Introduction to Autonomous Ground Vehicles in Harsh Environments
Harsh environments on industrial sites present unique challenges for automation. Extreme temperatures, corrosive atmospheres, uneven topography and remote locations demand solutions that maintain reliability under stress. In response, Autonomous Ground Vehicles (AGVs) have evolved beyond factory floors to undertake tasks previously considered too hazardous or complex. This summary examines the current state of AGVs engineered for mining tunnels, offshore platforms, defense installations and forestry operations, highlighting how design innovations have enabled mission-critical performance. Through ruggedized drive systems, reinforced chassis materials and advanced sensor suites, modern AGVs deliver consistent uptime and precise navigation even when visibility is limited or terrain is unstable. Key stakeholders-from equipment manufacturers to end users in mining, oil and gas, agriculture, aerospace and marine sectors-are investing in these platforms to reduce labor risks, optimize resource utilization and meet stringent safety regulations. Through integration with digital twin environments and cloud-based analytics, these vehicles support predictive maintenance and optimize route planning. Open communication protocols enable seamless interoperability with fixed automation systems and other autonomous agents, creating a unified operations ecosystem. Customization options in powertrain configuration and navigational algorithms allow users to tailor AGV performance to specific environmental constraints, from deep underground mining to offshore wind farms. This synthesis underscores the transformative potential of AGVs to drive operational efficiency, enhance safety and deliver ROI in settings where traditional vehicles falter. With this foundation, executives can align strategic objectives with the evolving landscape of automation in extreme settings, ensuring competitive resilience as deployment scales globally.
Transformative Shifts Reshaping the AGV Landscape
Recent years have witnessed significant shifts that are redefining the potential of AGVs in challenging environments. Advances in sensor fusion, machine learning and edge computing have introduced unprecedented levels of autonomy, enabling vehicles to navigate dynamic obstacles and adapt to real-time changes in terrain. Concurrently, the push for sustainability and energy efficiency has accelerated the development of alternative power supply systems, such as hybrid configurations combining battery-electric drives with hydraulic or pneumatic actuation to extend operational duration while reducing emissions. Meanwhile, safety has moved to the forefront, prompting the integration of sophisticated monitoring systems and collision avoidance protocols that operate effectively even in conditions of limited visibility. On the business side, supply chain disruptions have highlighted the necessity of localizing component production and diversifying sourcing strategies, spurring partnerships between system integrators and regional manufacturers. Furthermore, the rise of cloud-based fleet management platforms is enabling centralized control and predictive maintenance capabilities at scale, driving down downtime and lowering total cost of ownership.
At the same time, material science breakthroughs have yielded corrosion-resistant alloys and impact-tolerant composites that extend vehicle lifespan in harsh chemical or abrasive environments. Modularity in system architecture now allows rapid swapping of key components, from drive units to sensor arrays, simplifying maintenance and enabling quick mission reconfiguration for varied tasks. With commercialization cycles shortening, OEMs are accelerating time to market through agile development methodologies, conducting iterative field trials to refine performance. As a result, operators are witnessing an acceleration from conceptual proofs to production-scale deployments, with fleet sizes doubling in certain sectors over the last two years. This momentum is underpinned by growing collaboration between robotics specialists, software developers and end users, forging integrated solutions that address complex logistical challenges. Collectively, these transformative shifts are setting the stage for AGVs to become foundational assets in operations where human intervention is either risky or impractical.
Assessing the Cumulative Impact of United States Tariffs 2025 on AGV Deployments
Tariff adjustments scheduled for 2025 in the United States are poised to influence the economics of AGV production and deployment significantly. Proposed duties on specialized components such as precision motors, sensor modules and ruggedized electronics have the potential to elevate import costs. As many system integrators rely on global supply chains to source high-quality parts, these additional levies may drive up capital expenditures and prompt a reexamination of bill of materials. Consequently, manufacturers are evaluating strategies to mitigate cost pressure, including relocating subassembly operations stateside and negotiating volume-based discounts with domestic suppliers. Some end users are assessing the feasibility of shifting partially to rental or leasing models to avoid upfront tariff-induced capital charges, while others are exploring joint ventures to establish regional manufacturing clusters that qualify for preferential trade treatment. These dynamics are likely to vary across end use segments; for example, sectors with higher regulatory compliance costs, such as defense and aerospace, may absorb tariff-related increases more readily than price-sensitive industries like agriculture. In response, stakeholders are advised to engage in proactive scenario planning, stress test procurement workflows and leverage tariff classification expertise to identify potential exemptions or duty drawback opportunities. By understanding the cumulative impact of upcoming tariff measures, decision-makers can safeguard project economics and maintain competitive positioning as headwinds intensify.
