Introduction: Setting the Stage for Air Spinning Machine Market Dynamics
The air spinning machine market stands at a pivotal juncture, propelled by rapid technological advances and evolving end-user demands. As textile manufacturers strive for higher productivity, consistent yarn quality, and reduced environmental footprints, air-jet, open-end rotor, and vortex spinning technologies have become central to meeting these objectives. This landscape is shaped by emerging digital toolsets, sustainable material trends, and shifting supply chain dynamics that collectively redefine competitive advantage. Industry leaders are embracing automation, predictive maintenance, and integrated control systems to streamline operations and unlock new revenue streams. Concurrently, global economic policies and trade measures are prompting strategic realignments in sourcing, production, and market entry. The following executive summary outlines transformative shifts, policy impacts, granular segmentation insights, regional differentiators, and profiles of key participants-all leading to actionable guidance for decision-makers seeking to navigate this dynamic environment.
Transformative Shifts Redefining Air Spinning Machine Landscape
Over the past decade, several transformative forces have converged to redefine the air spinning machine landscape. First, the advent of Industry 4.0 frameworks has accelerated the integration of IoT sensors, digital twins, and advanced analytics into spinning lines-enabling real-time quality control and predictive upkeep. Second, sustainability mandates and consumer demand for eco-friendly textiles have driven a shift toward energy-efficient designs and closed-loop water management, prompting OEMs to incorporate servo motors, regenerative braking, and green materials.
Third, the rise of lightweight and high-performance textiles-spanning automotive upholstery, medical gowns, and technical fabrics-has elevated the role of precise jet configurations, rotor geometries, and feed preparation systems. These advancements empower mills to craft yarns with tailored tenacity, elongation, and surface properties. Lastly, supply chain resilience initiatives, spurred by geopolitical fluctuations and tariff pressures, are encouraging nearshoring, supplier diversification, and collaborative R&D alliances. Together, these shifts underscore a market in flux, demanding agility, innovation, and strategic foresight.
Evaluating the Cumulative Impact of United States Tariffs in 2025
The implementation of additional United States tariffs in early 2025 has reverberated across the air spinning equipment sector, triggering a series of strategic responses. Manufacturers sourcing key components-such as jets, rotors, and PLC controls-from tariffed regions have encountered heightened input costs, compelling them to reassess supplier portfolios and negotiate long-term contracts to stabilize pricing. Some machine builders have accelerated investment in domestic machining capabilities to offset duties, while others have restructured assembly footprints to higher-favorability trade zones.
On the demand side, converting mills faced margin pressures, prompting selective capital budgeting and extended machine deployment cycles. This environment has stimulated partnerships between OEMs and end users to co-finance upgrades and retrofit programs that minimize duty liabilities. Meanwhile, service providers have gained prominence by offering refurbishment, spare-parts pooling, and remote diagnostics to sustain aging fleets economically. Collectively, these adaptations illustrate how tariff dynamics continue to shape procurement strategies, technology adoption rates, and collaborative business models.
Key Segmentation Insights Driving Market Opportunities
Insights derived from machine type segmentation reveal that air-jet spinning remains the frontrunner, driven by its ability to produce high-strength yarns for technical textiles; within this category, the compact jet system is increasingly preferred for fine counts, while the continuous jet system addresses high-volume applications. Open-end rotor spinning captures significant share by offering rapid throughput and lower labor intensity; the fully automated systems excel in large-scale mills, whereas semi-automated setups provide cost-effective entry points for mid-tier operations. Vortex spinning, though newer, is carving a niche in specialty yarns-direct feed systems optimize raw fiber integration, and feed preparation setups enhance uniformity for luxury blends.
Material type breakdown indicates that blended fibers lead investments, as manufacturers seek the performance benefits of the nylon-cotton blend in workwear and the polyester-cotton blend in home textiles. Natural fibers continue to command premium positioning; cotton remains ubiquitous, silk is leveraged for high-end fashion, and wool addresses thermal and moisture-management needs. Synthetic fibers are also rising, with acrylic used in low-cost apparel, nylon valued for strength in industrial uses, and polyester dominating due to its cost efficiency and recyclability potential.
Examining end-use industry segmentation highlights that automotive applications are harnessing air-jet lines for durable car covers and sophisticated upholstery textures. Furniture manufacturers rely on vortex and open-end rotor machines for cushion filling and decorative fabrics, balancing output speed with aesthetic quality. The medical sector demands stringent hygiene and consistency, driving growth in hospital textiles and surgical garments produced on highly controlled air-jet platforms. Traditional textile mills continue to deploy a mix of machines to serve apparel and home textile markets, focusing on versatility and rapid changeover.
