Introduction to the Evolution of 3D AI AOI Wafer Inspection Systems
The evolution of wafer inspection has entered a defining era with the convergence of three-dimensional imaging, artificial intelligence, and automated optical inspection. Modern semiconductor devices demand micron-level precision across complex topographies, pushing legacy two-dimensional inspection methods to their limits. In response, 3D AI AOI wafer inspection systems leverage advanced metrology and optoelectronic components to deliver unparalleled defect detection, dimensional analysis, and process control. By integrating high-resolution sensors with machine learning algorithms, these systems not only identify minute anomalies on silicon, gallium arsenide, and sapphire substrates, but also classify and prioritize defects in real time.
This introduction sets the stage for understanding how emerging capabilities are reshaping quality assurance in semiconductor manufacturing. Through contact and non-contact metrology techniques-ranging from optical interferometry to ultrasonic scanning-manufacturers achieve tighter process tolerances and higher throughput. Meanwhile, AI-powered software platforms process vast volumes of inspection data to predict failure modes and optimize yield. As design rules shrink and wafer complexity grows, the imperative for robust, data-driven inspection solutions has never been stronger. Consequently, technology providers and end users alike are adopting integrated platforms that transcend traditional workflow boundaries, combining inline and offline metrology, cloud-based analytics, and robotic integration to meet the demands of next-generation device fabrication.
Key Transformative Shifts Shaping 3D AI AOI Wafer Inspection Landscape
Over the past decade, the semiconductor inspection landscape has undergone transformative shifts driven by several converging trends. First, the transition from 2D to 3D metrology has elevated defect detection capabilities: non-contact optical and ultrasonic techniques now reveal subsurface anomalies and three-dimensional structural deviations that were once invisible. This shift has been accompanied by the emergence of advanced optoelectronic components-LEDs, optical amplifiers, photodetectors-that enhance sensor sensitivity and throughput without compromising resolution.
Simultaneously, machine learning and AI-powered software have become integral to interpretation and decision-making. Pattern recognition algorithms and neural networks sift through terabytes of imaging data to classify defects, forecast process drifts, and recommend corrective actions, reducing manual intervention and accelerating time-to-resolution. Additionally, integration with collaborative robotics and autonomous handling systems has streamlined wafer transport, inspection, and data feedback loops, delivering a seamless inline-offline workflow.
Finally, deployment models have shifted toward hybrid cloud-edge architectures, enabling real-time processing at the fab floor while consolidating historical data in secure, scalable environments. Together, these shifts are redefining inspection standards, driving greater consistency, and empowering manufacturers to maintain yield targets amid increasing complexity.
Assessing the Cumulative Impact of United States Tariffs in 2025
The implementation of new tariff measures by the United States in 2025 has rippled across the global supply chain for wafer inspection systems. Heightened duties on critical components-such as high-precision optics, advanced sensors, and semiconductor wafers-have increased input costs for system manufacturers and their end users. As a result, suppliers are evaluating nearshoring strategies and alternative sourcing to mitigate duty burdens, while OEMs reassess pricing models to preserve margins without sacrificing quality.
At the same time, equipment makers and fabs are recalibrating capital expenditure plans in light of these added costs. Some have accelerated investments in automation to offset labor expenses and secure predictable throughput, thereby diluting the relative impact of tariffs over the equipment’s lifecycle. Others are leveraging strategic partnerships with local suppliers to establish duty-free assembly hubs and streamline customs processes. Meanwhile, risk management teams are monitoring regulatory changes to anticipate further adjustments in trade policy, ensuring that procurement cycles remain agile.
Although short-term project budgets may feel the pressure of increased duties, the long-term outlook favors resilient, geographically diversified supply networks and a shift toward modular system architectures that can accommodate component substitutions. In this context, the ability to adapt quickly to evolving trade environments has become a competitive differentiator for both solution providers and manufacturing end users.
Key Segmentation Insights Across Technology, Product, and Market Dimensions
A comprehensive segmentation analysis reveals nuanced market dynamics across multiple dimensions. Based on technology type, the market divides into 3D Metrology and Advanced Optoelectronics. Within 3D Metrology, contact metrology techniques remain vital for tactile measurements, while non-contact metrology proceeds via optical techniques-such as interferometry and confocal microscopy-and ultrasonic scanning for subsurface inspection. Concurrently, the advanced optoelectronics segment incorporates light-emitting diodes for uniform illumination, optical amplifiers to boost signal strength, and photodetectors to capture high-speed imaging data.
In terms of product type, the market differentiates between fully automated optical inspection systems that deliver end-to-end wafer handling and inspection, and manual optical inspection systems suited for lab-scale and low-volume fabs. Wafer types under inspection span gallium arsenide for high-frequency applications, sapphire for LED manufacturing, and silicon, which continues to dominate mainstream semiconductor production.
