Introduction to Airplane Fuselage Skin Dynamics
The global airplane fuselage skin market stands at a pivotal crossroads where material innovation, manufacturing excellence, and regulatory landscapes converge to reshape the future of aircraft structures. As pressure to reduce weight, lower fuel consumption, and enhance performance intensifies, industry stakeholders are compelled to explore new alloys, composites, and advanced fabrication techniques. The rising adoption of carbon fiber reinforced polymers alongside breakthroughs in titanium alloys underscores a dynamic shift from traditional aluminum solutions toward multi-material fuselage configurations. Moreover, advancements in digital manufacturing-ranging from automated tape laying to electron beam welding-are elevating precision, reducing production cycle times, and enabling scalable customization.
Against this backdrop, geopolitical and trade dynamics, particularly the imposition of U.S. tariffs scheduled for 2025, introduce fresh complexity into supply chains. Procurement strategies will need to balance cost, reliability, and regional trade agreements. Meanwhile, regional demand patterns vary sharply between North America’s established OEM hubs, Europe’s robust defense sector, and Asia-Pacific’s rapid commercial aircraft expansion. Navigating these diverse market drivers requires a holistic understanding of segmentation by material type, construction technique, application, and manufacturing process. This introduction frames the key forces steering fuselage skin development and sets the stage for deeper analysis of transformative shifts, tariff impacts, segmentation insights, regional trends, and actionable recommendations.
Transformative Shifts Reshaping Skin Materials and Manufacturing
Over the past decade, the landscape of fuselage skin manufacturing has undergone transformative shifts driven by weight reduction imperatives, sustainability mandates, and digital innovation. The rise of composite materials-once confined to secondary structures-has accelerated into primary fuselage sections, as carbon fiber reinforced polymers deliver remarkable strength-to-weight ratios. Simultaneously, titanium alloys such as Ti-6Al-4V and Ti-5Al-2.5Sn are finding niche applications in areas demanding high fatigue resistance and corrosion tolerance. Beyond material evolution, manufacturing techniques have evolved from traditional riveting to cutting-edge approaches; automated tape laying systems now enable precise fiber orientation, while friction stir welding and electron beam welding eliminate mechanical fasteners, reduce distortion, and improve structural continuity.
Furthermore, the integration of digital twins and real-time quality monitoring is redefining production workflows, empowering engineers to simulate stress distributions, optimize panel geometries, and enforce stringent defect detection before physical fabrication. Coupled with additive manufacturing’s burgeoning role in producing complex stiffeners and fittings, these shifts not only promise lower production costs and shorter lead times but also open avenues for customized fuselage skins tailored to specific aircraft variants. As a result, manufacturers must align cross-functional teams-materials scientists, process engineers, and regulatory experts-to harness hybrid material architectures and advanced joining processes, thereby maintaining a competitive edge in a rapidly evolving arena.
Assessing the 2025 U.S. Tariff Impact on Supply Chains and Costs
The imposition of United States tariffs scheduled for 2025 introduces a new vector of complexity that will reverberate across global supply chains and cost structures. Materials imported under metallurgical classifications-particularly aluminum alloys like 2024-T3 and 7075-T6, along with high-performance titanium grades-are expected to face increased duties, prompting procurement teams to re-evaluate sourcing strategies. In response, some OEMs may accelerate localization efforts, fostering closer partnerships with domestic suppliers or incentivizing in-country production of raw inputs to mitigate duty exposure. At the same time, composite processors reliant on glass and carbon fiber reinforcements sourced from abroad will need to negotiate long-term contracts or invest in regional manufacturing hubs to preserve margin stability.
Beyond procurement, the tariff environment will affect cost modeling, inventory planning, and contractual negotiations with tier-one integrators. Firms that proactively adapt through hedging strategies, multi-sourcing, and collaborative R&D agreements stand to soften the financial impact. Moreover, the mandated inclusion of domestic content for certain defense and commercial programs may drive innovation in alloy development, prompting material scientists to explore next-generation formulations that deliver comparable performance at lower tariff classifications. Ultimately, the 2025 tariff regime will serve as a catalyst for supply chain resilience, compelling stakeholders to adopt agile sourcing frameworks and to reassess the total cost of ownership of fuselage skin solutions.
