Introduction: Navigating the 3D Manufacturing Simulation Software Ecosystem
The accelerating complexity of modern manufacturing demands precision, agility, and foresight. 3D manufacturing simulation software has emerged as a cornerstone technology that empowers organizations to visualize, validate, and optimize production processes before committing resources to physical prototypes. By creating virtual replicas of manufacturing environments, engineers and decision-makers can identify bottlenecks, validate design changes, and anticipate quality issues without halting the production line.
This report offers a comprehensive exploration of the 3D manufacturing simulation software ecosystem, covering the latest technological advances, market segmentation, geopolitical influences, regional variations, and leading industry players. We begin by mapping the transformative shifts that are redefining how digital twins, additive manufacturing, and AI-driven analytics converge to drive operational excellence. Next, we assess the cumulative impact of recently enacted tariffs in the United States, highlighting how cost structures and supply-chain strategies must adapt. A detailed segmentation analysis reveals the multitude of components, technologies, deployment models, industries, applications, software types, functionalities, and business models that constitute this dynamic market. Regional insights illuminate adoption patterns across the Americas, Europe, Middle East & Africa, and Asia-Pacific. We then profile the companies at the forefront of innovation, charting competitive landscapes and partnership ecosystems. Finally, actionable recommendations will guide industry leaders in crafting resilient, future-ready strategies.
By synthesizing these elements into a cohesive narrative, this executive summary equips experts and decision-makers with the clarity and confidence required to leverage 3D manufacturing simulation software as a strategic differentiator.
Transformative Technological Shifts Reshaping 3D Manufacturing Simulation
Manufacturing simulation has evolved beyond isolated analyses into an integrated, data-driven discipline that underpins Industry 4.0 initiatives. A primary shift is the emergence of digital twin platforms that synchronize real-time sensor data from the factory floor with high-fidelity virtual models, enabling continuous monitoring and predictive maintenance. Concurrently, advances in computational fluid dynamics, finite element analysis, and discrete event simulation are converging into unified environments where multiphysics simulations deliver holistic insights.
Artificial intelligence and machine learning algorithms now power automated design optimization, recommending material selections and geometries that meet cost, weight, and performance targets. The rise of cloud computing-and specifically hybrid cloud configurations-has democratized access to high-performance computing resources, allowing organizations of all sizes to run complex simulations without heavy capital expenditure on dedicated servers.
Interoperability has become a critical enabler, with open APIs and standard data formats facilitating seamless integration between simulation suites and enterprise systems such as PLM, ERP, and MES. Moreover, virtual reality and augmented reality interfaces are extending simulation’s reach into operator training and collaborative design review, further blurring the boundary between virtual and physical workflows.
These technological shifts are redefining product development cycles, accelerating time-to-market while enhancing quality control. As organizations embrace these innovations, they position themselves to respond rapidly to changing customer demands, supply-chain disruptions, and sustainability imperatives.
Assessing the Cumulative Impact of United States Tariffs in 2025
Beginning in 2025, a series of additional tariff measures in the United States has introduced new complexities into the global supply chain for both software and hardware components integral to 3D manufacturing simulation. These tariffs apply not only to imported simulation software licenses packaged on physical media but also to key server components and specialized peripherals sourced from overseas.
As a result, organizations face increased total cost of ownership for on-premises deployments, prompting many to reassess their infrastructure strategies. Cloud-native providers have leveraged this moment to highlight the cost predictability and scalability of their subscription and pay-per-use models, though some caution remains over potential future trade tensions affecting data sovereignty and cross-border data flows.
Tariff-induced cost inflation is also driving a resurgence of regional development centers and localized software packaging to mitigate import duties. Several vendors have announced strategic partnerships with domestic distributors to bundle hardware and software under a single tariff classification, offering clients a workaround for escalating import fees.
These shifts underscore the importance of flexible procurement strategies, scenario planning for supply disruptions, and close collaboration between procurement, IT, and engineering teams. Organizations that proactively adapt to this evolving trade environment will secure a competitive edge by stabilizing budget forecasts and maintaining uninterrupted access to critical simulation capabilities.
Key Segmentation Insights Driving Market Dynamics
A multi-dimensional segmentation framework reveals the nuanced landscape of 3D manufacturing simulation software. The market component dimension draws a clear line between services-such as consulting, custom integration, and training-and the core software platforms that power simulation workflows. Within the technology dimension, a spectrum of specialized modules addresses distinct analytical needs, from computational fluid dynamics for thermal and fluid flow analysis to finite element analysis for structural integrity; discrete event simulation for process optimization; and digital twin platforms that encapsulate real-time system behavior.
