heat treatment cycles. These enhancements not only mitigate cost volatility but also deliver tangible operational benefits for end users, reducing downtime and maintenance expenditures. Concurrently, the quest for cost containment has spurred collaborative ventures between metallurgical research institutes and blade producers, fostering innovation in high-strength, low-cost steel formulations.
Strategically, the tariff-driven environment has encouraged supply chain diversification. Some manufacturers have established buffer inventories or aligned with regional partners to ensure continuity amid policy fluctuations. Others have leveraged long-term supplier agreements to lock in favorable terms, while integrating digital procurement platforms to enhance visibility and agility. Collectively, these approaches illustrate how the market has adapted to external policy shifts, transforming potential disruptions into catalysts for performance improvement and resilience building.
Decoding Demand through Multi-Faceted Segmentation
Segmentation insights reveal nuanced preferences and performance expectations across the Type, Application, and Distribution Channel dimensions. When examining Type, security-sensitive environments gravitate toward micro cut blades, valuing maximal particle reduction and confidentiality, while high-volume industrial settings often select strip cut options for throughput efficiency. Cross cut blades occupy an intermediate niche, balancing security needs with operational speed, making them a versatile choice for mixed-use facilities.
Application-driven trends further differentiate demand. In commercial offices, where regulatory compliance and user convenience intersect, cross cut and micro cut blades dominate, supported by integrated maintenance services. Industrial applications prioritize robust blade profiles capable of processing heavy materials and abrasive media, leading to sustained interest in specialized heat-treated steel alloys. Residential users, meanwhile, continue to seek affordable yet reliable strip cut solutions for occasional personal use, demonstrating a preference for compact designs and noise reduction features.
Distribution channel evolution underscores a shift toward omnichannel engagement. Offline channels, including industrial suppliers and specialty stores, remain vital for customers requiring expert consultation and hands-on demonstrations. However, the efficiency and convenience of online platforms have gained traction, with manufacturer websites offering direct purchasing options and third party ecommerce sites providing rapid delivery and user reviews. This fusion of digital and physical touchpoints highlights the importance of integrated sales strategies that cater to diverse customer journeys.
This comprehensive research report categorizes the Shredder Blades market into clearly defined segments, providing a detailed analysis of emerging trends and precise revenue forecasts to support strategic decision-making.
- Type
- Application
- Distribution Channel
Regional Landscapes and Market Drivers Explored
Regional insights illuminate how geographic factors shape market dynamics, with each area presenting distinct growth enablers and challenges. In the Americas, robust regulatory frameworks for data protection and waste management have underpinned steady demand for advanced shredding solutions. The presence of large corporate headquarters and financial institutions ensures ongoing investment in high-security blade technologies, while initiatives promoting domestic manufacturing have spurred capacity expansions among local producers.
Across Europe, the Middle East & Africa, stringent environmental directives and circular economy mandates have elevated the market for recyclable blade materials and energy-efficient designs. European Union policies incentivize sustainable sourcing and waste reduction, driving innovation in blade coatings and refurbishing services. Meanwhile, emerging markets in the Middle East and Africa exhibit growing awareness of secure document destruction, creating white space for entry-level products and educational outreach on compliance requirements.
In Asia-Pacific, rapid industrialization and infrastructure development fuel demand for heavy-duty blades capable of processing diverse materials, from paper to plastics and textiles. Government-led smart city projects and digital transformation agendas encourage the integration of IoT-enabled shredding systems. Moreover, rising consumer spending and e-commerce proliferation have expanded opportunities through online channels, challenging established distributors to enhance digital capabilities and service offerings.
This comprehensive research report examines key regions that drive the evolution of the Shredder Blades market, offering deep insights into regional trends, growth factors, and industry developments that are influencing market performance.
- Americas
- Europe, Middle East & Africa
- Asia-Pacific
Proven Strategies of Leading Market Participants
Major players in the shredder blade market are deploying a combination of innovation, strategic partnerships, and operational excellence to strengthen their positions. Leading manufacturers are investing in advanced research facilities, collaborating with material science experts to pioneer proprietary alloy formulations that balance hardness with ductility. These breakthroughs result in blades that resist wear longer and perform reliably under varied operating conditions.
Strategic alliances with equipment manufacturers and service providers are another hallmark of competitive strategy. By embedding blade maintenance and refurbishment programs into broader service packages, companies can foster long-term customer relationships and create recurring revenue streams. Some industry leaders have also pursued targeted acquisitions of specialized coating firms, integrating unique surface treatments into their product portfolios to differentiate on longevity and cutting efficiency.
Operationally, best-in-class practices focus on lean manufacturing and digital twin simulations to optimize production workflows and accelerate time to market. Quality management systems, certified to rigorous international standards, ensure consistent blade performance and facilitate global market access. Through these combined efforts, key companies are not only reinforcing their market share but also shaping industry benchmarks for product innovation and customer service excellence.
This comprehensive research report delivers an in-depth overview of the principal market players in the Shredder Blades market, evaluating their market share, strategic initiatives, and competitive positioning to illuminate the factors shaping the competitive landscape.
- ANDRITZ AG
- Metso Outotec Oyj
- Coperion GmbH
- Bühler AG
- Vecoplan AG
- Allgaier SE
- Weima Maschinenbau GmbH
- Franklin Miller, Inc.
