The Aero-Engine Composites Market size was estimated at USD 4.32 billion in 2024 and expected to reach USD 4.79 billion in 2025, at a CAGR 10.28% to reach USD 7.78 billion by 2030.

Unveiling the Strategic Imperative of Aero-Engine Composite Solutions Amidst Industry Dynamics and Sustainable Innovation
The aerospace sector’s relentless pursuit of higher efficiency and lower environmental impact has propelled composite materials to the forefront of aero-engine design. These advanced materials, characterized by superior strength-to-weight ratios and enhanced thermal resistance, are revolutionizing engine performance while simultaneously contributing to global decarbonization goals. In recent years, stringent emissions regulations and fuel efficiency targets have converged with rapid advances in composite manufacturing, resulting in unprecedented demand for innovative solutions that can withstand extreme operating conditions and facilitate next-generation propulsion architectures.
Against this evolving backdrop, industry stakeholders must navigate a complex interplay of regulatory mandates, technological breakthroughs, and shifting supply-chain dynamics. Material suppliers and engine OEMs are investing heavily in research and development to push the boundaries of ceramic matrix composites, carbon fiber-reinforced polymers, and titanium matrix composites. As collaboration between aerospace primes, tiered suppliers, and technology providers intensifies, the imperative to understand core market drivers and potential bottlenecks becomes ever more critical. In the following sections, this report dissects the forces reshaping the landscape, analyzes policy and procurement impacts, and uncovers strategic pathways for sustained competitive advantage.
Embracing Radical Transformations in Aero-Engine Composites as Sustainability Imperatives and Ultra-High Performance Benchmarks Surge Across Aviation
The aerospace materials ecosystem is undergoing a paradigm shift defined by the intersection of sustainability imperatives and performance ambitions. Driven by ambitious carbon-reduction targets set by international regulatory bodies, manufacturers are accelerating their adoption of high-temperature ceramic matrix composites to replace legacy metal alloys in turbine sections. Simultaneously, the maturation of automated fiber placement techniques is enabling more intricate geometries and higher productivity, effectively balancing cost pressures against uncompromising safety and reliability standards.
Furthermore, digitalization is embedding itself more deeply into composite design and production workflows. Coupled with multi-scale simulation and real-time process monitoring, digital twins are empowering engineers to refine fiber orientation, resin flow, and curing cycles for both off-axis and on-axis placement strategies. As airlines and defense customers alike prioritize lifecycle performance, the fusion of advanced analytics with additive manufacturing and resin transfer molding processes is charting a new course for aero-engine composites-one in which agility, traceability, and sustainability coalesce to define competitive leadership.
Unraveling the Escalating Cumulative Impact of United States Tariff Measures on Aero-Engine Composite Supply Chains and Cost Structures by 2025
Recent U.S. trade policies have introduced layers of complexity to composite supply chains, amplifying cost volatility and necessitating strategic recalibrations. The extension of Section 232 tariffs on select imported alloys combined with heightened scrutiny under Section 301 investigations has reverberated through precursor and fiber markets, contributing to upstream price pressures. These measures, intended to bolster domestic production capacity, have had the unintended consequence of driving buyers to seek alternative suppliers offshore, often resulting in longer lead times and added logistical overhead.
Over the long term, the cumulative impact of these tariff measures is reshaping procurement strategies for both OEMs and Tier 1 providers. Companies are reevaluating sourcing footprints, increasing inventory buffers, and in some instances forging strategic partnerships with domestic fiber and resin manufacturers to mitigate exposure. At the same time, investment in process innovations such as in-house fiber oxidation and dispersion techniques is gaining traction as a means to bypass import constraints. As a result, ecosystem players that proactively address tariff-induced disruptions will be best positioned to maintain supply continuity and cost stability.
Distilling Actionable Segmentation Insights Across Material Types, Applications, Engine Classes, End Users, and Advanced Composite Technologies
Detailed segmentation of the aero-engine composite market reveals that material type plays a pivotal role in value chain dynamics. Carbon fiber-reinforced polymers continue to dominate in applications where high strength-to-weight performance in fan cases and compressor blades is paramount, while ceramic matrix composites are rapidly gaining traction in high-temperature turbine sections. Titanium matrix composites, although adopted more selectively, are emerging in niche applications that demand a blend of stiffness and thermal resilience at reduced mass compared with conventionally wrought alloys.