Moreover, the potential for reciprocal trade measures from key export markets underscores the need for vigilance; retaliatory tariffs could affect export channels for domestically produced AGVs, adding further complexity to revenue forecasting and market entry plans. Technology providers are considering modularization of critical systems to decouple high-tariff components, enabling easier substitution or upgrade without full vehicle redesign. Simultaneously, financial stakeholders are revising ROI benchmarks to account for tariff-driven cost inflation and potential delays in deployment schedules. Leadership teams should maintain close dialogue with customs authorities and industry associations to track regulatory developments and advocate for clarifications that minimize disruption. Through such coordinated efforts, organizations can adapt supply chain architectures and procurement strategies to absorb tariff pressures while continuing to advance automation initiatives.
Key Market Segmentation Insights for Harsh Environment AGVs
An end user industry analysis reveals a spectrum of demand drivers spanning aerospace facilities requiring precise part transport, agricultural operations seeking autonomous harvesting support, defense establishments prioritizing logistical resilience, forestry enterprises handling heavy timber, marine platforms conducting cargo transfers and oil and gas sites overseeing equipment movement under corrosive conditions. Within the mining subsector, surface mining applications emphasize high-capacity payloads and wide clearance, whereas underground environments demand compact form factors with robust obstacle negotiation. Concurrently, distinct preferences emerge in drive system architectures: hybrid vehicles combine multiple propulsion methods to balance torque and endurance, legged AGVs navigate uneven terrain by emulating biological locomotion, tracked platforms deliver enhanced traction on slippery surfaces, and wheeled designs offer efficiency in smoother settings. Power supply choices range from electric battery packs favored for zero onsite emissions to hydraulic systems delivering high force density and pneumatic setups suited to intrinsically safe environments. Material handling requirements further segment the market between solutions optimized for carrying giant loads, mixed mode tasks, pallet manipulation and towing soldier’s duty scenarios. Navigation technology adoption is split among inductive guidance embedded in flooring, line-of-sight laser navigation, magnetic strip systems affixed to pathways and vision-based guidance leveraging advanced algorithms. Load handling typologies include integration into assembly line workflows, automated forklift replacements, tow vehicles for convoys and unit load carriers. Safety mandates propel the integration of advanced monitoring systems, automated collision avoidance, emergency stop mechanisms and sensor and alarm networks. Deployment areas span assembly line operations, inventory management processes, material transport corridors and robotics integration hubs. Finally, system components bifurcate into hardware-controls, drive units and motors-and software-control systems and navigation algorithms-that collectively determine performance and upgrade potential.
This comprehensive research report categorizes the AGV for Harsh Environments market into clearly defined segments, providing a detailed analysis of emerging trends and precise revenue forecasts to support strategic decision-making.
- End User Industry
- Type Of Drive System
- Power Supply System
- Material Handling Capability
- Navigation Technology
- Load Handling Type
- Safety Features
- Application
- System Component
Critical Regional Insights for Global AGV Deployment
In the Americas, robust infrastructure investment paired with stringent workplace safety regulations is accelerating AGV adoption in mining, oil and gas and logistics hubs. Demand concentration along established industrial corridors and innovation clusters in North America is fostering North-South collaboration, while Latin American markets are emerging as growth avenues for cost-effective platforms adapted to remote operations. Europe, the Middle East and Africa exhibit heterogeneous uptake driven by regulatory frameworks prioritizing sustainability and digital transformation. Western Europe leads in integrating AGVs with broader Industry 4.0 initiatives, whereas the Middle East’s energy and construction sectors are deploying vehicles for offshore and desert applications. In Africa, the mining sector’s appetite for reliable automation under challenging geological conditions is encouraging partnerships with global OEMs. Asia-Pacific stands out for rapid prototype to production cycles, with key markets in China, Japan and Australia pioneering electric-driven AGVs for manufacturing and resource extraction. Regional supply chain resilience efforts, bolstered by government incentives, are nurturing local assembly hubs and component manufacturing facilities. Collectively, these regional dynamics define a mosaic of opportunity, necessitating tailored strategies to address local regulatory, environmental and operational requirements.
