Introduction to the Critical Role of 3D Wafer Bump Inspection
The growing complexity of semiconductor packaging has elevated the importance of precise inspection techniques for ensuring device reliability. As industries embrace advanced 3D wafer bump architectures to meet demands for miniaturization and high performance, inspection systems that detect defects early in the manufacturing process become indispensable. This executive summary explores the latest breakthroughs in inspection modalities, highlights seismic shifts reshaping the competitive landscape, and examines how evolving trade policies influence operations. By delving into segmented market dynamics, regional divergence, and the strategic positioning of leading providers, decision-makers can align their strategies to harness emerging opportunities. Transitioning from traditional 2D methods to hybrid acoustic, optical, and radiographic solutions, the industry seeks to optimize yields while reducing risks. This introduction sets the stage for a detailed analysis of the transformative forces propelling the 3D wafer bump inspection ecosystem.
Transformative Shifts Redefining the Inspection Landscape
The inspection ecosystem has undergone transformative shifts driven by converging technological and market forces. First, the fusion of acoustic B-Scan and C-Scan capabilities with optical 3D imaging has enabled holistic defect detection that was previously unattainable. Advances in computed tomography and X-ray radiography add another layer of depth, revealing subsurface irregularities and voids. Second, end-user demand from automotive and aerospace sectors for high-reliability packages has accelerated adoption of multi-modal inspection platforms. Electric vehicles and connected cars now mandate stringent quality controls, while diagnostic equipment in the medical field requires zero-defect processes. Third, the integration of edge computing and AI-driven image processing software has turned raw data into actionable insights in real time, shortening cycle times and reducing false-call rates. Fourth, the shift toward in-line production inspection, including post-bond and reflow checks, enables proactive process adjustments, minimizing scrap. Together, these converging trends have elevated inspection from a final quality gate to a continuous assurance mechanism.
Assessing the Cumulative Impact of 2025 U.S. Tariffs
The introduction of new tariff measures in 2025 has compounded the complexity of cross-border supply chains for wafer bump inspection equipment. As duties apply to critical components such as laser scanners and camera systems sourced globally, manufacturers face increased landed costs and extended lead times. These tariffs have prompted firms to reassess contractual terms with suppliers, negotiate localized warranties, and explore alternative manufacturing hubs to mitigate cost pressures. Additionally, some vendors have streamlined product portfolios to focus on high-margin solutions less susceptible to tariff fluctuations. Trade policy uncertainty has also encouraged collaborative R&D initiatives between domestic and foreign players to develop qualification protocols that may qualify inspection equipment for preferential treaties. Consequently, stakeholders must maintain agile sourcing strategies and closely monitor regulatory developments to safeguard margins and avoid production bottlenecks.
Key Insights Derived from Comprehensive Segmentation Analysis
When segmenting by Technology Type, the landscape comprises acoustic inspection modalities-split between B-Scan and C-Scan techniques-alongside optical systems that deliver both 2D and 3D imaging, as well as radiography approaches leveraging computed tomography and X-ray inspections for subsurface analysis. Customers in different end-user industries demand tailored solutions, with aerospace navigation and military equipment requiring ultra-high reliability, connected cars and electric vehicles emphasizing throughput, smartphones and wearables focusing on miniaturized inspection stages, factory automation and robotics prioritizing in-line integration, and diagnostic equipment and implantable devices necessitating zero-defect assurance. Considering Component Type, the ecosystem spans hardware such as camera systems, laser scanners, and a variety of sensors, complemented by software solutions that include both data analysis platforms and advanced image processing suites. Inspection Process segmentation reveals distinct workflows: final product inspections covering form-factor and packaging checks, in-line production inspections encompassing post-bond and reflow stages, and pre-production inspections dedicated to bump and wafer scrutiny. Finally, wafer inspection varies by die interconnect methodology, with ball grid array wafers, C4 wafers, and flip chip wafers each presenting unique challenges in bump uniformity, coplanarity, and void detection. By understanding these layered segmentation dimensions, stakeholders can pinpoint where innovation and investment will yield maximum quality gains.
This comprehensive research report categorizes the 3D Wafer Bump Inspection System market into clearly defined segments, providing a detailed analysis of emerging trends and precise revenue forecasts to support strategic decision-making.
- Technology Type
- End-User Industry
- Component Type
- Inspection Process
- Type of Inspection Wafer
Regional Dynamics Shaping Inspection System Adoption
Across the Americas, strong growth in semiconductor fabrication capacity-particularly in the United States and Mexico-drives demand for robust inspection platforms capable of handling high-mix, low-volume production. Meanwhile, research investments in Canada have seeded niche innovation in acoustic scanning. In Europe, Middle East & Africa, stringent automotive quality standards and defense procurement cycles in Germany, France, and the U.K. reinforce requirements for integrated optical and radiographic inspection systems, while burgeoning manufacturing hubs in Israel and the Gulf States explore robotics-enabled in-line solutions. The Asia-Pacific region stands out as the largest adopter, with China’s rapidly expanding foundries and advanced packaging ventures in Taiwan and South Korea fueling demand for end-to-end inspection suites. Japan’s legacy inspection equipment manufacturers continue to innovate, and Southeast Asian electronics clusters leverage cost-effective pre-production inspection to improve yield before final assembly.
This comprehensive research report examines key regions that drive the evolution of the 3D Wafer Bump Inspection System market, offering deep insights into regional trends, growth factors, and industry developments that are influencing market performance.
