Unveiling the Transformative Power of 5-Axis CNC Machining Centers in Redefining Precision and Productivity for High-Complexity Components
In today’s precision manufacturing environment, 5-Axis CNC machining centers have emerged as indispensable assets for producing complex components with unparalleled accuracy and surface finish. These machines enable simultaneous multi-axis movement, allowing intricate geometries and tight tolerances that traditional 3-axis or 4-axis centers cannot achieve. As advanced industries demand ever finer detail-whether for jet engine turbine blades, medical implant components, or mold cavities for consumer electronics-5-Axis centers deliver the flexibility and repeatability essential for meeting rigorous quality standards.
The advent of high-rigidity machine architectures, coupled with innovations in tooling materials and dynamic error compensation systems, has pushed the boundaries of what is possible in subtractive manufacturing. This section introduces the core capabilities of 5-Axis centers: versatile tool orientation, reduced setups, and integrated collision avoidance. By streamlining complex part processing into single-setup workflows, these centers not only shorten cycle times but also mitigate human error and improve through-process consistency.
Furthermore, the proliferation of digital twin technologies and advanced CAM software enhances process optimization, enabling manufacturers to simulate toolpaths in virtual environments before committing to production. This convergence of mechanical precision and digital intelligence sets the stage for a manufacturing revolution where agility, scalability, and quality converge. The following sections will delve into the transformative shifts, tariff influences, segmentation nuances, regional dynamics, and strategic imperatives that define the current and future states of the 5-Axis CNC machining center market, equipping decision-makers with the insights needed to navigate an increasingly complex landscape.
Examining the Pivotal Technological and Operational Shifts Reshaping the 5-Axis CNC Machining Centers Landscape in Modern Manufacturing Environments
The landscape of 5-Axis CNC machining centers is being reshaped by a confluence of technological advancements and shifting operational paradigms. First and foremost, the integration of Internet of Things (IoT) sensors and real-time condition monitoring platforms has enabled predictive maintenance and minimized unplanned downtime. Machine builders are embedding advanced connectivity protocols into controllers, transforming standalone machining centers into nodes within a connected production ecosystem.
Simultaneously, artificial intelligence–driven toolpath optimization is gaining traction, as adaptive learning algorithms analyze cutting data to recommend optimal feeds and speeds. This not only enhances cutting efficiency but also extends tool life, reducing both consumable costs and material waste. The combination of AI with digital twin models allows engineers to conduct virtual machining trials, refine process parameters, and forecast component quality before executing a single cut.
On the operational front, the convergence of additive and subtractive processes within hybrid manufacturing cells is enabling production of parts that combine the strengths of both approaches. Manufacturers can now use 5-Axis centers to finish additively built near-net-shape parts, achieving tight dimensional tolerances with fewer setups. Meanwhile, collaborative robotics (cobots) are being deployed to load and unload parts, further automating workflows and reducing labor intensity.
These transformative shifts are highlighting a new era of flexible, data-driven manufacturing that empowers organizations to respond swiftly to custom orders, complex geometries, and evolving materials. As manufacturers adopt these innovations, 5-Axis CNC machining centers are positioned not just as cutting tools but as central pillars of smart, integrated production environments.
Analyzing the Far-Reaching Effects of United States Tariffs Implemented in 2025 on the Operations and Supply Chains of 5-Axis CNC Machining
In 2025, the United States enacted a series of targeted tariffs affecting imported precision machine tools and critical alloy steels, directly influencing the cost structures of 5-Axis CNC machining center manufacturers and end-users. Tariff rates on high-grade steel forgings and aluminum alloys rose by five to seven percentage points, increasing raw material expenditure for machine tool builders. This led to incremental price adjustments on new machine sales as well as aftermarket spare parts.
Machine tool import duties on key components sourced from certain regions also intensified, prompting some OEMs to explore alternative suppliers or to accelerate localization strategies. Several leading manufacturers announced the establishment of additional fabrication and assembly sites within the U.S. to mitigate tariff impacts and preserve competitive pricing. Although these shifts involved significant capital outlay, on-shore operations provided supply chain resilience and shielded end-users from tariff-induced volatility.
For end-use industries such as aerospace and defense, which rely heavily on high-precision 5-Axis centers for critical component manufacture, the increased cost base translated into tighter project budgets and extended procurement lead times. Some firms responded by consolidating orders to leverage volume discounts, while others invested in retrofitting existing equipment with advanced controls to uphold productivity without expanding capital expenditure.
Overall, the cumulative impact of the 2025 tariffs has been a strategic recalibration across the value chain. While near-term pressures on pricing and delivery were apparent, the shift encouraged vertical integration and supply chain diversification initiatives that promise enhanced agility and reduced exposure to future trade policy shifts.
