The Automotive Contract Manufacturing Market size was estimated at USD 71.61 billion in 2024 and expected to reach USD 78.64 billion in 2025, at a CAGR 9.74% to reach USD 125.08 billion by 2030.

Navigating the Evolving Terrain of Automotive Contract Manufacturing
The automotive contract manufacturing sector stands at a pivotal crossroads, merging legacy production expertise with the pressures of electrification, digitalization, and geopolitical realignment. Driven by the dual imperative to reduce costs and deliver innovation, original equipment manufacturers and their tiered partners are redefining the paradigms of outsourcing and collaboration. In this evolving ecosystem, contract manufacturers have become linchpins in balancing flexibility with scale, serving as both custodians of complex assembly processes and incubators for next-generation technologies.
Amid mounting regulatory scrutiny on emissions and safety, alongside escalating capital intensity for advanced powertrain and sensor integration, this analysis unpacks the forces reshaping production footprints, supply-chain architecture, and partnership models. By examining the drivers of transformation-from emerging vehicle architectures and modular platforms to new service offerings-this executive summary provides decision-makers with a clear lens on current dynamics and strategic imperatives. It establishes the foundation for understanding how shifts in policy, consumer demand, and technology adoption are catalyzing a new era of collaborative manufacturing excellence.
Emerging Forces Reshaping the Manufacturing Ecosystem
Transformation in contract manufacturing is propelled by the convergence of electrification mandates, autonomous mobility ambitions, and heightened sustainability targets. Electrified powertrains, spanning battery electric and plug-in hybrid configurations, demand closer integration between battery systems, electric motors, and control units than traditional internal combustion engine platforms. Meanwhile, autonomous capabilities are escalating requirements for advanced sensors, control algorithms, and vehicle-level validation, ushering in an era of software-driven production and iterative prototyping.
Simultaneously, digital engineering and Industry 4.0 frameworks are enabling real-time visibility into line performance and quality metrics. Additive manufacturing for rapid prototyping, combined with precision stamping and robotics-driven welding, is compressing development cycles while supporting customization at scale. These technological accelerators are complemented by an increased focus on circularity, with painting and coating processes optimized for lower emissions and high-strength materials. Together, these forces are dismantling traditional batch-and-queue models in favor of flexible, cell-based assembly lines that can pivot quickly to new vehicle variants and volumes.
Assessing the Ripple Effects of New US Tariffs in 2025
The introduction of new United States tariffs in 2025 has injected renewed complexity into global supply chains, particularly for steel and aluminum components crucial to chassis and body fabrication. Rising import duties have prompted many contract manufacturers to reassess supplier agreements and evaluate nearshore alternatives to mitigate cost exposure. Subsequently, partnerships with North American steel mills and aluminum extruders have intensified as firms seek tariff-free material flows and reduced lead times.
Moreover, the cumulative impact extends beyond raw materials. Electronics sub-modules, such as infotainment systems and sensors imported from Asia, now face stepped-up scrutiny and higher levies, compelling OEMs and their transaction manufacturing partners to diversify sourcing or localize critical assembly operations. In response, several service providers are expanding their footprint in Mexico and Canada, leveraging existing free-trade frameworks. These strategic shifts underline the necessity for agile procurement strategies and robust scenario planning to balance cost containment with product integrity under evolving trade policies.
Decoding Market Segmentation to Drive Strategic Positioning
Understanding market segmentation is essential to aligning production capabilities with shifting demand patterns. When viewed through the lens of vehicle type, contract manufacturers must accommodate the distinct requirements of autonomous vehicles ranging from Level 2 driver assistance systems to fully autonomous Level 5 buses or shuttles. Simultaneously, growth in heavy and light commercial vehicles has placed a premium on high-duty drivetrain components and robust chassis assemblies, while the surge in battery electric vehicles and plug-in hybrid electric vehicles intensifies competition for expertise in battery module assembly and electric motor integration. At the same time, traditional hybrid electric and mild hybrid vehicle lines continue to sustain a significant share of contract assembly workloads, and passenger vehicle segments from compact to luxury sedans require tailored interior and exterior trim system processes.
Component-level insights further refine strategic positioning, as body and interior sub-assemblies-including exterior panels, seating systems, and trim modules-demand sophisticated robotics and quality inspection systems, whereas chassis functions such as brake, steering, and suspension assemblies depend on precise tooling and material traceability. Electronics subcomponent production has evolved to encompass everything from control unit programming to sensor calibration and infotainment module final testing. Meanwhile, powertrain worksites are increasingly focused on integrating advanced battery systems, electric motors, engines, and transmissions within unified assembly cells to streamline handoffs and reduce cycle times.
