The Aerospace Riveting Equipment Market size was estimated at USD 120.57 million in 2024 and expected to reach USD 127.45 million in 2025, at a CAGR 5.44% to reach USD 165.77 million by 2030.
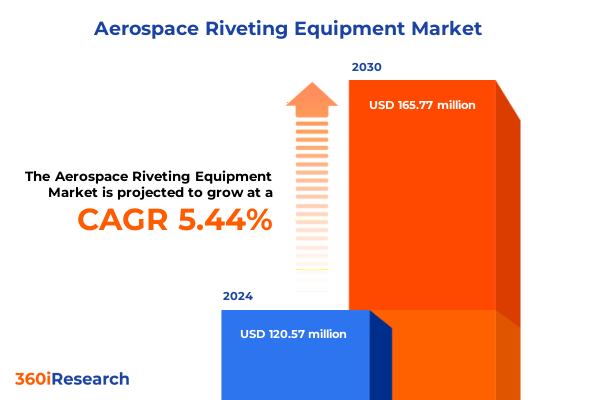
Introduction to the Aerospace Riveting Equipment Ecosystem
The aerospace sector relies on precision, reliability, and efficiency in every riveted joint that holds critical structures aloft. As aircraft manufacturers and maintenance teams strive to meet escalating safety standards and production targets, the tools and systems used for riveting have evolved into high‐performance solutions. From bench machines housed in specialized jigs to portable riveters deployed on wings at cruising altitude, the equipment landscape is diversifying in response to demands for tighter tolerances, faster cycle times, and lower lifecycle costs. This introduction frames our executive summary, guiding decision-makers through the pivotal dynamics shaping the aerospace riveting market and setting the stage for deeper insights into emerging shifts, tariff impacts, segmentation nuances, regional variations, and competitive strategies.
Transformative Shifts Reshaping the Market Landscape
The aerospace riveting market is undergoing transformative shifts driven by the convergence of automation, advanced materials, and digital integration. Robotic and CNC systems are gaining ground as manufacturers pursue consistent joint quality and throughput gains. Simultaneously, the rise of composite airframes and lightweight alloys demands riveters capable of handling diverse material properties without compromising fatigue resistance. Digital connectivity and predictive maintenance platforms are extending equipment uptime while offering real-time analytics on joint integrity. Trade tensions and evolving regulatory frameworks are compelling OEMs and suppliers to reconfigure supply chains closer to end-use hubs. Environmental imperatives are fostering greater adoption of systems that minimize waste and serve water-based cleaning protocols. Collectively, these shifts are redefining what constitutes best-in-class riveting equipment and catalyzing a new generation of solutions that marry mechanical precision with data-driven intelligence.
Cumulative Impact of United States Tariffs 2025
The introduction of new U.S. tariffs in 2025 has imposed additional layers of complexity on aerospace riveting equipment flows. Import duties on finished machines and critical spare components have elevated acquisition and maintenance costs, motivating domestic investment into local assembly and service operations. In parallel, retaliatory measures by key trading partners have affected the availability of popular pneumatic and hydraulic hand tools sourced overseas, prompting manufacturers to diversify supplier portfolios. Tariffs have also accelerated the shift toward automated rivet insertion cells assembled in North America, reducing exposure to cross-border duties while preserving lead times. While some manufacturers are absorbing incremental costs to maintain pricing stability, others are leveraging tariff-driven incentives to repatriate production of specialized CNC riveting platforms. The net effect is a rebalanced supply chain where tariff considerations now play a central role in procurement strategies and capital expenditure planning.
