Introduction
The rapid advancement of precision engineering has propelled 5-axis vertical CNC milling machines to the forefront of modern manufacturing. By integrating simultaneous multi-axis movement, these machines achieve unparalleled accuracy, complex geometry, and efficient toolpaths that meet the demanding requirements of aerospace components, intricate medical implants, and high-tolerance automotive parts. As industries strive to maximize productivity and minimize cycle times, the adoption of sophisticated control algorithms and adaptive machining strategies has become indispensable.
Manufacturers now face a competitive imperative: stay ahead by leveraging cutting-edge technology or risk falling behind. Against this backdrop, this executive summary delves into the transformative shifts reshaping the landscape, examines the cumulative impact of recent tariff policies, unveils key segmentation and regional insights, highlights leading players driving innovation, and offers actionable recommendations for decision-makers. By synthesizing the latest developments, challenges, and strategic imperatives, this report equips stakeholders with the clarity and foresight needed to capitalize on opportunities and navigate uncertainties in the evolving 5-axis vertical CNC milling market.
Transformative Shifts in the Industry Landscape
Over the last decade, multi-axis capabilities have evolved from niche applications into mainstream production tools. Enhanced servo drives and real-time adaptive control have unlocked unprecedented levels of process stability, enabling manufacturers to transition from manual interventions to fully automated machining sequences. Concurrently, the integration of digital twins and predictive maintenance modules has accelerated workflows by reducing unplanned downtime and extending tool life.
At the same time, customer expectations have shifted toward mass customization and just-in-time delivery, compelling OEMs to adopt flexible cell configurations and modular designs. Breakthrough developments in high-pressure coolant delivery and specialized tool coatings have further elevated material removal rates while preserving surface integrity across a wider range of alloys and composites. This convergence of digital transformation, advanced materials science, and lean manufacturing practices has redefined competitive benchmarks.
Cumulative Impact of United States Tariffs in 2025
In 2025, newly imposed tariffs on imported machine tools and critical components have introduced additional cost pressures across the supply chain. Domestic manufacturers encounter higher input expenses for controls, spindles, and specialized tooling sourced from overseas, impacting profit margins and forcing pricing adjustments. Simultaneously, end-users have adopted localized sourcing strategies to mitigate financial exposure, leading to reconfigured procurement networks and strategic partnerships with domestic equipment suppliers.
The ripple effects extend to aftermarket services and spare parts, where higher duties have prompted distributors to stock critical inventory domestically, thereby reducing lead times but increasing carrying costs. In response, several machine tool builders have restructured production footprints, moving subassembly operations closer to key markets. This reorganization underscores the importance of agility in supply chain management and has accelerated investments in nearshoring, contract manufacturing, and collaborative R&D ventures to secure resilient operations.
Key Segmentation Insights
Examining the market through end-use lenses reveals that the aerospace and defense sector continues to invest heavily in 5-axis machining for both aircraft manufacturing and space technologies, where complex geometries and tight tolerances are non-negotiable. Parallel growth in medical and healthcare applications underscores demand for precision implants and surgical instruments, while industrial machinery producers leverage multi-axis flexibility to streamline production lines. The automotive and transportation industry, seeking lighter yet stronger components, also drives adoption, alongside energy and power companies machining intricate turbine housings and heat exchangers.
From a technology perspective, advanced control systems now dominate, with adaptive control and predictive maintenance capabilities enabling self-learning machining cycles. Sophisticated cooling and lubrication systems optimize thermal stability, while deep integration of CAD/CAM software streamlines toolpath generation. Tool holder designs, tailored for dynamic rigidity, further enhance performance.
Performance capabilities continue to advance. Material removal efficiency has improved through high-feed strategies, and five-axis coordination ensures consistent precision across complex contours. Hybrid coordination approaches blend interpolated movements for roughing and finishing passes, delivering superior surface finish quality. Precision engineering protocols now routinely deliver sub-micron tolerances.
