Revolutionizing Orthopedic Treatment with Advanced 3D Printed Titanium Implants Delivering Customized Patient Solutions and Superior Clinical Results
In recent years, the intersection of additive manufacturing and biomedical engineering has ushered in a new era for orthopedic care, with titanium emerging as the material of choice for next-generation implants. Titanium’s remarkable combination of biocompatibility, corrosion resistance, and mechanical strength has empowered medical device designers to overcome the limitations of traditional manufacturing, enabling the creation of intricate geometries that mimic bone porosity and promote osseointegration. This convergence of material science and 3D printing technology has opened avenues for patient-specific implants that conform precisely to anatomical requirements, reducing surgical time and enhancing postoperative outcomes.
Following the FDA’s approval of several 3D-printed titanium spinal cages and vertebral body devices in 2024, healthcare providers have begun integrating additive-manufactured implants into mainstream clinical workflows. Parallel advancements in digital imaging software, surgical planning platforms, and in-situ process monitoring systems have streamlined the design-to-production cycle, allowing for rapid iteration and clinical validation. As a result, 3D-printed titanium solutions are now gaining traction across dental, joint replacement, spinal fusion, and trauma fixation procedures, reflecting a transformative shift toward personalized orthopedics that prioritize patient-specific fit and function.
Navigating a Paradigm Shift in Orthopedic Implant Production Fueled by Breakthrough Additive Techniques and Next-Level Personalization
The orthopedic implant landscape is undergoing a paradigm shift driven by a synergy of additive manufacturing breakthroughs and precision medicine initiatives. Advanced lattice architectures and topology-optimized designs, enabled by selective laser melting and electron beam melting techniques, are redefining the boundaries of implant performance, offering customizable porosity gradients that emulate natural bone structures. Concurrently, direct energy deposition systems are expanding possibilities for on-site, near-patient production, enhancing supply chain resilience and shortening lead times for critical components. This technological evolution is further supported by regulatory bodies adapting approval pathways to accommodate the unique characteristics of 3D-printed devices, exemplified by streamlined FDA review mechanisms for reproducible additive processes and biocompatibility assessments.
Moreover, healthcare providers and manufacturers are forging new collaborations to integrate digital preoperative planning with intraoperative guidance, ultimately improving surgical precision and patient outcomes. From real-time imaging to AI-driven design platforms, the integration of data analytics, and automation technologies is accelerating implant innovation. As a result, the ecosystem of hardware suppliers, software developers, and clinical partners is coalescing around a shared vision: delivering bespoke titanium implants that address complex anatomical challenges while meeting stringent safety and performance standards.
Assessing the Cumulative Consequences of Recent United States Tariff Measures on Titanium Supply and Orthopedic Implant Accessibility
Amidst the rapid adoption of additive manufacturing, the United States’ evolving tariff environment has imposed significant pressures on titanium supply chains and implant costs. Notably, Chinese titanium sponge remains subject to a 60 percent duty introduced in 2019, while unwrought titanium imports from key allies-including Japan, Kazakhstan, and Saudi Arabia-incur a 15 percent levy. Although titanium and its derivatives were exempted from the broad reciprocal tariffs announced in April 2025, existing duties continue to inflate raw material expenses for domestic manufacturers and service bureaus Œciteturn1search1.
Additionally, the extension of Section 232 steel and aluminum tariffs to all countries on March 12, 2025, heightened uncertainty across metal supply chains, prompting manufacturers to reassess sourcing strategies. While titanium itself was carved out of these new measures, the broader tariff landscape has disrupted economies of scale, leading to elevated logistics costs and administrative burdens. Industry stakeholders, particularly smaller custom implant producers, face diminished margins and longer production timelines, as they navigate fluctuating duties and potential retaliatory actions. The complexity of these cumulative tariff effects underscores the importance of strategic nearshoring, supplier diversification, and advocacy for tailored trade exemptions to safeguard innovation and ensure patient access to critical orthopedic devices.
Unveiling Critical Segmentation Dynamics Defining Diverse Applications, Implant Varieties, End-User Channels, Printing Technologies, and Material Grade Considerations
A nuanced understanding of market segmentation reveals the multifaceted drivers of demand for 3D-printed titanium orthopedic implants. Across dental restorations, joint replacement procedures, spinal fusion, and trauma fixation applications, clinicians leverage additive capabilities to deliver implants that match the biomechanical and anatomical requirements of diverse patient populations. Within implant types, locking and compression plates address fracture stabilization needs, while hip, knee, and shoulder prostheses benefit from lattice-infused designs that foster bone ingrowth. Cancellous and cortical screws, tailored through precise control of thread profiles, further exemplify how material placement and structural integrity optimize fixation performance.
