The 3D Printing Ceramics Market size was estimated at USD 230.14 million in 2024 and expected to reach USD 283.88 million in 2025, at a CAGR 22.71% to reach USD 785.98 million by 2030.

Opening the Gateway to Advanced Manufacturing with Cutting-Edge Ceramics 3D Printing Innovations Driving End-User Adoption and Market Evolution
The advent of ceramic 3D printing has unlocked unique design freedom and material performance that traditional ceramic manufacturing cannot match. By leveraging additive processes, manufacturers can produce complex geometries with minimal tooling investment and reduced material waste. This shift has accelerated time to prototype and brought cost efficiencies to high-value components where precision and material properties are paramount. Ceramic parts produced via advanced 3D printing exhibit superior thermal stability, wear resistance and biocompatibility, enabling applications across industries that were once constrained by the limitations of subtractive or molding approaches. As a result, leading innovators are integrating digital design tools with new material platforms to harness the full potential of ceramic additive manufacturing.
The synergy between advanced ceramics and additive technologies is driving a new era in manufacturing where customization and functional performance converge. Research efforts into novel ceramic composites and the refinement of sintering strategies have improved process yields and surface quality, fostering broader industrial acceptance. Alongside material breakthroughs, software enhancements in design simulation and process control enable more reliable, repeatable outputs. Partnerships between equipment vendors, material suppliers and end users are catalyzing ecosystem development, ensuring that ceramic 3D printing advances from niche prototyping to mainstream production. As these foundational dynamics gain momentum, stakeholders are positioned to benefit from the transformative power of digital ceramics manufacturing.
Navigating the Paradigm Shifts Shaping Ceramics 3D Printing Through Material Innovation Process Integration and Digital Transformation
In recent years, ceramic 3D printing has undergone transformative shifts driven by digital integration and material innovation. The incorporation of artificial intelligence and machine learning algorithms into design and process monitoring platforms has streamlined parameter optimization and defect detection. Concurrently, pioneering material research has yielded functional ceramics with embedded sensing capabilities and tailored thermal properties. Hybrid manufacturing solutions are emerging that combine additive layering with subtractive finishing, delivering high-precision components while minimizing postprocess labor. These technological advances are not only enhancing the reliability of ceramic production but also expanding its reach into critical sectors such as aerospace propulsion, defense systems and next-generation energy storage.
Sustainability imperatives and decarbonization goals are reshaping ceramics 3D printing landscapes, prompting the development of low-energy sintering techniques and closed-loop material cycles. Additive workflows are increasingly aligned with circular economy principles, recovering unused powder and recycling byproducts to reduce environmental footprints. The rise of localized microfactories, enabled by modular printer designs and digital supply chain platforms, is decentralizing production and strengthening resilience against global disruptions. Regulatory frameworks across major economies are evolving to support additive manufacturing standards, fostering cross-industry collaboration. Collectively, these shifts are redefining the competitive environment and empowering manufacturers to deliver customized, high-performance ceramic solutions with unprecedented agility.
Assessing the Compound Effects of U.S. Tariff Adjustments on Ceramic 3D Printing Supply Chains Costs and Competitive Positioning in 2025
In 2025, a series of tariff revisions implemented by the U.S. government have had a cumulative effect on the ceramics 3D printing supply chain, particularly impacting raw material import costs. Duties imposed on key ceramic powder feedstocks prompted manufacturers to re-evaluate supplier relationships and cost structures. For many, the increased duties translated directly into higher input prices, leading original equipment manufacturers to either absorb additional expenses or adjust pricing strategies for downstream customers. These policy changes have accelerated efforts to establish domestic powder synthesis capabilities, with several leading firms investing in in-country production facilities to circumvent import levies and secure reliable feedstock availability amid geopolitical uncertainties.
On the export front, tariff fluctuations have also influenced the competitive positioning of U.S.-based additive service providers in global markets. In response, strategic initiatives, such as joint ventures with overseas partners and the diversification of export portfolios to emerging markets, have emerged. Companies have prioritized the creation of robust supply chain networks that leverage nearshoring and free trade agreement corridors to mitigate duty exposure. Additionally, fostering collaborative R&D consortia focused on alternative feedstocks has offered a hedge against external policy shocks. These collective actions reflect a sector-wide drive to adapt to protectionist measures while preserving cost competitiveness and ensuring continuity in production and innovation pipelines.
