Introduction to the 14nm Wafer Foundry Market
The 14nm wafer foundry segment has emerged as a critical inflection point in semiconductor manufacturing, balancing performance, power efficiency and cost-effectiveness. Serving as a bridge between mature process nodes and the cutting edge of 10nm and below, the 14nm node continues to command strong demand across diverse industries. As device architectures evolve, this node’s robust yields and proven supply chains offer a reliable foundation for high-volume applications.
In recent years, market dynamics have been shaped by accelerated digital transformation, expanded connectivity and growing appetite for intelligent systems. From automotive safety features to advanced consumer electronics, the 14nm node underpins a spectrum of innovations. Moreover, supply chain disruptions have reinforced the value of established process technologies that deliver consistent throughput at scale.
This introduction sets the stage for an in-depth examination of shifting market forces, tariff impacts, segmentation insights, regional dynamics and competitive positioning. By understanding these facets, decision-makers can navigate complexities, seize opportunities and chart a resilient path forward in the 14nm wafer foundry landscape.
Transformative Shifts Redefining the 14nm Foundry Landscape
The wafer foundry landscape is undergoing transformative shifts that redefine competitive advantage. First, the maturation of FinFET architectures has unlocked new performance thresholds, driving widespread adoption of three-dimensional transistor designs. Alongside, FD-SOI and bulk CMOS variants offer differentiated power-efficiency profiles, enabling tailored solutions for low-power IoT devices and high-performance computing alike.
Concurrently, the industry is accelerating its embrace of advanced lithography. While deep ultraviolet (DUV) tools remain indispensable for 14nm node production, deployment of extreme ultraviolet (EUV) is gaining traction, signaling a readiness to transition toward next-generation nodes. This confluence of lithography strategies is reshaping equipment supply chains and capital spending patterns.
Furthermore, market consolidation among suppliers and strategic alliances between foundries and design houses are intensifying. Collaborative R&D platforms are emerging to mitigate escalating development costs, while sustainability initiatives are guiding process optimization toward reduced carbon footprints. Together, these shifts illustrate an industry in rapid evolution, balancing innovation, collaboration and environmental stewardship.
Cumulative Impact of United States Tariffs on 14nm Production by 2025
By 2025, expanded U.S. tariffs on semiconductor imports have introduced new layers of complexity to the 14nm wafer foundry ecosystem. Heightened duties on equipment components and raw materials have translated into incremental production costs. Many foundries relying on cross-border supply chains face elevated lead times and inventory carrying expenses as they navigate customs repricing and compliance procedures.
These measures have also reshuffled competitive dynamics. Domestic manufacturers have benefitted from preferential treatment under tariff exemptions, while offshore players have accelerated localization strategies to mitigate duty exposures. Asian-based foundries, in particular, have been compelled to establish or expand facilities outside the tariff zone, reallocating capital to regions with favorable trade terms.
Against this backdrop, risk management has become paramount. Foundry operators are reinforcing dual-sourcing policies, diversifying procurement channels and investing in tariff engineering solutions. As a result, agility in supply chain orchestration and regulatory foresight have emerged as key differentiators for market leaders.
Key Segmentation Insights for the 14nm Wafer Foundry Market
Segmentation analysis reveals the multifaceted nature of the 14nm wafer foundry market. When viewed through the lens of technology node, this market centers on the 14nm process and its variants-bulk CMOS for established high-volume applications, FD-SOI for ultra-low-power designs, and FinFETs for performance-intensive workloads-while benchmark comparisons against 10nm, 7nm and 5nm nodes highlight trade-offs between cost, yield and integration density.
Application segmentation underscores the broad spectrum of end uses. Aerospace and defense programs leverage 14nm’s proven reliability; automotive and transportation systems integrate advanced driver assistance, electric powertrain controllers and infotainment modules; consumer electronics span laptops, smartphones, tablets and wearables; healthcare platforms incorporate medical imaging, telemedicine suites and wearable health monitors; industrial automation, robotics and smart grid projects demand robust processing capabilities; and the IoT and connectivity segment extends from industrial IoT sensors to personal IoT devices and smart home ecosystems.