The nature of service engagement also shapes investment imperatives. Complex assembly workflows, whether final assembly of fully built vehicles or sub-assembly of critical modules, contrast sharply with high-volume series production lines designed for thin margins and predictable volumes. Low-volume runs and prototyping initiatives, including rapid prototyping and tooling developments, require a different operational mindset, prioritizing agility and design feedback loops. Production scale further diversifies the landscape, as high-volume gigafactories and assembly plants co-exist with medium-batch artisanal workshops and small-scale pilot lines.
Technology adoption is another key vector. Additive manufacturing platforms offer bespoke tooling and rapid design iteration, while painting and coating systems calibrated for waterborne and powder coat processes support sustainability targets. Traditional stamping and welding operations remain fundamental for high-strength steel and aluminum structures, demanding ongoing investment in servo-drive presses and laser-guided robotic arms. Contract arrangements also differ by engagement model, whether pure contract manufacturing with predefined scopes, toll manufacturing that leverages client-owned materials, or turnkey projects where full end-to-end responsibility is assumed. Finally, the distinction between OEM production and aftermarket refurbishment underscores divergent quality assurance protocols and turnaround expectations, reinforcing the need for specialized capabilities and certifications across the value chain.
This comprehensive research report categorizes the Automotive Contract Manufacturing market into clearly defined segments, providing a detailed analysis of emerging trends and precise revenue forecasts to support strategic decision-making.
- Vehicle Type
- Component Type
- Service Type
- Production Scale
- Technology
- Contract Type
- End Use
Regional Dynamics Steering Production and Partnerships
Regional dynamics are shaping the competitive landscape and investment decisions across the contract manufacturing domain. In the Americas, the promise of nearshoring has driven a resurgence of production activity along the Mexico–United States corridor, leveraging favorable trade agreements to offset tariff pressures. Automotive clusters in the Midwest and Southeastern states continue to attract joint ventures between OEMs and manufacturing partners, while Canada’s specialized facilities concentrate on high-value electrified drivetrain modules and precision-machined components.
Across Europe, the Middle East & Africa region, stringent emissions regulations and consumer appetite for premium offerings have catalyzed a shift toward electric vehicle platforms, prompting a wave of capacity expansions in Germany, France, and the United Kingdom. These hubs are complemented by emerging low-cost manufacturing zones in Eastern Europe and North Africa, where labor arbitrage and logistics access to both European and Middle Eastern markets create compelling value propositions. Investment in advanced painting, coating, and joining technologies in these markets underscores a regional strategy that balances cost optimization with regulatory compliance and quality excellence.
Asia-Pacific remains a focal point for scale and innovation, led by China’s vertically integrated supply chains for battery modules, electric motors, and control electronics. India’s burgeoning assembly plants have begun integrating medium-volume production lines for passenger and commercial vehicles, while ASEAN countries are solidifying their positions as export gateways for both internal combustion and electrified platforms. Technology outsourcing to specialized providers in South Korea and Japan continues to flourish, particularly for sensors, infotainment, and powertrain control units, highlighting the region’s pivotal role in end-to-end system integration and rapid prototyping.
This comprehensive research report examines key regions that drive the evolution of the Automotive Contract Manufacturing market, offering deep insights into regional trends, growth factors, and industry developments that are influencing market performance.
- Americas
- Europe, Middle East & Africa
- Asia-Pacific
Profiles of Leading Innovators Transforming Supply Chains
Leading contract manufacturing firms are redefining industry norms through strategic investments and collaborative alliances. Established automotive suppliers have enhanced their value proposition by integrating digital engineering suites that facilitate virtual commissioning and predictive maintenance of production lines. These capabilities not only shrink time to market but also ensure higher first-pass yields in body-in-white and drivetrain sub-assembly processes.
At the same time, nimble specialized providers are carving out niches in advanced battery assembly and high-precision stamping, securing partnerships with both OEMs and battery cell manufacturers. These firms leverage modular plant designs and shared digital twins to enable fast changeovers between vehicle variants. Their ability to co-develop rapid prototyping services with in-house additive manufacturing labs has become a critical differentiator for automakers pursuing custom mobility solutions and limited-edition runs.
Moreover, alliances between global engineering consultancies and contract producers are becoming more common, aiming to deliver turnkey manufacturing solutions that encompass everything from facility design and process validation to training programs and aftermarket support. This convergence of consulting and execution expertise underscores an industry trend toward integrated service offerings that cover the entire vehicle lifecycle.
This comprehensive research report delivers an in-depth overview of the principal market players in the Automotive Contract Manufacturing market, evaluating their market share, strategic initiatives, and competitive positioning to illuminate the factors shaping the competitive landscape.