End users span ambulatory surgical centers seeking rapid turnaround, large hospitals requiring high-volume consistency, and specialty clinics-both dental and orthopedic-that champion bespoke solutions. Each segment demands specific service levels, from digital preoperative simulation to post-production sterilization protocols. On the production front, direct energy deposition systems enable localized refurbishment of worn implants, electron beam melting platforms offer vacuum environments for high-purity builds, and selective laser melting machines strike a balance between detail resolution and throughput. Throughout, Ti6Al4V remains the predominant grade, underpinning implant reliability with its proven mechanical and biocompatibility credentials.
This comprehensive research report categorizes the 3D Printed Titanium Orthopedic Implant market into clearly defined segments, providing a detailed analysis of emerging trends and precise revenue forecasts to support strategic decision-making.
- Application
- Implant Type
- End User
- Printing Technique
- Material Grade
Illuminating Regional Orthopedic Implant Insights Spanning the Americas, Europe Middle East and Africa, and Rapidly Transforming Asia-Pacific Markets
Regional dynamics shape both the rate of adoption and the strategic priorities for 3D-printed titanium implants. In the Americas, mature healthcare systems in the United States and Canada are at the forefront of integrating additive workflows, supported by early regulatory guidance and robust reimbursement pathways. Hospitals and surgical centers in this region are investing in in-house production capabilities, forging collaborations with technology providers to streamline digital-to-physical implant lifecycles.
Europe, the Middle East, and Africa exhibit a diverse landscape where regulatory harmonization and collaborative research consortia drive innovation. Key European markets benefit from strong manufacturing clusters in Germany, the Netherlands, and the UK, where partnerships between academic institutions and implant specialists fuel clinical trials and technology transfer. Meanwhile, emerging economies in the Middle East and Africa are beginning to allocate resources toward additive manufacturing infrastructure, recognizing its potential to address localized surgical needs and supply constraints.
In the Asia-Pacific region, rapid modernization of healthcare infrastructure and growing geriatric populations are spurring accelerated demand for personalized titanium implants. Government incentives and investments in biomedical additive capabilities are encouraging domestic producers to adopt advanced printing techniques, while international collaborations are fostering knowledge exchange and standardization efforts.
This comprehensive research report examines key regions that drive the evolution of the 3D Printed Titanium Orthopedic Implant market, offering deep insights into regional trends, growth factors, and industry developments that are influencing market performance.
- Americas
- Europe, Middle East & Africa
- Asia-Pacific
Profiling Leading Innovators and Industry Giants Driving the Evolution of 3D Printed Titanium Orthopedic Implant Solutions
A competitive ecosystem of hardware providers, material specialists, software innovators, and implant manufacturers is propelling the evolution of 3D-printed titanium solutions. Leading machine builders such as 3D Systems and EOS GmbH deliver high-throughput platforms optimized for complex titanium geometries, while Renishaw’s modular systems integrate real-time process monitoring to ensure build consistency. Materialise stands out for its proprietary design software that enhances lattice optimization and surgical planning, and SMC digital enriches the digital workflow through comprehensive verification tools.
On the clinical device front, established orthopedic giants including DePuy Synthes, Medtronic, and Stryker have incorporated additive manufacturing into their portfolios, launching patient-specific spinal cages, hip replacements, and trauma implants. Zimmer Biomet and Aesculap are deepening collaborations with powder producers to refine Ti6Al4V formulations, while smaller specialists such as Conformis focus exclusively on custom knee implants, and Implantcast excels in rapid fabrication of trauma plates. Emerging material innovators like Amastan Technologies and Global Orthopaedic Technology contribute advanced powder development and post-processing expertise, reinforcing quality assurances throughout the supply chain.
This comprehensive research report delivers an in-depth overview of the principal market players in the 3D Printed Titanium Orthopedic Implant market, evaluating their market share, strategic initiatives, and competitive positioning to illuminate the factors shaping the competitive landscape.
- Stryker Corporation
- DePuy Synthes, Inc.
- Zimmer Biomet Holdings, Inc.
- Medtronic plc
- Smith & Nephew plc
- LimaCorporate S.p.A.
- Renishaw plc
- 3D Systems, Inc.
- Materialise NV
- Anatomics Pty Ltd
Strategic Roadmap and Actionable Recommendations to Capitalize on Additive Orthopedic Manufacturing Opportunities and Mitigate Supply Chain Risks
To navigate the complexities of additive orthopedic manufacturing, industry leaders should first prioritize supply chain diversification by establishing dual-source agreements for titanium sponge and powder, leveraging both domestic production and allied foreign suppliers. Investing in nearshoring strategies for critical components can mitigate exposure to unpredictable tariff fluctuations and bolster production resilience. Additionally, formulating partnerships with regulatory agencies to pilot standardized additive approval pathways will accelerate product clearances while maintaining rigorous safety standards.
Furthermore, device OEMs and service bureaus are encouraged to integrate digital design platforms with AI-driven topology optimization tools, enabling more rapid customization and iterative testing. Collaborative consortia that bring together academic research centers, clinical institutions, and technology providers will be essential in validating novel lattice structures and biomaterial coatings. Finally, companies should consider targeted talent development initiatives-such as specialized training academies-to close the skills gap in additive design, process monitoring, and post-processing, ensuring a qualified workforce capable of sustaining innovation.