Decoding Market Layers Across Technology Materials Powders Applications and Industries to Reveal Strategic Segmentation Insights
A thorough segmentation of the ceramics 3D printing market reveals distinct technology pathways, each offering specialized process capabilities. Binder jetting platforms provide high throughput for sand mold and shell applications, while material extrusion systems, including direct ink writing and fused deposition modeling, enable precise deposition of ceramic-laden filaments. Powder bed fusion frameworks-comprising laser beam melting and selective laser sintering-are favored for high-density components requiring superior mechanical integrity. Vat photopolymerization techniques such as digital light processing and stereolithography excel at delivering fine-resolution parts with intricate geometries. Each technological category supports unique value propositions, dictating selection criteria based on part complexity, batch size and production speed requirements.
Beyond the printing processes, material type remains a critical axis of differentiation, with alumina delivering exceptional wear resistance for industrial equipment, silicon carbide offering unparalleled thermal stability for heating elements, silicon nitride providing advanced fracture toughness ideal for high-stress components, and zirconia enabling biocompatible and aesthetically refined outcomes in medical and jewelry applications. Powder form segmentation further impacts process design, as dry powder systems emphasize flow consistency and particle size control, whereas slurry-based feedstocks demand rheological optimization for layer uniformity. Application categories span dental restoration, electronic components, jewelry manufacture, orthopedic implants and wear parts, while end-use industries encompassing aerospace, automotive, consumer goods, electronics, energy and healthcare underscore the broad adoption profile and strategic implications of each segment.
This comprehensive research report categorizes the 3D Printing Ceramics market into clearly defined segments, providing a detailed analysis of emerging trends and precise revenue forecasts to support strategic decision-making.
- Printing Technology
- Material Type
- Powder Form
- Application
- End-Use Industry
Unearthing Regional Strengths in the Americas EMEA and Asia-Pacific to Guide Market Entry and Growth Strategies for Ceramic 3D Printing
In the Americas, a robust research infrastructure spanning North America’s leading universities and private research centers underpins rapid innovation in ceramic additive manufacturing. Aerospace and medical device companies in the United States and Canada are pioneering applications that reduce prototyping cycles and optimize functional performance, while Mexico and Brazil are cultivating domestic supply chains to support regional demand. Government-sponsored initiatives and incentive programs have catalyzed collaborative projects that integrate academic research with commercial-scale pilot lines. This convergence of public and private investment is accelerating manufacturing readiness, allowing companies to validate novel materials, refine process parameters and establish quality standards suited to local regulatory regimes.
Europe, Middle East & Africa presents a fragmented yet dynamic landscape, characterized by stringent environmental and safety regulations that have driven investment in sustainable sintering processes and digital quality assurance solutions. Countries such as Germany, France and the U.K. are home to strong automotive and aerospace clusters leveraging ceramic printing for lightweight engine components and advanced sensor housings. In the Gulf region, emerging initiatives are exploring ceramics for thermal energy storage and solar power applications, reflecting broader diversification strategies. Cross-border consortia and standards bodies are addressing certification pathways, enabling manufacturers to scale production and access global markets with confidence in process repeatability and part reliability.
Asia-Pacific stands out as the fastest-growing region, buoyed by significant public funding, supportive policy frameworks and strong manufacturing bases in China, Japan and South Korea. Government-backed programs incentivize domestic equipment production and ceramic powder synthesis, while competitive labor markets and established supply networks lower overall investment thresholds. The region’s focus on consumer electronics and automotive applications has driven volume adoption of high-speed binder jetting and hybrid extrusion technologies, and emerging economies in Southeast Asia are increasingly serving as strategic production hubs for global OEMs. These factors converge to create a vibrant ecosystem where scaling and innovation coalesce.