Examining end-use industries, automotive powertrain and safety systems rely on mature nodes for deterministic performance, while telecommunications infrastructure-including 5G radio access networks and broadband backhaul-leans on 14nm to balance throughput and cost. Customer-type segmentation further differentiates fabless design houses, integrated device manufacturers and original equipment manufacturers by their unique volume requirements and design‐for‐manufacturability constraints.
Chip-type distinctions span application-specific integrated circuits, digital signal processors, logic ICs and microprocessors, each demanding tailored process flows. Manufacturing process segmentation encompasses deposition and etching methods alongside photolithography, the latter subdivided into deep ultraviolet and extreme ultraviolet techniques. Finally, market trends reflect the expansion of IoT ecosystems, growth in automotive electronics and surging demand for artificial intelligence and machine-learning accelerators, whereas key challenges center on cost management, resource scalability and technological complexity.
This comprehensive research report categorizes the 14nm Wafer Foundry market into clearly defined segments, providing a detailed analysis of emerging trends and precise revenue forecasts to support strategic decision-making.
- Technology Node
- Application
- End-Use Industry
- Customer Type
- Chip Type
- Manufacturing Process
- Market Trends
- Key Challenges
Key Regional Insights in the 14nm Foundry Ecosystem
Regional dynamics in the 14nm wafer foundry market reveal distinct strategic priorities. In the Americas, foundry operators are focusing on domestic capacity expansions, driven by incentives for on-shore chip manufacturing and a robust automotive electronics sector demanding timely supply. Research collaborations between universities and local fabs are also accelerating process optimization.
Across Europe, the Middle East and Africa, sovereign technology initiatives are catalyzing partnerships among regional foundries. Emphasis on sustainability and energy-efficient fabs has led to investments in green manufacturing practices. Collaboration with government agencies and consortia on advanced packaging and heterogeneous integration is elevating the region’s role in the broader semiconductor value chain.
Asia-Pacific remains the world’s largest 14nm production hub, anchored by established leaders and emerging domestic players. Capacity investments in China, South Korea and Taiwan continue apace, supported by government subsidies and strategic partnerships with equipment suppliers. Meanwhile, Southeast Asian nations are positioning themselves as emerging assembly and test centers, completing a comprehensive regional supply network.
This comprehensive research report examines key regions that drive the evolution of the 14nm Wafer Foundry market, offering deep insights into regional trends, growth factors, and industry developments that are influencing market performance.
- Americas
- Asia-Pacific
- Europe, Middle East & Africa
Key Company Insights Driving the 14nm Foundry Sector
The competitive landscape of 14nm wafer foundries is defined by the strategic positioning and technological prowess of major players. Taiwan Semiconductor Manufacturing Company, Samsung Electronics and SMIC lead capacity installations, each leveraging advanced node roadmaps and comprehensive service portfolios. Intel and GlobalFoundries, with their integrated manufacturing capabilities, are optimizing modular process platforms to address diverse design requirements.
Broadcom and Texas Instruments, as high-volume consumers of 14nm wafers, influence capacity planning through long-term supply agreements, while Micron and SK hynix drive memory applications on mature geometries. NXP Semiconductors and STMicroelectronics, focusing on automotive and industrial markets, collaborate closely with foundry partners to validate reliability standards.
United Microelectronics and other regional foundries are carving niches in specialized process variants, including FD-SOI and embedded memory. Across the board, these companies are enhancing service offerings-ranging from design enablement and advanced packaging to post-silicon validation-to strengthen customer loyalty and differentiate in an increasingly commoditized market.
This comprehensive research report delivers an in-depth overview of the principal market players in the 14nm Wafer Foundry market, evaluating their market share, strategic initiatives, and competitive positioning to illuminate the factors shaping the competitive landscape.
- Broadcom Inc.
- GlobalFoundries Inc.
- Intel Corporation
- Micron Technology, Inc.
- NXP Semiconductors N.V.
- Samsung Electronics Co., Ltd.
- Semiconductor Manufacturing International Corporation (SMIC)
- SK hynix Inc.