- SSI Shredding Systems, Inc.
- Eldan Recycling A/S
Practical Roadmap for Market Leadership
Industry leaders can fortify their competitive edge by embracing a multi-pronged strategy centered on innovation, sustainability, and customer-centricity. Prioritizing research and development in materials science will unlock next-generation blade alloys that deliver enhanced durability and reduced energy requirements, addressing both performance and environmental goals. Integrating digital monitoring and predictive analytics into product offerings can further differentiate solutions, enabling customers to anticipate maintenance needs and minimize operational disruptions.
Supply chain resilience demands proactive diversification of raw material sources and the establishment of collaborative partnerships with domestic and regional suppliers. Embedding circular economy principles through blade refurbishing and recycling programs can generate new revenue channels while demonstrating a commitment to environmental stewardship. Companies should also refine their value propositions across distribution channels by offering tailored training programs, virtual demonstrations, and responsive after-sales support to foster loyalty and facilitate seamless adoption.
Finally, cultivating an organizational culture that values continuous improvement and cross-functional collaboration will ensure that strategic initiatives translate into measurable business outcomes. By aligning research, manufacturing, and commercial teams around shared performance metrics, firms can accelerate innovation cycles and deliver cohesive experiences that resonate with an increasingly discerning customer base.
Robust Approach Underlying Market Analysis
This analysis is founded on a rigorous methodology combining secondary research, primary interviews, and data triangulation to ensure depth and accuracy. The secondary research phase involved examination of industry publications, regulatory documents, and technical white papers to establish a comprehensive contextual baseline. Macroenvironmental factors, including policy developments and sustainability frameworks, were systematically reviewed to inform market dynamics.
Primary research included in-depth interviews with key stakeholders across the value chain, from blade material suppliers to end users in commercial, industrial, and residential segments. These conversations provided qualitative insights into performance expectations, procurement criteria, and emerging use cases. The data collected was then validated and cross-verified through targeted surveys and comparative analysis of company annual reports and product specifications.
Analytical techniques such as SWOT analysis, competitive benchmarking, and Porter’s Five Forces were employed to assess market structure, competitive intensity, and potential areas of opportunity. The resulting findings were synthesized into actionable insights, ensuring that recommendations are grounded in both quantitative evidence and expert perspectives. This robust approach underpins the reliability and relevance of the research outcomes.
Explore AI-driven insights for the Shredder Blades market with ResearchAI on our online platform, providing deeper, data-backed market analysis.
Ask ResearchAI anything
World's First Innovative Al for Market Research
Synthesizing Insights for Strategic Clarity
In conclusion, the shredder blades market is characterized by a convergence of security, sustainability, and technological innovation. Regulatory imperatives and environmental considerations have elevated the importance of blade materials and maintenance solutions, while digital integration continues to redefine performance expectations. The impact of policy shifts, such as revised tariffs, has catalyzed strategic responses that enhance supply chain resilience and product differentiation.
Segmentation analysis reveals diverse needs across blade types, application areas, and distribution channels, underscoring the value of tailored offerings and omnichannel engagement strategies. Regional landscapes vary in regulatory frameworks, infrastructure development, and market maturity, presenting both established and emerging opportunities. Leading companies are leveraging cross-industry partnerships, proprietary research, and lean operations to secure competitive positions and drive incremental innovation.
By synthesizing these insights, stakeholders gain a holistic understanding of the market environment and the strategic imperatives required to navigate future challenges. This conclusion encapsulates the critical themes and sets the stage for informed decision-making that aligns with both current demands and long-term growth trajectories.
This section provides a structured overview of the report, outlining key chapters and topics covered for easy reference in our Shredder Blades market comprehensive research report.
- Preface
- Research Methodology
- Executive Summary
- Market Overview
- Market Dynamics
- Market Insights
- Cumulative Impact of United States Tariffs 2025
- Shredder Blades Market, by Type
- Shredder Blades Market, by Application
- Shredder Blades Market, by Distribution Channel
- Americas Shredder Blades Market
- Europe, Middle East & Africa Shredder Blades Market
- Asia-Pacific Shredder Blades Market
- Competitive Landscape
- ResearchAI
- ResearchStatistics
- ResearchContacts
- ResearchArticles
- Appendix
- List of Figures [Total: 22]
- List of Tables [Total: 233 ]
Connect with Our Expert to Unleash Market Insights
To explore the full breadth of strategic insights and in-depth analysis of the shredder blades market, reach out to Ketan Rohom, Associate Director, Sales & Marketing. His expertise in aligning market intelligence with business goals will help you navigate competitive challenges and seize new growth avenues. Schedule a conversation to discover how the comprehensive market research report can inform your next strategic move and drive value in your organization.
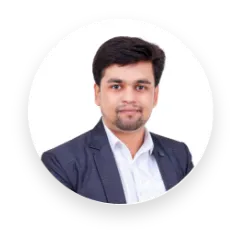
- How big is the Shredder Blades Market?
- What is the Shredder Blades Market growth?
- When do I get the report?
- In what format does this report get delivered to me?
- How long has 360iResearch been around?
- What if I have a question about your reports?
- Can I share this report with my team?
- Can I use your research in my presentation?