Introduction to Aliphatic Polyketone: Innovative Polymer with Exceptional Properties
Aliphatic polyketone stands at the forefront of high-performance polymers, combining exceptional chemical resistance, mechanical strength, and thermal stability in a sustainable package. Its molecular backbone alternates carbonyl and methylene units, delivering a unique balance of toughness and processability. As manufacturers and product designers strive to meet stringent regulatory requirements and evolving consumer expectations, aliphatic polyketone emerges as a compelling alternative to conventional thermoplastics and engineering resins.
This introduction outlines the polymer’s key attributes: resistance to acids and solvents ensures durability in harsh chemical environments; tensile and flexural strength enable load-bearing applications; high thermal resistance expands its use across elevated temperature processes. Moreover, the polymer’s straightforward synthesis and recyclability align with global sustainability initiatives, reducing environmental footprints without sacrificing performance.
Interest in aliphatic polyketone extends across diverse sectors. Automotive engineers integrate it into fuel system components and engine parts to reduce weight while improving corrosion resistance. Electrical and electronics specialists deploy it for connectors and circuit protection in demanding thermal cycles. Industrial fabricators adopt it for tubing and protective components, benefiting from its robustness under mechanical stress. This introductory overview sets the stage for deeper exploration of market dynamics, regulatory influences, and strategic imperatives shaping the future of aliphatic polyketone.
Transformative Shifts Reshaping the Aliphatic Polyketone Landscape
The aliphatic polyketone landscape is undergoing transformative shifts driven by sustainability mandates, advanced processing technologies, and cross-industry collaboration. First, the push toward a circular economy has elevated interest in polymers that combine high performance with recyclability; as a result, chemical recycling initiatives and closed-loop supply chains have gained momentum. Second, process innovations such as gas-assist injection molding and micro-injection molding enable intricate geometries and finer tolerances, broadening application horizons in sectors like medical devices and telecommunications.
Simultaneously, stricter emissions regulations in automotive and industrial markets have accelerated substitution of traditional materials with low-emission alternatives; suppliers are responding by developing formulations that lower volatile organic compound outputs during processing. Digital transformation in manufacturing-through additive manufacturing and Industry 4.0 analytics-provides real-time insights into quality control, minimizing waste and enhancing yield rates of aliphatic polyketone products. Collaboration between polymer scientists and OEMs fosters hybrid blends and reinforced grades optimized for specific applications, reinforcing the material’s versatility.
These combined forces are reshaping supply chains, prompting companies to invest in localized polymer production and downstream compounding facilities. As these transformative shifts unfold, stakeholders must adapt strategies to capitalize on a rapidly evolving market environment.
Assessing the Cumulative Impact of United States Tariffs in 2025 on Aliphatic Polyketone
In 2025, new United States tariff measures have introduced significant headwinds for aliphatic polyketone importers, altering cost structures across the value chain. Raw polymer sourced from international manufacturers now carries additional duties that can exceed standard import fees, compelling downstream converters to reassess sourcing strategies. To mitigate margin erosion, many companies are exploring near-shoring options, establishing compounding and extrusion facilities within tariff-exempt zones or leveraging Free Trade Agreements.
The cumulative effect of these tariffs extends beyond direct cost increases. Importers face longer lead times as alternative supply routes are evaluated, while inventory management becomes more complex due to batch variability and customs clearances. Conversely, domestic polymer producers benefit from enhanced price competitiveness, creating opportunities for strategic partnerships with OEMs seeking to stabilize supply and control costs.
Trade policy uncertainty also influences investment decisions in processing equipment; firms are prioritizing modular systems capable of handling both imported and locally produced polyketone. In this environment, transparency in total landed cost and proactive engagement with customs authorities prove critical to maintaining production continuity and safeguarding profit margins.
Key Segmentation Insights for Aliphatic Polyketone Market Analysis
A nuanced understanding of market segmentation reveals the varied demand drivers and growth pockets within the aliphatic polyketone industry. When examined by application, automotive sectors consume significant volumes for engine components, exterior trim, and interior fixtures, while consumer goods manufacturers integrate polyketone into household appliances and sports equipment for its durability and lightweight properties. Electrical and electronics markets rely on this polymer for circuit protection elements, connectors, and switches that withstand thermal cycling, whereas industrial fabricators employ it in pipes, tubes, and protective components subject to chemical exposure.
