The Aerospace Coatings Market size was estimated at USD 2.97 billion in 2024 and expected to reach USD 3.21 billion in 2025, at a CAGR 7.65% to reach USD 4.63 billion by 2030.

Setting the Stage for Aerospace Coatings Innovation
The aerospace coatings sector sits at a crossroads of technological innovation, regulatory change, and evolving customer demands. As airlines and defense contractors seek lighter, more durable, and environmentally friendly surface treatments, coatings manufacturers must adapt at pace to protect aircraft structures and systems under increasingly stringent operational conditions. This executive summary opens with a high-level overview, framing the core trends that are reshaping the landscape from raw material selection to end‐use deployment.
As the industry grapples with heightened sustainability targets and supply chain volatility, stakeholders are demanding greater visibility into every stage of the value chain. Coatings performance now extends beyond corrosion protection to include multifunctional properties such as thermal shielding, anti‐icing, and conductive capabilities. Coupled with shifting trade policies and regional investment patterns, these forces are converging to create both challenges and opportunities. The following sections dive deep into the most significant shifts, tariff impacts, segmentation nuances, and strategic imperatives that will define market winners and laggards moving forward.
Disruptive Forces Redefining Coating Technologies
Over the past five years, breakthroughs in resin chemistry and application technologies have accelerated product differentiation. The transition from solvent‐borne systems to UV‐curable and waterborne formulations reflects an industry‐wide commitment to lower volatile organic compound levels without sacrificing performance. At the same time, powder coatings have gained traction for their durability and minimal waste, while advanced intumescent and ceramic‐based thermal barrier solutions deliver unprecedented heat resistance.
Simultaneously, digitalization is entering production floors through smart application equipment that monitors film thickness and cure states in real time. Sustainability initiatives are driving manufacturers toward life‐cycle analyses that quantify environmental benefits and total cost of ownership. And cross‐industry collaboration with automotive and marine coatings suppliers is fostering technology transfer, catalyzing innovation in abrasion resistance, anti‐icing functionality, and conductive formulations. Taken together, these disruptive forces are propelling a new era of high‐performance, eco‐efficient aerospace coatings.
Navigating New Tariff Realities in 2025
The implementation of U.S. tariffs in early 2025 has introduced a new layer of complexity for both domestic and international suppliers. Import duties on key raw materials, including specialty resins and performance pigments, have heightened the cost base and pressured margin structures. In response, some manufacturers have re-evaluated their reliance on imported feedstocks, forging new alliances with local resin producers and reevaluating their logistics networks to mitigate exposure to further tariff escalations.
Moreover, second‐ and third‐tier suppliers are reassessing their supplier qualification processes and qualification cycles to reduce lead times and secure alternate sources. For end‐users, the elevated cost of premium coatings has prompted a renewed focus on coating life extension and maintenance optimization, with maintenance, repair, and overhaul (MRO) providers advancing novel repair primers and touch-up materials. Although the immediate fallout has triggered short-term price adjustments, the wave of restructured sourcing strategies promises enhanced resilience against future trade policy shifts.
Unpacking Critical Segmentation Dynamics
A deeper understanding of the market’s segmentation reveals discrete areas primed for growth and innovation. Across resin type, acrylic formulations lead in color retention and weatherability while epoxy variants deliver exceptional adhesion and chemical resistance; polyurethane polymers strike a balance of flexibility and durability and waterborne resins are increasingly adopted to meet stringent environmental standards.
Application segments further refine the landscape, with anti-corrosion coatings remaining foundational for airframe protection, decorative finishes evolving in both aesthetics and scratch resistance, and fire-resistant systems differentiated between fireproof coatings designed for structural integrity and intumescent solutions that expand under heat. Functional coatings are partitioned into abrasion-resistant options for surface reinforcement, anti-icing treatments to mitigate in-flight hazards, and conductive layers that support de-icing and electromagnetic shielding. Thermal barrier coatings split into ceramic coatings for extreme heat environments and thermal shield technologies that protect critical components.
