Introduction to 3-Axis CNC Horizontal Machining Center Market Dynamics
Since the advent of automated machining systems, 3-axis CNC horizontal machining centers have emerged as cornerstone equipment in precision manufacturing. These machines deliver rigid construction, optimized chip evacuation, and pallet systems that boost throughput for components ranging from aerospace structural elements to automotive engine blocks. Over the past decade, enhancements in spindle speed, thermal stability management, and tool-change mechanisms have driven unprecedented accuracy, shorter cycle times, and reduced per-part costs. Simultaneously, the emphasis on sustainability and operator safety has led to the integration of energy-efficient drive systems, closed-loop coolant management, and noise-dampening enclosures. As digital transformation accelerates, these centers are evolving from standalone production units into interconnected nodes within smart factories, offering real-time monitoring, automated calibration, and seamless integration with enterprise systems. This executive introduction sets the stage for a comprehensive analysis of the market dynamics, regulatory influences, and strategic imperatives that will shape deployment and utilization strategies for the next generation of horizontal machining centers.
Transformative Shifts Shaping the 3-Axis Horizontal Machining Center Industry
In response to evolving production paradigms, several transformative shifts are reshaping the 3-axis horizontal machining center industry. The proliferation of Industry 4.0 concepts has fueled adoption of digital twin simulations, enabling engineers to model cutting processes and optimize parameters before material engagement. Coupled with the deployment of IoT sensors, this trend underpins predictive analytics that monitors spindle health, coolant quality, and tool wear, dramatically reducing unplanned downtime. Robotics integration has matured to support automated loading and pallet swapping, facilitating lights-out operations that address skilled labor shortages. Furthermore, the complexity of modern components-driven by multi-material aerospace designs and additive-to-subtractive hybrid workflows-has elevated demand for machines offering high rigidity and sophisticated multi-stage sequencing. Sustainability targets are also influencing machine design, prompting the incorporation of energy-saving drives, closed-loop coolant systems, and low-carbon manufacturing processes. Moreover, collaborations between equipment OEMs and software providers are delivering seamless control interface integration with enterprise resource planning systems. Consequently, the sector is witnessing a convergence of mechanical innovation, advanced control strategies, and digital services that together define the next horizon of machining center performance.
Cumulative Impact of United States Tariffs on 3-Axis Horizontal Machining in 2025
In January 2025, the United States enacted tariffs of up to 25% on steel and aluminum imports, directly impacting the cost structure of horizontal machining centers. Manufacturers faced rising expenses for structural castings, drive motors, and tool holders, triggering a wave of supply chain optimization. Domestic OEMs responded by partnering with local foundries, expanding raw material recycling initiatives, and absorbing a portion of cost increases to maintain competitive pricing. International suppliers, confronting compressed margins, are evaluating relocation of final assembly to tariff-free zones under existing trade agreements. End users in aerospace and automotive sectors are recalibrating capital expenditure plans, favoring lease-to-own arrangements and service contracts that stabilize cash flow amid tariff-induced volatility. The resulting delays in component availability have underscored the importance of strategic inventory buffers and diversified sourcing models. Furthermore, many industry players are leveraging tariff classification reviews and exploring material substitutions to mitigate duty liabilities. These adaptive strategies demonstrate how the 2025 tariff regime, while disruptive, can be navigated through proactive supply chain resilience measures and collaborative vendor relationships.
Key Market Segmentation Insights for 3-Axis Horizontal Machining Centers
An in-depth examination of market segmentation reveals distinct demand drivers across product types, end-user industries, technologies, applications, materials, machine sizes, and service models. Regarding product categories, automated machining centers equipped with integrated pallet systems are gaining traction in high-volume environments, while shops focused on complex five-axis contouring still leverage multi-axis solutions. Conventional vertical machining centers maintain a stable share for simpler prismatic parts but are outpaced by horizontal alternatives in cycle-time efficiency. In aerospace, demand splits between large airframe structures and precision spacecraft components, both requiring sub-0.01 mm tolerances. The automotive sector balances investments in aftermarket component refurbishment alongside high-speed OEM production lines. Electronics manufacturers deploy horizontal centers for consumer device enclosures and industrial control hardware, each with unique surface-finish requirements. Healthcare applications span medical device housings and surgical instrument prototypes, driving micron-level accuracy. Industrial machinery customers seek heavy-duty machining for factory equipment and core components for machine tools. On the technology front, the integration of robotics and automation modules works in tandem with advanced CNC controls featuring CAD/CAM integration and sophisticated G-code programming, while IoT connectivity enables remote diagnostics. Application-wise, mold making and tooling operations exploit horizontal centers’ deep-cavity capabilities, and production and prototyping workflows leverage consistent cycle times. Material selection ranges from lightweight composites to aluminum, steel, and titanium alloys, extending to acrylics, PVC plastics, and specialty wood. Machine footprint preferences span large systems for high-volume runs, medium cells for balanced floor-space utilization, and compact units for contract shops and academic institutions. Service portfolios encompass turnkey installation, preventive maintenance plans, and retrofit upgrades that extend machine lifecycles and optimize performance.