Segmentation Analysis by Material, Technique, Application, and Process
Insights across material type reveal that aluminum alloys remain a baseline solution for many commercial and military platforms, with 2024-T3 favored for its formability during roll forming and 7075-T6 selected where high yield strength is critical. Yet composite materials, encompassing carbon fiber reinforced polymers and glass fiber reinforced polymers, are rapidly supplanting traditional metals in long-span fuselage sections, offering exceptional stiffness and fatigue life. In parallel, titanium alloys-specifically Ti-5Al-2.5Sn and Ti-6Al-4V-address niche requirements, notably where ballistic protection or elevated temperature performance is essential.
When considering construction techniques, advanced welding systems, including electron beam and friction stir welding, are unlocking monolithic skin structures with fewer joints, thereby improving aerodynamic efficiency and reducing maintenance demands. Automatic tape laying technology complements these joining methods by precisely placing composite plies in complex contours, while traditional riveting remains a mainstay for certain fuselage frames and patches due to proven reliability.
In terms of application, commercial aircraft development is heading toward a dual divide: narrow-body platforms continue to proliferate as low-cost carriers expand their short-haul networks, whereas wide-body airframes target long-haul operators seeking superior range and payload capabilities. Each segment imposes distinct skin design criteria, from stringer patterns to fastener arrangements.
Finally, manufacturing process trends underscore the emergence of additive manufacturing for intricate stiffeners, roll forming for high-volume metal skins, and sheet metal forming processes-such as hydroforming and stamping-that strike a balance between cost efficiency and design flexibility.
This comprehensive research report categorizes the Airplane Fuselage Skins market into clearly defined segments, providing a detailed analysis of emerging trends and precise revenue forecasts to support strategic decision-making.
- Material Type
- Construction Technique
- Application in Aircraft
- Manufacturing Process
Unveiling Regional Drivers and Adoption Patterns
Regional dynamics exert a profound influence on fuselage skin strategy, beginning in the Americas where the United States and Canada host major OEM and tier-one clusters. Here, established metal suppliers and composite fabricators collaborate with defense primes to drive iterative improvements in panel toughness and weight reduction. Moving across the Atlantic into Europe, Middle East & Africa, manufacturers benefit from strong aerospace research consortiums, flexible labor markets, and an emphasis on sustainability through circular economy initiatives. This EMEA region also serves as a bellwether for regulatory harmonization across civil aviation authorities. In Asia-Pacific, rapid fleet expansions in China and India, combined with Japan’s material science expertise and Australia’s growing defense modernization programs, fuel surging demand for both metallic and composite fuselage skins. Each region’s supply chain configuration-from raw material availability to skilled workforce distribution-dictates differential adoption rates for advanced manufacturing and material innovations.
This comprehensive research report examines key regions that drive the evolution of the Airplane Fuselage Skins market, offering deep insights into regional trends, growth factors, and industry developments that are influencing market performance.
- Americas
- Asia-Pacific
- Europe, Middle East & Africa
Competitive Benchmarking of Leading Industry Players
Within this competitive landscape, several leading companies set the benchmark for fuselage skin development. Airbus SE and The Boeing Company continue to refine multi-material design philosophies for their flagship airliners, leveraging partnerships with Hexcel Corporation and Toray Industries, Inc. to secure high-performance carbon fiber supply. Alcan Global Aerospace and GKN Aerospace spearhead novel aluminum and titanium alloy treatments, while AVIC Shenyang Aircraft Corporation and Mitsubishi Heavy Industries, Ltd. are expanding their footprint in Asia-Pacific through joint ventures and technology licensing.
Specialized players like DENEL Aerostructures and Dynamic NC, Inc. excel in precision machining and advanced sheet metal forming, catering to specialized military applications. Bombardier Aerospace and Embraer S.A. drive narrow-body fuselage innovations for regional jets, integrating automatic tape laying with proprietary tape-edge mandrel designs. Leonardo S.p.A and Kawasaki Heavy Industries, Ltd. focus on friction stir welding processes to reduce defect rates in primary skin assemblies. Meanwhile, Saab Aerostructures Division and Sonaca Group are exploring additive manufacturing for lightweight structural components. Tier-one integrators such as Spirit AeroSystems, Inc., Vought Aircraft Industries, Inc., and The Boeing Company manage end-to-end fuselage assembly, coupling digital quality systems with supply chain orchestration to deliver on-time, on-spec panels.
This comprehensive research report delivers an in-depth overview of the principal market players in the Airplane Fuselage Skins market, evaluating their market share, strategic initiatives, and competitive positioning to illuminate the factors shaping the competitive landscape.
