Introduction to the Strategic Significance of Aerospace MIM Parts
The aerospace industry has witnessed a significant shift toward precision manufacturing techniques, placing metal injection molding (MIM) parts at the forefront of design innovation and cost efficiency. Engine components, avionics housings, and intricate structural brackets now demand materials and geometries that only advanced MIM processes can deliver at scale. As manufacturers balance stringent weight limitations, high-temperature performance requirements, and exacting tolerance standards, MIM emerges as a compelling solution that bridges the gap between traditional powder metallurgy and additive manufacturing.
In this context, key stakeholders-from original equipment manufacturers to tier 1 suppliers-are exploring how MIM can reduce material waste, compress lead times, and enable complex micro-assemblies that were once impossible or prohibitively expensive. With regulatory bodies emphasizing sustainability and life-cycle accountability, the allure of producing near-net-shape components with minimal post-processing has intensified. Consequently, the evolution of machine capabilities, binder chemistries, and sintering technologies has consistently aligned with the aerospace sector’s demand for durability under extreme conditions. Transitioning from pilot runs to mass production, industry decision-makers now seek a holistic understanding of how MIM can optimize supply chains, mitigate risk, and maintain competitiveness in an era defined by rapid technological transformation.
Transformative Shifts Redefining Aerospace MIM Production
Emerging digitalization trends and additive manufacturing breakthroughs are revolutionizing how aerospace components are designed and manufactured. Whereas conventional forging and casting once dominated production, hybrid approaches that integrate metal powder injection, laser-based sintering, and robotics are streamlining workflows and elevating precision. Additionally, the rise of composite-reinforced MIM alloys, combined with advanced superalloys and titanium-based formulations, underpins a new wave of structural innovation, allowing engineers to integrate cooling channels and lattice architectures directly into high-temperature engine components.
Supply chain resilience has also become paramount. In response, major suppliers are forging cross-industry alliances with research institutes and tier 1 manufacturers, accelerating the development of hybrid manufacturing methods and proprietary binder systems. Moreover, a growing focus on emerging propulsion technologies has led to experimentation with micro- and nano-complex parts for electric and hybrid-electric powertrains. As materials science converges with digital twins and predictive maintenance platforms, aerospace stakeholders are setting new benchmarks for part traceability, functional performance, and energy efficiency. Consequently, this transformative landscape demands agile strategies that harness the full potential of metal injection molding while anticipating regulatory and sustainability imperatives.
Cumulative Impact of United States Tariffs Through 2025
The imposition of new tariffs on select metallic imports has exerted measurable pressure on raw material costs and downstream manufacturing economics. With heightened duties applied to aluminum, superalloys, and specialty stainless steels, aerospace MIM part producers have experienced an uptick in procurement expenses that ripples through supply chains. Rather than relying on a single geographic source for feedstock powders, manufacturers are diversifying their supplier base to manage volatility and secure preferential pricing terms.
Furthermore, the cost impact has spurred regional consolidation of sintering and debinding operations to exploit economies of scale, while certain tier 1 players are renegotiating long-term contracts to pass savings to OEMs. Performance-driven partnerships between end users and material technicians are also becoming more common, aimed at engineering binder systems that reduce processing temperatures and energy consumption. Although short-term margins may compress due to tariff-driven overheads, the industry’s proactive adoption of localized powder production, coupled with lean inventory management, is mitigating broader financial repercussions. Ultimately, these measures position aerospace MIM supply chains to remain responsive and cost-conscious through 2025 and beyond.
Comprehensive Segmentation Insights Across Key Market Dimensions
In dissecting the aerospace MIM landscape, segmentation by material type reveals that traditional aluminum alloys maintain a strong market presence, even as emerging composite materials and high-performance titanium formulations gain traction for weight-sensitive airframe applications. Stainless steel and super alloys continue to dominate engine components, while forward-looking enterprises invest in composite-metal hybrids to improve fatigue resistance. When evaluating application-specific needs, airframe parts and landing gear components still represent significant volume, whereas avionics housings and emerging propulsion technologies drive demand for micro-precision MIM items.
