Introduction to Alumina Material-Based Wafer Vacuum Chuck Market Dynamics
In the realm of precision wafer handling, vacuum chucks fabricated from alumina materials have emerged as critical enablers of high-throughput microfabrication processes. Leveraging the inherent properties of alumina-exceptional thermal stability, electrical insulation, and chemical inertness-manufacturers across microelectronics, semiconductor fabrication, and solar cell production rely on these chucks to secure wafers with micron-level accuracy. As wafer geometries evolve toward larger diameters and thinner profiles, the demand for highly reliable, dimensionally stable chucking solutions has intensified. In parallel, advances in material science have introduced composite formulations and high-purity alumina variants that push the limits of temperature tolerance and surface flatness. Coupled with modern deposition, etching, and polishing techniques, these developments are redefining equipment capabilities and production yield.
Strategic adoption of custom and standard design variants allows fabricators to address unique process requirements while maintaining cost efficiencies. With the semiconductor and renewable energy sectors poised for sustained expansion, a comprehensive understanding of market drivers and constraints becomes essential for stakeholders aiming to capture value at each stage of the wafer fabrication value chain.
This executive summary delves into the dynamic landscape of alumina-based wafer vacuum chucking, highlighting transformative shifts in manufacturing processes, the influence of regulatory measures, nuanced segmentation trends, regional performance differentials, and competitive positioning of leading technology suppliers. By examining these facets, decision-makers can identify strategic opportunities to optimize supply chains, accelerate innovation cycles, and bolster market position in an increasingly competitive arena.
Transformative Shifts Reshaping the Wafer Vacuum Chuck Landscape
Over the past decade, wafer vacuum chuck technology has undergone several transformative shifts, propelled by converging trends in material innovation, process optimization, and digital integration. First, the introduction of novel high-purity alumina formulations has enabled chucks to withstand extreme thermal cycles associated with advanced chemical mechanical polishing and high-temperature etching processes. Concurrently, manufacturing processes such as hot isostatic pressing and spark plasma sintering have matured, delivering microstructural homogeneity and surface flatness previously unattainable with conventional sintering techniques. These materials and process advancements coincide with the push toward larger wafers, where 300 mm and ultra-large 450 mm systems demand vacuum chucks with enhanced rigidity and minimal warp.
Simultaneously, the era of Industry 4.0 has ushered in real-time monitoring, predictive maintenance, and closed-loop control systems that rely on vacuum chuck-integrated sensors to optimize hold-down force and temperature uniformity. This level of integration not only boosts yield in microelectronics and semiconductor manufacturing but also accelerates throughput in solar cell production lines. Moreover, sustainability pressures are driving the adoption of composite alumina materials and energy-efficient sintering approaches, reducing carbon footprints across the supply chain. As these shifts converge, stakeholders must adopt agile strategies to harness cutting-edge materials, embrace digital tools, and respond swiftly to evolving equipment requirements.
Assessing the Cumulative Impact of 2025 US Tariffs on the Market
Since 2025, the imposition of United States tariffs on imported semiconductor equipment and raw materials has exerted a profound influence on the wafer vacuum chuck market, compelling stakeholders to reexamine sourcing strategies and cost structures. The tariffs have elevated import duties on critical alumina components, directly impacting the cost of high-purity and composite alumina feedstocks. In response, original equipment manufacturers and wafer fabrication facilities have accelerated efforts to qualify domestic suppliers, fostering the expansion of local cold pressing, sintering, and grinding capabilities. This shift toward nearshoring has not only mitigated tariff-related cost increases but also streamlined lead times and reduced exposure to international logistics disruptions.
At the same time, the heightened cost of imported vacuum chuck systems has prompted investment in modular designs that allow in-field replacement of chuck inserts, minimizing capital expenditure. In parallel, strategic partnerships between material producers and equipment vendors have emerged to co-develop tariff-resilient supply networks, emphasizing multi-sourcing of alumina grades and collaborative R&D to tailor material properties. Moreover, this realignment has spurred innovation in alternative ceramic materials and composite architectures designed to circumvent tariff constraints without compromising performance. By integrating recycled alumina waste streams and optimizing process yields, the industry is charting a path toward tariff-resistant production models that balance cost efficiency with technical excellence.
Key Segmentation Insights Driving Strategic Market Understanding
In dissecting the wafer vacuum chuck market, material composition serves as a foundational lens, distinguishing composite materials engineered for enhanced toughness, high-purity alumina grades that deliver superior dielectric and thermal performance, and standard alumina variants offering cost-effective stability. Layering on manufacturing processes, the market encompasses hot isostatic pressing, which yields dense microstructures; conventional sintering, which balances performance and cost; and spark plasma sintering, which accelerates densification with fine grain control. Application-specific requirements further segment the landscape: microelectronics leverages vacuum chucks in LED manufacturing and micro-electromechanical systems (MEMS) for precision component placement; semiconductor manufacturing relies on chemical mechanical polishing, etching, and wafer handling processes that demand immaculate surface flatness; and solar cell production utilizes vacuum chucks in both concentrated solar power systems and photovoltaic cell fabrication lines.