- Magna International Inc.
- Lear Corporation
- Forvia SA
- Plastic Omnium SE
- Adient plc
- Valeo SA
- Gestamp, S.A.
- Benteler International AG
- Jabil Inc.
- Valmet Automotive Oyj
Strategic Imperatives to Secure Competitive Advantage
To maintain a competitive edge, companies must invest in flexible, reconfigurable assembly lines that support both high-volume series production and low-volume custom builds. Strengthening local supplier networks through strategic nearshoring initiatives can mitigate exposure to future tariff shocks while improving responsiveness to demand fluctuations. Investing in digital twins and predictive analytics will enhance operational transparency, enabling proactive maintenance and real-time quality control.
Leaders should also prioritize sustainability by adopting eco-friendly painting and coating methods and integrating closed-loop recycling processes for critical materials. Cross-functional collaboration between design, engineering, and manufacturing teams will accelerate product introductions and reduce variant complexity. Finally, upskilling the workforce in areas such as robotics programming, software validation, and additive manufacturing will be essential to harness the full potential of next-generation production technologies.
Rigorous Methodology Underpinning the Market Analysis
This analysis is grounded in a multi-stage research methodology that combines qualitative and quantitative approaches. Primary interviews were conducted with senior executives at vehicle manufacturers, Tier 1 suppliers, and contract producers to capture firsthand insights on operational challenges and strategic priorities. Secondary research encompassed industry whitepapers, trade publications, and regulatory filings to validate emerging trends and regional developments.
Data triangulation techniques were employed to reconcile divergent viewpoints and ensure robustness in identifying critical success factors. Regional coverage spanned North America, Europe, the Middle East & Africa, and Asia-Pacific, reflecting the global nature of contract manufacturing networks. Detailed segmentation frameworks were developed to assess variations in service type, technology adoption, and production scale, facilitating an in-depth understanding of market drivers without relying on proprietary estimations or forecasts.
Explore AI-driven insights for the Automotive Contract Manufacturing market with ResearchAI on our online platform, providing deeper, data-backed market analysis.
Ask ResearchAI anything
World's First Innovative Al for Market Research
Synthesis of Key Takeaways for Stakeholder Action
The convergence of electrification, autonomy, and trade policy adjustments is fundamentally altering the contours of automotive contract manufacturing. Segmented insights into vehicle and component types highlight the need for specialized assembly capabilities, while regional analyses underscore the importance of adaptive sourcing strategies. Technology imperatives, from additive manufacturing to advanced welding and coating, continue to raise the bar for quality and efficiency. Together with targeted recommendations, this summary equips industry stakeholders with the context needed to navigate complexity and position their organizations for sustainable growth.
This section provides a structured overview of the report, outlining key chapters and topics covered for easy reference in our Automotive Contract Manufacturing market comprehensive research report.
- Preface
- Research Methodology
- Executive Summary
- Market Overview
- Market Dynamics
- Market Insights
- Cumulative Impact of United States Tariffs 2025
- Automotive Contract Manufacturing Market, by Vehicle Type
- Automotive Contract Manufacturing Market, by Component Type
- Automotive Contract Manufacturing Market, by Service Type
- Automotive Contract Manufacturing Market, by Production Scale
- Automotive Contract Manufacturing Market, by Technology
- Automotive Contract Manufacturing Market, by Contract Type
- Automotive Contract Manufacturing Market, by End Use
- Americas Automotive Contract Manufacturing Market
- Europe, Middle East & Africa Automotive Contract Manufacturing Market
- Asia-Pacific Automotive Contract Manufacturing Market
- Competitive Landscape
- ResearchAI
- ResearchStatistics
- ResearchContacts
- ResearchArticles
- Appendix
- List of Figures [Total: 30]
- List of Tables [Total: 822 ]
Connect with Ketan Rohom to Accelerate Your Next Move
To explore these insights in depth and secure tailored strategies for your organization, reach out to Ketan Rohom, Associate Director, Sales & Marketing, to purchase the comprehensive market research report and gain an actionable edge in automotive contract manufacturing
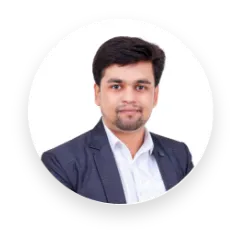
- How big is the Automotive Contract Manufacturing Market?
- What is the Automotive Contract Manufacturing Market growth?
- When do I get the report?
- In what format does this report get delivered to me?
- How long has 360iResearch been around?
- What if I have a question about your reports?
- Can I share this report with my team?
- Can I use your research in my presentation?