Operational methodologies have embraced full automation integration, incorporating robotic loading cells with self-diagnostics that identify tool wear before failure. Customization options allow end-users to reconfigure machining centers rapidly for diverse job requirements, while process optimization algorithms fine-tune cutting parameters in real time.
Structural design innovations prioritize floor space efficiency and frame robustness, with monolithic castings and reinforced box-way architectures enhancing rigidity. Flexible machine architecture accommodates future upgrades, and advanced spindle configurations balance high-speed operation with torque maximization to tackle a broader range of materials.
Comprehensive service and support offerings, including installation and training programs, tailored maintenance services, multi-tier technical support, and warranty and upgrade packages, have become key differentiators. By ensuring minimal downtime and rapid knowledge transfer, leading providers enable smoother adoption curves and higher overall equipment effectiveness.
This comprehensive research report categorizes the 5-axis Vertical CNC Milling Machine market into clearly defined segments, providing a detailed analysis of emerging trends and precise revenue forecasts to support strategic decision-making.
- End Use
- Machine Technology
- Performance Capabilities
- Operational Methodology
- Structural Design
- Service And Support
Key Regional Insights
In the Americas, investment in reshoring and advanced manufacturing incentives has accelerated deployment of 5-axis vertical CNC machines in both established automotive hubs and burgeoning aerospace clusters. Companies benefit from localized service networks and government programs aimed at bolstering competitiveness.
The Europe, Middle East & Africa region leverages its strong aerospace and defense manufacturing base, with several Tier 1 suppliers and integrators adopting sophisticated 5-axis cells. Demand is further driven by medical device producers in Central Europe and the Gulf, where precision machining under strict regulatory standards is essential.
In Asia-Pacific, the landscape is characterized by rapid industrial digitalization across China, Japan, South Korea, and Southeast Asia. Manufacturers in this region emphasize high-speed spindle configurations and smart factory implementations to meet surging domestic and export demand, capitalizing on substantial investments in Industry 4.0 initiatives.
This comprehensive research report examines key regions that drive the evolution of the 5-axis Vertical CNC Milling Machine market, offering deep insights into regional trends, growth factors, and industry developments that are influencing market performance.
- Americas
- Asia-Pacific
- Europe, Middle East & Africa
Key Companies Insights
Leading solution providers are differentiating through technology portfolios and global service footprints. Established multinational corporations such as DMG MORI AG, Mazak Corporation, and Okuma Corporation continue to set industry benchmarks with their high-precision machining platforms and integrated software suites. At the same time, agile innovators like Advance CNC Technologies Inc., Craft CNC Solutions Inc., and QEM Technologies are carving out niches by delivering customizable systems with rapid lead times.
Legacy specialists including Haas Automation Incorporated, Hardinge Inc., and EMCO Group extend their appeal through cost-effective small-batch machining centers tailored for job shops and educational institutions. Japanese titans Citizen Machinery Co., Ltd., Brother Industries, Ltd., and Matsuura Machinery Corporation prioritize vertical integration, leveraging in-house control systems and spindle technologies to optimize performance. Meanwhile, emerging players such as Dalian Minli CNC Equipment Co., Ltd., Vertex CNC Industries, and Yangli Machinery Co., Ltd. gain traction by offering competitive configurations and localized support in key growth markets.
This comprehensive research report delivers an in-depth overview of the principal market players in the 5-axis Vertical CNC Milling Machine market, evaluating their market share, strategic initiatives, and competitive positioning to illuminate the factors shaping the competitive landscape.
- Advance CNC Technologies Inc.
- Brother Industries, Ltd.
- Chiron Group
- Citizen Machinery Co., Ltd.
- Craft CNC Solutions Inc.
- Dalian Minli CNC Equipment Co., Ltd.
- DMG MORI AG
- Doosan Machine Tools
- EMCO Group
- Fadal Engineering Inc.
- GF Machining Solutions
- Haas Automation Incorporated
- Hardinge Inc.
- Hermle AG
- Hurco Companies, Inc.
