The 3D Printing Metals Market size was estimated at USD 2.32 billion in 2024 and expected to reach USD 2.67 billion in 2025, at a CAGR 15.04% to reach USD 5.40 billion by 2030.

Charting the Future Trajectory of Metal 3D Printing
Metal additive manufacturing has emerged as a transformative force within modern production landscapes, offering unprecedented design flexibility and material efficiency. As traditional subtractive processes confront limitations in part complexity and lead times, the shift toward three-dimensional printing of metals enables stakeholders to produce lightweight, high-strength components with geometries previously unattainable. This introduction provides an executive overview of the strategic importance of metal 3D printing, highlighting how adoption trends are reshaping supply chains and unlocking new opportunities across aerospace, automotive, healthcare, and beyond. By examining the core drivers, technological enablers, and competitive dynamics, this summary equips decision makers with a clear perspective on why metal additive manufacturing stands at the forefront of industrial innovation.
Pivotal Innovations Redefining Industrial Metal Printing
The rapid maturation of metal additive processes reflects a confluence of technological breakthroughs and shifting industrial priorities. Advancements in powder bed fusion, binder jetting, and directed energy deposition are enabling manufacturers to tailor material microstructures and mechanical properties with a precision once reserved for laboratory environments. Concurrently, integration of real-time monitoring systems and artificial intelligence-driven process controls has driven reproducibility and throughput to new highs, overcoming historical barriers to scale.
At the same time, sustainability imperatives are reshaping equipment design and material selection. Efforts to recycle unused powder, reduce energy consumption during build cycles, and leverage lower-density alloys are unlocking cost efficiencies and greener production footprints. In tandem, the proliferation of digital thread strategies is uniting design for additive manufacturing (DfAM) principles with enterprise resource planning and quality management platforms, fostering end-to-end traceability and accelerated time to market.
Assessing the 2025 U.S. Tariff Shock on Metal Additive Manufacturing
The implementation of United States tariffs in 2025 on imported metal powders and related additive equipment has imposed a multilayered impact on the industry. Manufacturers reliant on high-purity alloys face higher raw material costs, driving them to reevaluate sourcing strategies and to explore domestic powder production partnerships. Equipment suppliers have reacted by localizing certain manufacturing operations, negotiating adjusted supply agreements, and developing alternative alloy chemistries to mitigate tariff pressures.
In parallel, downstream adopters encounter a shift in cost-per-part metrics, prompting some to consolidate orders and to invest in larger build volumes to spread overhead across more units. While short-term price increases introduce budgetary challenges, they have also accelerated regional supply chain diversification, pushing companies to explore new procurement corridors in Europe and Asia. Overall, the tariff landscape has become a catalyst for supply chain resilience, compelling participants to reassess partnerships, inventory strategies, and vertical integration models.
Segment-Level Revelations in Metal 3D Printing Markets
Examining the market through the lens of material types reveals a competitive hierarchy in which stainless steel and titanium maintain commanding shares, driven by their corrosion resistance and high strength-to-weight properties, respectively. Aluminum alloys continue to gain traction as manufacturers seek cost-effective, lightweight solutions, while nickel alloys and cobalt chromium find specialized applications requiring exceptional heat and fatigue performance.
Technological segmentation uncovers distinct adoption patterns. Powder bed fusion remains the dominant method for high-precision, complex geometries, while binder jetting has surged where throughput and post-process speed are critical. Directed energy deposition complements these by enabling repair and surface enhancement operations, and material extrusion preserves its role in prototyping and low-cost tooling applications.
On the equipment front, laser-based machines account for a significant portion of installed capacity, benefiting from mature optics and widely available support networks. Electron beam systems hold niche advantages in high-vacuum environments for aerospace components, whereas binder jet machines attract manufacturers prioritizing rapid build speeds. Material extrusion platforms, though more prevalent in polymer printing, are carving out entry-level pathways for metal experimentation.
Sector-specific demand highlights aerospace and defense as the largest consumer of metal additive services, leveraging the technology for weight reduction in aircraft components and rapid production of defense equipment. The automotive industry follows closely, focusing on performance parts and tooling efficiency, while energy, healthcare, consumer goods, and broader manufacturing applications continue to expand as reliability and repeatability metrics improve.