- Americas
- Asia-Pacific
- Europe, Middle East & Africa
Strategic Positioning of Leading Inspection System Providers
Market leaders vary in their strategic focus and technological strengths. Camtek Ltd. excels in high-precision optical metrology, continually enhancing its 3D imaging throughput. FCM Co., Ltd. is recognized for customized acoustic scanning modules that address complex geometry in next-generation packages. Hitachi High-Tech Corporation leverages decades of radiography expertise to deliver computed tomography systems with rapid reconstruction algorithms. Inspectrology, LLC combines multi-modal hardware with turnkey software to simplify adoption for mid-tier manufacturers. KLA-Tencor Corporation remains a frontrunner in integrated inspection suites that align with foundry-grade process controls. Nordson Corporation and Rudolph Technologies, Inc. both prioritize software-centric platforms, offering scalable data analytics and cloud-enabled monitoring. Onto Innovation Inc. differentiates by unifying imaging and metrology under a single user interface. Silicon Valley Microelectronics, Inc. focuses on miniaturized sensor nodes for in-line inspection, while Trio-Tech International specializes in portable laser scanning solutions suited for R&D and field service applications. Collectively, these key players drive competitive innovation and set performance benchmarks.
This comprehensive research report delivers an in-depth overview of the principal market players in the 3D Wafer Bump Inspection System market, evaluating their market share, strategic initiatives, and competitive positioning to illuminate the factors shaping the competitive landscape.
- Camtek Ltd.
- FCM Co., Ltd.
- Hitachi High-Tech Corporation
- Inspectrology, LLC
- KLA-Tencor Corporation
- Nordson Corporation
- Onto Innovation Inc.
- Rudolph Technologies, Inc.
- Silicon Valley Microelectronics, Inc.
- Trio-Tech International
Actionable Recommendations to Navigate Market Complexities
Leaders should adopt a multi-pronged strategy to stay ahead. First, invest in converged inspection modalities that harmonize acoustic, optical, and radiographic data streams to provide a unified defect map. Second, cultivate partnerships with foundries and packaging houses to co-develop qualification protocols that shorten customer adoption cycles. Third, focus R&D spending on AI-driven image processing software that reduces false calls and automates root-cause analysis. Fourth, build modular hardware architectures that can be upgraded in the field to adapt to evolving process nodes and wafer formats. Fifth, establish regional support centers near key fabrication clusters in North America, EMEA, and Asia-Pacific to deliver responsive service and training. Finally, engage proactively with standards bodies and trade associations to influence inspection norms and preempt regulatory shifts.
Explore AI-driven insights for the 3D Wafer Bump Inspection System market with ResearchAI on our online platform, providing deeper, data-backed market analysis.
Ask ResearchAI anything
World's First Innovative Al for Market Research
Concluding Perspectives on Future Growth Trajectories
The 3D wafer bump inspection market stands at a pivotal juncture, propelled by rapid advances in imaging technology and shifts in global supply chains. As end-users demand higher reliability and lower defect rates, inspection systems must evolve from passive quality gates to active process optimization tools. The interplay of tariff policies, regional capacity expansions, and emerging end-user requirements underscores the need for agility and collaboration. By leveraging detailed segmentation insights, understanding regional dynamics, and learning from the strategic playbooks of leading providers, stakeholders can develop robust roadmaps for growth. A disciplined focus on modularity, AI-integration, and multi-modal convergence will set the stage for sustained leadership in this critical facet of semiconductor manufacturing.
This section provides a structured overview of the report, outlining key chapters and topics covered for easy reference in our 3D Wafer Bump Inspection System market comprehensive research report.
- Preface
- Research Methodology
- Executive Summary
- Market Overview
- Market Dynamics
- Market Insights
- Cumulative Impact of United States Tariffs 2025
- 3D Wafer Bump Inspection System Market, by Technology Type
- 3D Wafer Bump Inspection System Market, by End-User Industry
- 3D Wafer Bump Inspection System Market, by Component Type
- 3D Wafer Bump Inspection System Market, by Inspection Process
- 3D Wafer Bump Inspection System Market, by Type of Inspection Wafer
- Americas 3D Wafer Bump Inspection System Market
- Asia-Pacific 3D Wafer Bump Inspection System Market
- Europe, Middle East & Africa 3D Wafer Bump Inspection System Market
- Competitive Landscape
- ResearchAI
- ResearchStatistics
- ResearchContacts
- ResearchArticles
- Appendix
- List of Figures [Total: 26]
- List of Tables [Total: 768 ]
Contact Ketan Rohom to Access the Detailed Market Research Report
To explore the full depth of this market analysis and secure a competitive edge, contact Ketan Rohom, Associate Director, Sales & Marketing. Reach out via email or phone to obtain the comprehensive report, which offers granular insights, case studies, and strategic frameworks tailored to your organization’s needs. Act now to harness these findings and drive your inspection strategy forward.
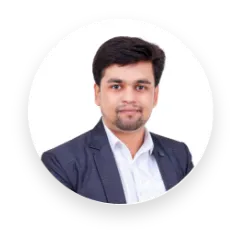
- When do I get the report?
- In what format does this report get delivered to me?
- How long has 360iResearch been around?
- What if I have a question about your reports?
- Can I share this report with my team?
- Can I use your research in my presentation?