- JTEKT Corporation
- Kitamura Machinery Inc.
- Makino Inc.
- Matsuura Machinery Corporation
- Mazak Corporation
- Mid West Machine Tools
- Nakamura-Tome Precision Industry Co., Ltd.
- Okamoto Machine Tools Inc.
- Okuma Corporation
- ProTech Machining Systems
- QEM Technologies
- Qinchuan Machine Tool Group Corporation
- Sany Machine Tools Co., Ltd.
- Vertex CNC Industries
- Yangli Machinery Co., Ltd.
Actionable Recommendations for Industry Leaders
Industry leaders should prioritize investment in adaptive control algorithms and digital twin integration to maintain a competitive edge. Establishing robust local service and spare parts ecosystems will mitigate the impact of tariff fluctuations and reduce unplanned downtime. Collaborative R&D partnerships with materials science innovators can unlock new tooling solutions that enhance material removal rates and surface integrity.
Furthermore, piloting modular machine architectures that support incremental upgrades allows manufacturers to adapt to evolving job requirements without full capital replacement. Implementing real-time process optimization software will drive consistency and yield improvements, while training programs focused on advanced multi-axis programming will empower operators and reduce cycle times. Finally, aligning sales and marketing strategies with regional industrial policies and incentive programs ensures that value propositions resonate with local and global stakeholders alike.
Explore AI-driven insights for the 5-axis Vertical CNC Milling Machine market with ResearchAI on our online platform, providing deeper, data-backed market analysis.
Ask ResearchAI anything
World's First Innovative Al for Market Research
Conclusion
The 5-axis vertical CNC milling landscape is at a pivotal juncture, driven by technological breakthroughs, shifting supply chain dynamics, and evolving end-use demands. By understanding the interplay between advanced controls, structural design innovations, and service-oriented business models, industry stakeholders can chart a path toward sustainable growth.
As markets adapt to new tariff realities and regional investment patterns, companies that embrace digital transformation, agile production methodologies, and strategic partnerships will lead the next wave of precision machining excellence.
This section provides a structured overview of the report, outlining key chapters and topics covered for easy reference in our 5-axis Vertical CNC Milling Machine market comprehensive research report.
- Preface
- Research Methodology
- Executive Summary
- Market Overview
- Market Dynamics
- Market Insights
- Cumulative Impact of United States Tariffs 2025
- 5-axis Vertical CNC Milling Machine Market, by End Use
- 5-axis Vertical CNC Milling Machine Market, by Machine Technology
- 5-axis Vertical CNC Milling Machine Market, by Performance Capabilities
- 5-axis Vertical CNC Milling Machine Market, by Operational Methodology
- 5-axis Vertical CNC Milling Machine Market, by Structural Design
- 5-axis Vertical CNC Milling Machine Market, by Service And Support
- Americas 5-axis Vertical CNC Milling Machine Market
- Asia-Pacific 5-axis Vertical CNC Milling Machine Market
- Europe, Middle East & Africa 5-axis Vertical CNC Milling Machine Market
- Competitive Landscape
- ResearchAI
- ResearchStatistics
- ResearchContacts
- ResearchArticles
- Appendix
- List of Figures [Total: 28]
- List of Tables [Total: 550 ]
Call-To-Action (CTA) with Ketan Rohom
Elevate your strategic decision-making with in-depth market intelligence and bespoke guidance. Contact Ketan Rohom, Associate Director, Sales & Marketing, to secure access to the definitive report on 5-axis vertical CNC milling. Gain the insights you need to drive innovation, optimize operations, and outperform the competition.
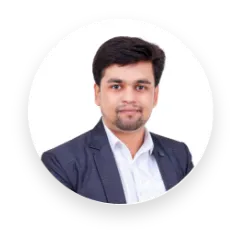
- When do I get the report?
- In what format does this report get delivered to me?
- How long has 360iResearch been around?
- What if I have a question about your reports?
- Can I share this report with my team?
- Can I use your research in my presentation?