Introduction to the 4 Die 4 Below Bolt Cold Forging Machine Market Dynamics
The evolving demands of modern manufacturing have placed unprecedented emphasis on precision, speed, and flexibility in cold forging processes, thrusting the 4 Die 4 Below bolt cold forging machine into the spotlight. As industries pivot toward lighter, stronger, and more complex components, this specialized equipment has emerged as a critical enabler of high-efficiency production. By leveraging a four-die configuration combined with a downward stroke mechanism, manufacturers achieve tight dimensional tolerances while minimizing material waste and cycle times.
In response to tightening quality standards and surging demand for miniature yet robust components in automotive, aerospace, and electronics sectors, the 4 Die 4 Below platform offers a balance of rigidity and repeatability. Advanced control systems synchronize die movements, ensuring uniform deformation across high-volume runs. Meanwhile, modular tooling designs facilitate rapid product changeovers, empowering operations to address volatile order patterns without compromising turnaround.
Transitioning into the era of interconnected factories, this machinery represents a nexus of mechanical engineering excellence and digital integration. Its capabilities extend beyond traditional forging to embrace data-driven insights, predictive maintenance, and real-time process adjustments. As we explore the forces reshaping this market, it becomes clear that mastering these machines is essential for stakeholders seeking competitive advantage in a complex global landscape.
Transformative Shifts Reshaping the Cold Forging Machine Landscape
Over the past decade, the cold forging landscape has undergone seismic shifts driven by digital transformation, material innovation, and evolving customer expectations. Industry 4.0 initiatives have infused smart sensors and cloud connectivity into forging presses, enabling adaptive control loops that optimize force profiles and detect anomalies before they escalate. Consequently, manufacturers are achieving up to 20% reductions in downtime and significantly lower scrap rates.
Simultaneously, the push for lightweighting has propelled the adoption of non-ferrous alloys and high-strength steels, prompting machine builders to refine force distribution and bolster structural frames. Customization has also surged, with end users demanding small-batch runs of intricate components. To accommodate these needs, suppliers have introduced rapid-change die systems and software-driven toolpath planning.
Moreover, sustainability mandates have elevated the importance of energy-efficient hydraulics and regenerative braking technologies. Producers are integrating variable-frequency drives and energy recovery modules to curtail power consumption, aligning forging operations with corporate carbon reduction targets. These transformative shifts underscore an industry in continuous evolution-one where agility and technological sophistication define success.
Cumulative Impact of 2025 United States Tariffs on Cold Forging Equipment
As of 2025, escalating United States tariffs on imported forging machinery have introduced a layer of complexity to procurement strategies. Facing duty increases on select equipment categories, manufacturers have reevaluated supply agreements and accelerated local sourcing. Consequently, domestic machine builders are experiencing heightened demand, while import-reliant operations seek tariff mitigation through free trade agreements and tariff engineering techniques.
The cost pass-through effect has been palpable, with forgings of critical fasteners and precision components experiencing modest price adjustments. However, companies that proactively diversified their supplier base have insulated themselves from the steepest duty hikes. Some have relocated assembly lines closer to domestic markets, optimizing logistics and compliance with local content provisions.
Furthermore, tariff-driven margins have incentivized investments in in-house forging capabilities. By reclaiming value from duty-affected imports, several industry leaders have expanded their production portfolios. Ultimately, the cumulative impact of these measures has reshaped competitive dynamics, underscoring the importance of strategic agility in navigating evolving trade policies.
Key Segmentation Insights Informing Market Strategies and Technology Adoption
A granular view of the market reveals diverse performance across machine type, where hydraulic cold forging machinery continues to dominate due to its robust force control, while mechanical units gain traction in high-speed applications and servo-driven models appeal to those prioritizing energy efficiency and precision. When examining product type, electrical components and fasteners maintain steady volume, yet non-ferrous metals are capturing share amid lightweighting trends, and precision components-particularly automotive parts and industrial machinery parts-are commanding premium pricing and driving technology upgrades.
End-use industry segmentation highlights that aerospace and marine sectors demand exacting tolerances, while construction projects rely on cost-effective steel components. The automotive domain differentiates between commercial vehicles and passenger cars, each with unique volume and customization needs. From the perspective of material type, aluminum and brass sustain growth in corrosion-resistant applications, copper remains vital for electrical conductivity, and steel-especially carbon steel and stainless steel-retains its status as the backbone of heavy-duty forging.