When evaluating applications, high-pressure compressor blades and high-pressure turbine blades represent the most stringent performance requirements, driving material innovation and certification efforts. Innovations in automated fiber placement processes for both off-axis and on-axis configurations are delivering tighter tolerances and lower defect rates for these critical components. Beyond engine internals, market segmentation by engine type highlights distinct trajectories: narrow-body turbofans are fueling near-term volume growth, while wide-body variants and turboprop platforms are setting the stage for next-generation hybrid propulsion concepts. Finally, end users ranging from business aviation to military operators demand tailored solutions, and technology pathways through resin transfer molding versus automated fiber placement further differentiate supplier offerings in an increasingly complex competitive landscape.
This comprehensive research report categorizes the Aero-Engine Composites market into clearly defined segments, providing a detailed analysis of emerging trends and precise revenue forecasts to support strategic decision-making.
- Material Type
- Application
- Engine Type
- End User
- Technology
Highlighting Pivotal Regional Dynamics Shaping Aero-Engine Composite Adoption Trends Across Americas, EMEA, and Asia-Pacific Markets
In the Americas, the presence of leading aero-engine OEMs and extensive defense spending have catalyzed the development of localized composite supply chains. Government incentives for advanced manufacturing and additive processes are fostering domestic R&D hubs, while the proximity of major engine assembly facilities in the United States and Canada ensures rapid collaboration across design, testing, and certification phases. Nonetheless, regional players must also navigate trade tensions and maintain agility as U.S. tariff policies evolve.
Europe, the Middle East, and Africa present a heterogeneous landscape characterized by both mature aerospace clusters and emerging hubs. Western European heavyweights are leveraging decades of expertise in composite qualification for flagship commercial and military platforms, whereas Middle Eastern carriers are investing in next-generation fuel efficiency to meet ambitious net-zero targets. Concurrently, growing defense procurements in Africa are stimulating partnerships with established manufacturers to transfer composite know-how, underpinning wider regional diversification.
Asia-Pacific stands out for its rapid industrialization and rising domestic engine programs. Nations like China and India are integrating composite capabilities into national propulsion strategies, often through joint ventures and technology transfer agreements with established Western suppliers. Japan and South Korea continue to refine high-precision fiber placement technologies to serve local OEMs, while Southeast Asian markets are emerging as assembly and MRO centers. This collective dynamism underscores Asia-Pacific’s prominence as both a production powerhouse and a demanding end-market for advanced aero-engine composite solutions.
This comprehensive research report examines key regions that drive the evolution of the Aero-Engine Composites market, offering deep insights into regional trends, growth factors, and industry developments that are influencing market performance.
- Americas
- Europe, Middle East & Africa
- Asia-Pacific
Examining Strategic Maneuvers and Innovation Trajectories of Leading Aero-Engine Composite Suppliers and System Integrators Globally
Leading suppliers in the aero-engine composite domain are actively forging strategic alliances to accelerate technology maturation and market penetration. Global prime OEMs are deepening partnerships with fiber and resin specialists to co-develop next-generation ceramic matrix composites via novel chemical vapor infiltration processes. Concurrently, tiered machine builders are integrating advanced process controls into automated fiber placement systems, enabling real-time quality assurance and reducing cycle times for fan case and compressor blade production.
Established materials companies are also expanding their footprints through targeted acquisitions of niche process innovators, while engine manufacturers are investing in in-house composite capabilities to secure greater vertical integration. This trend is complemented by robust collaboration on digital platforms, where shared data ecosystems support predictive maintenance models for composite components. Collectively, these strategic moves underscore a market environment where innovation trajectories are closely tied to cross-sector partnerships, and the ability to scale both capacity and expertise will define the next wave of competitive advantage.
This comprehensive research report delivers an in-depth overview of the principal market players in the Aero-Engine Composites market, evaluating their market share, strategic initiatives, and competitive positioning to illuminate the factors shaping the competitive landscape.
- Hexcel Corporation
- Toray Industries, Inc.
- Solvay S.A.
- Teijin Limited
- Mitsubishi Chemical Holdings Corporation
- SGL Carbon SE
- Owens Corning
- Gurit Holding AG
- DuPont de Nemours, Inc.
- Park Aerospace Corporation
Crafting High-Impact Strategic Recommendations to Propel Competitiveness, Resilience, and Sustainable Growth within the Aero-Engine Composite Industry Landscape
To thrive in this rapidly evolving market, industry leaders should prioritize investment in ceramic matrix composites as a cornerstone of high-temperature engine architectures. Allocating R&D resources toward scalable chemical vapor infiltration processes and next-generation fiber surface treatments will yield materials capable of withstanding peak turbine section temperatures while delivering weight reduction. In parallel, expanding in-house capabilities for automated fiber placement-including both off-axis and on-axis system integration-will accelerate validation cycles and improve yield in critical blade and case components.