End-use segmentation distinguishes MRO activities-encompassing base maintenance and line maintenance workflows-from OEM applications across airframe structures and engine assemblies, each with unique certification demands and performance metrics. Technology choices drive further specialization: powder coatings offer minimal overspray and robust finish properties, solvent-borne systems provide proven reliability, UV-curable formulations deliver rapid cure cycles, and water-borne technologies reduce environmental impact.
Aircraft platform segmentation differentiates commercial fleets from general aviation categories such as business jets, piston engine aircraft, and turboprops, while military and unmanned aerial vehicle sectors demand tailored stealth or sensor-compatible coatings. Finally, product form considerations-in aerosol, liquid, and powder formats-shape distribution models, application equipment requirements, and maintenance protocols. Together, these layered segmentation dynamics present a roadmap for targeted innovation and strategic investment.
This comprehensive research report categorizes the Aerospace Coatings market into clearly defined segments, providing a detailed analysis of emerging trends and precise revenue forecasts to support strategic decision-making.
- Resin Type
- Application
- End Use
- Technology
- Aircraft Platform
- Product Form
Regional Drivers Shaping Coating Demand
Market dynamics vary markedly across regions, with the Americas driven by fleet modernization programs and robust MRO infrastructure that amplify demand for high-performance anti-corrosion and functional coatings. In Europe, Middle East & Africa, stringent environmental regulations and expanding defense budgets stimulate adoption of waterborne and UV-curable systems, alongside a growing emphasis on thermal barrier solutions to support advanced engine designs.
Meanwhile, Asia-Pacific exhibits the fastest pace of capacity expansion, underpinned by rising commercial aircraft orders, burgeoning regional low-cost carriers, and government-sponsored aerospace clusters. Sustainability imperatives in key markets are accelerating uptake of eco-friendly formulations, while local producers invest in state-of-the-art application and curing technologies. Supply chain resilience remains a priority, driving strategic onshore alliances and localized production footprints.
This comprehensive research report examines key regions that drive the evolution of the Aerospace Coatings market, offering deep insights into regional trends, growth factors, and industry developments that are influencing market performance.
- Americas
- Europe, Middle East & Africa
- Asia-Pacific
Strategic Moves by Leading Coating Providers
Leading players have sharpened their competitive positioning through a combination of technological leadership, strategic partnerships, and targeted acquisitions. Global coating manufacturers are elevating R&D investments in multifunctional platforms that merge corrosion protection with thermal or anti-icing functionality. Strategic alliances with chemical innovators enable joint development of next-generation resins and proprietary pigments that deliver weight savings and extended service life.
Concurrently, forward-integrated suppliers are extending into MRO services, leveraging diagnostic tools and digital inspection systems to bundle coating application with maintenance contracts. Select firms have strengthened their footprint in emerging markets through joint ventures with regional coatings producers, thereby achieving faster market entry and localized customization. In response to tariff pressures, some companies have diversified sourcing channels and reshaped their global tariff mitigation strategies to safeguard margins and maintain service levels.
This comprehensive research report delivers an in-depth overview of the principal market players in the Aerospace Coatings market, evaluating their market share, strategic initiatives, and competitive positioning to illuminate the factors shaping the competitive landscape.
- PPG Industries, Inc.
- Akzo Nobel N.V.
- Axalta Coating Systems Ltd.
- The Sherwin-Williams Company
- Hempel A/S
- Mankiewicz Gebr. & Co. GmbH & Co. KG
- Jotun A/S
- Kansai Paint Co., Ltd.
- RPM International Inc.
- Nippon Paint Holdings Co., Ltd.
Blueprint for Leadership in a Shifting Market
To maintain competitive advantage, industry leaders should prioritize broadening product portfolios toward multifunctional coatings that reduce total system weight and lifecycle cost. Investing in modular application technologies that support both high-volume OEM lines and agile MRO environments will maximize asset utilization. Establishing collaborative research agreements with resin suppliers and academic institutions can accelerate innovation in low-VOC, high-temperature, and conductive formulations.
