The Aero Structure Equipments Market size was estimated at USD 13.93 billion in 2024 and expected to reach USD 14.91 billion in 2025, at a CAGR 6.96% to reach USD 20.86 billion by 2030.

Setting the Stage for Aerostructures Excellence with a Comprehensive Overview of Industry Dynamics and Emerging Opportunities
The aerostructure equipment sector stands at the confluence of advanced engineering, global supply chain intricacies, and evolving regulatory frameworks. Over recent years, both OEMs and MRO providers have grappled with rising performance expectations, necessitating innovations in materials, manufacturing processes, and digital integration. As a result, industry stakeholders are reevaluating traditional design paradigms while embracing new collaboration models that promise efficiency, resilience, and sustainability.
Amid this dynamic backdrop, it becomes essential to understand how diverse product categories-from control surfaces like ailerons, flaps, and spoilers to critical assemblies such as fuselage barrel, nose, and tail cone sections-interact with shifting demand patterns. Similarly, segmenting the market by aircraft type, whether business jets, commercial airliners, helicopters, military platforms, or regional commuters, reveals divergent growth trajectories. These nuances underscore the importance of an inclusive market perspective that accounts for the interplay between advanced composite usage, legacy aluminum alloys, and high-performance titanium and nickel alloys.
By setting this strategic foundation, executives can better anticipate transformative shifts and craft resilience strategies. This section introduces the critical themes and lays the groundwork for a detailed exploration of tariff impacts, segmentation insights, regional dynamics, and actionable recommendations that will steer decision-makers toward informed investments and sustainable competitive advantage.
Navigating the New Frontiers of Aerostructure Manufacturing Fueled by Digital Integration Lightweight Composites and Sustainable Innovations
The aerostructure landscape is being reshaped by digital integration, lightweight composites, and sustainability mandates that collectively redefine manufacturing paradigms. Traditional metal processing techniques now coexist with automated fiber placement technologies, enabling the precise fabrication of complex composite components with reduced production times. Concurrently, predictive maintenance platforms powered by digital twins and IoT sensors are enhancing fleet reliability while lowering operational expenditures.
Amid these technological advances, manufacturers and tier suppliers are investing heavily in additive manufacturing to produce optimized components with minimal material waste. The shift toward carbon fiber–reinforced polymers and thermoplastic composites is driving a decline in overall aircraft weight, leading to improved fuel efficiency and lowered emissions. This transition is further bolstered by regulatory incentives aimed at reducing the carbon footprint of aviation, signaling a broader industry alignment with environmental stewardship goals.
Moreover, ecosystem stakeholders are fostering collaborative innovation through public–private partnerships and cross-industry alliances. By integrating digital thread strategies and embracing advanced analytics, companies can streamline design iterations, accelerate certification processes, and enhance quality control. These transformative shifts not only elevate manufacturing agility but also cultivate a culture of continuous improvement that underpins long-term competitiveness.
Unraveling the Effects of 2025 US Tariffs on Aerostructure Production Costs Supply Chain Dynamics and Import Dependency Realignment
In early 2025, the United States implemented a new tranche of tariffs targeting imported aerostructure assemblies and raw materials, compelling manufacturers to reassess procurement strategies. The levies have elevated costs for key inputs such as titanium forgings, composite prepregs, and specialized alloy skins, triggering a reassessment of global sourcing dependencies. As a consequence, some OEMs and tier suppliers have expedited the qualification of domestic suppliers to mitigate tariff-driven cost pressures.
These measures have also prompted shifts in regional supply chain configurations. Asian and European component producers, historically reliant on US-sourced subassemblies, are exploring localized manufacturing agreements and joint ventures to circumvent tariff barriers. This realignment is fostering nearshoring trends, particularly among midsize parts fabricators seeking greater control over logistics and lead times. In tandem, design engineers are evaluating modular assembly architectures that facilitate the substitution of tariff-impacted components without extensive requalification cycles.
