The Aircraft Strut Market size was estimated at USD 349.56 million in 2024 and expected to reach USD 377.28 million in 2025, at a CAGR 7.78% to reach USD 548.19 million by 2030.

Navigating the Foundations of the Aircraft Strut Market
The aircraft strut market serves as a vital backbone to the aerospace industry, providing structural support, load distribution, and motion control across a diverse range of airframes. As global demand for safer, more efficient aircraft intensifies, understanding the intricate mechanics and evolving material science behind strut design has never been more critical. Struts not only absorb and transfer loads during takeoff, flight, and landing but also play an essential role in weight optimization and fuel efficiency. This analysis delves into the fundamental drivers propelling market expansion, ranging from advances in high-performance alloys and composites to stringent regulatory requirements aimed at enhancing passenger safety.
In this environment of accelerating innovation, manufacturers and suppliers must navigate a landscape shaped by intense competitive pressures, supply chain complexities, and shifting customer expectations. Decision-makers are increasingly focused on holistic lifecycle performance, including durability under extreme conditions, maintainability, and total cost of ownership. Against this backdrop, the subsequent sections offer a comprehensive view of transformative trends, regulatory headwinds, strategic segmentation, regional dynamics, and actionable insights designed to equip industry professionals with the clarity needed to thrive in a rapidly evolving marketplace.
Emerging Forces Reshaping Industry Dynamics
Recent years have witnessed profound shifts in how struts are conceptualized, designed, and produced. Materials science breakthroughs have accelerated adoption of carbon fiber, titanium, and advanced composites, enabling significant weight reductions and enhanced fatigue resistance. Concurrently, digital transformation has ushered in predictive modeling, digital twins, and integrated sensors that monitor in-service performance in real time, allowing maintenance schedules to transition from fixed intervals toward condition-based paradigms.
Sustainability imperatives are also driving manufacturers to assess end-of-life recyclability and life cycle carbon footprints, prompting collaborative research into bio-resins and metal-matrix composites. Additive manufacturing platforms have moved from prototyping toward small-batch production, offering unprecedented geometric complexity and supply chain agility. In parallel, globalization and shifting trade patterns have reshaped supplier networks, compelling leaders to balance cost optimization with resilience. These converging trends are redefining the competitive playing field and setting new benchmarks for quality, efficiency, and environmental stewardship.
Toll of Tariffs Redefining Supply Chain Equations
The implementation of expanded tariffs on aerospace components originating from key export markets has introduced a new layer of complexity. Import duties levied in early 2025 have elevated landed costs, triggered renegotiations of long-term supply contracts, and accelerated considerations for nearshoring. Pass-through pricing has placed additional burden on original equipment manufacturers, prompting many to seek alternative sources or to re-evaluate design specifications to minimize tariff exposure.
Supplier consolidation has gained momentum as firms with diversified production footprints leverage their geographic positioning to mitigate trade friction. Meanwhile, procurement teams are deploying more sophisticated tariff engineering strategies, including value-content audits and tariff classification reviews. Although these measures introduce upfront costs, they shield operational continuity from the volatility of international trade policy. The net effect is a market balancing between higher material costs and robust demand for reliable, high-performance struts essential to next-generation aircraft fleets.
Deep Dive into Material, Application, and Aircraft Type Dynamics
Analysis of the market through the lens of material types reveals that aluminum struts continue to dominate volume due to their proven balance of cost and performance, while carbon fiber and composite variants are rapidly gaining ground on platforms prioritizing weight savings. Steel struts remain integral for heavy-duty applications where toughness under cyclic loads is paramount, and titanium struts secure niche roles where corrosion resistance and strength-to-weight ratios reach critical thresholds.
When examining application domains, control surface linkages and landing gear struts represent the highest value segments, driven by stringent safety standards and the need for precision motion control. Engine mount struts, benefiting from materials engineered for vibration damping, support powerplant integration on both commercial and military jetliners. In fuselage and wing bracing applications, the interplay of structural loads and aerodynamic demands has spurred iterative refinements in forging techniques and heat-treatment processes.
The bifurcation between commercial and military aircraft underscores distinct procurement cycles, regulatory environments, and performance imperatives. Commercial platforms prioritize fuel economy, fleet commonality, and maintainability to support high-frequency operations, whereas military applications emphasize survivability, operational readiness, and customization to mission profiles. These diverging requirements shape R&D investments and production footprints across the value chain.
This comprehensive research report categorizes the Aircraft Strut market into clearly defined segments, providing a detailed analysis of emerging trends and precise revenue forecasts to support strategic decision-making.
- Material Type
- Application
- Aircraft Type
Regional Footprints Revealing Growth Hotspots
The Americas region leads with a robust manufacturing ecosystem supported by a dense network of OEMs, Tier 1 suppliers, and research institutions, fostering rapid innovation and aftermarket services. In Europe, Middle East & Africa, defense spending and regional certification frameworks drive demand for high-specification military struts, while collaborative programs among EU nations promote harmonized standards and cost sharing.
Asia-Pacific is emerging as the fastest-growing market, propelled by expanding commercial fleets, domestic aircraft development initiatives, and strategic investments in aerospace infrastructure by national carriers. Localized production hubs in Southeast Asia and East Asia are attracting technology transfers and joint ventures, enabling manufacturers to reduce lead times and align more closely with regional procurement policies. Across all geographies, harmonization of quality and safety regulations remains a critical enabler for seamless cross-border integration.
This comprehensive research report examines key regions that drive the evolution of the Aircraft Strut market, offering deep insights into regional trends, growth factors, and industry developments that are influencing market performance.
