Unveiling the Critical Role of 3D Printed High Strength Aluminum Powder in Revolutionizing Manufacturing Across Multiple Industrial Verticals
Three-dimensional printing of high strength aluminum powder represents a transformative frontier in advanced manufacturing, combining the lightweight characteristics of aluminum alloys with superior mechanical performance. As demand for precision-engineered metal components escalates across aerospace, automotive, industrial, and medical industries, this powder-based additive technology underpins initiatives to reduce part complexity, accelerate prototyping cycles, and optimize structural integrity. Leveraging alloys such as AlSi10Mg, AlSi12, and AlSi7Mg, manufacturers achieve a compelling balance of ductility, strength, and thermal stability, thereby enabling weight reduction and performance gains that were previously unattainable through traditional subtractive methods.
Moreover, the intrinsic layer-by-layer construction inherent to binder jetting, powder bed fusion, and direct energy deposition allows for intricate geometries and consolidated assemblies that minimize secondary machining steps. This capability invites novel design paradigms, particularly in high-stress applications like engine components and structural airframes, where material anisotropy can be precisely managed through tailored build orientations and heat treatments. Consequently, investment in high strength aluminum powder today signals a strategic commitment to next-generation manufacturing paradigms where customization, speed, and performance coalesce to redefine product lifecycles.
Exploring the Emerging Technological and Market Dynamics Driving Disruptive Shifts in High Strength Aluminum Powder Additive Manufacturing
Recent years have witnessed a slew of transformative shifts reshaping the landscape of high strength aluminum powder utilization. First and foremost, advancements in powder atomization techniques and spheroidization processes have significantly enhanced powder flowability and layer deposition uniformity, directly elevating build quality and reducing porosity. Simultaneously, enhancements in laser modulation algorithms and electron beam source controls have improved layer fusion consistency in powder bed fusion and direct energy deposition systems, enabling the production of components with fatigue characteristics that rival those manufactured by casting or forging.
In parallel, the convergence of digital twins, in situ monitoring, and artificial intelligence-driven defect detection tools has ushered additive manufacturing into the realm of Industry 4.0. Manufacturers are now able to calibrate process parameters in real time, ensuring statistical process control within highly regulated sectors. Furthermore, the increasing adoption of sustainable manufacturing frameworks underscores a shift toward powder recycling loops and closed-loop material management, which mitigate waste and reduce dependency on primary feedstock. Collectively, these technological and operational advances herald a new era of precision, repeatability, and cost-effectiveness for high strength aluminum powder applications in aerospace, automotive prototyping, industrial tooling, and medical device fabrication.
Assessing the Layered Effects of 2025 United States Tariffs on High Strength Aluminum Powder Supply Chains and Industry Competitiveness
The introduction of a new tranche of United States tariffs in 2025 has exerted a multifaceted impact on high strength aluminum powder supply chains and cost structures. Specifically, increased import duties on aluminum feedstock and finished powder products have elevated landed material costs for domestic additive manufacturing service providers and OEMs reliant on international powder producers. In response, many stakeholders have reevaluated their sourcing strategies, exploring nearshoring options and diversifying supplier networks to mitigate exposure to tariff fluctuations.
Additionally, these elevated tariffs have prompted a strategic shift toward domestic alloy production and investment in localized powder atomization facilities. While capital expenditures have climbed, this move promises greater supply chain resilience and reduced lead times for critical aerospace and defense projects that demand stringent certification. Concurrently, research institutions and service bureaus are collaborating more deeply with metal powder specialists to qualify alternative alloy compositions that can circumvent tariff classifications without compromising mechanical performance. Thus, the cumulative effect of 2025’s tariff changes has been to accelerate regional supply chain realignment, foster innovation in alloy engineering, and stimulate investment in advanced powder production capabilities.