Press capacity analysis indicates that medium-tonnage equipment in the 1,000–5,000 ton range is the workhorse of most facilities, whereas machines above 5,000 ton are reserved for heavy-duty production, and presses below 1,000 ton enable light-duty, specialized runs. Focusing on application, bolt forging still accounts for the bulk of output, but nut forging, screw forging, and stud forging each carve out niche segments based on part complexity and cycle requirements.
Technological features such as automatic feed systems, CNC integration, and high-speed performance have become decision-critical, with production volume considerations ranging from high-volume, cost-driven operations to low-volume, high-mix job shops and medium-volume balanced setups. Finally, end-user profiles vary across aftermarket suppliers, custom manufacturers, and OEMs, with automobile manufacturers representing a significant subset of OEM demand.
This comprehensive research report categorizes the 4 Die 4 Below Bolt Cold Forging Machine market into clearly defined segments, providing a detailed analysis of emerging trends and precise revenue forecasts to support strategic decision-making.
- Machine Type
- Product Type
- End-Use Industry
- Material Type
- Press Capacity
- Application
- Technological Features
- Production Volume
- End-User Profile
Key Regional Insights Highlighting Geographical Market Drivers and Trends
Regional dynamics play a pivotal role in shaping market opportunities and challenges. In the Americas, robust automotive and aerospace supply chains anchor demand for advanced cold forging solutions, with domestic manufacturers leveraging proximity to end users to deliver agile support. Meanwhile, local content rules and tariff considerations continue to influence procurement decisions.
Across Europe, the Middle East & Africa, emphasis on environmental regulations has spurred the adoption of energy-efficient machinery, while longstanding engineering hubs in Germany and Italy remain centers of innovation. Emerging markets in the Gulf Cooperation Council offer growth potential tied to infrastructure development and diversification efforts.
The Asia-Pacific region stands out for its blend of mature markets in Japan and South Korea-where precision and automation are paramount-and rapid expansion in China and India, driven by heavy concentrations of automotive assembly, consumer electronics, and construction projects. Supply chain resilience and trade agreements will dictate how these regions capture value and respond to global shifts.
This comprehensive research report examines key regions that drive the evolution of the 4 Die 4 Below Bolt Cold Forging Machine market, offering deep insights into regional trends, growth factors, and industry developments that are influencing market performance.
- Americas
- Asia-Pacific
- Europe, Middle East & Africa
Key Companies Insights Spotlighting Leading Manufacturers and Strategic Focus
The competitive landscape features a mix of established multinationals and specialized OEMs driving continuous improvement. AIDA Engineering, Ltd. leads in heavy-duty press innovations, while Chin Fong Machine Industrial Co., Ltd. integrates high-speed performance into its product lineup. Hatebur Metalforming Equipment Ltd. excels in servo-driven platforms, and Henan Jiyuan Iron & Steel (Group) Co., Ltd. leverages integrated steel production to optimize material flow. Komatsu Ltd. brings proven reliability and digital monitoring capabilities to its presses.
In parallel, National Machinery LLC and National Machinery Taiwan Corporation offer tailored solutions with robust service networks, whereas Nedschroef Machinery focuses on high-precision fastener forging systems. Sacma Limbiate S.p.A. combines Italian craftsmanship with automation, and Sakamura USA Inc. addresses North American demand with localized support. Meanwhile, Sinosteel XTMMC benefits from commodity metal integration, Wuxi Zhengyao Machinery Co., Ltd. capitalizes on competitive pricing, and Zhejiang Shengtuo Machinery Manufacturing Co., Ltd. pursues niche customization strategies.
This comprehensive research report delivers an in-depth overview of the principal market players in the 4 Die 4 Below Bolt Cold Forging Machine market, evaluating their market share, strategic initiatives, and competitive positioning to illuminate the factors shaping the competitive landscape.
- AIDA Engineering, Ltd.
- Chin Fong Machine Industrial Co., Ltd.
- Hatebur Metalforming Equipment Ltd.
- Henan Jiyuan Iron & Steel (Group) Co., Ltd.
- Komatsu Ltd.
- National Machinery LLC
- National Machinery Taiwan Corporation
- Nedschroef Machinery
- Sacma Limbiate S.p.A.
- Sakamura USA Inc.
- Sinosteel XTMMC
- Wuxi Zhengyao Machinery Co., Ltd.