Examining end-user verticals, aerospace and defense sectors demand rigorous inspection protocols to ensure reliability, consumer electronics manufacturers require rapid cycle times to support high-volume device assembly, and the healthcare industry-encompassing diagnostic platforms and medical device production-emphasizes traceability and regulatory compliance. Semiconductor manufacturing end users focus on minimizing yield loss through precise defect classification and auto-repair workflows.
Application segmentation highlights 3D reconstruction of wafer topography, automated defect inspection, dimensional metrology for critical feature measurement, and advanced pattern recognition for overlay and circuit integrity checks. Components are bifurcated into hardware-3D cameras and laser scanners-and software, which includes AI-powered analytics suites and pattern recognition algorithms. Workflow preferences split between inline metrology embedded in fab lines and offline metrology stations for targeted analysis. Deployment models range from cloud-based solutions offering scalable data management to on-premise installations ensuring data sovereignty. Finally, integration modes encompass collaborative systems-spanning autonomous platforms and cobots-and fully robotic integration for high-throughput, hands-free operation.
This comprehensive research report categorizes the 3D AI AOI Wafer Inspection System market into clearly defined segments, providing a detailed analysis of emerging trends and precise revenue forecasts to support strategic decision-making.
- Technology Type
- Product Type
- Wafer Type
- End User
- Application
- Component
- Workflow
- Deployment Model
- Integration
Key Regional Insights Driving Adoption in Major Geographies
Regional nuances play a pivotal role in shaping the adoption and evolution of 3D AI AOI wafer inspection solutions. In the Americas, robust semiconductor manufacturing hubs in the United States and emerging fabs in Mexico drive demand for high-precision systems that deliver rapid throughput and yield improvement. Strong government incentives and partnerships with research institutions accelerate technology transfer and pilot deployments.
Turning to Europe, Middle East & Africa, inspection requirements are influenced by stringent regulatory frameworks and a growing emphasis on sustainable manufacturing. Localized production of gallium arsenide devices for defense applications and sapphire-based LED components for automotive lighting fosters demand for adaptable inspection platforms. Moreover, regional collaborations geared toward Industry 4.0 integration spur investment in cloud-edge hybrid systems that optimize data analytics and resource utilization.
In the Asia-Pacific region, leading wafer fabrication centers in Taiwan, South Korea, Japan, and China underpin the largest share of global capacity. High-volume consumer electronics assembly and the rapid adoption of next-generation node technologies amplify the need for advanced defect detection and automated metrology. The prevalence of silicon wafer production, coupled with rising interest in novel substrate materials, sustains a dynamic ecosystem for inspection equipment providers and end users alike.
This comprehensive research report examines key regions that drive the evolution of the 3D AI AOI Wafer Inspection System market, offering deep insights into regional trends, growth factors, and industry developments that are influencing market performance.
- Americas
- Asia-Pacific
- Europe, Middle East & Africa
Key Company Insights: Leading Innovators in Wafer Inspection Technology
The competitive landscape in the 3D AI AOI wafer inspection market features a diverse array of specialized technology providers and established semiconductor equipment manufacturers. Applied Materials, Inc. remains at the forefront with its integrated platform that couples metrology hardware and AI-driven analytics. Camtek Ltd. distinguishes itself through advanced X-ray and optical inspection hybrid solutions, while Cohu, Inc. focuses on high-speed, high-resolution cameras tailored for throughput-critical applications.
Hitachi High-Tech Corporation leverages decades of experience in electron microscopy and optoelectronics to deliver precision inspection modules, and KLA Corporation’s deep learning frameworks augment its legacy inspection offerings. Mirtec Corp. specializes in turnkey automated optical inspection systems for circuit board and wafer analysis, whereas Nordson Corporation applies its expertise in precision dispensing to support advanced metrology workflows.
Onto Innovation Inc. and Orbotech (A KLA Company) continuously innovate in pattern recognition algorithms and photodetector technologies. Rudolph Technologies, Inc. integrates adaptive inspection lanes with real-time yield management solutions, while Semiconductor Technologies & Instruments (STI) brings modular, cost-effective inspection cells to niche markets. Finally, Topcon Corporation’s laser scanning expertise enhances non-contact metrology accuracy, solidifying its role as a key player in the evolving ecosystem.
This comprehensive research report delivers an in-depth overview of the principal market players in the 3D AI AOI Wafer Inspection System market, evaluating their market share, strategic initiatives, and competitive positioning to illuminate the factors shaping the competitive landscape.
- Applied Materials, Inc.
- Camtek Ltd.
- Cohu, Inc.
- Hitachi High-Tech Corporation
- KLA Corporation
- Mirtec Corp.
- Nordson Corporation
- Onto Innovation Inc.
- Orbotech (A KLA Company)
- Rudolph Technologies, Inc.