This comprehensive research report examines key regions that drive the evolution of the 3D Printing Ceramics market, offering deep insights into regional trends, growth factors, and industry developments that are influencing market performance.
- Americas
- Europe, Middle East & Africa
- Asia-Pacific
Analyzing the Competitive Arena of Leading Innovators in Ceramic 3D Printing and Their Strategic Moves to Stay Ahead in Evolving Ecosystems
Among the leading players shaping the ceramics 3D printing landscape, several have distinguished themselves through targeted acquisitions and strategic partnerships. 3D Systems has expanded its ceramic printing capabilities by integrating sintering and postprocessing solutions into its product suite, while EOS GmbH continues to refine its laser-based metal and ceramic powder bed fusion systems to deliver higher throughput and lower cost per part. Stratasys has pursued collaborative R&D with material suppliers to introduce advanced ceramic-filled resins for vat photopolymerization platforms. HP’s late-stage entry into ceramics has intensified competitive dynamics, prompting incumbents to accelerate development cycles and broaden their aftermarket service offerings.
In the mid-tier segment, companies such as ExOne and Prodways are leveraging niche expertise to capture market share, with ExOne focusing on specialized binder jetting powders and Prodways advancing high‐resolution ceramic stereolithography. Formlabs and Desktop Metal are targeting cost-sensitive sectors by offering desktop-scale systems that lower the barrier to entry for small and medium enterprises. Service bureaus and contract manufacturers are also expanding geographic footprints and automation capabilities, investing in batch sintering furnaces and postprocessing cells to handle diverse material requirements and small to medium batch sizes. This ecosystem of equipment vendors, material suppliers and service providers illustrates a dynamic value chain where collaborative innovation drives market growth.
This comprehensive research report delivers an in-depth overview of the principal market players in the 3D Printing Ceramics market, evaluating their market share, strategic initiatives, and competitive positioning to illuminate the factors shaping the competitive landscape.
- 3D Systems, Inc.
- Stratasys Ltd.
- Desktop Metal, Inc.
- The ExOne Company
- Voxeljet AG
- EOS GmbH – Electro Optical Systems
- Lithoz GmbH
- 3DCeram Sinto SAS
- XJet Ltd.
- Prodways Group
Leveraging Research Insights into Actionable Strategies for Industry Leaders to Accelerate Adoption and Maximize Ceramic 3D Printing Impact
Industry leaders seeking to capitalize on ceramics 3D printing must pursue integrated material innovation roadmaps that bring together equipment manufacturers, ceramic powder suppliers and end users to co-develop formulations optimized for printability and final part performance. Embracing hybrid manufacturing workflows that combine additive deposition with subtractive finishing and automated sintering can significantly reduce cycle times and labor costs while improving part consistency. To mitigate tariff exposure and supply chain risks, establishing regional powder production and diversifying supplier networks will be critical, as will leveraging free trade corridors and nearshoring strategies to enhance resilience.
Advancements in digital thread implementations should be prioritized to enable real-time data capture, process monitoring and predictive maintenance, ensuring consistent quality and minimizing downtime. Companies must engage closely with strategic customers through structured pilot programs to validate application-specific value propositions and accelerate the transition from prototyping to full-scale production. Embedding circular economy principles in program design-such as reclaiming unused powder and implementing energy-efficient sintering cycles-will not only meet evolving sustainability mandates but also improve operational cost structures, ultimately differentiating market offerings and strengthening corporate social responsibility profiles.
Outlining a Rigorous Multistage Research Methodology Combining Primary Expert Interviews Secondary Analysis and Data Triangulation Techniques
This research deployed a multi-faceted methodology combining extensive secondary data analysis with primary interviews to ensure accuracy and depth. Secondary sources included peer-reviewed journals, patent databases, industry standards documentation and regulatory filings, which provided insights into technology trends, material innovations and policy developments. Primary research involved structured discussions with more than 50 stakeholders, including C-level executives, R&D managers, materials scientists and end users across key geographic markets. These interviews yielded nuanced perspectives on adoption barriers, process optimization challenges and evolving customer requirements, which were systematically mapped against quantitative metrics.