Deployment options accommodate diverse IT strategies. On-premises installations remain vital for organizations with stringent data-privacy requirements or legacy infrastructure, while cloud solutions-available in public, private, and hybrid configurations-deliver rapid scalability and lower upfront investment. End-user industries span aerospace and defense to healthcare, with automotive manufacturers leaning on aftermarket and original equipment manufacturer applications to refine designs and validate performance under dynamic conditions.
Applications reinforce the value proposition: workflow automation within process optimization reduces manual intervention, while 3D modeling and prototype simulation accelerate product design and development. Performance analysis and virtual testing streamline testing and quality control, and immersive operator training and virtual reality exercises enhance workforce readiness. Software types range from add-on modules that extend existing platforms to integrated suites offering end-to-end functionality; plugin solutions tailored to CAD, CAE, or CAM tools; and standalone products optimized for specific tasks.
Functional domains cover everything from design and analysis to material handling, production planning and scheduling, robotics simulation, and supply-chain modeling. Business models reflect evolving customer preferences: traditional perpetual licensing coexists with enterprise licensing agreements, subscription licensing that bundles updates and support, and pay-per-use schemes that align costs with consumption.
This comprehensive research report categorizes the 3D Manufacturing Simulation Software market into clearly defined segments, providing a detailed analysis of emerging trends and precise revenue forecasts to support strategic decision-making.
- Component
- Technology
- Deployment Type
- End-User Industry
- Application
- Software Type
- Functionality
- Business Model
Regional Insights Highlight Variances in Adoption and Growth
Regional variation in 3D manufacturing simulation adoption underscores disparate maturity levels and strategic priorities. In the Americas, early adopters in automotive and aerospace have championed digital twins and high-fidelity multiphysics simulations, supported by a robust ecosystem of local service providers and research institutions. This region continues to lead in advanced implementations, particularly where additive manufacturing is reshaping supply chains.
Europe, the Middle East & Africa exhibits a strong focus on regulatory compliance and sustainability. Automotive and industrial machinery sectors drive demand for simulation software that can validate emissions reduction strategies and optimize energy efficiency. Government incentives for digital transformation and cross-border collaboration in the European Union further bolster adoption, even as geopolitical uncertainties prompt risk-mitigation planning.
In Asia-Pacific, rapid industrialization and the pursuit of manufacturing excellence have fueled investments in both cloud-based and on-premises simulation solutions. Electronics and energy utilities leverage simulation to accelerate new product introductions and refine power-grid infrastructures. Cost-sensitive organizations often gravitate toward subscription and pay-per-use models, while government-backed initiatives in countries such as China and India promote indigenous development of digital twin technologies.
This comprehensive research report examines key regions that drive the evolution of the 3D Manufacturing Simulation Software market, offering deep insights into regional trends, growth factors, and industry developments that are influencing market performance.
- Americas
- Asia-Pacific
- Europe, Middle East & Africa
Leading Companies Shaping the 3D Simulation Software Landscape
The competitive landscape is led by a group of established technology providers and innovative challengers. Altair Engineering focuses on multiphysics optimization and high-performance computing, enabling engineers to explore design trade-offs rapidly. Ansys remains a leader in physics-based simulation, offering deep capabilities across fluid, structural, and electromagnetic domains. Autodesk integrates simulation within a broad CAD portfolio, simplifying workflows for product designers.
Bentley Systems extends its expertise in infrastructure digital twins to manufacturing environments, while Dassault Systèmes delivers end-to-end PLM and virtual twin experiences for complex assemblies. ESI Group specializes in virtual prototyping with a strong presence in crash simulation and material characterization. Hexagon AB combines metrology with simulation to close the loop between physical measurements and virtual models.
iBASEt integrates manufacturing execution with digital manufacturing planning, and PTC leverages IoT connectivity in its simulation-driven service offerings. Siemens AG weaves simulation into its NX and Simcenter platforms, fostering concurrent engineering. Simio LLC’s discrete event simulation excels at process flow analysis, and Visual Components Oy brings intuitive 3D production flow simulation to factory planners.
These companies differentiate through partnerships, vertical-specific solutions, and investments in AI, cloud, and XR technologies, creating a dynamic ecosystem in which collaboration and healthy competition spur continuous innovation.
This comprehensive research report delivers an in-depth overview of the principal market players in the 3D Manufacturing Simulation Software market, evaluating their market share, strategic initiatives, and competitive positioning to illuminate the factors shaping the competitive landscape.