Additionally, forging regional supply alliances and exploring capacity builds in tariff-free jurisdictions will enhance supply chain resilience. Executives must also integrate advanced data analytics across production and maintenance operations to predict coating degradation and optimize refurbishment cycles. Finally, embedding sustainability criteria into product roadmaps and client proposals will differentiate offerings and align with the expanding regulatory landscape.
Rigorous Approach to Market Intelligence
This analysis blends primary interviews with senior executives and technical experts across OEMs, MRO operators, raw material suppliers, and coating formulators. Secondary research encompassed industry reports, patent filings, regulatory publications, and trade association data. Information was triangulated through cross-referencing shipment statistics, regional aircraft order books, and environmental standards to ensure accuracy and relevance.
A structured framework guided segmentation mapping and competitive profiling, while thematic workshops validated emerging trends and innovation trajectories. Quality control procedures included peer reviews by subject matter experts, consistency checks against historic industry benchmarks, and ongoing updates to reflect regulatory amendments. This robust methodology underpins the insights presented herein, offering decision-makers a reliable foundation for strategic planning.
Explore AI-driven insights for the Aerospace Coatings market with ResearchAI on our online platform, providing deeper, data-backed market analysis.
Ask ResearchAI anything
World's First Innovative Al for Market Research
Synthesizing Insights for Future Growth
As the aerospace coatings market navigates transformative technological shifts and regulatory headwinds, stakeholders that adopt a segmented, data-driven approach will unlock sustainable growth. Innovation in resin chemistry and application systems promises to redefine performance benchmarks, while regional dynamics and tariff considerations will continue to shape strategic investment decisions.
By focusing on multifunctional solutions, supply chain resilience, and digital integration, industry participants can transform challenges into competitive differentiators. The evolving landscape rewards agility, collaboration, and foresight, and those who align their portfolios with emerging demands are best positioned to lead this dynamic sector into its next chapter.
This section provides a structured overview of the report, outlining key chapters and topics covered for easy reference in our Aerospace Coatings market comprehensive research report.
- Preface
- Research Methodology
- Executive Summary
- Market Overview
- Market Dynamics
- Market Insights
- Cumulative Impact of United States Tariffs 2025
- Aerospace Coatings Market, by Resin Type
- Aerospace Coatings Market, by Application
- Aerospace Coatings Market, by End Use
- Aerospace Coatings Market, by Technology
- Aerospace Coatings Market, by Aircraft Platform
- Aerospace Coatings Market, by Product Form
- Americas Aerospace Coatings Market
- Europe, Middle East & Africa Aerospace Coatings Market
- Asia-Pacific Aerospace Coatings Market
- Competitive Landscape
- ResearchAI
- ResearchStatistics
- ResearchContacts
- ResearchArticles
- Appendix
- List of Figures [Total: 28]
- List of Tables [Total: 551 ]
Partner with Ketan Rohom to Access In-Depth Analysis
To secure a comprehensive view of the aerospace coatings market and its strategic imperatives, contact Ketan Rohom, Associate Director of Sales & Marketing. His expertise will guide you through detailed competitive analyses, advanced segmentation breakdowns, and regional outlooks tailored to your business needs. Reach out to schedule a consultation and unlock the full report’s insights, equipping your organization with the intelligence required to outpace competitors and capitalize on emerging opportunities.
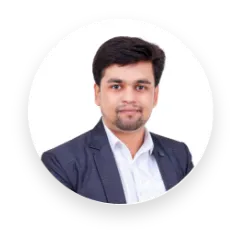
- How big is the Aerospace Coatings Market?
- What is the Aerospace Coatings Market growth?
- When do I get the report?
- In what format does this report get delivered to me?
- How long has 360iResearch been around?
- What if I have a question about your reports?
- Can I share this report with my team?
- Can I use your research in my presentation?