The Aerospace 3D Printing Market size was estimated at USD 4.10 billion in 2024 and expected to reach USD 4.79 billion in 2025, at a CAGR 16.58% to reach USD 10.31 billion by 2030.

Pioneering the Future of Aerospace with 3D Printing
Additive manufacturing has evolved from a prototyping novelty to a mission-critical production technology for aerospace. The introduction of layer-by-layer fabrication has unlocked complex geometries, reduced material waste, and accelerated time-to-market. Aerospace manufacturers are harnessing 3D printing to produce engine components, lightweight interior structures, and structural brackets that defy traditional constraints. Early adoption centered on polymers and rapid prototyping, but now the spectrum spans ceramics, composites, metals, and high-performance thermoplastics certified for flight. This technological leap has been underpinned by advances in powder bed fusion, directed energy deposition, and vat photopolymerization that provide precision and repeatability at scale.
Collaborative innovation between original equipment manufacturers, tier one suppliers, and technology vendors has driven qualification standards and supply chain integration. As regulatory bodies establish guidelines for additive manufacturing in aviation and space, quality assurance processes have matured, ensuring that printed parts meet stringent safety and performance benchmarks. Consequently, aerospace engineers are rethinking design paradigms, focusing on topology optimization, lattice architectures, and multi-material assemblies. The convergence of digital simulation, real-time monitoring, and post-processing automation has transformed additive manufacturing from a workshop curiosity into a strategic enabler of competitive differentiation.
As global supply chains adapt and regulatory frameworks mature, additive manufacturing is poised to redefine value chains. The following sections explore the transformative shifts, tariff headwinds, segmentation nuances, and regional drivers shaping the aerospace 3D printing frontier
The New Dynamics Reshaping Aerospace Manufacturing
Additive manufacturing in aerospace is propelling a paradigm shift that extends beyond component production into value chain orchestration. Manufacturers are integrating digital design files with on-demand printing capabilities to minimize inventory and accelerate delivery. Consequently, the traditional cadence of machining and casting gives way to just-in-time fabrication, where digital warehousing and remote printing centers ensure uninterrupted supply. Simultaneously, design freedom has fostered the emergence of parts consolidation, replacing assemblies of dozens of pieces with single, topology-optimized structures that reduce weight and simplify certification.
Moreover, hybrid manufacturing strategies are blending additive processes with conventional machining to optimize surface finishes and dimensional accuracy. Collaborative robots and automated post-processing cells enable consistent throughput, while digital twins of machines and parts facilitate predictive maintenance. These advancements not only enhance productivity but also help maintain traceability and compliance under rigorous aerospace standards.
Finally, the shift toward service-oriented business models is redefining manufacturer relationships with end-users. Service bureaus equipped with advanced additive fleets are offering turnkey solutions, while original equipment manufacturers expand offerings to include digital inventory management and lifecycle support. Together, these transformative shifts are establishing additive manufacturing as the backbone of a more agile, sustainable, and resilient aerospace industry
Tariff Pressures Redefining Supply Chains and Costs
The introduction of new tariff measures in 2025 has imposed additional duties on imported metal powders, polymer feedstocks, and specialized equipment critical to additive manufacturing. As a result, aerospace firms are navigating elevated input costs that affect both prototyping and production phases. In response, many have accelerated domestic sourcing initiatives and partnered with local material producers to secure qualification processes that align with aerospace certification requirements. Consequently, supply chains are being restructured to favor suppliers capable of delivering flight-grade alloys and thermoplastics within the domestic tariff framework.
Tariff pressures have also prompted manufacturers to revisit inventory strategies, balancing the cost of carrying excess feedstock against the risk of production delays. Some organizations are investing in onshore blending capabilities for metal and composite powders, while others leverage multi-supplier networks to maintain competitive pricing and mitigate single-source dependencies. These adjustments not only safeguard production schedules but also reinforce compliance with evolving trade policies and regulatory checks at customs.
Looking ahead, the cumulative impact of these duties extends beyond cost considerations, influencing decisions around facility location, capital investment in additive printing assets, and collaboration models with technology partners. Companies that proactively adapt sourcing and operational strategies will be better positioned to absorb tariff fluctuations and sustain momentum in aerospace additive manufacturing
Unearthing Value Across Material Technology and Application Dimensions
A nuanced understanding of market segments reveals distinct opportunities across material classes, printing technologies, applications, end-use industries, and printer types. Material segmentation highlights that ceramics, including oxide and non-oxide variants, address high-temperature and wear-resistant component needs. Composite offerings span carbon fiber reinforced and glass fiber reinforced formulations, delivering strength-to-weight advantages for structural and interior parts. Metal powders, such as aluminum alloys, nickel alloys, and titanium alloys, are critical for engine components and airframe structures, while polymers, comprising photopolymers and thermoplastics, serve prototyping and tooling applications.