- Altair Engineering Inc.
- Ansys, Inc.
- Autodesk, Inc.
- Bentley Systems, Incorporated
- Dassault Systèmes SA
- ESI Group
- Hexagon AB
- iBASEt
- PTC Inc.
- Siemens AG
- Simio LLC
- Visual Components Oy
Actionable Recommendations for Industry Leaders
To capitalize on the 3D manufacturing simulation opportunity, industry leaders should pursue a multi-pronged strategy. First, integrate digital twin initiatives with IoT and analytics platforms to establish a continuous feedback loop between virtual models and operational data. Second, adopt hybrid cloud architectures that balance data security with on-demand scalability-this approach mitigates the risks posed by tariff-induced cost increases for on-premises hardware.
Third, embed AI-driven optimization within simulation workflows to automate design iterations and reveal performance gains that might otherwise be overlooked. Fourth, cultivate strategic alliances with specialized vendors to augment core simulation capabilities and accelerate time-to-value. Fifth, standardize data formats and APIs to ensure seamless interoperability across PLM, ERP, MES, and emerging manufacturing technologies such as additive and robotics simulation.
Sixth, invest in workforce upskilling programs, leveraging virtual reality and gamified training modules to shorten the learning curve and foster a simulation--centric culture. Seventh, incorporate sustainability metrics into simulation scenarios to quantify environmental impact and support compliance with evolving regulations. Finally, embed cybersecurity protocols at every layer of the digital thread to safeguard intellectual property and maintain operational continuity.
Explore AI-driven insights for the 3D Manufacturing Simulation Software market with ResearchAI on our online platform, providing deeper, data-backed market analysis.
Ask ResearchAI anything
World's First Innovative Al for Market Research
Conclusion: Harnessing Simulation for Competitive Advantage
3D manufacturing simulation software has transitioned from a niche engineering tool into a strategic asset that drives innovation, efficiency, and resilience. By embracing digital twins, advanced analytics, and cloud-native architectures, organizations can de-risk product development, optimize resource utilization, and elevate quality standards.
The convergence of AI, immersive technologies, and multiphysics simulation promises to unlock new avenues for smart manufacturing and product personalization. As tariffs and geopolitical shifts introduce fresh challenges, the ability to adapt procurement, deployment, and partnership strategies will separate market leaders from followers.
Ultimately, the organizations that weave simulation deeply into their operational fabric will realize accelerated time-to-market, reduced development costs, and a sustainable competitive advantage in an increasingly complex manufacturing landscape.
This section provides a structured overview of the report, outlining key chapters and topics covered for easy reference in our 3D Manufacturing Simulation Software market comprehensive research report.
- Preface
- Research Methodology
- Executive Summary
- Market Overview
- Market Dynamics
- Market Insights
- Cumulative Impact of United States Tariffs 2025
- 3D Manufacturing Simulation Software Market, by Component
- 3D Manufacturing Simulation Software Market, by Technology
- 3D Manufacturing Simulation Software Market, by Deployment Type
- 3D Manufacturing Simulation Software Market, by End-User Industry
- 3D Manufacturing Simulation Software Market, by Application
- 3D Manufacturing Simulation Software Market, by Software Type
- 3D Manufacturing Simulation Software Market, by Functionality
- 3D Manufacturing Simulation Software Market, by Business Model
- Americas 3D Manufacturing Simulation Software Market
- Asia-Pacific 3D Manufacturing Simulation Software Market
- Europe, Middle East & Africa 3D Manufacturing Simulation Software Market
- Competitive Landscape
- ResearchAI
- ResearchStatistics
- ResearchContacts
- ResearchArticles
- Appendix
- List of Figures [Total: 32]
- List of Tables [Total: 689 ]
Call to Action: Engage with Ketan Rohom for Comprehensive Market Intelligence
Ready to transform your manufacturing processes with deep market intelligence? Reach out to Ketan Rohom, Associate Director, Sales & Marketing, to explore bespoke insights and secure access to the full market research report. Gain the data-driven guidance you need to stay ahead of technological shifts, regulatory changes, and competitive dynamics. Contact Ketan today to empower your organization’s 3D manufacturing simulation strategy.
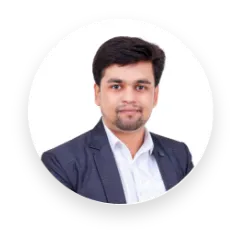
- When do I get the report?
- In what format does this report get delivered to me?
- How long has 360iResearch been around?
- What if I have a question about your reports?
- Can I share this report with my team?
- Can I use your research in my presentation?