- Americas
- Europe, Middle East & Africa
- Asia-Pacific
Strategic Profiles of Market-Moving Companies
Leading suppliers are leveraging integrated solutions to differentiate across engineering, manufacturing, and aftermarket support. Established aerospace conglomerates emphasize advanced forging processes, digital inspection systems, and global service networks to secure long-term contracts with major airframers. Meanwhile, specialized fabricators focus on niche materials or tailormade designs for military applications, forging partnerships with defense prime contractors to align proprietary technologies with evolving threat environments.
Several forward-thinking companies are investing heavily in research alliances with universities and innovation labs to pioneer smart struts embedded with sensors for structural health monitoring. Others are expanding additive manufacturing capabilities to produce complex geometries with reduced tooling footprints, shortening development cycles for next-generation programs. Across the competitive landscape, strategic alliances and mergers continue to reshape the market matrix, creating entities with the scale and technical prowess to serve integrated platform programs worldwide.
This comprehensive research report delivers an in-depth overview of the principal market players in the Aircraft Strut market, evaluating their market share, strategic initiatives, and competitive positioning to illuminate the factors shaping the competitive landscape.
- Safran Landing Systems SAS
- Collins Aerospace Inc.
- Parker Hannifin Corporation
- Eaton Corporation plc
- Honeywell International Inc.
- Moog Inc.
- Triumph Group, Inc.
- Liebherr-International Deutschland GmbH
- RTX Corporation
- Intrex Aerospace
Tactical Playbook for Operational Excellence
To capitalize on emergent opportunities, industry participants should prioritize diversification of material sources to safeguard against supply chain disruptions and tariff volatility. Embracing digital engineering tools-such as simulation-driven design and predictive maintenance platforms-can accelerate product development cycles and enhance operational reliability. Furthermore, investing in additive manufacturing capabilities will unlock new design freedoms, reduce inventory carrying costs, and enable rapid response production for low-volume or custom struts.
Collaborative R&D partnerships with OEMs, research institutions, and materials specialists are essential to refine next-generation alloys and composites that meet stringent performance and sustainability criteria. Leaders should also expand regional footprints through strategic joint ventures and capacity expansions in high-growth Asia-Pacific markets. Finally, embedding sustainability metrics across product life cycles and pursuing certification for circular economy practices will resonate with environmentally conscious stakeholders and regulatory bodies alike.
Rigorous Approach Underpinning the Analysis
This analysis is underpinned by a rigorous methodology combining primary interviews with senior executives, engineers, procurement specialists, and maintenance planners across the aerospace ecosystem. Secondary research encompassed industry publications, patent filings, government regulations, and investment reports to triangulate market dynamics and validate emerging trends.
Quantitative data was normalized and cross-verified through multiple sources to ensure reliability, while qualitative insights were synthesized from expert roundtables and technical working groups. Segmentation frameworks were applied to assess performance across material types, application domains, and aircraft categories, as well as to map regional variations. The integration of tariff impact analysis further refines the assessment of cost structures and supply chain resilience under evolving trade policies.
Explore AI-driven insights for the Aircraft Strut market with ResearchAI on our online platform, providing deeper, data-backed market analysis.
Ask ResearchAI anything
World's First Innovative Al for Market Research
Synthesized Insights Driving Strategic Clarity
The convergence of advanced materials, digital transformation, and shifting geopolitical landscapes marks a pivotal moment for the aircraft strut market. Stakeholders equipped with a nuanced understanding of segmentation dynamics, regional growth drivers, and competitive positioning will be best positioned to anticipate disruptions and seize growth opportunities.
By synthesizing insights on tariff impacts, emerging technologies, and strategic partnerships, this report delivers a clear roadmap for informed decision-making. Whether refining product portfolios, optimizing supply chains, or charting new market entries, the analysis provides the strategic clarity necessary to navigate complexity and drive sustainable success in the years ahead.
This section provides a structured overview of the report, outlining key chapters and topics covered for easy reference in our Aircraft Strut market comprehensive research report.
- Preface
- Research Methodology
- Executive Summary
- Market Overview
- Market Dynamics
- Market Insights
- Cumulative Impact of United States Tariffs 2025
- Aircraft Strut Market, by Material Type
- Aircraft Strut Market, by Application
- Aircraft Strut Market, by Aircraft Type
- Americas Aircraft Strut Market
- Europe, Middle East & Africa Aircraft Strut Market
- Asia-Pacific Aircraft Strut Market
- Competitive Landscape
- ResearchAI
- ResearchStatistics
- ResearchContacts
- ResearchArticles
- Appendix
- List of Figures [Total: 22]
- List of Tables [Total: 149 ]
Secure Your Competitive Edge Today
Engaging with Ketan Rohom, Associate Director, Sales & Marketing, is the fastest path to unlocking unparalleled insights and seizing market leadership in the evolving aircraft strut sector. By securing the in-depth report, you gain access to proprietary analysis, customization options, and strategic guidance tailored to your unique business challenges. Act now to transform data into decisive action and fortify your competitive positioning. Connect directly with Ketan Rohom to arrange a personalized consultation and begin capitalizing on the market’s next wave of opportunities.
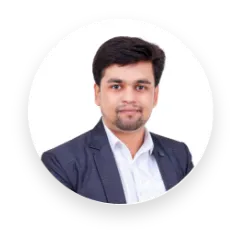
- How big is the Aircraft Strut Market?
- What is the Aircraft Strut Market growth?
- When do I get the report?
- In what format does this report get delivered to me?
- How long has 360iResearch been around?
- What if I have a question about your reports?
- Can I share this report with my team?
- Can I use your research in my presentation?