The 3D Printing Plastics Market size was estimated at USD 1.55 billion in 2024 and expected to reach USD 1.87 billion in 2025, at a CAGR 20.06% to reach USD 4.66 billion by 2030.

Unveiling the Next Generation of 3D Printing Plastics
The landscape of additive manufacturing has evolved from niche prototyping laboratories to a critical pillar of modern production strategies, driven by rapid advances in material science and process engineering. Central to this transformation is the emergence of next-generation 3D printing plastics that offer enhanced mechanical performance, chemical resistance, and sustainability credentials. As industries ranging from aerospace to consumer products embrace additive workflows, the demand for specialized polymer formulations capable of meeting stringent functional requirements has never been greater.
This executive summary illuminates key dynamics in the 3D printing plastics arena, providing decision-makers with a strategic overview of market drivers, disruptive innovations, and emerging challenges. By focusing on material diversity-from robust filaments and high-precision resins to versatile powders-organizations can identify opportunities to optimize production, shorten development cycles, and reduce costs. As you explore the insights that follow, you will gain clarity on how to leverage these materials to drive competitive advantage and align your additive manufacturing roadmap with evolving industry imperatives.
Navigating the Pivotal Shifts Shaping the Industry
Over the past decade, the 3D printing plastics sector has undergone a series of transformative shifts that are reshaping its competitive landscape. Breakthroughs in polymer chemistry have introduced advanced resin and powder formulations with tailored thermal stability and mechanical toughness, enabling end-use applications previously considered out of reach. Simultaneously, the maturation of printing platforms-particularly fused deposition modeling, stereolithography, and selective laser sintering-has expanded the palette of compatible materials while driving down barrier-to-entry costs.
Furthermore, heightened focus on circular economy principles has spurred the development of recyclable and bio-based plastics that reduce environmental footprints without compromising performance. This sustainability imperative is prompting material suppliers, equipment manufacturers, and end users to collaborate in establishing robust closed-loop systems. As digital design and simulation tools become more sophisticated, manufacturers are unlocking new efficiencies, elevating quality control, and accelerating time-to-market. These converging trends underscore a pivotal moment in which technological innovation and environmental stewardship converge to redefine value creation in additive manufacturing.
Assessing the Ripple Effects of 2025 Tariff Measures
The introduction of tariffs on imported polymers and printing materials in 2025 has generated significant repercussions across the additive manufacturing supply chain. Unexpected duties on resin, filament, and powder shipments to the United States have elevated input costs, compelling manufacturers to reassess sourcing strategies and explore nearshoring alternatives. In response, some producers have accelerated investments in domestic polymer production capacity, while others have engaged in strategic hedging and long-term contracts to mitigate price volatility.
Beyond cost pressures, these trade measures have stimulated innovation in processing techniques to optimize material utilization and minimize waste. Companies are enhancing powder recovery systems and refining resin recycling workflows to safeguard margins. Additionally, the tariff environment has catalyzed closer collaboration between material suppliers and equipment manufacturers to co-develop formulations that balance performance requirements with tariff-eligible classifications. Looking ahead, market participants will need to remain agile, leveraging data-driven procurement practices and real-time analytics to anticipate regulatory shifts and sustain competitive resilience.
Deep Dive into Market Segmentation Nuances
The market’s complexity becomes evident when examining it through multiple segmentation lenses, each revealing distinct growth patterns and strategic imperatives. When viewed by material form, filament dominates entry-level printing and prototyping due to its ease of use and compatibility with FDM systems, but powder-based technologies are gaining traction in high-performance sectors where nylon, polypropylene, and TPU powders deliver superior mechanical properties. Meanwhile, resin applications are rapidly diversifying; dental specialists are leveraging biocompatible photopolymers while engineering teams demand resins designed for high-temperature resistance and fine feature resolution, and standard photopolymers continue to fulfill aesthetic and rapid prototyping needs.
Delving into printing technologies, FDM remains the bedrock of cost-sensitive applications, particularly in consumer goods and hobbyist segments, whereas SLA offers unparalleled surface finish and accuracy for dental, jewelry, and eyewear markets. SLS platforms, with their capacity for support-free, complex geometries, are increasingly chosen for functional parts that require robustness and chemical resistance. Across application categories, prototyping retains its status as the principal entry point for most adopters, but production parts are expanding rapidly, especially in custom production runs and low-volume manufacturing that benefit from design freedom and minimized tooling costs. Functional components, once relegated to lab environments, are transitioning into end-use scenarios, reinforcing the need for validated material qualifications.