Deciphering Market Segmentation Patterns by Application Product Type Technology End User and Sales Channel to Illuminate Strategic Growth Pathways
Comprehensive market segmentation reveals nuanced insights across multiple dimensions, starting with application categories that encompass aerospace, automotive, industrial, and medical. Within aerospace, engine components, interior parts, and structural assemblies each demand distinct powder properties and post-processing protocols, whereas automotive segments such as body parts, engine components, and functional prototypes prioritize rapid turnaround and cost efficiency. Industrial consumers leverage high strength aluminum powder for fixtures, molds, and tooling that benefit from localized reinforcement, and medical innovators harness implants, prosthetics, and surgical instruments to deliver bespoke solutions with biocompatible finish treatments.
Turning to product types, AlSi10Mg remains a widely adopted workhorse alloy known for its versatile mechanical profile, while AlSi12 offers superior creep resistance and thermal stability for high-heat environments. AlSi7Mg balances ductility and yield strength, making it a preferred choice for applications requiring moderate loads and fine feature resolution. In terms of manufacturing technology, binder jetting permits high-volume production with minimal thermal distortion, direct energy deposition affords in-process alloy customization and repair capabilities, and powder bed fusion enables intricate geometries with tight tolerances.
Examining end user classifications, OEMs drive large-scale adoption through integrated manufacturing lines, research institutions spearhead exploratory development and material characterization, and service bureaus-ranging from tier 1 global operators to tier 2 regional specialists-offer on-demand production services that cater to both prototyping and low-volume series. Finally, distribution channels span direct sales channels for strategic accounts, traditional distributor networks for broad market outreach, and online platforms that include manufacturer websites and third-party marketplaces, each tailoring customer engagement and order fulfillment to specific buyer preferences.
This comprehensive research report categorizes the 3D Printed High Strength Aluminum Powder market into clearly defined segments, providing a detailed analysis of emerging trends and precise revenue forecasts to support strategic decision-making.
- Application
- Product Type
- Technology
- End User
- Sales Channel
Unraveling Regional Demand Trends for High Strength Aluminum Powder across Americas EMEA and Asia-Pacific Manufacturing Ecosystems
Regional dynamics highlight divergent adoption rates and strategic priorities across the Americas, Europe Middle East & Africa, and Asia-Pacific zones. In the Americas, the presence of established aerospace and defense ecosystems accelerates development of qualification protocols for high strength aluminum powder, while localized regulatory frameworks and environmental mandates drive investments in closed-loop powder recycling. Concurrently, domestic OEMs and service bureaus in North America emphasize speed to market and supply chain security, investing in nearshore production sites that reduce lead times for critical components.
Across Europe Middle East & Africa, the confluence of stringent certification standards and cross-border trade agreements shapes a landscape where collaborative research consortia drive standardization of powder specifications. European service providers lead in integrating advanced post-processing techniques, and emerging markets in the Middle East are investing in additive manufacturing hubs to diversify industrial capabilities. Meanwhile, EMEA stakeholders exhibit a growing preference for sustainable materials management, tightening environmental compliance by optimizing powder reuse and energy-efficient build processes.
In the Asia-Pacific region, robust industrial automation infrastructure and aggressive R&D incentives have spurred widespread adoption of binder jetting and direct energy deposition platforms. Major markets such as China, Japan, and South Korea focus on vertical integration of powder production and component manufacturing, leveraging scale economies to offer competitively priced parts. Additionally, regional governments are offering subsidies for high strength aluminum powder research, accelerating pilot programs that explore novel alloy blends and digital process controls.
This comprehensive research report examines key regions that drive the evolution of the 3D Printed High Strength Aluminum Powder market, offering deep insights into regional trends, growth factors, and industry developments that are influencing market performance.
- Americas
- Europe, Middle East & Africa
- Asia-Pacific
Highlighting Major Industry Players Innovating in High Strength Aluminum Powder Production Technologies and Collaborative Ecosystems
Key industry players are at the forefront of advancing high strength aluminum powder production, forging collaborations and refining proprietary processes to maintain competitive positioning. Leading metallurgy firms have introduced next-generation atomization systems that produce powders with ultra-low oxygen levels, ensuring superior flow characteristics and reduced porosity in additively manufactured parts. Concurrently, equipment OEMs have expanded service offerings to include in situ process monitoring modules powered by machine learning algorithms, enabling real-time defect detection during powder bed fusion and direct energy deposition operations.