Technology segmentation underscores the diversity of additive processes. Binder jetting offers high throughput and minimal thermal stress, whereas directed energy deposition-through laser-based and wire-arc approaches-enables repair and near-net-shape fabrication of large structures. Material extrusion delivers cost-effective polymer and composite parts, powder bed fusion powered by electron beam or laser beam ensures fine resolution and metallurgical integrity, and vat photopolymerization produces detailed plastic and ceramic prototypes.
Application segmentation differentiates end-use parts, prototyping, and tooling. End-use parts, including engine components, interiors, and structural assemblies, demand rigorous qualification and traceability. Prototyping accelerates design validation cycles, and tooling applications reduce lead times for jigs, fixtures, and molds. End-use industries such as commercial aviation, defense, and space exploration each impose unique performance and certification requirements. Finally, printer type segmentation distinguishes between desktop printers suited for small-batch production and industrial printers built for high-volume aerospace manufacturing, enabling stakeholders to align technology investments with operational objectives
This comprehensive research report categorizes the Aerospace 3D Printing market into clearly defined segments, providing a detailed analysis of emerging trends and precise revenue forecasts to support strategic decision-making.
- Material
- Technology
- Application
- End-Use Industry
- Printer Type
Regional Forces Driving Aerospace 3D Printing Growth
Regional dynamics exert a powerful influence on the adoption and evolution of aerospace additive manufacturing capabilities. In the Americas, established aviation clusters and robust R&D ecosystems drive early adoption of advanced materials and printing technologies. Leading aerospace hubs in the United States and Canada benefit from strong government support for aerospace initiatives, fueling investments in high-precision powder bed fusion and directed energy deposition systems.
Across Europe, the Middle East, and Africa, collaborative consortia between OEMs, research institutions, and regional suppliers are advancing standardization efforts and certification pathways. European aerospace programs are particularly focused on sustainable materials, recycling of metal powders, and digital thread integration. Investments in defense applications and space exploration initiatives in the Middle East are also bolstering local additive capabilities.
In Asia-Pacific, rapidly growing commercial aviation markets and supportive industrial policies are accelerating the deployment of industrial printers for both structural components and aftermarket parts. Countries such as China, Japan, and Australia are cultivating additive manufacturing clusters that integrate local feedstock production, specialized service bureaus, and training centers. These regional forces together shape a multifaceted global landscape where innovation ecosystems and regulatory environments dictate the pace and scale of aerospace 3D printing adoption
This comprehensive research report examines key regions that drive the evolution of the Aerospace 3D Printing market, offering deep insights into regional trends, growth factors, and industry developments that are influencing market performance.
- Americas
- Europe, Middle East & Africa
- Asia-Pacific
Competitive Strategies of Leading Additive Manufacturing Innovators
Leading players in aerospace additive manufacturing are adopting differentiated strategies to capture market share and foster innovation. Established equipment manufacturers are expanding their portfolios through strategic acquisitions of software providers and material specialists, creating end-to-end solutions that streamline design-to-print workflows. They are also investing in certified service centers to offer turnkey solutions encompassing design optimization, material testing, and post-processing.
Material producers are forming joint ventures with technology vendors to co-develop alloys and composite formulations tailored for aerospace requirements. These collaborations accelerate the qualification of new feedstocks, reduce development cycles, and ensure consistent quality control. Meanwhile, digital workflow providers are enhancing interoperability between design software, printer hardware, and data management platforms to facilitate traceability and compliance.
Service bureaus and contract manufacturers are cultivating specialized capabilities in large-format printing and multi-material builds. By securing long-term agreements with major OEMs and defense primes, they ensure capacity utilization and access to flight-critical production projects. Across the ecosystem, companies are prioritizing sustainability initiatives-such as powder recycling and energy-efficient equipment design-to align with corporate responsibility commitments and evolving regulatory standards
This comprehensive research report delivers an in-depth overview of the principal market players in the Aerospace 3D Printing market, evaluating their market share, strategic initiatives, and competitive positioning to illuminate the factors shaping the competitive landscape.
- GE Additive, Inc.
- EOS GmbH Electro Optical Systems
- 3D Systems Corporation
- Stratasys Ltd.
- SLM Solutions Group AG
- Renishaw plc
- HP Inc.
- Desktop Metal, Inc.
- Materialise NV
- Markforged, Inc.
Strategic Pathways for Industry Leadership in Additive Aerospace
Industry leaders should pursue a multifaceted strategy to capitalize on aerospace additive manufacturing’s potential. First, integrating digital design, simulation, and quality assurance tools into a unified platform will streamline certification processes and reduce time-to-market. Embracing hybrid manufacturing systems that combine additive printing with subtractive finishing will enable production of parts that meet demanding aerospace tolerances.
Second, organizations should forge strategic alliances with material suppliers and service bureaus to secure qualified feedstocks and scale capacity flexibly. Collaborative development of new alloy and composite formulations will accelerate the introduction of high-performance materials certified for flight. Third, investing in workforce development programs that build expertise in additive design, machine operation, and inspection techniques will ensure talent pipelines align with growth trajectories.