Application segmentation demonstrates that prototyping remains a foundational use case, bridging design validation with iterative testing, but industrial end-use parts are rapidly closing the gap as process qualifications advance. In tooling, jigs and fixtures have become standard deliverables for assembly lines, and molds and dies are benefiting from conformal cooling designs that shorten cycle times and enhance product quality.
This comprehensive research report categorizes the 3D Printing Metals market into clearly defined segments, providing a detailed analysis of emerging trends and precise revenue forecasts to support strategic decision-making.
- Material
- Technology
- Equipment Type
- End Use Industry
- Application
How Regional Dynamics Are Shaping Metal Additive Adoption
Regional analysis underscores divergent growth trajectories shaped by investment climates, regulatory regimes, and industry concentration. In the Americas, robust aerospace and automotive clusters have propelled adoption, supported by governmental incentives and research grants that bolster domestic powder production and equipment manufacturing. Canada and Brazil are emerging as regional innovators, leveraging university partnerships to translate academic breakthroughs into commercial solutions.
Europe, the Middle East, and Africa present a mosaic of maturity levels. Western European nations lead with extensive industrial infrastructure and advanced testing facilities, often collaborating across borders to standardize quality frameworks. Within the Middle East, strategic investments in national defense and energy sectors are cultivating nascent capabilities, while Africa’s market remains opportunistic, with localized applications in mining and medical devices.
Asia-Pacific continues to set the pace in volume and scale, driven by China’s aggressive capacity expansions and Japan’s material science expertise. South Korea and Australia are also investing heavily in next-generation deposition processes, and India’s growing manufacturing base is increasingly adopting metal additive for both domestic use and export-oriented production. These regional variations reflect how policy priorities and industrial strengths dictate the speed and scope of technology uptake.
This comprehensive research report examines key regions that drive the evolution of the 3D Printing Metals market, offering deep insights into regional trends, growth factors, and industry developments that are influencing market performance.
- Americas
- Europe, Middle East & Africa
- Asia-Pacific
Spotlight on Industry Leaders Driving Metal Printing Evolution
The competitive ecosystem is anchored by original equipment manufacturers that combine material development with machine innovation and service offerings. One leading player has differentiated itself through strategic acquisitions that broaden its material portfolio and integrate automated post-processing solutions. Another major supplier focuses on open-architecture platforms that enable collaborative research with academic institutions and end users, fostering ecosystem growth and application diversification.
Several companies have carved niches in high-power laser systems, securing partnerships with aerospace giants to certify components for flight. Others have pursued a modular machine design, allowing customers to upgrade deposition sources and build envelopes without replacing entire units. Meanwhile, a cohort of agile newcomers is targeting specialized segments such as biomedical implants and microfabrication, often collaborating with healthcare providers to validate biocompatible alloys and to streamline regulatory approvals.
In parallel, material powder producers are forging alliances with equipment vendors to co-develop pre-alloyed powders optimized for specific processes. These collaborations have yielded new chemistries designed to minimize porosity, enhance build rates, and reduce support structures. Across the landscape, intellectual property portfolios and cross-industry partnerships serve as critical differentiators, shaping the trajectory of competitive advantage.
This comprehensive research report delivers an in-depth overview of the principal market players in the 3D Printing Metals market, evaluating their market share, strategic initiatives, and competitive positioning to illuminate the factors shaping the competitive landscape.
- 3D Systems Inc.
- BASF SE
- Carpenter Technology Corporation
- Nano Dimension Ltd.
- EOS GmbH
- Eplus3D
- Höganäs AB
- Incredible Am Pvt Ltd.
- Markforged, Inc.
- Materialise NV
- OC Oerlikon Corporation AG
- Optomec Inc.
- Pollen AM Inc.
- Prodways Group
- Proto Labs, Inc.
- Renishaw PLC
- Sandvik AB
- Sciaky Inc.
- Nikon SLM Solutions AG
- Steinbach AG
- Tethon Corporation
- TRUMPF SE + Co. KG
- voxeljet AG
- Wipro Limited
- HP Development Company, L.P.
Strategic Imperatives to Capitalize on Metal Additive Growth
To build on the momentum of metal additive adoption, industry stakeholders should prioritize investments in in-house research programs that explore emerging alloy systems and process monitoring technologies. Establishing strategic alliances with powder suppliers and equipment innovators can yield co-development opportunities that accelerate time to market and secure preferential access to next-generation materials.