Key Segmentation Insights Across Product, Rivet, Material, Industry, Technology, and Application
Delving into product-type segmentation reveals that bench riveting machines remain the cornerstone of high-precision jigs, with automatic variants accelerating pilot production runs, while semi-automatic models deliver a balance of flexibility and cost-efficiency. Floor riveting machines bifurcate into heavy-duty platforms engineered for fuselage subassemblies and standard units optimized for moderate throughput applications. Portable riveting devices span hydraulic hand riveters favored for heavy-gauge panels and pneumatic tools suited to swift repair operations. Across rivet types, blind rivets now include closed-end solutions for leak-proof seals and open-end versions that facilitate inspection access. Solid rivets present button head profiles for surface contour compatibility and flat heads for flush aerodynamic finish. Tubular rivets cover full-body styles offering mechanical collapse and semi-tubular options ensuring ease of clinching. Material-type segmentation underscores the dominance of aluminum alloys tailored for lightweight skins, pure aluminum for corrosion resistance, brass and pure copper for electrical grounding, carbon and stainless steel for structural reinforcement, and grade-specific titanium varieties used in hot sections and critical fasteners. End-user industries range from commercial aviation production and maintenance to business jets in general aviation, combat and support platforms in defense, and spacecraft assembly for both satellite payloads and exploration vehicles. On the automation spectrum, fully automatic riveting cells and robot-assisted units drive high-volume assembly, 3-axis and 5-axis CNC machines enable complex joint geometries, and manual options including foot-operated and hand-operated tools remain essential for in-field repairs. Finally, applications span fuselage and wing airframe assembly, compressor and turbine engine parts, and cabin interior fittings, with each requiring tailored joint parameters to meet performance specifications.
This comprehensive research report categorizes the Aerospace Riveting Equipment market into clearly defined segments, providing a detailed analysis of emerging trends and precise revenue forecasts to support strategic decision-making.
- Product Type
- Rivet Type
- Material Type
- End-User Industry
- Technology Type
- Application
Key Regional Insights Shaping Market Dynamics
Regional dynamics illustrate distinct strategic priorities and adoption curves. In the Americas, near-shoring trends and robust maintenance, repair, and overhaul activities sustain demand for portable and floor riveting solutions, while incentives for domestic manufacturing spur local production of automated bench cells. Europe, the Middle East & Africa exhibit a dual focus on stringent certification standards and fleet modernization programs, driving uptake of advanced CNC systems and closed-loop quality monitoring. Meanwhile, the Asia-Pacific region experiences rapid expansion in commercial aviation infrastructure, incentivizing investments in versatile semi-automatic machines that balance capital cost with throughput. Growth in defense and spacecraft projects in emerging APAC markets further fuels demand for specialized riveters capable of handling exotic alloys. Across all regions, service networks and technical training offerings have become pivotal selection criteria as end-users seek to maximize uptime and ensure consistent joint integrity.
This comprehensive research report examines key regions that drive the evolution of the Aerospace Riveting Equipment market, offering deep insights into regional trends, growth factors, and industry developments that are influencing market performance.
- Americas
- Asia-Pacific
- Europe, Middle East & Africa
Key Companies Insights and Strategic Emphases
Leading players across the aerospace riveting equipment landscape are honing their competitive positioning through product innovation, strategic partnerships, and expanded service portfolios. Aircraft Spruce leverages its distribution network to support aftermarket tool availability, while Allfast Fastening Systems emphasizes integrated fastener-to-machine solutions. Apex Tool Group and ATF Inc. invest heavily in R&D for next-generation pneumatic riveters, as Atlas Copco AB and Ingersoll Rand pursue electrification of traditionally hydraulic platforms. Avdel (India) pivots toward local assembly to circumvent tariff barriers, and companies such as Bay Supply and Boltun Corporation augment offerings with digital maintenance support. Bossard Group and Sherex Fastening Solutions differentiate through assembly consultancy services, while Broetje-Automation and KUKA AG lead the charge on fully automated riveting cells. Brown Aviation Tool Company and Loyd's Rivet Drill Guide uphold legacy reputations in manual applications, and High-tech innovators like Novacam Technologies and Precimac Tool LTD. introduce non-destructive inspection integration. The extensive roster of players including Cherry Aerospace, Fastening Systems International, Goebel Fasteners, Howmet Aerospace, Indo Schöttle, LAS Aerospace, Sioux Tools, and Stanley Engineered Fastening collectively underscores an ecosystem where collaboration, customization, and service excellence define market leadership.
This comprehensive research report delivers an in-depth overview of the principal market players in the Aerospace Riveting Equipment market, evaluating their market share, strategic initiatives, and competitive positioning to illuminate the factors shaping the competitive landscape.
- Aircraft Spruce
- Allfast Fastening Systems
- Apex Tool Group, LLC
- ATF Inc.