Assessing manufacturing processes underscores the persistence of forging and casting for bulkier parts, but metal additive manufacturing and powder metallurgy increasingly intersect with MIM to support complex geometries. Component complexity itself ranges from simple brackets to highly complex parts with integrated channels, and the proliferation of micro-complex parts is opening new opportunities in thermal management. End users span business jets, commercial airlines, military aviation platforms, and the nascent space exploration sector, all of which require bespoke designs for medium, large, small, and even miniature components. Throughout the product life cycle-from prototype and development through mass production, maintenance and repair, and end-of-life disposition-functionality requirements such as structural integrity, corrosion resistance, and non-structural load bearing influence material and process selection. Finally, strategic partnerships with OEMs, research institutes, and cross-industry alliances have become critical to advancing next-generation MIM solutions.
This comprehensive research report categorizes the Aerospace MIM Parts market into clearly defined segments, providing a detailed analysis of emerging trends and precise revenue forecasts to support strategic decision-making.
- Material Type
- Application
- Manufacturing Process
- Part Complexity
- End User
- Component Size
- Product Life Cycle Phase
- Functionality
- Industry Collaboration & Partnerships
Key Regional Dynamics Driving Aerospace MIM Development
Regional dynamics reflect distinct drivers and opportunities for aerospace MIM adoption. In the Americas, a concentration of major OEMs and tier 1 integrators fuels investment in localized powder manufacturing and sintering facilities, enabling rapid prototyping and scale-up for business jet and military aviation programs. Meanwhile, Europe, Middle East & Africa benefit from strong aerospace clusters in Western Europe, where stringent environmental regulations and advanced R&D funding accelerate innovation in composite-reinforced MIM alloys and micro-precision applications.
In Asia-Pacific, expanding commercial aviation fleets and government-backed space exploration initiatives have catalyzed investments in mass production infrastructure, particularly for cost-competitive engine component manufacturing. Regional trade agreements and the development of free trade zones are also lowering barriers for raw material imports and finished part exports. Across all regions, collaborative research partnerships and knowledge-sharing forums drive continuous refinement of binder chemistries, sintering protocols, and quality assurance methodologies, ensuring that aerospace MIM maintains a resilient outlook in the face of shifting geopolitical and economic landscapes.
This comprehensive research report examines key regions that drive the evolution of the Aerospace MIM Parts market, offering deep insights into regional trends, growth factors, and industry developments that are influencing market performance.
- Americas
- Asia-Pacific
- Europe, Middle East & Africa
Insights into Leading Aerospace MIM Manufacturers
Leading enterprises are reinforcing their competitive edge through proprietary powder production, advanced sintering ovens, and integrated quality control systems. Advanced Powder Products, Inc. has expanded its alloy roster to include custom titanium MIM powders for thermal management applications, while ARC Group Worldwide, Inc. leverages its global network to optimize debinding and sintering cycles across multiple continents. CMG Technologies Ltd and Dynacast International Inc. are collaborating on hybrid manufacturing cells that seamlessly integrate metal injection molding with additive layering, reducing secondary machining.
Form Technologies and Indo-MIM Pvt Ltd emphasize micro-precision MIM for avionics housings and microvalve components, and MIM International Pvt Ltd is pioneering binder formulations that lower sintering temperatures by up to 15%. Schunk Sintermetalltechnik GmbH focuses on high-temperature superalloy MIM parts for turbine applications, while SINTOKOGIO, LTD. and Smith Metal Products have partnered to enhance process automation and inline inspection capabilities. Collectively, these initiatives underscore a broader shift toward vertically integrated solutions that span powder metallurgy, process engineering, and digital quality assurance.
This comprehensive research report delivers an in-depth overview of the principal market players in the Aerospace MIM Parts market, evaluating their market share, strategic initiatives, and competitive positioning to illuminate the factors shaping the competitive landscape.
- Advanced Powder Products, Inc.
- ARC Group Worldwide, Inc.
- CMG Technologies Ltd
- Dynacast International Inc.
- Form Technologies
- Indo-MIM Pvt Ltd
- MIM International Pvt Ltd
- Schunk Sintermetalltechnik GmbH
- SINTOKOGIO, LTD.