Despite initial supply bottlenecks and cost pass-through challenges for end users, the tariff regime has stimulated innovation in material substitution and process optimization. Advanced materials labs are investigating alternative alloy systems and bio-based resins that offer comparable performance while remaining exempt from certain levies. In aggregate, these developments underscore the industry’s resilience, adaptability, and commitment to sustaining aerodynamic performance within an evolving trade policy landscape.
Decoding Multi-Dimensional Segmentation to Reveal Critical Product Aircraft Material End User Application and Distribution Channel Trends
A granular view of aerostructure equipment reveals diverse performance requirements across product categories, each demanding tailored materials and manufacturing processes. Control surfaces encompassing aileron, flap, and spoiler assemblies prioritize lightweight strength and responsive actuation systems, whereas empennage structures such as horizontal stabilizers and rudders balance stiffness with aerodynamic precision. Fuselage sections, including barrel, nose cone, and tail assemblies, necessitate airtight integrity and structural robustness to withstand pressurization cycles.
Aircraft type segmentation underscores unique procurement drivers. Business jets often leverage premium composite interiors combined with advanced alloys to maximize range and comfort. Commercial airliners focus on high-volume production efficiencies for wing skins, spars, and landing gear assemblies, while military platforms demand rigorous fatigue resilience and survivability characteristics. Helicopters and regional aircraft, with their distinct aerodynamic profiles, require flexible fuselage panels and dynamic support structures tuned for vertical lift and frequent short-haul cycles.
Material selection illuminates further differentiation, with aluminum alloys still prevalent for cost-sensitive components and composite materials gaining traction for weight-critical applications. Steel remains indispensable for high-load fittings, while titanium and nickel alloys are reserved for extreme-temperature sections. End user considerations bifurcate between OEMs, driving new build programs, and MRO service providers, focused on retrofit and overhaul operations that extend asset life. Lastly, distribution channels span direct sales for specialized assemblies and aftermarket platforms catering to unplanned maintenance workflows, ensuring component availability across the lifecycle.
This comprehensive research report categorizes the Aero Structure Equipments market into clearly defined segments, providing a detailed analysis of emerging trends and precise revenue forecasts to support strategic decision-making.
- Product Type
- Aircraft Type
- Material
- End User
- Application
- Distribution Channel
Comparative Regional Dynamics Highlighting Growth Drivers Supply Chain Nuances and Innovation Hotspots across the Americas EMEA and Asia-Pacific
Regionally, the Americas maintain a leadership position in aerostructure manufacturing, driven by robust OEM activity and extensive MRO networks. The presence of established hubs in the United States and Canada supports advanced composite facilities and titanium processing plants, catering to both domestic and export markets. Furthermore, collaboration between research institutions and industry players in North America accelerates the integration of digital manufacturing and lightweight materials.
In Europe, Middle East, and Africa, stringent environmental regulations and ambitious fleet expansion programs are catalyzing demand for next-generation aerostructures. European manufacturers are at the forefront of hybrid composite innovations and have established certification pathways for novel materials. Gulf nations are channeling investments into aerospace clusters that focus on integrated assembly lines and aftermarket services, while select African countries are exploring component fabrication for regional commuter platforms.
Asia-Pacific represents a rapidly emerging frontier, with China and India scaling up capabilities in fuselage and wing subassembly production. Incentivized by government subsidies and favorable trade agreements, local suppliers are enhancing precision tooling and surface treatment processes. Collaborative ventures with Western players facilitate technology transfer, enabling the maturation of domestically produced control surfaces, empennage sections, and landing gear components for burgeoning domestic carriers and export customers alike.
This comprehensive research report examines key regions that drive the evolution of the Aero Structure Equipments market, offering deep insights into regional trends, growth factors, and industry developments that are influencing market performance.