Sales channel analysis underscores a dual approach: direct sales channels cement relationships via distributors and manufacturer representatives, offering turnkey solutions and on-site consulting, while online retailers-through company websites and major e-commerce platforms-provide expedited procurement, transparent pricing, and modular add-ons. This hybrid model caters to a broad customer base, from established global players to agile start-ups.
From a machine components perspective, advanced control systems anchor performance enhancements, with PLC controls delivering precise process management and servo motors optimizing speed and energy use. Spinning elements such as drafting systems, jets, and rotors are central to yarn quality; mills prioritizing modularity opt for quick-change drafting frames, variable-geometry jets, and high-durability rotors to adapt rapidly to shifting product lines.
Finally, mapping the market across product life cycle stages reveals that R&D initiatives continue to spawn breakthrough prototypes, introduction-stage machines are gaining traction among early adopters, growth-stage offerings are scaling globally, mature products are undergoing incremental upgrades, and decline-stage units are being phased out or retrofitted for extended service life.
This comprehensive research report categorizes the Air Spinning Machine market into clearly defined segments, providing a detailed analysis of emerging trends and precise revenue forecasts to support strategic decision-making.
- Machine Type
- Material Type
- End-Use Industry
- Sales Channel
- Machine Components
- Product Life Cycle
Key Regional Insights Shaping Global Market Growth
Throughout the Americas, a combination of reshoring initiatives and regulatory incentives has fueled investments in energy-efficient air spinning solutions. North American auto manufacturers are validating prototypes on domestic lines, while South American textile parks are modernizing legacy installations to capture export opportunities. Sustainability standards and labor cost considerations continue to shape equipment selection, with mills favoring integrated waste-water treatments and operator-friendly controls.
In Europe, Middle East & Africa, stringent environmental regulations and customer demand for premium textiles have accelerated the adoption of closed-loop air-jet systems and servo-driven rotor machines. Luxury fashion hubs in Italy and France are collaborating with OEMs to develop count-specific spindles, while Middle Eastern textile parks leverage automation to offset labor constraints. Across Africa, entry-level open-end rotor units are expanding rapidly in cost-sensitive markets, supported by regional financing schemes.
The Asia-Pacific region remains the market’s epicenter, powered by high production volumes in China, India, and Southeast Asia. Government subsidies for modern textile parks and skill-development programs have propelled widespread installation of compact jet systems and fully automated open-end lines. Meanwhile, emerging economies are integrating digital maintenance platforms to enhance uptime. The relentless drive for cost optimization has spurred local manufacturing of key components, gradually reshaping the global supply chain hierarchy.
This comprehensive research report examines key regions that drive the evolution of the Air Spinning Machine market, offering deep insights into regional trends, growth factors, and industry developments that are influencing market performance.
- Americas
- Asia-Pacific
- Europe, Middle East & Africa
Leading Companies Shaping Technological Advancements and Competition
Jingwei Textile Machinery Co., Ltd. continues to lead in integrated spinning solutions, merging in-house R&D with robust after-sales networks to optimize line performance for Chinese and export markets. Lakshmi Machine Works Ltd. excels in open-end rotor innovations, leveraging decades of field data to refine rotor geometries and airflow dynamics for improved yarn strength. Murata Machinery, Ltd. holds a pioneering position in air-jet technology, delivering compact and continuous jet systems that balance speed with precision. Rieter Holding AG offers end-to-end spinning platforms, capitalizing on modular architectures that allow mills to scale rapidly and swap out components with minimal downtime. Saurer AG has strengthened its portfolio through digital service suites, enabling remote diagnostics on servo-driven machines and predictive maintenance leveraging AI algorithms. Savio Macchine Tessili S.p.A. remains synonymous with high-performance spinning elements, providing customizable drafting systems, jets, and rotors tailored to niche yarn specifications. TMT Machinery, Inc. sustains its global footprint by combining cost-effective rotor lines with comprehensive training programs, enhancing operator proficiency across diverse regions. Toyota Industries Corporation integrates precision engineering with IoT-enabled control systems to deliver smart spinning machines that facilitate data-driven decisions. Trutzschler Group spans both nonwoven and yarn spinning markets, deploying sustainable technologies such as closed-circuit air streams and renewable energy integrations. Zhejiang Taitan Co., Ltd. has emerged as an agile competitor, offering competitively priced machine lines and aftermarket services that rapidly address maintenance and upgrade requirements.