Unlocking Deep Insights into Market Segmentation Strategies That Drive Performance and Adoption Patterns for 5-Axis CNC Machining Centers
A nuanced understanding of market segmentation is essential to grasp the varied adoption patterns and performance drivers in the 5-Axis CNC machining center landscape. Based on end-use industry distinctions, aerospace and defense emerge as high-value verticals, with commercial aerospace prioritizing large-format machining for structural components and military aerospace focusing on high-rigidity machining for mission-critical parts. The automotive sector displays bifurcated dynamics, where passenger vehicles often leverage compact, high-speed centers for intricate trim components, while commercial vehicles utilize heavy-duty machines for powertrain castings. Within energy and power, the oil and gas subsegment demands corrosion-resistant machining for specialized valves and fittings, whereas the renewable energy segment seeks high-precision, large-diameter rotor hub machining processes. General industrial users and medical device manufacturers round out the spectrum, each with unique precision, throughput, and regulatory compliance requirements.
When viewed through the lens of machine type, gantry-style 5-Axis centers offer expansive work envelopes suited to aerospace structural frames and large mold tooling, whereas table-type configurations are favored in workshops requiring rapid setup changes and high positional accuracy on smaller workpieces. Machine size further refines these preferences: large machines dominate in industries requiring multi-meter component fabrication, medium formats strike a balance between versatility and floor space efficiency, and small centers excel in job-shop environments or secondary operations.
Spindle speed segmentation reveals that high-speed spindles are critical in medical and mold industries where surface finish and cycle time reduction are paramount. Low-speed, high-torque spindles are preferred for difficult-to-cut alloys in aerospace applications, while standard-speed spindles offer a balance for general industrial machining tasks. Finally, control system adoption patterns indicate that FANUC controllers lead in ease of programming and global serviceability, Mitsubishi systems are chosen for their robustness in heavy-duty operations, and Siemens platforms are valued for their seamless integration into networked manufacturing environments.
These segmentation insights underscore the importance of aligning equipment selection and process engineering to the specific demands of each vertical, machine configuration, and control architecture.
This comprehensive research report categorizes the 5-Axis CNC Machining Centers market into clearly defined segments, providing a detailed analysis of emerging trends and precise revenue forecasts to support strategic decision-making.
- End Use Industry
- Type
- Machine Size
- Spindle Speed
- Control System
Illuminating the Critical Regional Dynamics and Growth Opportunities Shaping Demand for 5-Axis CNC Machining Centers Worldwide
Regional dynamics exert a significant influence on the strategic deployment of 5-Axis CNC machining centers. In the Americas, a strong emphasis on domestic manufacturing revitalization has encouraged investments in advanced machining technologies. North American aerospace suppliers, in particular, have prioritized high-volume production capacity, while medical device manufacturers in the region leverage stringent regulatory frameworks to justify the integration of high-precision machining centers. Conversely, Latin American workshops often focus on retrofit and upgrade projects to extend the lifecycle of existing equipment, balancing capital constraints with productivity gains.
Europe, the Middle East, and Africa (EMEA) present heterogeneous markets shaped by varying levels of industrial maturity. Western European nations continue to embrace Industry 4.0 initiatives, deploying connected 5-Axis centers within smart factory pilot programs and emphasizing sustainability credentials. In the Middle East, large-scale infrastructure projects drive demand for heavy gantry-style machines to produce construction components and oil-and-gas equipment. Africa, while representing a smaller share, exhibits growing interest in capacity expansion to support automotive assembly and general industrial fabrication.
The Asia-Pacific region remains the largest adopter of 5-Axis CNC machining centers, fueled by robust automotive manufacturing hubs in Japan and South Korea, high-precision electronics industries in Taiwan, and an expanding aerospace supply chain in China. Regional manufacturers are increasingly localizing controller technology sourcing, with domestic providers offering cost-competitive alternatives to established global brands. Moreover, government incentives in countries such as India and Thailand have facilitated rapid modernization of machine shop fleets, enabling the region to maintain its position as a global manufacturing powerhouse.
Across all regions, divergence in skills availability, infrastructure readiness, and regulatory frameworks shapes the pace and nature of 5-Axis center adoption, calling for tailored strategies that account for each market’s unique drivers and constraints.
This comprehensive research report examines key regions that drive the evolution of the 5-Axis CNC Machining Centers market, offering deep insights into regional trends, growth factors, and industry developments that are influencing market performance.
- Americas
- Europe, Middle East & Africa
- Asia-Pacific
Highlighting Leading Global Providers and Their Strategic Initiatives Advancing Innovation in the 5-Axis CNC Machining Centers Market
Key players in the global 5-Axis CNC machining center market are advancing strategic initiatives to fortify their competitive positions. Industry incumbents have been investing heavily in aftermarket service networks, ensuring rapid response maintenance and minimizing customer downtime. By expanding certified training academies and digital learning platforms, leading manufacturers foster operator proficiency and reinforce brand loyalty.