This comprehensive research report categorizes the 3-axis CNC Horizontal Machining Center market into clearly defined segments, providing a detailed analysis of emerging trends and precise revenue forecasts to support strategic decision-making.
- Product Type
- End-User Industries
- Technology
- Application Type
- Material Type
- Machine Size
- Service Type
Key Regional Insights Across Americas, EMEA, and Asia-Pacific Markets
Regional dynamics exhibit clear variations across the Americas, Europe, the Middle East & Africa, and Asia-Pacific, each presenting unique opportunities and challenges. In the Americas, reshoring initiatives and tax incentives in the United States have driven steady capital investment in horizontal machining centers, while cross-border supply chains under free-trade agreements support automotive and aerospace clusters in Canada and Mexico. European manufacturers, particularly in Germany and Italy, continue to innovate within strict environmental frameworks, accelerating the uptake of energy-efficient machines, whereas Eastern Europe’s subcontracting networks are expanding high-precision capabilities. The Middle East is modernizing its oil and gas infrastructure with heavy-duty machining solutions, complemented by diversification efforts into aerospace and defense manufacturing. Africa’s market remains emergent, with pockets of demand in South Africa’s mining equipment sector. Asia-Pacific experiences rapid growth in China, Southeast Asia, and India driven by consumer electronics and appliance production, while Japan and South Korea maintain leadership in high-precision applications. Government subsidies in China and India for domestic machine tool manufacturing are reshaping competitive dynamics, prompting both foreign and local OEMs to adapt their market strategies to these evolving regional landscapes.
This comprehensive research report examines key regions that drive the evolution of the 3-axis CNC Horizontal Machining Center market, offering deep insights into regional trends, growth factors, and industry developments that are influencing market performance.
- Americas
- Asia-Pacific
- Europe, Middle East & Africa
Competitive Landscape: Profiles and Strategies of Leading CNC Manufacturers
The competitive landscape is defined by a blend of global incumbents and regional specialists, each advancing distinct value propositions. DMG MORI Co., Ltd. leads with integrated digital ecosystems and high-rigidity machine platforms optimized for rapid pallet changes. Doosan Machine Tools Co., Ltd. emphasizes modular architectures that allow phased upgrades of controls and automation modules. Haas Automation, Inc. delivers user-friendly interfaces and cost-competitive solutions that appeal to small and medium enterprises. Hurco Companies, Inc. differentiates through adaptive control algorithms that simplify part programming and reduce setup times. Hyundai WIA Corporation and Kitamura Machinery Co., Ltd. offer robust mechanical designs suited for heavy cutting and multistage operations. Makino Milling Machine Co., Ltd. and Matsuura Machinery Corporation command market share in ultraprecision segments for aerospace and medical components. Mazak Corporation’s SmartBox IoT platform provides real-time performance monitoring and analytics, while Mori Seiki Co., Ltd. and Okuma Corporation excel in thermal stability and structural rigidity. Shenyang Machine Tool Co., Ltd. leverages state support to deliver competitively priced machines in emerging markets, and Tsugami Corporation specializes in micro-turning and high-precision milling for compact part fabrication. Collectively, these OEMs raise the bar for machine performance, service excellence, and digital integration.
This comprehensive research report delivers an in-depth overview of the principal market players in the 3-axis CNC Horizontal Machining Center market, evaluating their market share, strategic initiatives, and competitive positioning to illuminate the factors shaping the competitive landscape.
- DMG MORI Co., Ltd.
- Doosan Machine Tools Co., Ltd.
- Haas Automation, Inc.
- Hurco Companies, Inc.
- Hyundai WIA Corporation
- Kitamura Machinery Co., Ltd.
- Makino Milling Machine Co., Ltd.
- Matsuura Machinery Corporation
- Mazak Corporation
- Mori Seiki Co., Ltd.
- Okuma Corporation
- Shenyang Machine Tool Co., Ltd.