- Smith Metal Products
Actionable Recommendations for Aerospace MIM Industry Leaders
Industry leaders must proactively align strategic priorities with evolving technologies and regulatory frameworks. First, investing in localized feedstock production and multi-material binder research will mitigate tariff-driven cost pressures and foster supply chain agility. Second, forging deeper collaborations with research institutes and OEMs ensures access to cutting-edge hybrid manufacturing methods, particularly for emerging propulsion technologies that demand micro-level precision. Third, integrating digital twins and predictive maintenance algorithms into sintering and debinding operations can enhance process repeatability and reduce scrap rates.
Fourth, adopting end-to-end traceability platforms will address growing sustainability mandates and support circular economy initiatives through improved end-of-life disposition tracking. Fifth, tailoring product portfolios across complexity tiers-from simple brackets to micro-complex thermal management parts-allows organizations to capture diverse end-user segments spanning commercial, military, and space exploration applications. Finally, industry stakeholders should champion cross-industry alliances to share best practices in automation, simulation, and quality assurance, accelerating time-to-market for next-generation aerospace MIM solutions.
Explore AI-driven insights for the Aerospace MIM Parts market with ResearchAI on our online platform, providing deeper, data-backed market analysis.
Ask ResearchAI anything
World's First Innovative Al for Market Research
Conclusion: Positioning for Sustained Leadership in Aerospace MIM
The aerospace MIM sector stands at a pivotal inflection point, driven by advancements in materials science, process integration, and digitalization. Through strategic segmentation, regional positioning, and the adoption of hybrid manufacturing paradigms, stakeholders can unlock significant efficiencies while meeting stringent performance and sustainability standards. Proactive measures to diversify feedstock sources, collaborate on binder and powder innovations, and implement predictive quality control will be crucial for navigating tariff uncertainties and geopolitical shifts.
Moreover, the fusion of MIM with additive manufacturing and real-time process analytics heralds a new era of micro-precision component production, fueling applications from avionics to space exploration. As key players refine their value propositions through vertical integration and cross-industry partnerships, they will set the benchmark for resilient, cost-effective supply chains capable of supporting the aerospace sector’s most demanding programs.
This section provides a structured overview of the report, outlining key chapters and topics covered for easy reference in our Aerospace MIM Parts market comprehensive research report.
- Preface
- Research Methodology
- Executive Summary
- Market Overview
- Market Dynamics
- Market Insights
- Cumulative Impact of United States Tariffs 2025
- Aerospace MIM Parts Market, by Material Type
- Aerospace MIM Parts Market, by Application
- Aerospace MIM Parts Market, by Manufacturing Process
- Aerospace MIM Parts Market, by Part Complexity
- Aerospace MIM Parts Market, by End User
- Aerospace MIM Parts Market, by Component Size
- Aerospace MIM Parts Market, by Product Life Cycle Phase
- Aerospace MIM Parts Market, by Functionality
- Aerospace MIM Parts Market, by Industry Collaboration & Partnerships
- Americas Aerospace MIM Parts Market
- Asia-Pacific Aerospace MIM Parts Market
- Europe, Middle East & Africa Aerospace MIM Parts Market
- Competitive Landscape
- ResearchAI
- ResearchStatistics
- ResearchContacts
- ResearchArticles
- Appendix
- List of Figures [Total: 34]
- List of Tables [Total: 428 ]
Call to Action: Secure Your Aerospace MIM Market Intelligence Today
Ready to gain an in-depth understanding of these trends and capitalize on emerging opportunities? Contact Ketan Rohom, Associate Director, Sales & Marketing, to purchase the comprehensive market research report and secure actionable intelligence for your aerospace MIM strategy.
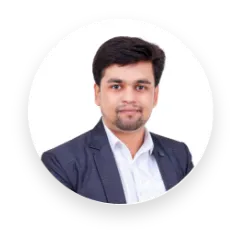
- When do I get the report?
- In what format does this report get delivered to me?
- How long has 360iResearch been around?
- What if I have a question about your reports?
- Can I share this report with my team?
- Can I use your research in my presentation?