- Semiconductor Technologies & Instruments (STI)
- Topcon Corporation
Actionable Recommendations for Industry Leaders in Wafer Inspection
Industry leaders can seize competitive advantages by adopting a strategic, multi-pronged approach. First, invest in modular, scalable architectures that support rapid sensor upgrades and AI software enhancements, enabling swift adaptation to new wafer materials and process nodes. Second, diversify supply chains by qualifying multiple sources for critical optoelectronic components and high-precision optics, thereby mitigating the impact of geopolitical tensions and tariff fluctuations.
Third, embrace hybrid deployment models: on-premise systems ensure low-latency feedback for inline inspection, while secure cloud platforms consolidate historical data for advanced analytics and predictive modeling. Fourth, pursue partnerships with collaborative robotics integrators to automate wafer handling and reduce manual errors, increasing throughput and yield consistency. Fifth, develop domain-specific AI models that incorporate defect libraries unique to end-user applications-whether aerospace-grade substrates or medical device assembly-to enhance detection accuracy and classification speed.
Sixth, implement continuous training programs for process engineers and maintenance teams, ensuring proficiency in AI software tuning, sensor calibration, and workflow optimization. Finally, align product roadmaps with emerging industry standards and regulatory requirements, positioning inspection offerings as compliant, future-proof solutions capable of addressing the stringent demands of next-generation semiconductor fabrication.
Explore AI-driven insights for the 3D AI AOI Wafer Inspection System market with ResearchAI on our online platform, providing deeper, data-backed market analysis.
Ask ResearchAI anything
World's First Innovative Al for Market Research
Conclusion: Strategic Takeaways for 3D AI AOI Wafer Inspection Success
As high-density integration and advanced node manufacturing become standard, 3D AI AOI wafer inspection will remain a cornerstone of process control and yield optimization. Manufacturers must proactively integrate multi-dimensional metrology, AI-driven analytics, and flexible deployment options to stay ahead of escalating complexity. The confluence of hardware innovation-from ultrasonic scanning to laser-based imaging-and software advancements in neural network classifiers ensures that inspection systems will continue to evolve in capability and efficiency.
Strategic segmentation insights highlight the importance of tailoring solutions to specific wafer types, applications, and end-user verticals. Regional dynamics emphasize the need for localized support, compliance with diverse regulatory landscapes, and alignment with national semiconductor initiatives. Meanwhile, competitive intelligence underscores the advantage of leveraging partnerships and continuous R&D investment to differentiate in a crowded marketplace.
Ultimately, success hinges on balancing high-throughput inspection demands with the flexibility to address emerging materials and novel device architectures. By adopting a roadmap focused on modularity, AI sophistication, and collaborative integration, stakeholders can drive sustained improvements in yield, cost-efficiency, and time-to-market for the next generation of semiconductor technologies.
This section provides a structured overview of the report, outlining key chapters and topics covered for easy reference in our 3D AI AOI Wafer Inspection System market comprehensive research report.
- Preface
- Research Methodology
- Executive Summary
- Market Overview
- Market Dynamics
- Market Insights
- Cumulative Impact of United States Tariffs 2025
- 3D AI AOI Wafer Inspection System Market, by Technology Type
- 3D AI AOI Wafer Inspection System Market, by Product Type
- 3D AI AOI Wafer Inspection System Market, by Wafer Type
- 3D AI AOI Wafer Inspection System Market, by End User
- 3D AI AOI Wafer Inspection System Market, by Application
- 3D AI AOI Wafer Inspection System Market, by Component
- 3D AI AOI Wafer Inspection System Market, by Workflow
- 3D AI AOI Wafer Inspection System Market, by Deployment Model
- 3D AI AOI Wafer Inspection System Market, by Integration
- Americas 3D AI AOI Wafer Inspection System Market
- Asia-Pacific 3D AI AOI Wafer Inspection System Market
- Europe, Middle East & Africa 3D AI AOI Wafer Inspection System Market
- Competitive Landscape
- ResearchAI
- ResearchStatistics
- ResearchContacts
- ResearchArticles
- Appendix
- List of Figures [Total: 34]
- List of Tables [Total: 721 ]
Call to Action: Engage with Associate Director Ketan Rohom for Report Acquisition
For detailed guidance tailored to your organization’s objectives and to access the full market research report, reach out to Ketan Rohom, Associate Director, Sales & Marketing. He will guide you through the findings and discuss how these insights can inform your strategic planning and technology investments.
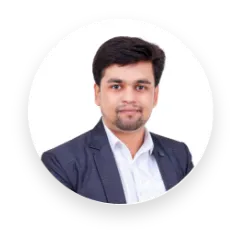
- When do I get the report?
- In what format does this report get delivered to me?
- How long has 360iResearch been around?
- What if I have a question about your reports?
- Can I share this report with my team?
- Can I use your research in my presentation?