Moreover, companies must cultivate resilient supply chains by diversifying raw material sourcing across multiple geographies and forging strategic collaborations with regional fiber manufacturers. Engaging proactively with policymakers and standards bodies can mitigate the impact of evolving tariff environments, while scenario-based strategic planning will enable rapid reconfiguration of procurement and production footprints. Finally, embedding digital twins and predictive analytics into both design and aftermarket support functions will enhance lifecycle management and generate new revenue streams through value-added service offerings.
Detailing Robust Research Methodology Combining Primary Engagements, Comprehensive Secondary Exploration, and Rigorous Analytical Frameworks
This report’s insights are underpinned by a rigorous, multi-tiered research approach. Primary inputs were gathered through in-depth interviews with engineering leaders at OEMs, CTOs of specialty material firms, procurement heads at tiered suppliers, and regulatory experts from international aviation authorities. These firsthand engagements provided granular perspective on certification challenges, cost structures, and emerging performance targets across diverse engine platforms.
Secondary exploration encompassed comprehensive analysis of technical journals, patent databases, trade association publications, and public financial disclosures. Data triangulation methodologies were applied to validate quantitative findings against qualitative trends, ensuring consistency and accuracy. Advanced analytics, including scenario-driven forecasting and sensitivity testing, further enriched the research framework, while peer validation workshops with industry stakeholders affirmed the robustness of conclusions and strategic imperatives.
Explore AI-driven insights for the Aero-Engine Composites market with ResearchAI on our online platform, providing deeper, data-backed market analysis.
Ask ResearchAI anything
World's First Innovative Al for Market Research
Concluding Reflections on the Future Trajectory of Aero-Engine Composite Innovations, Market Challenges, and Regulatory Imperatives
The convergence of sustainability mandates, performance aspirations, and policy interventions is charting a transformative pathway for aero-engine composite technologies. As material systems evolve from carbon fiber-reinforced polymers to high-temperature ceramic composites, the industry is poised to redefine propulsion efficiency, reduce lifecycle emissions, and enable advanced aircraft architectures. Simultaneously, external pressures-ranging from regional tariff measures to emerging certification protocols-are reshaping supply-chain realities and challenging stakeholders to adapt with agility.
Looking ahead, success will hinge on the ability to synchronize innovation with strategic resilience. Companies that leverage data-driven design tools, granular segmentation insights, and diversified regional partnerships will secure a competitive edge. By embracing proactive engagement with regulatory bodies and investing in next-generation manufacturing processes, leaders can transform potential disruptions into opportunity catalysts. Collectively, these themes illustrate an industry at the threshold of a new era-one defined by the fusion of advanced materials science, digitalization, and global collaboration.
This section provides a structured overview of the report, outlining key chapters and topics covered for easy reference in our Aero-Engine Composites market comprehensive research report.
- Preface
- Research Methodology
- Executive Summary
- Market Overview
- Market Dynamics
- Market Insights
- Cumulative Impact of United States Tariffs 2025
- Aero-Engine Composites Market, by Material Type
- Aero-Engine Composites Market, by Application
- Aero-Engine Composites Market, by Engine Type
- Aero-Engine Composites Market, by End User
- Aero-Engine Composites Market, by Technology
- Americas Aero-Engine Composites Market
- Europe, Middle East & Africa Aero-Engine Composites Market
- Asia-Pacific Aero-Engine Composites Market
- Competitive Landscape
- ResearchAI
- ResearchStatistics
- ResearchContacts
- ResearchArticles
- Appendix
- List of Figures [Total: 28]
- List of Tables [Total: 824 ]
Empowering Decision Makers to Secure Comprehensive Aero-Engine Composite Market Intelligence through Direct Engagement and Tailored Support Offerings
To unlock the full breadth of insights, decision makers are encouraged to connect directly with Ketan Rohom, Associate Director, Sales & Marketing, who stands ready to guide discussions around tailored research packages and bespoke analytical frameworks. By engaging in a strategic dialogue, organizations can align their specific strategic imperatives with a customized service roadmap that addresses unique challenges in material sourcing, supply chain resilience, and technology adoption. This collaborative approach ensures that every recommendation is grounded in actionable intelligence and underpinned by rigorous methodological rigor. Reach out to explore how this comprehensive market intelligence offering can be seamlessly integrated into strategic planning processes, enabling informed, future-ready decisions.
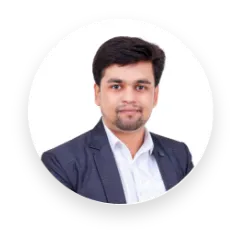
- How big is the Aero-Engine Composites Market?
- What is the Aero-Engine Composites Market growth?
- When do I get the report?
- In what format does this report get delivered to me?
- How long has 360iResearch been around?
- What if I have a question about your reports?
- Can I share this report with my team?
- Can I use your research in my presentation?