Plastic type also exerts a strong influence: ABS continues to serve as the workhorse for general-purpose applications, yet nylon’s superior strength and thermal tolerance make it indispensable in automotive and industrial use cases. PETG and PLA, lauded for their balanced performance and broader material availability, are capturing market share in consumer-centric and educational settings. Finally, end-use industry segmentation highlights divergent trajectories: aerospace stakeholders prioritize weight reduction and flame retardancy, automotive companies seek durable under-hood components, healthcare providers depend on biocompatible and sterilizable materials, while industrial and consumer goods enterprises explore all material categories to address their distinct performance and regulatory demands.
This comprehensive research report categorizes the 3D Printing Plastics market into clearly defined segments, providing a detailed analysis of emerging trends and precise revenue forecasts to support strategic decision-making.
- Material Form
- Printing Technology
- Application
- Plastic Type
- End Use Industry
Regional Dynamics Driving 3D Plastics Adoption
Regional dynamics play a critical role in shaping the trajectory of 3D printing plastics adoption, driven by factors such as regulatory frameworks, infrastructure maturity, and localized industry demand. In the Americas, robust investments in aerospace and automotive additive programs have fueled demand for high-performance materials, while government incentives in North America have accelerated the development of domestic polymer manufacturing and recycling ecosystems. Latin American markets, though still emerging, are showing early interest in low-cost filament solutions, particularly for educational and small-batch production use cases.
Across Europe, Middle East & Africa, stringent environmental regulations and circular economy mandates are compelling material suppliers to innovate in recyclable and bio-based polymers. Western European nations lead in precision resin applications for healthcare and jewelry, whereas Eastern European manufacturers are adopting SLS and FDM at a rapid clip to modernize legacy industrial processes. In the Middle East, infrastructure investments and defense projects are catalyzing the adoption of advanced powders and resins, while African markets are gradually integrating entry-level systems and PLA-based materials for prototyping and educational initiatives.
The Asia-Pacific region exhibits the fastest overall growth, underpinned by expansive industrial modernization programs in China, Japan, and South Korea. Automotive OEMs are co-developing nylon powders for functional parts, electronics manufacturers are deploying PETG in rapid prototyping cycles, and a surge of domestic resin producers is meeting demand for standard and engineering photopolymers. Southeast Asian markets are likewise embracing 3D printing plastics at an accelerated pace, driven by cost-efficient FDM solutions and increasing local capacity for material formulation and post-processing services.
This comprehensive research report examines key regions that drive the evolution of the 3D Printing Plastics market, offering deep insights into regional trends, growth factors, and industry developments that are influencing market performance.
- Americas
- Europe, Middle East & Africa
- Asia-Pacific
Competitive Landscape Leading Innovators and Emerging Players
The competitive landscape of 3D printing plastics is characterized by established chemical conglomerates intensifying their focus on additive-tailored formulations and agile startups pioneering disruptive materials. Legacy polymer suppliers are leveraging their scale to optimize production and distribution networks, enabling them to offer consistent quality across filament, powder, and resin lines. Concurrently, specialized resin producers are investing in patent-protected chemistries that deliver unmatched thermal stability, abrasion resistance, or rapid cure kinetics, often collaborating with equipment manufacturers to co-engineer integrated hardware-material solutions.
Emerging players are carving out niches by addressing underserved opportunities, such as biocompatible dental resins, soft-touch TPU powders, and recycled PLA filaments tailored for consumer markets. Strategic alliances between material scientists and digital design platforms are accelerating the validation of new plastic types, while mergers and acquisitions are reshaping the supplier ecosystem by consolidating IP portfolios and broadening material catalogs. These dynamics underscore the importance of agility, as companies with robust R&D capabilities and strategic partnerships will be best positioned to respond to evolving customer specifications and regulatory requirements.
This comprehensive research report delivers an in-depth overview of the principal market players in the 3D Printing Plastics market, evaluating their market share, strategic initiatives, and competitive positioning to illuminate the factors shaping the competitive landscape.
- BASF SE
- Covestro AG
- Evonik Industries AG
- Arkema S.A.
- Koninklijke DSM N.V.
- Saudi Basic Industries Corporation
- Stratasys Ltd.
- 3D Systems Corporation
- DuPont de Nemours, Inc.
- Eastman Chemical Company
Strategic Imperatives for Forward-Thinking Organizations
Organizations aiming to thrive in the rapidly evolving 3D printing plastics market must adopt a multi-pronged strategy that prioritizes material agility, supply chain robustness, and collaborative innovation. First, expanding material portfolios to include high-performance powders and specialized resins will enable a broader range of end-use applications and insulate businesses from segment-specific downturns. Closely linked to this is the need to forge partnerships across the value chain-engaging with equipment manufacturers, design software providers, and end users-to co-develop formulations that align with precise functional requirements.