Finally, monitoring geopolitical shifts and tariff developments will inform supply chain resilience planning. Diversifying sourcing strategies, nearshoring critical material production, and maintaining digital inventories of certified print files can mitigate disruptions. By aligning investments with these strategic pathways, industry leaders will strengthen their competitive position and drive the next wave of innovation in aerospace additive manufacturing
Rigorous Approach to Comprehensive Market Analysis
The research methodology underpinning this market analysis combines primary and secondary approaches to ensure rigor and relevance. Primary research included in-depth interviews with aerospace engineers, additive manufacturing specialists, and procurement leaders across original equipment manufacturers, tier one suppliers, and service bureaus. These discussions provided qualitative insights into technology adoption drivers, certification challenges, and future investment priorities.
Secondary research involved comprehensive review of technical papers, regulatory guidelines, industry roadmaps, and trade publications. Data from patent filings and conference proceedings were analyzed to identify innovation hotspots and emerging applications. Product catalogs and financial reports from key equipment and material suppliers were examined to map competitive landscapes and strategic collaborations.
Market segmentation was defined across material classes, printing technologies, applications, end-use industries, and printer types, with each segment validated through cross-referencing of primary feedback and published data. Regional analysis incorporated macroeconomic indicators, aerospace production volumes, and government funding initiatives. Finally, all findings underwent internal quality assurance checks, ensuring consistency, accuracy, and adherence to industry best practices
Explore AI-driven insights for the Aerospace 3D Printing market with ResearchAI on our online platform, providing deeper, data-backed market analysis.
Ask ResearchAI anything
World's First Innovative Al for Market Research
Converging Trends Steering the Trajectory of Aerospace Additive Manufacturing
Additive manufacturing is reshaping aerospace production through a convergence of advanced materials, innovative processes, and evolving business models. The integration of topology-optimized designs, multi-material assemblies, and digital workflow solutions has transformed 3D printing from a niche prototyping tool into a strategic enabler of competitive advantage. Simultaneously, evolving regulatory frameworks and tariff landscapes are driving supply chain adaptations and domestic sourcing initiatives.
Segmentation insights highlight distinct value pools across ceramics, composites, metals, and polymers, as well as between binder jetting, directed energy deposition, powder bed fusion, and other processes. Regional dynamics further underscore how established clusters in the Americas, standardization efforts across Europe, the Middle East, and Africa, and rapid market expansion in Asia-Pacific are collectively shaping the global ecosystem.
As leading companies refine their strategies-integrating digital platforms, pursuing material partnerships, and optimizing hybrid manufacturing workflows-the industry stands at the cusp of a new era. Organizations that embrace these converging trends, invest in workforce capabilities, and proactively manage geopolitical and regulatory shifts will be best positioned to lead aerospace additive manufacturing into its next chapter
This section provides a structured overview of the report, outlining key chapters and topics covered for easy reference in our Aerospace 3D Printing market comprehensive research report.
- Preface
- Research Methodology
- Executive Summary
- Market Overview
- Market Dynamics
- Market Insights
- Cumulative Impact of United States Tariffs 2025
- Aerospace 3D Printing Market, by Material
- Aerospace 3D Printing Market, by Technology
- Aerospace 3D Printing Market, by Application
- Aerospace 3D Printing Market, by End-Use Industry
- Aerospace 3D Printing Market, by Printer Type
- Americas Aerospace 3D Printing Market
- Europe, Middle East & Africa Aerospace 3D Printing Market
- Asia-Pacific Aerospace 3D Printing Market
- Competitive Landscape
- ResearchAI
- ResearchStatistics
- ResearchContacts
- ResearchArticles
- Appendix
- List of Figures [Total: 26]
- List of Tables [Total: 548 ]
Partner with Ketan Rohom to Access In-Depth Market Intelligence
Unlock unparalleled market insights with Ketan Rohom, Associate Director, Sales & Marketing. Engage directly to explore tailored analysis, detailed segmentation, and strategic guidance that align with your organization’s objectives. Whether you seek clarity on tariff impacts, regional dynamics, or advanced material adoption, Ketan will guide you through the findings and recommendations that matter most. Elevate decision-making, mitigate risks, and accelerate your roadmap by securing the full aerospace 3D printing research report today
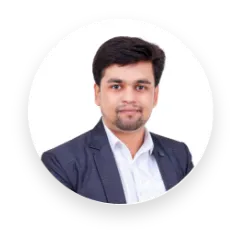
- How big is the Aerospace 3D Printing Market?
- What is the Aerospace 3D Printing Market growth?
- When do I get the report?
- In what format does this report get delivered to me?
- How long has 360iResearch been around?
- What if I have a question about your reports?
- Can I share this report with my team?
- Can I use your research in my presentation?