This comprehensive research report examines key regions that drive the evolution of the AGV for Harsh Environments market, offering deep insights into regional trends, growth factors, and industry developments that are influencing market performance.
- Americas
- Asia-Pacific
- Europe, Middle East & Africa
Leading Companies Driving Innovation in Harsh Environment AGVs
A diverse set of technology providers spearheads research, development and commercialization of AGVs suited to extreme conditions. Aethon, Inc. champions corridor-based navigation solutions, while AGILOX Services GmbH focuses on modular, scalable platforms for dynamic warehouse environments. Boston Dynamics, Inc. pushes the boundaries of legged AGV capabilities, enabling operation on uneven terrain inaccessible to traditional wheeled systems. Fanuc Corporation delivers integrated robotic cells with high payload capacity and precision control. Geek+, operating as Beijing Geekplus Technology Co., Ltd., introduces AI-driven fleet orchestration for indoor and outdoor logistics. GreyOrange Pte Ltd. offers hybrid powertrain options to extend operational ranges in temperature-sensitive settings. John Bean Technologies Corporation (JBT) leverages its heritage in airport ground support to provide robust vehicles for material transfer under corrosive exposure. KUKA AG’s expertise in industrial automation manifests in ruggedized tracked and wheeled designs. Locus Robotics Corporation excels in collaborative multi-robot coordination, enhancing throughput in large-scale operations. Mobile Industrial Robots (MiR) distinguishes itself with flexible deployment software and plug-and-play safety features. OTTO Motors, a division of Clearpath Robotics Inc., integrates advanced monitoring and predictive maintenance tools. Savioke, Inc. focuses on last-mile delivery in sterile and controlled environments. Seegrid Corporation’s vision guidance systems underpin high-speed pallet handling solutions. Toyotetsu AGV Systems, Inc. designs tailor-made vehicles for heavy-duty tasks, and Vecna Robotics, Inc. builds smart logistics platforms that fuse automated collision avoidance with data analytics. Together, these companies drive forward the capabilities and reliability of AGVs in the most demanding operational contexts.
This comprehensive research report delivers an in-depth overview of the principal market players in the AGV for Harsh Environments market, evaluating their market share, strategic initiatives, and competitive positioning to illuminate the factors shaping the competitive landscape.
- Aethon, Inc.
- AGILOX Services GmbH
- Boston Dynamics, Inc.
- Fanuc Corporation
- Geek+ (Beijing Geekplus Technology Co., Ltd.)
- GreyOrange Pte Ltd.
- John Bean Technologies Corporation (JBT)
- KUKA AG
- Locus Robotics Corporation
- MiR (Mobile Industrial Robots)
- OTTO Motors (A Division of Clearpath Robotics Inc.)
- Savioke, Inc.
- Seegrid Corporation
- Toyotetsu AGV Systems, Inc.
- Vecna Robotics, Inc.
Actionable Recommendations for Industry Leaders
Industry leaders seeking to capitalize on the momentum in harsh environment AGV deployment should pursue several strategic initiatives. First, invest in modular architectures that permit rapid reconfiguration of powertrains, sensor suites and material handling attachments, thereby accelerating response to evolving operational needs. Next, localize critical components and subassembly operations to insulate supply chains from tariff risks and minimize lead times, while maintaining agreements with multiple suppliers to safeguard continuity. Third, prioritize safety feature integration by implementing automated collision avoidance, advanced monitoring systems and standardized emergency stop protocols, ensuring compliance with diverse regional regulations and protecting personnel. Fourth, cultivate specialized talent in robotics, systems integration and data analytics by forging partnerships with academic institutions and sponsoring targeted training programs. Fifth, engage in collaborative pilot projects with technology providers and end users to validate performance in real-world scenarios, collecting data to refine navigation algorithms and predictive maintenance models. Sixth, monitor regulatory developments and trade policy shifts closely, adapting procurement strategies to leverage potential exemptions or drawback opportunities. Seventh, adopt digital twin and cloud-based fleet management platforms to gain granular visibility into vehicle health, utilization patterns and energy consumption. Finally, establish cross-functional governance structures to align engineering, operations and finance teams on AGV implementation roadmaps, ensuring that investments deliver measurable ROI and sustainable competitive advantage.