From the vantage point of customer types, integrated device manufacturers prioritize tight process integration, research institutes focus on prototyping advanced materials, and wafer fabrication facilities emphasize throughput optimization. Wafer size introduces additional complexity with platforms for 200 mm and 300 mm wafers alongside emerging 450 mm and ultra-large wafer systems requiring distinct chuck geometries. The product spectrum spans fixed vacuum chucks for stationary processing and rotary vacuum chucks for spin-coating and etch applications. End-user industries range from aerospace and defense to automotive sensor fabrication, consumer electronics, medical devices in imaging and surgical instruments, and telecommunications. Finally, design type segmentation underscores the strategic balance between custom solutions engineered for specialized applications and standard configurations that facilitate rapid time-to-market deployment.
This comprehensive research report categorizes the Alumina Materials Wafer Vacuum Chucks market into clearly defined segments, providing a detailed analysis of emerging trends and precise revenue forecasts to support strategic decision-making.
- Material Composition
- Manufacturing Process
- Application
- Customer Type
- Wafer Size
- Product Type
- End-User Industry
- Design Type
Key Regional Insights Highlighting Global Market Variations
Regional dynamics play a pivotal role in shaping the trajectory of alumina-based wafer vacuum chuck development. In the Americas, established semiconductor hubs have invested in domestic supply chain expansion, enabling rapid adoption of high-purity alumina chucks integrated with advanced process control systems. This region’s emphasis on nearshoring has bolstered local manufacturing capabilities for both fixed and rotary vacuum chuck variants, particularly in emerging ultra-large wafer lines. Regulatory incentives and government programs have further catalyzed research collaborations between material producers and wafer fab operators.
Conversely, Europe, Middle East & Africa exhibits a diverse spectrum of maturity levels, with Western Europe leading in precision ceramic fabrication and Eastern Europe emerging as a competitive low-cost production center. The region’s focus on sustainability has driven innovation in composite alumina materials and energy-efficient manufacturing processes. In EMEA, demand from aerospace, defense, and medical device sectors is a key driver, encouraging manufacturers to develop chucks that meet stringent reliability and cleanliness protocols.
Asia-Pacific remains the fastest-growing market, underpinned by robust semiconductor and solar cell manufacturing ecosystems in China, South Korea, Taiwan, and Japan. Regional governments’ supportive industrial policies have accelerated investments in 300 mm and 450 mm wafer fabs, fueling demand for both custom and standard design chucks. The APAC region continues to lead in spark plasma sintering adoption and high-throughput production of high-purity alumina components.
This comprehensive research report examines key regions that drive the evolution of the Alumina Materials Wafer Vacuum Chucks market, offering deep insights into regional trends, growth factors, and industry developments that are influencing market performance.
- Americas
- Asia-Pacific
- Europe, Middle East & Africa
Key Companies Insights Unveiling Competitive Strengths
Competitive positioning in the wafer vacuum chuck arena reflects a blend of established equipment suppliers and specialized ceramic producers. Applied Materials, Inc. leverages its system-level expertise to integrate vacuum chucks seamlessly into chemical mechanical polishing platforms, while Bühler Group focuses on precision ceramic components, including composite and high-purity alumina chucks optimized for thermal stability. Ebara Corporation brings a legacy of vacuum pump technology, enhancing chuck performance through proprietary surface engineering techniques. Heidenhain Corporation differentiates itself through ultraprecise metrology and sensor integration, enabling real-time monitoring of hold-down forces.
Horiba, Ltd. contributes advanced analytical instrumentation that informs process parameter optimization, and KLA Corporation enhances wafer handling solutions through defect inspection and etch end-point control. LAM Research Corporation offers modular vacuum chuck designs for seamless maintenance, whereas Microcontrol Company, Inc. capitalizes on lean manufacturing to deliver cost-competitive fixed and rotary solutions. Micromanipulator Company, Inc. specializes in fine-positioning vacuum chucks for MEMS assembly, and NTI | AG differentiates with bespoke chuck interfaces for 450 mm wafers.
Okamoto Machine Tool Works, Ltd. applies precision grinding expertise to achieve sub-micron flatness, and Tecan Group Ltd. integrates automated handling platforms with vacuum chuck subsystems. Tokyo Electron Limited incorporates high-throughput vacuum chucks into cluster tools, while Versaline, Inc. focuses on customizable chuck geometries and, by leveraging agile manufacturing and close collaboration with end-users, tailors chuck surface patterns to align with next-generation process chemistries.
This comprehensive research report delivers an in-depth overview of the principal market players in the Alumina Materials Wafer Vacuum Chucks market, evaluating their market share, strategic initiatives, and competitive positioning to illuminate the factors shaping the competitive landscape.
- Applied Materials, Inc.
- Bühler Group
- Ebara Corporation
- Heidenhain Corporation
- Horiba, Ltd.
- KLA Corporation
- LAM Research Corporation
- Microcontrol Company, Inc.
- Micromanipulator Company, Inc.
- NTI | AG
- Okamoto Machine Tool Works, Ltd.
- Tecan Group Ltd.