This comprehensive research report delivers an in-depth overview of the principal market players in the Air Spinning Machine market, evaluating their market share, strategic initiatives, and competitive positioning to illuminate the factors shaping the competitive landscape.
- Jingwei Textile Machinery Co., Ltd.
- Lakshmi Machine Works Ltd.
- Murata Machinery, Ltd.
- Rieter Holding AG
- Saurer AG
- Savio Macchine Tessili S.p.A.
- TMT Machinery, Inc.
- Toyota Industries Corporation
- Trutzschler Group
- Zhejiang Taitan Co., Ltd.
Actionable Recommendations for Industry Leaders to Navigate Change
To thrive in this evolving landscape, industry leaders should prioritize the following strategic actions:
-
Accelerate digital transformation by deploying advanced analytics platforms and digital twin simulations to optimize machine utilization, reduce unplanned downtime, and forecast maintenance needs with precision.
-
Expand sustainable credentials through investment in energy-recovery systems, closed-loop water processes, and zero-waste initiatives-demonstrating compliance with environmental regulations and meeting customer expectations for green textiles.
-
Diversify supply chain footprints to mitigate tariff exposure, leveraging nearshoring and regional assembly hubs to access local incentives and shorten lead times, while forging strategic partnerships for critical component manufacturing.
-
Cultivate a future-ready workforce by implementing targeted training programs on automation, data literacy, and advanced maintenance practices-ensuring seamless adoption of next-generation air spinning platforms.
-
Enhance after-sales propositions with tiered service packages that combine remote monitoring, predictive upkeep, and rapid spare-parts logistics-strengthening customer loyalty and creating recurring revenue streams.
-
Foster collaborative R&D ecosystems with universities, startups, and industry consortia to co-develop specialty yarn capabilities, advanced control algorithms, and sustainable materials-maintaining a pipeline of breakthrough offerings.
By executing these recommendations, equipment manufacturers and textile mills can unlock new sources of value, navigate policy headwinds, and secure leadership positions in an increasingly competitive global market.
Explore AI-driven insights for the Air Spinning Machine market with ResearchAI on our online platform, providing deeper, data-backed market analysis.
Ask ResearchAI anything
World's First Innovative Al for Market Research
Conclusion: Strategic Imperatives for Future Success
The air spinning machine market today presents both formidable challenges and exceptional opportunities. Rapid technological evolution, shifting trade dynamics, and stringent sustainability imperatives have collectively raised the bar for performance and profitability. Yet, by embracing digital tools, optimizing supply chains, and reimagining product portfolios through an environmental lens, industry participants can chart robust growth paths. Strategic investment in workforce capabilities and collaborative innovation will underpin the next generation of high-speed, energy-efficient, and precision-oriented spinning solutions. Stakeholders who balance agility with long-term planning, and who align closely with evolving customer and regulatory demands, will emerge as leaders in this dynamic sector.
This section provides a structured overview of the report, outlining key chapters and topics covered for easy reference in our Air Spinning Machine market comprehensive research report.
- Preface
- Research Methodology
- Executive Summary
- Market Overview
- Market Dynamics
- Market Insights
- Cumulative Impact of United States Tariffs 2025
- Air Spinning Machine Market, by Machine Type
- Air Spinning Machine Market, by Material Type
- Air Spinning Machine Market, by End-Use Industry
- Air Spinning Machine Market, by Sales Channel
- Air Spinning Machine Market, by Machine Components
- Air Spinning Machine Market, by Product Life Cycle
- Americas Air Spinning Machine Market
- Asia-Pacific Air Spinning Machine Market
- Europe, Middle East & Africa Air Spinning Machine Market
- Competitive Landscape
- ResearchAI
- ResearchStatistics
- ResearchContacts
- ResearchArticles
- Appendix
- List of Figures [Total: 28]
- List of Tables [Total: 901 ]
Take the Next Step: Secure Your In-Depth Market Research Report with Ketan Rohom
For deeper insights, bespoke data, and tailored guidance on navigating the air spinning machine market, connect with Ketan Rohom, Associate Director of Sales & Marketing. Benefit from expert support in securing the full market research report and gain clarity on emerging trends, competitive landscapes, and actionable strategies to drive growth and innovation.
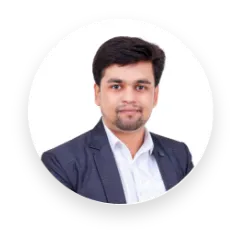
- When do I get the report?
- In what format does this report get delivered to me?
- How long has 360iResearch been around?
- What if I have a question about your reports?
- Can I share this report with my team?
- Can I use your research in my presentation?