- Atlas Copco AB
- Avdel (India) Pvt. Ltd
- Bay Supply
- Boltun Corporation, Ltd.
- Bossard Group
- Broetje-Automation GmbH
- Brown Aviation Tool Company
- Cherry Aerospace
- Fastening Systems International, Inc.
- Goebel Fasteners Inc.
- Howmet Aerospace Inc
- Indo Schöttle Pvt. Ltd.
- Ingersoll Rand
- KUKA AG
- LAS Aerospace Ltd.
- Loyd's Rivet Drill Guide
- Novacam Technologies, Inc.
- Precimac Tool LTD.
- Sherex Fastening Solutions
- Sioux Tools Inc
- Stanley Engineered Fastening
Actionable Recommendations for Industry Leaders
Industry leaders can capitalize on evolving market dynamics by prioritizing a set of actionable initiatives. First, integrate predictive analytics into riveting platforms to enhance preventative maintenance and reduce unplanned downtime. Second, cultivate localized support hubs in major aerospace clusters to mitigate tariff impacts and strengthen customer relationships. Third, expand modular automation offerings that allow seamless scaling from manual processes to fully robotic cells as production volumes fluctuate. Fourth, deepen partnerships with rivet and material suppliers to develop co-engineered solutions optimized for emerging alloys and composite substrates. Fifth, invest in comprehensive training programs that equip technicians with certification in smart riveting technologies and nondestructive inspection techniques. Finally, establish sustainability roadmaps that minimize consumable waste and align with aerospace decarbonization goals, reinforcing brand reputation and meeting regulatory expectations.
Explore AI-driven insights for the Aerospace Riveting Equipment market with ResearchAI on our online platform, providing deeper, data-backed market analysis.
Ask ResearchAI anything
World's First Innovative Al for Market Research
Conclusion
As aerospace manufacturers and service providers navigate a landscape marked by technological innovation, regulatory shifts, and geopolitical considerations, the ability to adapt riveting equipment strategies will determine competitive advantage. Embracing automation without losing sight of manual repair needs, instilling data-driven practices, and forging resilient supply chains are essential to delivering high-integrity joints under cost and performance pressures. By synthesizing segmentation insights, regional priorities, and competitive best practices, organizations can refine their equipment mix and service offerings to support both current fleet demands and next-generation air and space programs.
This section provides a structured overview of the report, outlining key chapters and topics covered for easy reference in our Aerospace Riveting Equipment market comprehensive research report.
- Preface
- Research Methodology
- Executive Summary
- Market Overview
- Market Dynamics
- Market Insights
- Cumulative Impact of United States Tariffs 2025
- Aerospace Riveting Equipment Market, by Product Type
- Aerospace Riveting Equipment Market, by Rivet Type
- Aerospace Riveting Equipment Market, by Material Type
- Aerospace Riveting Equipment Market, by End-User Industry
- Aerospace Riveting Equipment Market, by Technology Type
- Aerospace Riveting Equipment Market, by Application
- Americas Aerospace Riveting Equipment Market
- Asia-Pacific Aerospace Riveting Equipment Market
- Europe, Middle East & Africa Aerospace Riveting Equipment Market
- Competitive Landscape
- ResearchAI
- ResearchStatistics
- ResearchContacts
- ResearchArticles
- Appendix
- List of Figures [Total: 28]
- List of Tables [Total: 1163 ]
Call-To-Action: Engage with Ketan Rohom for Your Market Research Report
To explore these insights in greater depth and leverage a comprehensive market research report tailored to your strategic objectives, connect with Ketan Rohom, Associate Director, Sales & Marketing. Secure the detailed analysis and guidance you need to navigate the aerospace riveting equipment market with confidence. Reach out today to purchase your definitive resource.
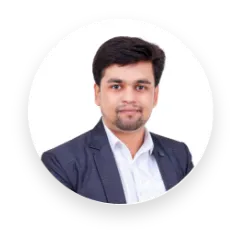
- How big is the Aerospace Riveting Equipment Market?
- What is the Aerospace Riveting Equipment Market growth?
- When do I get the report?
- In what format does this report get delivered to me?
- How long has 360iResearch been around?
- What if I have a question about your reports?
- Can I share this report with my team?
- Can I use your research in my presentation?