Evaluating end-user industries underscores additional distinctions: aftermarket and OEM automotive divisions demand tailored polyketone grades for parts replacement and original assembly, building and construction segments require formulations suited to commercial or residential projects, medical applications emphasize biocompatible and sterilizable variants for devices and surgical instruments, and telecommunications deploy fiber optic components and device housings that resist environmental stresses.
Product type segmentation further refines the landscape into copolymer aliphatic polyketone blends and hybrid polymers, modified grades with or without reinforcements for enhanced stiffness, and pure high-density or low-density resins catering to rigidity or flexibility requirements. Varied manufacturing processes-from extrusion blow molding and injection stretch blow molding to film and sheet extrusion, gas-assist injection, and micro-injection molding-enable precision shaping across complex part geometries. Finally, grade type distinctions between engineering, specialty, and standard categories, as well as property-based classification into acid-resistant, solvent-resistant, flexural-strength, tensile-strength, and high or medium thermal resistance variants, illuminate the material’s adaptability to exacting specifications.
This comprehensive research report categorizes the Aliphatic Polyketone market into clearly defined segments, providing a detailed analysis of emerging trends and precise revenue forecasts to support strategic decision-making.
- Application
- End-User Industry
- Product Type
- Manufacturing Process
- Grade Type
- Properties
Key Regional Dynamics Influencing Aliphatic Polyketone Adoption Worldwide
Regional dynamics play a pivotal role in shaping the adoption and supply of aliphatic polyketone. In the Americas, the drive toward lightweighting in automotive and rigorous chemical regulations in industrial manufacturing have fueled demand for high-performance polymers, supported by robust infrastructure for extrusion and molding. Trade policy shifts have prompted investment in domestic compounding capacities, reducing reliance on imports and enhancing supply chain resilience.
Europe, Middle East & Africa exhibit strong momentum in sustainable engineering, with stringent emissions standards accelerating the use of recyclable polymers. Regional initiatives promoting circular economy principles encourage collaboration between resin producers and recyclers, while local content requirements in the Middle East drive the establishment of new production facilities. Meanwhile, manufacturers in Africa are exploring niche applications in telecommunications and consumer goods, leveraging cost-effective molding processes.
Asia-Pacific remains a hotbed for manufacturing innovation, spurred by expanding automotive assembly lines, rising consumer electronics demand, and ongoing infrastructure projects. Polymer producers are optimizing production networks to serve high-growth markets in China, India, Japan, and Southeast Asia. Government incentives for advanced materials and research partnerships with universities further strengthen the region’s position as a leading hub for aliphatic polyketone development.
This comprehensive research report examines key regions that drive the evolution of the Aliphatic Polyketone market, offering deep insights into regional trends, growth factors, and industry developments that are influencing market performance.
- Americas
- Asia-Pacific
- Europe, Middle East & Africa
Competitive Landscape: Leading Players Driving Innovation in Aliphatic Polyketone
The competitive landscape of aliphatic polyketone features a mix of global chemical giants and specialized polymer manufacturers, each driving innovation through distinct strategic levers. Arkema S.A. and BASF Corporation leverage extensive research and development capabilities to introduce engineered grades optimized for mechanical performance and chemical resistance. Bayer AG and DSM Engineering Materials focus on specialized formulations for medical and electronics applications, while DuPont de Nemours, Inc. and EMS-Chemie Holding AG invest in sustainable production routes and closed-loop recycling programs.
Evonik Industries AG and Hyosung Chemical concentrate on high-purity extrusion grades, and Korea Engineering Plastics Co., Ltd. and LG Chem Ltd. expand regional manufacturing footprints to meet rising demand in Asia-Pacific. LyondellBasell Industries and Mitsubishi Chemical Advanced Materials explore hybrid polymer blends to tailor stiffness and impact resistance. RadiciGroup and SABIC Innovative Plastics enhance their portfolios with UV-stabilized and impact-strengthened specialty grades, and Shell Chemicals and Solvay S.A. emphasize feedstock flexibility and energy-efficient processing. Toray Industries, Inc. rounds out the competitive field by integrating advanced compounding technologies and forging strategic alliances to accelerate market penetration.
This comprehensive research report delivers an in-depth overview of the principal market players in the Aliphatic Polyketone market, evaluating their market share, strategic initiatives, and competitive positioning to illuminate the factors shaping the competitive landscape.