Additionally, strategic partnerships between powder producers and aerospace OEMs have facilitated the qualification of high strength aluminum alloys for critical applications, resulting in joint certification projects that streamline approval timelines. Collaborative research initiatives between technology providers and medical device manufacturers are also exploring novel post-processing protocols that enhance surface finish and biocompatibility for implants and surgical tools. As market fragmentation intensifies, vertically integrated firms are leveraging global footprints to offer end-to-end solutions-from powder supply and process training to component validation and lifecycle support-thereby creating differentiated value propositions in an increasingly competitive landscape.
This comprehensive research report delivers an in-depth overview of the principal market players in the 3D Printed High Strength Aluminum Powder market, evaluating their market share, strategic initiatives, and competitive positioning to illuminate the factors shaping the competitive landscape.
- Höganäs AB
- GKN Powder Metallurgy Holdings B.V.
- Carpenter Technology Corporation
- AP&C Canada Inc.
- Rio Tinto Metal Powders
- Sandvik AB
- TLS Technik GmbH & Co. Spezialpulver KG
- LPW Technology Ltd.
- ECKA Granules GmbH
- Metalysis Ltd.
Formulating Strategic Roadmaps for Industry Leaders to Capitalize on High Strength Aluminum Powder Opportunities and Mitigate Emerging Challenges
Leaders seeking to harness the full potential of high strength aluminum powder should prioritize strategic alloy development initiatives aimed at tailoring material properties for application-specific demands. By establishing dedicated R&D pipelines that explore variations of AlSi10Mg, AlSi12, and AlSi7Mg, organizations can optimize performance metrics such as yield strength, fatigue resistance, and thermal conductivity. In parallel, investing in advanced process control technologies-such as in situ sensor networks and closed-loop feedback systems-will ensure consistent build quality and enable rapid certification across regulated sectors.
Forging deeper partnerships with OEMs, research institutions, and tiered service bureaus can also accelerate the path from prototype to production. Collaborative efforts to standardize powder specifications and streamline qualification protocols will reduce barriers to entry, while jointly developed training programs can build workforce expertise in powder handling and machine operation. Furthermore, diversifying supply chains through a balanced mix of domestic and regional powder sources will mitigate tariff risks and enhance supply agility.
Finally, embedding sustainability principles across the powder lifecycle-through robust recycling initiatives and energy-efficient atomization methods-will not only align with evolving environmental regulations but also yield cost benefits over time. By adopting these integrated strategies, industry leaders can position themselves at the forefront of additive manufacturing innovation, capturing new market segments and driving long-term growth.
Outlining Rigorous Research Framework and Analytical Approaches Behind the Comprehensive Study of High Strength Aluminum Powder Market Dynamics
The research underpinning this comprehensive analysis employed a multi-pronged methodology designed to ensure rigor and relevance. Initial desk research involved the review of peer-reviewed journals, patent filings, technical white papers, and regulatory documentation to establish a foundational understanding of material properties, production technologies, and industry standards. Building upon this groundwork, primary interviews were conducted with representatives from OEMs, powder manufacturers, service bureaus, and research institutions to obtain insights into current adoption trends and pain points within real-world operations.
Quantitative data collection was complemented by a detailed segmentation framework that categorized market dynamics by application, product type, manufacturing technology, end user, and sales channel. Triangulation of these segments with regional demand patterns provided a holistic view of growth drivers and constraints. Additionally, expert panels comprising metallurgists, additive manufacturing engineers, and supply chain strategists validated key findings and contributed scenario-based analysis to assess the impact of regulatory shifts and tariff changes.
Finally, the integration of qualitative perspectives with quantitative data sets enabled the development of actionable recommendations grounded in both empirical evidence and practitioner experience. This layered approach ensures that the resultant insights accurately reflect current market conditions and anticipate near-term industry evolutions.