- Tsugami Corporation
Actionable Recommendations for CNC Horizontal Machining Center Leaders
To secure leadership in an increasingly complex market, manufacturers and end users must adopt a holistic strategy encompassing technology deployment, supply chain fortification, and customer-centric offerings. First, accelerate digital transformation by embedding IoT sensors, deploying machine-learning analytics, and utilizing digital twins to fine-tune cutting parameters, predict maintenance needs, and enhance overall equipment effectiveness. Second, build supply chain resilience through dual sourcing of critical castings and components, near-shoring of key processes, and strategic inventory buffering to offset tariff volatility and logistical disruptions. Third, design modular machine architectures that enable incremental integration of automation, robotic handling, and advanced controls, allowing customers to scale investments in line with production growth. Fourth, enrich service portfolios by bundling installation, preventive maintenance, and retrofit upgrades into subscription-based contracts that deliver predictable revenue and foster deeper customer relationships. Fifth, pursue sustainability objectives by integrating energy-efficient drives, closed-loop coolant systems, and eco-friendly materials that align with rigorous environmental standards. Sixth, forge strategic alliances with software developers, finance providers, and specialized training partners to offer turnkey solutions addressing technical, operational, and financial pain points. Finally, invest in workforce development through augmented reality training, certification programs, and cross-functional teams to ensure that technicians and operators can fully leverage advanced CNC capabilities. Implementing these recommendations in concert will position stakeholders for superior returns and enduring competitive advantage.
Explore AI-driven insights for the 3-axis CNC Horizontal Machining Center market with ResearchAI on our online platform, providing deeper, data-backed market analysis.
Ask ResearchAI anything
World's First Innovative Al for Market Research
Conclusion: Navigating Future Opportunities in 3-Axis Horizontal Machining
As manufacturing enters a new era of digital integration and supply chain complexity, 3-axis horizontal machining centers remain pivotal for high-precision, high-throughput operations. The synergy of advanced automation, predictive maintenance, and sustainable design has transformed these machines into dynamic, data-driven platforms capable of adapting to diverse production scenarios. By grasping the effects of tariff changes, regional growth patterns, and leading OEM strategies, decision-makers can align capital investments with strategic objectives. The segmentation, regional analysis, and recommendations presented here offer a clear roadmap for mitigating risks and exploiting market opportunities. Organizations that integrate mechanical robustness with digital agility, prioritize regulatory compliance, and deliver customer-centric service models will define the next wave of excellence. Maintaining vigilance over emerging technologies and evolving regulatory frameworks is essential for sustaining competitive positioning and achieving long-term success.
This section provides a structured overview of the report, outlining key chapters and topics covered for easy reference in our 3-axis CNC Horizontal Machining Center market comprehensive research report.
- Preface
- Research Methodology
- Executive Summary
- Market Overview
- Market Dynamics
- Market Insights
- Cumulative Impact of United States Tariffs 2025
- 3-axis CNC Horizontal Machining Center Market, by Product Type
- 3-axis CNC Horizontal Machining Center Market, by End-User Industries
- 3-axis CNC Horizontal Machining Center Market, by Technology
- 3-axis CNC Horizontal Machining Center Market, by Application Type
- 3-axis CNC Horizontal Machining Center Market, by Material Type
- 3-axis CNC Horizontal Machining Center Market, by Machine Size
- 3-axis CNC Horizontal Machining Center Market, by Service Type
- Americas 3-axis CNC Horizontal Machining Center Market
- Asia-Pacific 3-axis CNC Horizontal Machining Center Market
- Europe, Middle East & Africa 3-axis CNC Horizontal Machining Center Market
- Competitive Landscape
- ResearchAI
- ResearchStatistics
- ResearchContacts
- ResearchArticles
- Appendix
- List of Figures [Total: 30]
- List of Tables [Total: 683 ]
Next Steps: Secure Your In-Depth Machining Center Market Analysis Today
To gain deeper visibility into market dynamics, segmentation strategies, competitive positioning, and the implications of evolving tariff policies on 3-axis horizontal machining centers, reach out to Ketan Rohom, Associate Director of Sales & Marketing. Ketan will guide you through the full research report, answer your questions, and provide tailored insights aligned with your strategic priorities. Contact Ketan today to secure your copy of the market research, refine your investment decisions, optimize machine utilization, and position your organization for sustained growth and operational excellence.
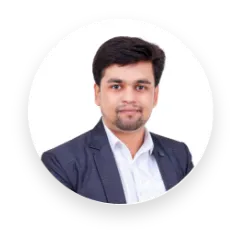
- When do I get the report?
- In what format does this report get delivered to me?
- How long has 360iResearch been around?
- What if I have a question about your reports?
- Can I share this report with my team?
- Can I use your research in my presentation?