- Arkema S.A.
- BASF Corporation
- Bayer AG
- DSM Engineering Materials
- DuPont de Nemours, Inc.
- EMS-Chemie Holding AG
- Evonik Industries AG
- Hyosung Chemical
- Korea Engineering Plastics Co., Ltd.
- LG Chem Ltd.
- LyondellBasell Industries
- Mitsubishi Chemical Advanced Materials
- RadiciGroup
- SABIC Innovative Plastics
- Shell Chemicals
- Solvay S.A.
- Toray Industries, Inc.
Actionable Recommendations for Industry Leaders in Aliphatic Polyketone
To secure a competitive edge, industry leaders should prioritize investment in advanced manufacturing and processing technologies that enhance yield and minimize waste. Establishing modular production lines capable of dual feedstock handling will buffer against tariff fluctuations and supply disruptions. Strategic collaborations with research institutions can accelerate development of hybrid polymers and reinforced grades tailored to high-value applications in medical, electronics, and automotive sectors.
Furthermore, companies must deepen engagement with policymakers and trade authorities to maintain clarity on tariff classifications and explore tariff-exempt production zones. Expanding recycling initiatives and chemical recovery programs will strengthen sustainability credentials and align with global circular economy goals. Finally, differentiating through value-added services-such as design support, custom compounding, and rapid prototyping-will foster stronger OEM partnerships and unlock new revenue streams beyond commodity resin sales.
Explore AI-driven insights for the Aliphatic Polyketone market with ResearchAI on our online platform, providing deeper, data-backed market analysis.
Ask ResearchAI anything
World's First Innovative Al for Market Research
Conclusion: Strategic Considerations for Stakeholders in Aliphatic Polyketone Market
Aliphatic polyketone is poised to redefine performance polymer benchmarks, with its combination of chemical, mechanical, and thermal properties addressing critical needs across multiple sectors. The convergence of sustainability pressures, regulatory complexities, and process innovations has created a dynamic environment in which strategic agility and technological excellence drive success. By leveraging differentiated grades, optimizing production footprints, and cultivating deep customer relationships, stakeholders can capture emerging opportunities in automotive, electronics, industrial, and medical markets.
As regional dynamics evolve and trade landscapes shift, companies that integrate resiliency into their supply chains while advancing circular economy practices will stand out. The insights presented in this executive summary underscore the importance of segmentation-based product development, regional market focus, and proactive response to tariff challenges. With a clear understanding of these factors, decision-makers can chart a course toward sustained growth and leadership in the aliphatic polyketone domain.
This section provides a structured overview of the report, outlining key chapters and topics covered for easy reference in our Aliphatic Polyketone market comprehensive research report.
- Preface
- Research Methodology
- Executive Summary
- Market Overview
- Market Dynamics
- Market Insights
- Cumulative Impact of United States Tariffs 2025
- Aliphatic Polyketone Market, by Application
- Aliphatic Polyketone Market, by End-User Industry
- Aliphatic Polyketone Market, by Product Type
- Aliphatic Polyketone Market, by Manufacturing Process
- Aliphatic Polyketone Market, by Grade Type
- Aliphatic Polyketone Market, by Properties
- Americas Aliphatic Polyketone Market
- Asia-Pacific Aliphatic Polyketone Market
- Europe, Middle East & Africa Aliphatic Polyketone Market
- Competitive Landscape
- ResearchAI
- ResearchStatistics
- ResearchContacts
- ResearchArticles
- Appendix
- List of Figures [Total: 28]
- List of Tables [Total: 1077 ]
Connect with Ketan Rohom to Acquire Comprehensive Aliphatic Polyketone Market Research Report
For a comprehensive deep dive into market dynamics, segmentation nuances, and competitive strategies, connect with Ketan Rohom, Associate Director, Sales & Marketing. He can guide you through the full research report, offering tailored insights to inform your strategic decisions and drive business growth.
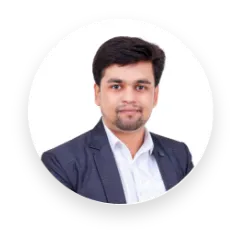
- When do I get the report?
- In what format does this report get delivered to me?
- How long has 360iResearch been around?
- What if I have a question about your reports?
- Can I share this report with my team?
- Can I use your research in my presentation?