Second, building resilience against trade policy shifts requires a proactive procurement framework. This includes diversifying sourcing geographies, investing in domestic polymer production capabilities, and establishing recycling and reuse programs to lower raw material dependencies. Third, organizations should harness digital twins and predictive analytics to fine-tune process parameters, optimize material consumption, and reduce quality deviations. Finally, committing to sustainability through bio-based polymers and closed-loop recycling will not only fulfill regulatory mandates but also resonate with end-customers who demand environmentally responsible manufacturing practices.
Rigorous Methodology Underpinning the Analysis
This research rests on a rigorous methodology designed to ensure both breadth and depth of analysis. Primary data collection involved interviews with senior executives, materials scientists, and manufacturing experts across a diverse range of industries to capture first-hand insights into material performance, adoption drivers, and supply chain challenges. These qualitative perspectives were complemented by a comprehensive review of secondary sources, including scientific journals, patent filings, trade associations, and regulatory publications, to validate emerging trends and benchmark technological advancements.
Quantitative data was sourced from proprietary industry databases and aggregated with publicly available statistics to construct a robust intelligence framework. Triangulation techniques were applied to reconcile discrepancies, while trend analysis and cross-segmentation comparisons illuminated growth pockets and strategic inflection points. All findings underwent peer review by subject matter experts to ensure objectivity, accuracy, and relevance, providing stakeholders with a reliable foundation for strategic planning and investment decisions.
Explore AI-driven insights for the 3D Printing Plastics market with ResearchAI on our online platform, providing deeper, data-backed market analysis.
Ask ResearchAI anything
World's First Innovative Al for Market Research
Synthesis of Core Insights and Strategic Outlook
As the 3D printing plastics landscape continues to expand, the interplay between material innovation, technological advancement, and regulatory dynamics will define the trajectory of additive manufacturing’s next chapter. Enhanced powders, resins, and filaments are breaking traditional performance barriers, unlocking applications in critical sectors such as aerospace, healthcare, and automotive. At the same time, evolving trade policies and sustainability imperatives are compelling industry participants to embrace agility and collaboration.
By synthesizing insights across segmentation, regional markets, and competitive dynamics, this summary offers a clear roadmap for navigating complexity and seizing emerging opportunities. As organizations refine their additive strategies, they must balance immediate operational efficiencies with long-term commitments to material diversification and sustainable practices. The ability to anticipate regulatory shifts, leverage strategic partnerships, and invest in next-generation polymers will ultimately determine market leadership in the rapidly evolving world of 3D printing plastics.
This section provides a structured overview of the report, outlining key chapters and topics covered for easy reference in our 3D Printing Plastics market comprehensive research report.
- Preface
- Research Methodology
- Executive Summary
- Market Overview
- Market Dynamics
- Market Insights
- Cumulative Impact of United States Tariffs 2025
- 3D Printing Plastics Market, by Material Form
- 3D Printing Plastics Market, by Printing Technology
- 3D Printing Plastics Market, by Application
- 3D Printing Plastics Market, by Plastic Type
- 3D Printing Plastics Market, by End Use Industry
- Americas 3D Printing Plastics Market
- Europe, Middle East & Africa 3D Printing Plastics Market
- Asia-Pacific 3D Printing Plastics Market
- Competitive Landscape
- ResearchAI
- ResearchStatistics
- ResearchContacts
- ResearchArticles
- Appendix
- List of Figures [Total: 26]
- List of Tables [Total: 373 ]
Secure Comprehensive Insights: Connect with Ketan Rohom
To gain an in-depth understanding of the forces molding the 3D printing plastics market and secure strategic guidance tailored to your organization’s priorities, engage directly with Ketan Rohom, Associate Director, Sales & Marketing at 360iResearch. Ketan brings a wealth of experience in guiding enterprises through complex market landscapes and can provide you with a customized consultation to explore sample insights, receive a detailed briefing, and discuss practical deployment of the report’s findings. Reach out today to schedule your consultation, gain early access to cutting-edge intelligence, and position your organization at the forefront of innovation in 3D printing plastics.
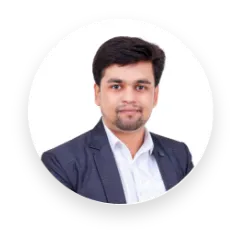
- How big is the 3D Printing Plastics Market?
- What is the 3D Printing Plastics Market growth?
- When do I get the report?
- In what format does this report get delivered to me?
- How long has 360iResearch been around?
- What if I have a question about your reports?
- Can I share this report with my team?
- Can I use your research in my presentation?