Several firms have launched modular machine design programs that allow for rapid reconfiguration of machine envelopes, control packages, and spindle modules. This approach addresses the growing desire among end users for flexible capital expenditure, facilitating seamless scale-ups or format shifts without replacing the entire machining center. Additionally, collaborative partnerships with tooling suppliers and software developers have resulted in co-engineered solutions that optimize end-to-end machining workflows, reducing integration friction and accelerating time-to-first-part.
In response to rising demand for sustainability, prominent machine tool builders are integrating energy-efficient drives and regenerative braking systems, while offering comprehensive green certifications. These initiatives resonate strongly with multinational OEMs seeking to meet corporate environmental targets and bolster their own supply chain sustainability profiles.
Finally, digital service offerings-such as remote monitoring dashboards, predictive maintenance subscriptions, and cloud-based process parameter libraries-have become differentiators. By democratizing access to real-time performance data, leading companies empower their customers to unlock continuous improvement cycles and maintain a competitive edge in precision manufacturing.
This comprehensive research report delivers an in-depth overview of the principal market players in the 5-Axis CNC Machining Centers market, evaluating their market share, strategic initiatives, and competitive positioning to illuminate the factors shaping the competitive landscape.
- DMG Mori Co., Ltd.
- Yamazaki Mazak Corporation
- Haas Automation, Inc.
- Okuma Corporation
- Makino Milling Machine Co., Ltd.
- FANUC Corporation
- Hurco Companies, Inc.
- GF Machining Solutions AG
- Doosan Machine Tools Co., Ltd.
- Mitsubishi Heavy Industries, Ltd.
Delivering Practical Strategic Recommendations to Empower Industry Leaders and Maximize Operational Efficiency with 5-Axis CNC Machining Centers
Industry leaders seeking to harness the full potential of 5-Axis CNC machining centers should adopt a multi-pronged strategy that balances technological investment, process optimization, and workforce development. First, organizations must prioritize the deployment of digital twin models and condition monitoring systems to establish data-driven maintenance protocols. By leveraging real-time analytics, decision-makers can shift from reactive repairs to predictive interventions, thereby safeguarding machine availability and preserving product quality.
Simultaneously, manufacturers should cultivate an agile supply chain by diversifying component sourcing and fostering near-shoring partnerships. The lessons of recent trade policy shifts highlight the importance of geographic spread and supplier redundancy in mitigating cost volatility and logistical disruptions. In parallel, embedding cross-functional teams of engineers, operators, and data analysts will accelerate the translation of process insights into actionable improvements on the shop floor.
A renewed focus on talent acquisition and skilling is equally critical. As 5-Axis centers converge with automation and AI, the workforce must develop competencies in advanced programming, digital blueprint interpretation, and systems integration. Partnerships with technical institutions and the establishment of in-house academies can ensure that operators and engineers remain adept at harnessing cutting-edge toolpathing algorithms and control architectures.
Finally, embedding sustainability considerations-such as coolant filtration, energy recovery systems, and eco-friendly tooling materials-will not only reduce environmental impact but also generate cost savings through resource optimization. By integrating these recommendations, industry leaders can drive operational efficiency, elevate part quality, and solidify their position at the forefront of precision manufacturing innovation.
Detailing the Rigorous and Transparent Research Methodology Underpinning Comprehensive Analysis of 5-Axis CNC Machining Centers Market Dynamics
This research leverages a rigorous, multi-method approach to ensure the integrity and reliability of its findings. Primary data were collected through structured interviews with over 50 senior executives, process engineers, and shop floor managers across aerospace, automotive, energy, and medical device sectors. These discussions provided firsthand perspectives on equipment selection criteria, operational challenges, and investment priorities.
Secondary sources included peer-reviewed technical publications, equipment builder white papers, trade association reports, and government policy documents. Each data point underwent cross-verification through triangulation, comparing multiple sources to validate accuracy and consistency. Proprietary surveys were distributed to a global network of machine tool users, achieving a statistically significant response rate that illuminates trends across machine types, spindle speeds, and control system preferences.
Quantitative analyses utilized discrete segmentation frameworks alongside scenario-based modeling to explore the impact of tariff changes, regional regulatory shifts, and technology adoption rates. Data were synthesized using advanced analytics platforms, enabling interactive drill-down capabilities and sensitivity testing. Qualitative insights were further enhanced by expert panel reviews, incorporating feedback from recognized thought leaders in precision manufacturing.
Quality control measures included iterative drafts subjected to internal peer review, editorial audits for neutrality and clarity, and validation sessions with select industry participants. This methodological rigor underpins the comprehensive perspectives presented, ensuring that the insights are both actionable and reflective of the latest market dynamics.