- Americas
- Europe, Middle East & Africa
- Asia-Pacific
Profiling Key Industry Players to Illuminate Competitive Strategies Collaborative Ventures and Technological Leadership in Aerostructures
Leading aerostructure suppliers are deploying differentiated strategies to secure market share and technological ascendancy. Major OEMs and tier-one manufacturers are forging strategic alliances that blend digital engineering prowess with scalable production networks. By integrating additive manufacturing pilots and automated assembly cells, these companies are reducing cycle times and enhancing quality control across complex part geometries.
Several suppliers have embarked on facility expansions in regions offering tariff advantages or proximity to key OEM programs. Such moves not only hedge against trade volatility but also deepen customer engagement through co-located engineering support. Concurrently, partnerships with material innovators are facilitating the accelerated adoption of high-strength aluminum alloys, advanced carbon composites, and corrosion-resistant titanium treatments.
Intellectual property differentiation remains central to competitive positioning. Firms that have recently secured patents in hybrid composite formulations and real-time structural health monitoring systems are gaining traction among forward-looking OEMs. Moreover, joint development agreements with defense contractors and major airlines are broadening the application scope of novel aerostructure technologies, thereby reinforcing supplier relevance in both commercial and military domains.
This comprehensive research report delivers an in-depth overview of the principal market players in the Aero Structure Equipments market, evaluating their market share, strategic initiatives, and competitive positioning to illuminate the factors shaping the competitive landscape.
- Spirit AeroSystems, Inc.
- GKN Aerospace Services Limited
- Collins Aerospace, Inc.
- Triumph Group, Inc.
- Leonardo S.p.A.
- Kawasaki Heavy Industries, Ltd.
- Latecoere S.A.
- FACC Aktiengesellschaft
- Senior plc
- Safran S.A.
Strategic Imperatives for Aerostructure Leaders to Harness Advanced Technologies Diversify Supply Chains and Drive Sustainable Growth
Industry leaders must prioritize investments in digital twins and predictive analytics to achieve predictive maintenance capabilities and accelerate certification cycles. By embedding sensor networks and leveraging cloud-based simulation platforms, manufacturers can preempt structural failures and optimize production workflows. In parallel, diversifying the supplier base to include dual-source arrangements for critical alloys and composite prepregs will fortify operations against future tariff shifts and geopolitical disruptions.
Embracing a modular architecture philosophy will enable rapid configuration changes and facilitate aftermarket upgrades without extensive requalification efforts. This approach, coupled with standardized interface protocols, will not only reduce inventory burden but also enhance service responsiveness for both new build programs and retrofit initiatives. Furthermore, cultivating collaborative innovation ecosystems with material scientists and software developers will unlock breakthroughs in bio-based resins and digital certification tools.
Finally, embedding sustainability at the core of design and procurement decisions will appeal to environmentally conscious stakeholders and align with emerging carbon offset regulations. Initiatives such as lifecycle assessments, end-of-life recyclability planning, and renewable energy integration in manufacturing processes will strengthen brand equity and ensure compliance with tightening environmental mandates.
Integrating Robust Primary and Secondary Research Techniques to Ensure Data Accuracy Stakeholder Insights and Comprehensive Market Analysis
This study synthesizes insights from both primary and secondary research methods to ensure a comprehensive and balanced analysis. Primary research included in-depth interviews with senior executives at OEMs, tier-one suppliers, and MRO service providers, capturing firsthand perspectives on technological adoption, tariff impacts, and regional growth drivers. Concurrently, over fifty technical whitepapers and academic publications were reviewed to validate emerging material trends and manufacturing innovations.
Secondary research involved rigorous scrutiny of trade association reports, government trade bulletins, and regulatory filings to map the 2025 tariff landscape and its implications for import-dependent components. Specialized databases were leveraged to track patent filings, merger and acquisition activity, and joint development agreements, providing insight into competitive positioning and intellectual property developments. This multi-source triangulation ensures that conclusions are robust and reflective of market realities.