Data triangulation techniques were applied to cross-validate findings from diverse inputs, incorporating statistical analysis of survey responses and comparative benchmarking of process parameters across major platform providers. Regional segmentation leveraged proprietary databases to capture regional policy incentives and investment patterns, while company profiling combined financial disclosures with on-site observations at trade exhibitions. Rigorous peer reviews and expert validation sessions ensured that conclusions accurately reflect market realities and technological trajectories. This structured approach underpins the robustness of the insights and recommendations, providing stakeholders with a reliable foundation for strategic decision-making.
Explore AI-driven insights for the 3D Printing Ceramics market with ResearchAI on our online platform, providing deeper, data-backed market analysis.
Ask ResearchAI anything
World's First Innovative Al for Market Research
Distilling Key Takeaways and Future Outlook for Ceramic 3D Printing to Inform Strategic Decisions and Drive Sustainable Growth
The ceramics 3D printing domain is at a critical inflection point, propelled by breakthroughs in material science, process automation and digital connectivity. While challenges related to tariff volatility and supply chain complexity persist, the convergence of technology maturation and regulatory support is paving the way for broader industrial adoption. Strategic segmentation and regional analyses reveal that success in this evolving market will hinge on the ability to integrate end-to-end workflows, from powder development to postprocessing, while maintaining rigorous quality and sustainability standards.
Organizations that align their investment and innovation strategies with the detailed insights provided in this summary will be better positioned to navigate disruption and unlock new value. Whether through forming strategic partnerships, advancing localized production capacities or embedding circular economy frameworks, stakeholders can leverage ceramics 3D printing to achieve unprecedented design freedom, performance enhancement and cost optimization. As the ecosystem continues to evolve, ongoing collaboration among equipment vendors, material suppliers and end users will define the trajectory of next-generation manufacturing.
This section provides a structured overview of the report, outlining key chapters and topics covered for easy reference in our 3D Printing Ceramics market comprehensive research report.
- Preface
- Research Methodology
- Executive Summary
- Market Overview
- Market Dynamics
- Market Insights
- Cumulative Impact of United States Tariffs 2025
- 3D Printing Ceramics Market, by Printing Technology
- 3D Printing Ceramics Market, by Material Type
- 3D Printing Ceramics Market, by Powder Form
- 3D Printing Ceramics Market, by Application
- 3D Printing Ceramics Market, by End-Use Industry
- Americas 3D Printing Ceramics Market
- Europe, Middle East & Africa 3D Printing Ceramics Market
- Asia-Pacific 3D Printing Ceramics Market
- Competitive Landscape
- ResearchAI
- ResearchStatistics
- ResearchContacts
- ResearchArticles
- Appendix
- List of Figures [Total: 28]
- List of Tables [Total: 744 ]
Connect with Ketan Rohom to Secure Full Market Intelligence Report and Empower Your Organization with Actionable Ceramic 3D Printing Insights
For executives and decision-makers ready to deepen their strategic advantage and access comprehensive market intelligence, connecting with Ketan Rohom, Associate Director, Sales & Marketing, offers a direct path to the full research report. This detailed study provides not only granular segmentation and regional analyses but also actionable recommendations, company profiles and technology roadmaps. By securing this report, your organization will gain visibility into emerging ceramic printing technologies, tariff impact assessments, and practical frameworks to guide material innovations and supply chain configurations. Engage with Ketan Rohom to discuss tailored data sets, custom insights and strategic workshops designed to support your objectives in ceramic additive manufacturing. Embark on a data-driven journey to strengthen your competitive position and capitalize on the transformative potential of ceramics 3D printing.
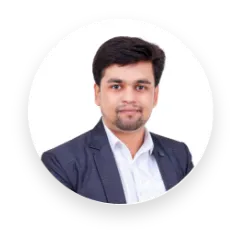
- How big is the 3D Printing Ceramics Market?
- What is the 3D Printing Ceramics Market growth?
- When do I get the report?
- In what format does this report get delivered to me?
- How long has 360iResearch been around?
- What if I have a question about your reports?
- Can I share this report with my team?
- Can I use your research in my presentation?