- Airbus SE
- Alcan Global Aerospace
- AVIC Shenyang Aircraft Corporation
- Bombardier Aerospace
- DENEL Aerostructures
- Dynamic NC, Inc.
- Embraer S.A.
- GKN Aerospace
- Hexcel Corporation
- Kawasaki Heavy Industries, Ltd.
- Leonardo S.p.A
- Mitsubishi Heavy Industries, Ltd.
- Saab Aerostructures Division
- Sonaca Group
- Spirit AeroSystems, Inc.
- The Boeing Company
- Toray Industries, Inc.
- Vought Aircraft Industries, Inc.
Strategic Recommendations for Sustained Competitive Advantage
Industry leaders must adopt a multifaceted strategy to thrive in a market defined by material innovation, cost pressures, and geopolitical shifts. First, investing in composite R&D partnerships and establishing pilot production lines for advanced fiber technologies will accelerate adoption curves and de-risk certification pathways. Second, diversifying supply chains through dual-sourcing arrangements-both domestically and within favorable free-trade regions-will mitigate tariff exposures and inventory volatility. Third, integrating digital twins and predictive quality analytics across the fabrication floor will reduce scrap rates, optimize welding parameters, and improve first-pass yield.
Furthermore, firms should explore vertical integration opportunities in titanium and aluminum refining to secure feedstock at competitive rates, while evaluating strategic alliances with additive manufacturing specialists to unlock on-demand stiffener production. Cross-industry collaborations with automotive and renewable energy players can yield valuable process insights and shared cost models. Finally, prioritizing workforce training programs in advanced welding, composite layup, and digital inspection technologies will build the skilled talent pipeline necessary to sustain long-term growth and innovation.
Explore AI-driven insights for the Airplane Fuselage Skins market with ResearchAI on our online platform, providing deeper, data-backed market analysis.
Ask ResearchAI anything
World's First Innovative Al for Market Research
Concluding Insights on Navigating Future Challenges
The airplane fuselage skin sector stands at the confluence of technological breakthroughs, evolving regulations, and shifting trade policies. Stakeholders who proactively embrace material diversity, advanced joining techniques, and digital manufacturing paradigms will secure resilience against cost fluctuations and supply chain disruptions. Simultaneously, a nuanced understanding of regional demand patterns and the strategic positioning of leading players provides a roadmap for collaboration, differentiation, and market leadership in both commercial and defense programs. By aligning R&D efforts with real-world application requirements and tariff mitigation strategies, decision-makers can unlock new degrees of performance, efficiency, and sustainability across the next generation of airframes.
This section provides a structured overview of the report, outlining key chapters and topics covered for easy reference in our Airplane Fuselage Skins market comprehensive research report.
- Preface
- Research Methodology
- Executive Summary
- Market Overview
- Market Dynamics
- Market Insights
- Cumulative Impact of United States Tariffs 2025
- Airplane Fuselage Skins Market, by Material Type
- Airplane Fuselage Skins Market, by Construction Technique
- Airplane Fuselage Skins Market, by Application in Aircraft
- Airplane Fuselage Skins Market, by Manufacturing Process
- Americas Airplane Fuselage Skins Market
- Asia-Pacific Airplane Fuselage Skins Market
- Europe, Middle East & Africa Airplane Fuselage Skins Market
- Competitive Landscape
- ResearchAI
- ResearchStatistics
- ResearchContacts
- ResearchArticles
- Appendix
- List of Figures [Total: 24]
- List of Tables [Total: 409 ]
Partner with Ketan Rohom to Unlock Comprehensive Market Intelligence
For an in-depth exploration of fuselage skin materials, manufacturing technologies, and market dynamics-supported by proprietary data, expert interviews, and comprehensive supply chain mapping-contact Ketan Rohom, Associate Director, Sales & Marketing. Leverage his expertise to tailor this research to your strategic initiatives and secure a competitive edge in the evolving aerospace landscape.
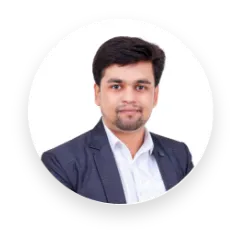
- When do I get the report?
- In what format does this report get delivered to me?
- How long has 360iResearch been around?
- What if I have a question about your reports?
- Can I share this report with my team?
- Can I use your research in my presentation?