- STMicroelectronics
- Taiwan Semiconductor Manufacturing Company (TSMC)
- Texas Instruments Incorporated
- United Microelectronics Corporation (UMC)
Actionable Recommendations for Industry Leaders in 14nm Manufacturing
To capitalize on the enduring relevance of the 14nm node, industry leaders should prioritize diversification of supply sources by establishing multi-regional production footprints, thereby mitigating tariff and geopolitical risks. Investing in hybrid lithography strategies-optimizing DUV for high-volume layers and selectively deploying EUV for critical patterning-will balance cost control with performance gains.
Collaboration models with design houses and equipment suppliers must evolve toward risk-and-reward frameworks, sharing development costs and accelerating time to market. Embedding AI-driven analytics into process control and yield management will unlock predictive maintenance insights and drive continuous improvement.
Furthermore, aligning sustainability objectives with manufacturing roadmaps by adopting water-recycling systems and energy-efficient fab equipment will enhance corporate responsibility profiles and comply with tightening environmental regulations. Finally, cultivating talent through cross-disciplinary training programs in photonics, materials science and data analytics will ensure the workforce remains adept at tackling next-generation challenges.
Explore AI-driven insights for the 14nm Wafer Foundry market with ResearchAI on our online platform, providing deeper, data-backed market analysis.
Ask ResearchAI anything
World's First Innovative Al for Market Research
Conclusion: Navigating the Future of 14nm Wafer Foundry
The 14nm wafer foundry node stands at the nexus of maturity and innovation. Its proven track record and adaptable process variants continue to support a wide array of applications, from safety-critical automotive systems to cutting-edge IoT ecosystems. Although pressure from advanced nodes persists, the strategic value of 14nm’s cost-performance balance remains compelling.
Amidst evolving trade policies and supply chain realignments, the ability to pivot between process technologies, diversify production sites and foster collaborative R&D emerges as a key to sustainable competitiveness. Moreover, integrating environmental stewardship into manufacturing roadmaps not only addresses regulatory demands but also resonates with end customers and investors.
By synthesizing these insights, stakeholders can navigate the complexities of the current landscape and chart a clear course for growth, leveraging the enduring strengths of the 14nm node while preparing for future transitions.
This section provides a structured overview of the report, outlining key chapters and topics covered for easy reference in our 14nm Wafer Foundry market comprehensive research report.
- Preface
- Research Methodology
- Executive Summary
- Market Overview
- Market Dynamics
- Market Insights
- Cumulative Impact of United States Tariffs 2025
- 14nm Wafer Foundry Market, by Technology Node
- 14nm Wafer Foundry Market, by Application
- 14nm Wafer Foundry Market, by End-Use Industry
- 14nm Wafer Foundry Market, by Customer Type
- 14nm Wafer Foundry Market, by Chip Type
- 14nm Wafer Foundry Market, by Manufacturing Process
- 14nm Wafer Foundry Market, by Market Trends
- 14nm Wafer Foundry Market, by Key Challenges
- Americas 14nm Wafer Foundry Market
- Asia-Pacific 14nm Wafer Foundry Market
- Europe, Middle East & Africa 14nm Wafer Foundry Market
- Competitive Landscape
- ResearchAI
- ResearchStatistics
- ResearchContacts
- ResearchArticles
- Appendix
- List of Figures [Total: 32]
- List of Tables [Total: 777 ]
Call to Action: Connect with Ketan Rohom for the Full Report
To explore a comprehensive analysis of these trends and strategic insights in greater depth, contact Ketan Rohom, Associate Director, Sales & Marketing, to purchase the full market research report. Understand how the 14nm wafer foundry market is evolving and gain the data-driven guidance needed to inform your next strategic move.
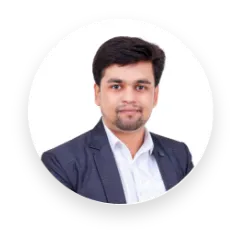
- When do I get the report?
- In what format does this report get delivered to me?
- How long has 360iResearch been around?
- What if I have a question about your reports?
- Can I share this report with my team?
- Can I use your research in my presentation?