Data integrity was upheld through cross-validation, wherein insights from interviews were contrasted against secondary data points to identify any discrepancies or biases. A structured validation framework was applied to confirm the consistency of emerging trends across regions and product segments. Ultimately, this methodological rigor underpins the credibility of the strategic recommendations and regional analyses presented in this report.
Explore AI-driven insights for the Aero Structure Equipments market with ResearchAI on our online platform, providing deeper, data-backed market analysis.
Ask ResearchAI anything
World's First Innovative Al for Market Research
Consolidating Strategic Takeaways to Steer Aerostructure Market Participants Toward Resilient Innovative and Sustainable Operational Pathways
The aerostructure equipment sector is poised for ongoing transformation driven by digital manufacturing, advanced composites, and shifting trade policies. Despite the complexities introduced by the 2025 tariff regime, the industry’s adaptability has been evident through supplier diversification and material innovation. As companies navigate these headwinds, the strategic emphasis on modular design, predictive maintenance, and sustainability will determine long-term resilience.
Segmentation and regional analyses reveal that while mature markets in the Americas and EMEA maintain leadership in R&D and certification, Asia-Pacific is rapidly augmenting its production capabilities through strategic investments and partnerships. Suppliers that effectively integrate digital twins and additive manufacturing into their core operations will command significant competitive advantages. Furthermore, embedding environmental considerations within procurement and design processes will not only mitigate regulatory risk but also align with global decarbonization efforts.
Together, these insights equip decision-makers with a nuanced understanding of market dynamics and actionable strategies to optimize operations. By synthesizing the interplay between tariffs, technology adoption, regional developments, and competitive actions, this report offers a holistic roadmap for achieving growth, innovation, and sustainability in the dynamic aerostructure landscape.
This section provides a structured overview of the report, outlining key chapters and topics covered for easy reference in our Aero Structure Equipments market comprehensive research report.
- Preface
- Research Methodology
- Executive Summary
- Market Overview
- Market Dynamics
- Market Insights
- Cumulative Impact of United States Tariffs 2025
- Aero Structure Equipments Market, by Product Type
- Aero Structure Equipments Market, by Aircraft Type
- Aero Structure Equipments Market, by Material
- Aero Structure Equipments Market, by End User
- Aero Structure Equipments Market, by Application
- Aero Structure Equipments Market, by Distribution Channel
- Americas Aero Structure Equipments Market
- Europe, Middle East & Africa Aero Structure Equipments Market
- Asia-Pacific Aero Structure Equipments Market
- Competitive Landscape
- ResearchAI
- ResearchStatistics
- ResearchContacts
- ResearchArticles
- Appendix
- List of Figures [Total: 30]
- List of Tables [Total: 1196 ]
Take Action Today: Partner with Ketan Rohom to Unlock In-Depth Aerostructure Market Intelligence and Propel Your Strategic Decision-Making
Embark on a transformative journey toward unparalleled market intelligence by reaching out to Ketan Rohom, Associate Director of Sales & Marketing. His expertise in aerostructure dynamics will equip you with the nuanced analysis, strategic frameworks, and actionable insights required to navigate complex tariffs, technological advancements, and supply chain disruptions. Whether you seek to optimize procurement strategies, accelerate product innovation, or fortify your competitive stance, Ketan’s guidance will ensure you extract maximum value from this comprehensive report. Contact him today to secure your access to the most authoritative and up-to-date aerostructure market research available.
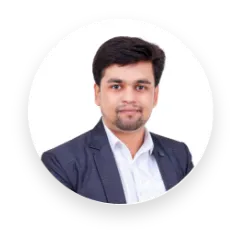
- How big is the Aero Structure Equipments Market?
- What is the Aero Structure Equipments Market growth?
- When do I get the report?
- In what format does this report get delivered to me?
- How long has 360iResearch been around?
- What if I have a question about your reports?
- Can I share this report with my team?
- Can I use your research in my presentation?