- Zhejiang Shengtuo Machinery Manufacturing Co., Ltd.
Actionable Recommendations for Industry Leaders in Cold Forging Machinery
To thrive amid intensifying competition and shifting regulatory landscapes, industry leaders should prioritize the integration of smart automation technologies, specifically advanced CNC controls and real-time process analytics that reduce cycle variability. Evaluating the adoption of servo-driven cold forging machines can yield significant energy savings and improve precision, particularly for high-mix, low-volume production scenarios.
Diversification of material capabilities-ranging from aluminum and brass to high-grade stainless steel-will unlock opportunities across lightweighting and corrosion-resistant applications. Concurrently, proactive monitoring of tariff developments and strategic supplier diversification will mitigate cost volatility and safeguard supply chain continuity.
Investments in modular tooling solutions, combined with rapid die-change systems, will enhance operational agility, while partnerships with OEMs and custom manufacturers can accelerate product development and secure long-term contracts. Finally, cultivating a workforce adept in digital maintenance and data analysis ensures that predictive maintenance programs maximize machine uptime and extend equipment lifespan.
Explore AI-driven insights for the 4 Die 4 Below Bolt Cold Forging Machine market with ResearchAI on our online platform, providing deeper, data-backed market analysis.
Ask ResearchAI anything
World's First Innovative Al for Market Research
Conclusion on Strategic Opportunities and Market Evolution
In aggregate, the 4 Die 4 Below cold forging sector stands at the intersection of precision engineering and digital transformation, offering manufacturers a pathway to drive efficiency, quality, and sustainability. By synthesizing insights from shifting market drivers, tariff impacts, segmentation analyses, regional dynamics, and competitive strategies, stakeholders can formulate cohesive roadmaps that capitalize on technological advancements and evolving customer requirements.
Ultimately, the ability to adapt machine capabilities, streamline procurement strategies, and engage in strategic partnerships will determine which organizations emerge as industry frontrunners. As the market continues its trajectory toward automation and customization, a clear-eyed focus on agility and innovation will underpin long-term success.
This section provides a structured overview of the report, outlining key chapters and topics covered for easy reference in our 4 Die 4 Below Bolt Cold Forging Machine market comprehensive research report.
- Preface
- Research Methodology
- Executive Summary
- Market Overview
- Market Dynamics
- Market Insights
- Cumulative Impact of United States Tariffs 2025
- 4 Die 4 Below Bolt Cold Forging Machine Market, by Machine Type
- 4 Die 4 Below Bolt Cold Forging Machine Market, by Product Type
- 4 Die 4 Below Bolt Cold Forging Machine Market, by End-Use Industry
- 4 Die 4 Below Bolt Cold Forging Machine Market, by Material Type
- 4 Die 4 Below Bolt Cold Forging Machine Market, by Press Capacity
- 4 Die 4 Below Bolt Cold Forging Machine Market, by Application
- 4 Die 4 Below Bolt Cold Forging Machine Market, by Technological Features
- 4 Die 4 Below Bolt Cold Forging Machine Market, by Production Volume
- 4 Die 4 Below Bolt Cold Forging Machine Market, by End-User Profile
- Americas 4 Die 4 Below Bolt Cold Forging Machine Market
- Asia-Pacific 4 Die 4 Below Bolt Cold Forging Machine Market
- Europe, Middle East & Africa 4 Die 4 Below Bolt Cold Forging Machine Market
- Competitive Landscape
- ResearchAI
- ResearchStatistics
- ResearchContacts
- ResearchArticles
- Appendix
- List of Figures [Total: 34]
- List of Tables [Total: 682 ]
Call-to-Action: Engage with Ketan Rohom for Comprehensive Market Insights
For a comprehensive exploration of these findings and to acquire in-depth market intelligence tailored to your strategic objectives, reach out to Ketan Rohom, Associate Director, Sales & Marketing. Engage now to secure the full report and equip your organization with the actionable insights needed to navigate the complexities of the cold forging machine market.
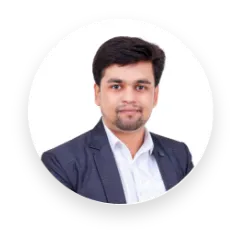
- When do I get the report?
- In what format does this report get delivered to me?
- How long has 360iResearch been around?
- What if I have a question about your reports?
- Can I share this report with my team?
- Can I use your research in my presentation?