Organizations must also cultivate talent pipelines by offering targeted training in additive design principles, metallurgical science, and digital simulation. Upskilling workforces to interpret real-time process data and to optimize build parameters will be essential for achieving consistent part quality at scale. Equally important is the implementation of robust quality management systems that integrate nondestructive evaluation and automated inspection to maintain regulatory compliance and customer confidence.
Finally, executives should evaluate opportunities for vertical integration, balancing the benefits of localized powder production and machine assembly against the capital requirements involved. By adopting modular production architectures and flexible contract models, companies can hedge against market volatility, manage inventory more effectively, and respond swiftly to shifts in end-use demand.
Ensuring Data Integrity Through Robust Research Framework
This analysis draws on a multi-tiered research protocol designed to ensure data integrity and actionable insights. Primary research was conducted through confidential interviews with C-level executives, materials scientists, and application engineers across key regions. Secondary data were collated from peer-reviewed journals, patent filings, regulatory disclosures, and corporate financial reports. These sources were triangulated to validate technology adoption rates, segment performance, and competitive positioning.
Quantitative data points underwent statistical consistency checks, and qualitative observations were subjected to thematic analysis to identify emerging patterns and disruptive inflection points. Market segmentation frameworks were refined through iterative expert workshops, aligning the categorization of materials, technologies, equipment types, industries, and applications with real-world deployment scenarios. Transparency in methodology and rigorous validation protocols underpin the trustworthiness of the conclusions and recommendations presented herein.
Explore AI-driven insights for the 3D Printing Metals market with ResearchAI on our online platform, providing deeper, data-backed market analysis.
Ask ResearchAI anything
World's First Innovative Al for Market Research
Final Reflections on Metal 3D Printing Market Evolution
Throughout this executive summary, metal additive manufacturing has been portrayed as a catalyst for industrial reinvention, driven by continuous innovation in materials, processes, and business models. The interplay between strategic tariffs and regional investment patterns underscores the need for agile supply chains and adaptive cost structures. Moreover, segmentation analyses reveal distinct value propositions across material types, methods, and end-use applications, emphasizing the importance of targeted strategies for market penetration.
As the competitive landscape evolves, stakeholders who harness advanced process controls, invest in collaborative R&D, and strengthen vertical integration will be best positioned to transform challenge into opportunity. The insights presented here aim to inform decisive action, enabling organizations to navigate complexity, mitigate risk, and capture the full potential of metal 3D printing technologies.
This section provides a structured overview of the report, outlining key chapters and topics covered for easy reference in our 3D Printing Metals market comprehensive research report.
- Preface
- Research Methodology
- Executive Summary
- Market Overview
- Market Dynamics
- Market Insights
- Cumulative Impact of United States Tariffs 2025
- 3D Printing Metals Market, by Material
- 3D Printing Metals Market, by Technology
- 3D Printing Metals Market, by Equipment Type
- 3D Printing Metals Market, by End Use Industry
- 3D Printing Metals Market, by Application
- Americas 3D Printing Metals Market
- Europe, Middle East & Africa 3D Printing Metals Market
- Asia-Pacific 3D Printing Metals Market
- Competitive Landscape
- ResearchAI
- ResearchStatistics
- ResearchContacts
- ResearchArticles
- Appendix
- List of Figures [Total: 26]
- List of Tables [Total: 331 ]
Take the Next Step to Acquire Your In-Depth Market Report
To explore detailed analyses on material performance, technology developments, equipment innovations, and regional dynamics for metal additive manufacturing, reach out to Ketan Rohom (Associate Director, Sales & Marketing at 360iResearch). Engage directly with an expert who can guide you through the comprehensive insights, tailored recommendations, and supporting data critical to your strategic decision making. Secure this authoritative market research report today and equip your organization with the intelligence needed to lead in the rapidly evolving metal 3D printing landscape.
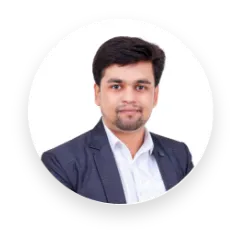
- How big is the 3D Printing Metals Market?
- What is the 3D Printing Metals Market growth?
- When do I get the report?
- In what format does this report get delivered to me?
- How long has 360iResearch been around?
- What if I have a question about your reports?
- Can I share this report with my team?
- Can I use your research in my presentation?