Explore AI-driven insights for the AGV for Harsh Environments market with ResearchAI on our online platform, providing deeper, data-backed market analysis.
Ask ResearchAI anything
World's First Innovative Al for Market Research
Conclusion: Navigating the Next Frontier in Harsh Environment Automation
As autonomous ground vehicles mature, their capacity to operate reliably in extreme conditions is unlocking new efficiencies, safety improvements and cost savings across industries. The convergence of advanced navigation technologies, ruggedized hardware designs and adaptive power supply systems is propelling AGVs from isolated use cases to integral components of end-to-end automation strategies. Navigating tariff landscapes, regional regulatory frameworks and supply chain dynamics will require proactive planning and stakeholder collaboration. By leveraging granular segmentation insights, regional market intelligence and competitive analyses, organizations can craft tailored approaches that align investment priorities with operational objectives. With the growth of fleet management platforms and predictive analytics, continuous improvement cycles will become standard practice, driving incremental gains and long-term performance resilience. As the pace of innovation accelerates, the companies that adopt agile architectures, invest in talent development and foster ecosystem partnerships will emerge as leaders in this evolving landscape. Looking ahead, the integration of AGVs with autonomous aerial and maritime systems promises multi-modal logistics networks capable of end-to-end material flow even in the planet’s most remote and hostile regions. Stakeholders who anticipate these developments and align roadmaps accordingly will secure a decisive edge in automating mission-critical operations at scale.
This section provides a structured overview of the report, outlining key chapters and topics covered for easy reference in our AGV for Harsh Environments market comprehensive research report.
- Preface
- Research Methodology
- Executive Summary
- Market Overview
- Market Dynamics
- Market Insights
- Cumulative Impact of United States Tariffs 2025
- AGV for Harsh Environments Market, by End User Industry
- AGV for Harsh Environments Market, by Type Of Drive System
- AGV for Harsh Environments Market, by Power Supply System
- AGV for Harsh Environments Market, by Material Handling Capability
- AGV for Harsh Environments Market, by Navigation Technology
- AGV for Harsh Environments Market, by Load Handling Type
- AGV for Harsh Environments Market, by Safety Features
- AGV for Harsh Environments Market, by Application
- AGV for Harsh Environments Market, by System Component
- Americas AGV for Harsh Environments Market
- Asia-Pacific AGV for Harsh Environments Market
- Europe, Middle East & Africa AGV for Harsh Environments Market
- Competitive Landscape
- ResearchAI
- ResearchStatistics
- ResearchContacts
- ResearchArticles
- Appendix
- List of Figures [Total: 34]
- List of Tables [Total: 558 ]
Next Steps: Unlock Comprehensive AGV Market Intelligence with Ketan Rohom
To gain in-depth analysis, detailed segmentation data and actionable foresight for AGVs in harsh environments, reach out to Ketan Rohom, Associate Director of Sales & Marketing. Schedule a personalized consultation to discuss how the full market research report can support strategic decision-making, optimize procurement planning and inform technology roadmaps. Secure access to proprietary insights that will equip your organization to navigate evolving regulatory landscapes, tariff impacts and competitive dynamics. Contact Ketan Rohom today to acquire the comprehensive study and position your enterprise at the forefront of industrial automation.
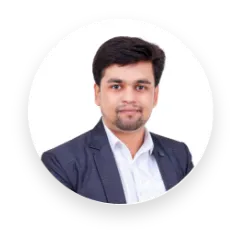
- When do I get the report?
- In what format does this report get delivered to me?
- How long has 360iResearch been around?
- What if I have a question about your reports?
- Can I share this report with my team?
- Can I use your research in my presentation?