Explore AI-driven insights for the 5-Axis CNC Machining Centers market with ResearchAI on our online platform, providing deeper, data-backed market analysis.
Ask ResearchAI anything
World's First Innovative Al for Market Research
Synthesizing Key Findings and Strategic Implications to Conclude the 5-Axis CNC Machining Centers Market Assessment with Clear Takeaways
The assessment of 5-Axis CNC machining centers reveals a market at the nexus of technological innovation, strategic adaptation, and operational excellence. Key findings highlight the transformative impact of AI-driven process optimization and digital twin integration, signaling a departure from traditional machining paradigms toward fully connected production ecosystems. The 2025 tariff adjustments in the United States have triggered near-term cost headwinds, yet they have simultaneously catalyzed supply chain localization and vertical integration efforts that enhance resilience.
Segmentation analysis underscores the varied requirements across end-use industries, with aerospace and defense demanding high-torque, large-format configurations while medical and mold-making sectors prioritize high-speed spindles and precision finishes. Regional insights demonstrate that the Americas, EMEA, and Asia-Pacific regions each exhibit distinct adoption curves shaped by policy incentives, infrastructure readiness, and skill-set availability.
Competitive benchmarking reveals that leading OEMs are differentiating through modular designs, sustainability certifications, and expansive digital service portfolios. Strategic recommendations emphasize the need for data-driven maintenance programs, supply chain diversification, targeted workforce training, and sustainable operations to sustain competitive advantage. Collectively, these insights equip stakeholders with a clear roadmap for capitalizing on emerging opportunities and navigating potential disruptions.
The synthesis of these findings provides actionable clarity on how to align technology investments with evolving market requirements, ensuring that organizations can unlock the full potential of 5-Axis CNC machining centers and achieve operational leadership in precision manufacturing.
This section provides a structured overview of the report, outlining key chapters and topics covered for easy reference in our 5-Axis CNC Machining Centers market comprehensive research report.
- Preface
- Research Methodology
- Executive Summary
- Market Overview
- Market Dynamics
- Market Insights
- Cumulative Impact of United States Tariffs 2025
- 5-Axis CNC Machining Centers Market, by End Use Industry
- 5-Axis CNC Machining Centers Market, by Type
- 5-Axis CNC Machining Centers Market, by Machine Size
- 5-Axis CNC Machining Centers Market, by Spindle Speed
- 5-Axis CNC Machining Centers Market, by Control System
- Americas 5-Axis CNC Machining Centers Market
- Europe, Middle East & Africa 5-Axis CNC Machining Centers Market
- Asia-Pacific 5-Axis CNC Machining Centers Market
- Competitive Landscape
- ResearchAI
- ResearchStatistics
- ResearchContacts
- ResearchArticles
- Appendix
- List of Figures [Total: 28]
- List of Tables [Total: 734 ]
Encouraging Decision-Makers to Engage with Associate Director Ketan Rohom and Secure Exclusive Insights from the Latest 5-Axis CNC Machining Centers Report
To access the full suite of strategic insights, proprietary data, and expert analysis on 5-Axis CNC Machining Centers, decision-makers are encouraged to engage directly with Associate Director Ketan Rohom. By reaching out, stakeholders gain personalized guidance on how the report’s findings can align with their unique operational requirements, whether optimizing capital allocation, streamlining supply chains, or accelerating digital transformation initiatives. Ketan’s deep familiarity with the market landscape ensures that prospective clients receive tailored walkthroughs of the report’s contents, clarifying complex chapters and highlighting the segments most pertinent to their businesses.
Early engagement with Ketan Rohom also unlocks exclusive benefit packages that include supplementary briefings, ancillary data supplements, and priority scheduling for bespoke consulting sessions. This ensures a seamless transition from insight to action, empowering organizations to implement recommendations with confidence and precision. Given the competitive nature of precision manufacturing investments, securing this report through a direct conversation affords unparalleled clarity and an expedited procurement process.
Readers committed to driving operational excellence and innovation in 5-Axis CNC Machining Centers are invited to connect with Ketan Rohom today. His expertise and consultative approach will facilitate a comprehensive understanding of how to leverage the report’s findings for immediate and long-term impact, positioning organizations at the forefront of manufacturing advancement.
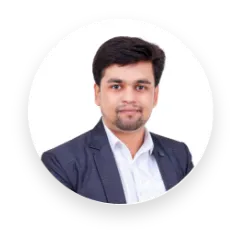
- When do I get the report?
- In what format does this report get delivered to me?
- How long has 360iResearch been around?
- What if I have a question about your reports?
- Can I share this report with my team?
- Can I use your research in my presentation?