Explore AI-driven insights for the 3D Printed High Strength Aluminum Powder market with ResearchAI on our online platform, providing deeper, data-backed market analysis.
Ask ResearchAI anything
World's First Innovative Al for Market Research
Synthesizing Core Findings on Technological Adoption Regulatory Impacts and Strategic Imperatives for High Strength Aluminum Powder Stakeholders
In conclusion, the landscape of high strength aluminum powder additive manufacturing is characterized by rapid technological evolution, strategic realignments driven by regulatory and tariff pressures, and diverse market segmentation insights that inform targeted growth strategies. Advancements in powder production and additive processes have unlocked new possibilities for lightweight, high-performance components, while the introduction of tariffs in 2025 has catalyzed supply chain reorientation and investments in localized production capacities.
Segmentation analysis underscores the importance of tailoring alloy selection, technology deployment, and distribution models to specific application needs-from aerospace structural components to medical implants-while regional insights reveal varied adoption curves across the Americas, EMEA, and Asia-Pacific. Competitive dynamics among leading producers and equipment OEMs further highlight the imperative to innovate in both materials science and digital process control. Ultimately, the most successful organizations will be those that integrate strategic alloy development, advanced qualification protocols, and collaborative partnerships into a cohesive roadmap that addresses emerging challenges and seizes new market opportunities.
This section provides a structured overview of the report, outlining key chapters and topics covered for easy reference in our 3D Printed High Strength Aluminum Powder market comprehensive research report.
- Preface
- Research Methodology
- Executive Summary
- Market Overview
- Market Dynamics
- Market Insights
- Cumulative Impact of United States Tariffs 2025
- 3D Printed High Strength Aluminum Powder Market, by Application
- 3D Printed High Strength Aluminum Powder Market, by Product Type
- 3D Printed High Strength Aluminum Powder Market, by Technology
- 3D Printed High Strength Aluminum Powder Market, by End User
- 3D Printed High Strength Aluminum Powder Market, by Sales Channel
- Americas 3D Printed High Strength Aluminum Powder Market
- Europe, Middle East & Africa 3D Printed High Strength Aluminum Powder Market
- Asia-Pacific 3D Printed High Strength Aluminum Powder Market
- Competitive Landscape
- ResearchAI
- ResearchStatistics
- ResearchContacts
- ResearchArticles
- Appendix
- List of Figures [Total: 28]
- List of Tables [Total: 1006 ]
Engage with Ketan Rohom to Acquire In-Depth Market Research Insights and Drive Competitive Advantage in High Strength Aluminum Powder
We invite industry decision-makers to engage directly with Ketan Rohom (Associate Director, Sales & Marketing) to secure a comprehensive market research report that delivers actionable intelligence on high strength aluminum powder technology. This report distills critical analyses across applications, product types, manufacturing technologies, end users, sales channels, and regional patterns, empowering organizations to navigate evolving regulatory landscapes, optimize supply chains, and capitalize on emerging innovation opportunities.
By partnering with Ketan Rohom, stakeholders will gain full access to detailed chapter breakdowns, proprietary data sets, expert forecasts, and strategic recommendations tailored to the additive manufacturing ecosystem. This includes exclusive insights into tariff impacts, competitive positioning of leading producers, and segmentation models that drive targeted market entry strategies. Requesting this report ensures a data-driven roadmap that aligns product development initiatives with the most promising industry verticals.
To initiate the report acquisition process, reach out to Ketan Rohom and unlock the depth of research that can sharpen competitive advantage, streamline operational planning, and accelerate time to market. Positioned at the intersection of technological innovation and market intelligence, this engagement promises unparalleled guidance for informed decision-making in the high strength aluminum powder domain.
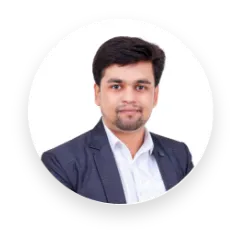
- When do I get the report?
- In what format does this report get delivered to me?
- How long has 360iResearch been around?
- What if I have a question about your reports?
- Can I share this report with my team?
- Can I use your research in my presentation?