- Tokyo Electron Limited
- Versaline, Inc.
Actionable Recommendations to Drive Competitive Advantage
To capitalize on emerging opportunities and mitigate market uncertainties, industry leaders should prioritize strategic initiatives across materials, processes, and partnerships. First, accelerate the development and qualification of high-purity alumina and composite formulations that withstand extreme thermal and chemical environments, ensuring compatibility with next-generation CMP, etch, and deposition techniques. Simultaneously, invest in advanced sintering processes such as spark plasma sintering and hot isostatic pressing to achieve superior microstructural control and surface flatness.
Second, strengthen supply chain resilience by cultivating domestic partnerships for alumina feedstocks and vacuum chuck fabrication, thereby reducing tariff exposure and logistics lead times. Embrace modular designs that allow rapid in-field maintenance and upgrade paths, extending equipment life cycles and lowering total cost of ownership. Third, integrate digital monitoring and predictive maintenance capabilities directly into chuck assemblies through embedded sensors and IoT connectivity, enabling real-time force and temperature analytics to boost yield and throughput.
Furthermore, target expansion into high-growth regional markets by aligning product portfolios with local wafer size preferences and regulatory frameworks. Collaborate with key OEMs and research institutes to co-develop custom solutions tailored to the unique demands of aerospace, automotive sensor manufacturing, and medical device applications. Finally, foster continuous innovation by dedicating R&D resources to alternative ceramic architectures and sustainable manufacturing practices, positioning the organization at the forefront of this dynamic landscape.
Explore AI-driven insights for the Alumina Materials Wafer Vacuum Chucks market with ResearchAI on our online platform, providing deeper, data-backed market analysis.
Ask ResearchAI anything
World's First Innovative Al for Market Research
Conclusion: Navigating Opportunities in Alumina Wafer Vacuum Chucks
In summary, the wafer vacuum chuck market for alumina materials stands at the intersection of advanced manufacturing, material science breakthroughs, and geopolitical dynamics. Transformative shifts in high-purity ceramic formulations, additive and sintering processes, and digital integration are redefining precision wafer handling across microelectronics, semiconductor fabrication, and solar cell industries. Meanwhile, the repercussions of US tariffs continue to reshape supply chain strategies, driving localization and collaborative innovation. Nuanced segmentation analysis reveals that optimal solutions vary widely based on material composition, manufacturing process, application requirements, wafer size, product design, and end-user industry.
By synthesizing regional and competitive insights, industry stakeholders can identify targeted opportunities to enhance operational efficiency, reduce risk, and secure market leadership. As fabrication nodes continue to shrink and wafer diameters expand, the ability to deliver reliable, high-performance vacuum chuck solutions will remain critical to enabling the next wave of technological advancement. Ultimately, success will hinge on agility, strategic partnerships, and a relentless focus on material and process excellence that anticipates the evolving needs of the global semiconductor and renewable energy sectors.
This section provides a structured overview of the report, outlining key chapters and topics covered for easy reference in our Alumina Materials Wafer Vacuum Chucks market comprehensive research report.
- Preface
- Research Methodology
- Executive Summary
- Market Overview
- Market Dynamics
- Market Insights
- Cumulative Impact of United States Tariffs 2025
- Alumina Materials Wafer Vacuum Chucks Market, by Material Composition
- Alumina Materials Wafer Vacuum Chucks Market, by Manufacturing Process
- Alumina Materials Wafer Vacuum Chucks Market, by Application
- Alumina Materials Wafer Vacuum Chucks Market, by Customer Type
- Alumina Materials Wafer Vacuum Chucks Market, by Wafer Size
- Alumina Materials Wafer Vacuum Chucks Market, by Product Type
- Alumina Materials Wafer Vacuum Chucks Market, by End-User Industry
- Alumina Materials Wafer Vacuum Chucks Market, by Design Type
- Americas Alumina Materials Wafer Vacuum Chucks Market
- Asia-Pacific Alumina Materials Wafer Vacuum Chucks Market
- Europe, Middle East & Africa Alumina Materials Wafer Vacuum Chucks Market
- Competitive Landscape
- ResearchAI
- ResearchStatistics
- ResearchContacts
- ResearchArticles
- Appendix
- List of Figures [Total: 32]
- List of Tables [Total: 634 ]
Next Steps: Engage with Ketan Rohom for Comprehensive Market Research
For a deeper exploration of these trends and to gain access to comprehensive data on alumina-based wafer vacuum chuck markets, please contact Ketan Rohom, Associate Director, Sales & Marketing. Leverage his expertise to secure customized insights that will guide your strategic decision-making. Reach out via email or phone to acquire the full market research report and position your organization for sustained growth and competitive advantage.
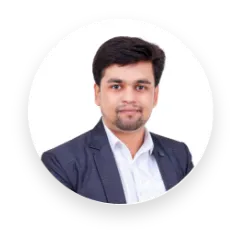
- When do I get the report?
- In what format does this report get delivered to me?
- How long has 360iResearch been around?
- What if I have a question about your reports?
- Can I share this report with my team?
- Can I use your research in my presentation?