Comprehensive Research Methodology Employed to Derive Robust and Insightful 3D Printed Titanium Implant Market Intelligence
This report’s findings are grounded in a rigorous multi-stage research methodology, combining both primary and secondary data sources to ensure comprehensive coverage. Primary research included in-depth interviews with orthopedic surgeons, additive manufacturing engineers, regulatory experts, and procurement officers across major healthcare systems. These conversations provided nuanced insights into clinical requirements, processing challenges, and adoption barriers.
Complementing primary inputs, secondary research encompassed regulatory filings, patent analyses, trade association publications, and peer-reviewed journal articles. Market triangulation techniques were employed to validate data points, while scenario modeling assessed the impact of tariff regimes and regional policy shifts. Technology readiness levels were mapped against clinical integration roadmaps, and sensitivity analyses illuminated the influence of material grade refinements and printing technique selections on operational performance.
Explore AI-driven insights for the 3D Printed Titanium Orthopedic Implant market with ResearchAI on our online platform, providing deeper, data-backed market analysis.
Ask ResearchAI anything
World's First Innovative Al for Market Research
Concluding Perspectives on the Future Trajectory of 3D Printed Titanium Orthopedic Implants Amidst Technological and Regulatory Shifts
In summary, the 3D-printed titanium orthopedic implant landscape is at a pivotal juncture, driven by converging forces of material innovation, additive manufacturing advancements, and evolving regulatory frameworks. As clinical adoption expands from dental restorations to complex spinal devices and trauma fixation systems, the industry must reconcile the benefits of personalized geometry with the imperatives of cost-effectiveness and supply chain stability. Tariff landscapes continue to challenge raw material sourcing, underscoring the need for strategic nearshoring and advocacy for tailored trade exemptions.
Looking forward, the maturation of direct energy deposition, electron beam melting, and selective laser melting techniques-coupled with AI-enabled design platforms-will further democratize access to bespoke implants. Regional dynamics will shape the pace of adoption, with established markets in the Americas and EMEA advancing regulatory harmonization, and Asia-Pacific accelerating infrastructure modernization. Ultimately, stakeholders that invest in digital integration, cross-sector collaborations, and targeted talent development will lead the charge toward delivering optimized patient outcomes and sustaining the momentum of additive orthopedic innovation.
This section provides a structured overview of the report, outlining key chapters and topics covered for easy reference in our 3D Printed Titanium Orthopedic Implant market comprehensive research report.
- Preface
- Research Methodology
- Executive Summary
- Market Overview
- Market Dynamics
- Market Insights
- Cumulative Impact of United States Tariffs 2025
- 3D Printed Titanium Orthopedic Implant Market, by Application
- 3D Printed Titanium Orthopedic Implant Market, by Implant Type
- 3D Printed Titanium Orthopedic Implant Market, by End User
- 3D Printed Titanium Orthopedic Implant Market, by Printing Technique
- 3D Printed Titanium Orthopedic Implant Market, by Material Grade
- Americas 3D Printed Titanium Orthopedic Implant Market
- Europe, Middle East & Africa 3D Printed Titanium Orthopedic Implant Market
- Asia-Pacific 3D Printed Titanium Orthopedic Implant Market
- Competitive Landscape
- ResearchAI
- ResearchStatistics
- ResearchContacts
- ResearchArticles
- Appendix
- List of Figures [Total: 28]
- List of Tables [Total: 820 ]
Unlock Deep Market Intelligence on 3D Printed Titanium Orthopedic Implants by Connecting with Associate Director Ketan Rohom and Securing Your Exclusive Report
Empower your organization with unparalleled market insights into the evolving 3D printed titanium orthopedic implant sector by engaging directly with Ketan Rohom, Associate Director, Sales & Marketing. By connecting with Ketan, you gain privileged access to a meticulously crafted research report that deciphers the complex interplay of technological advances, regulatory developments, and supply chain variables influencing implant innovation. His expertise will guide you through the report’s rich analysis of segmentation strategies, regional dynamics, and competitive intelligence, equipping you with the actionable intelligence needed to make strategic decisions and secure a leadership position in this rapidly expanding market. Take the next step to unlock critical data and strategic recommendations-reach out to Ketan Rohom to secure your exclusive copy today and accelerate your path to market success.
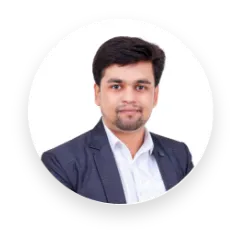
- When do I get the report?
- In what format does this report get delivered to me?
- How long has 360iResearch been around?
- What if I have a question about your reports?
- Can I share this report with my team?
- Can I use your research in my presentation?