Introduction to Alumina Polishing Slurry: Essential Role in Modern Surface Finishing
Alumina polishing slurry underpins precision surface finishing across multiple industries, delivering consistent abrasion control and achieving sub-micron smoothness on critical components. By suspending finely engineered ceramic particles in a tailored medium, this slurry enables manufacturers to meet stringent flatness, roughness, and surface integrity requirements. Its versatility extends from polishing aluminum and stainless steel automotive parts to refining optical lenses and semiconductor wafers. As demand accelerates for higher-performing components in aerospace, electronics, and automotive sectors, alumina slurry emerges as an indispensable enabler of advanced manufacturing processes. Moreover, evolving environmental regulations and end-user expectations have driven formulators to optimize slurry chemistries for enhanced safety and reduced waste. With this context, stakeholders gain insight into the technical underpinnings and market forces shaping the adoption of alumina polishing slurry solutions.
Transformative Shifts: Technological and Market Dynamics Redefining the Landscape
The alumina polishing slurry landscape is experiencing transformative shifts driven by innovations in particle engineering and evolving end-user requirements. Advances in nano- and sub-micron particle synthesis have increased consistency in material removal rates, enabling tighter tolerances for microelectronic wafers and high-precision optical elements. Concurrently, water-based formulations are gaining traction as manufacturers seek to minimize volatile organic compound emissions and comply with stringent environmental guidelines. Digital process monitoring tools now integrate with chemical mechanical planarization equipment to deliver real-time feedback, optimizing slurry consumption and reducing downtime.
End-user industries such as aerospace and defense are adopting specialty slurries to address the corrosion resistance and fatigue life of aluminum components, while the automotive sector is leveraging high-concentration dispersions to polish both aftermarket and original equipment parts more efficiently. In parallel, supply chain resilience has become a focal point: companies are diversifying raw material sources and forging strategic partnerships to mitigate geopolitical risks and tariff volatility. As production scales for consumer electronics and industrial applications, precision surface technology emerges as a complementary technique to traditional chemical mechanical planarization, broadening the scope of achievable surface finishes.
Analyzing the Cumulative Impact of United States Tariffs in 2025 on Industry Dynamics
The enactment of updated United States tariffs in 2025 has exerted notable pressure on both raw material and equipment costs, prompting industry participants to reassess sourcing and production strategies. Import duties on alumina powders and specialty chemical binders have elevated domestic procurement as a cost-containment lever, with some slurry manufacturers establishing local partnerships to secure preferential pricing and reduce lead times. Equipment suppliers have responded by offering bundled service agreements, coupling polishing tools with optimized slurry packages to offset incremental duty expenses.
Additionally, end users have accelerated process optimization initiatives to stretch existing inventories and improve yield per wafer or optical element. Collaborative efforts between material scientists and equipment engineers have yielded formulations with enhanced particle stability, mitigating waste and compensating for higher input costs. While some small-scale formulators face margin compression, larger producers with diversified portfolios are capitalizing on economies of scale. In this environment, agility in adjusting concentration levels and tailoring formulation types proves essential for maintaining competitive positioning and meeting rigorous performance benchmarks.
Key Segmentation Insights: Dissecting Applications, Formulations, and End-User Industries
A granular segmentation framework reveals nuanced demand patterns and performance requirements. Based on application, the market comprises metal polishing encompassing aluminum and stainless steel components, optical component manufacturing dedicated to lens polishing and optical fiber processing, and semiconductor manufacturing including microchip processing and wafer polishing. Formulation preferences split between solvent-based and water-based chemistries, with the latter increasingly favored for environmental compliance and operator safety.
End-user industries further diversify demand profiles: aerospace segments into commercial and defense aircraft, requiring slurries that uphold fatigue resistance and surface integrity; automotive divides into aftermarket and original equipment manufacturers seeking consistent polishing performance at scale; and electrical & electronics branches into consumer and industrial electronics, where dimensional precision and defect minimization are critical. Slurry concentration levels range from low to medium to high, tailoring abrasive loading to throughput and finish quality targets. Material types span aluminium oxide, cerium oxide-including specialized Type A grades-and silicon dioxide, each selected for unique hardness and chemical compatibility attributes.
Particle size distribution influences both material removal rate and surface roughness outcomes, with micro, nano, and sub-micron fractions engineered for specific applications. Technology platforms bifurcate into chemical mechanical planarization and emerging precision surface technologies, offering alternatives in removal mechanisms and edge control. Finally, distribution channels encompass direct sales agreements, regional and global distributors, and digital commerce platforms, ensuring customers’ access to technical support and supply chain flexibility.
This comprehensive research report categorizes the Alumina Polishing Slurry market into clearly defined segments, providing a detailed analysis of emerging trends and precise revenue forecasts to support strategic decision-making.
- Application
- Formulation Type
- End-User Industry
- Concentration Level
- Material Type
- Particle Size
- Technology Used
- Distribution Channel
Regional Insights: Divergent Trends across Americas, EMEA, and Asia-Pacific
Regional dynamics reflect distinct regulatory frameworks, industrial ecosystems, and supply chain configurations. In the Americas, integrated North American production networks benefit from aligned environmental regulations and free-trade arrangements, supporting domestic slurry producers and downstream manufacturers. Latin American markets are emerging as niche consumers of water-based slurry variants for automotive refinishing applications.
The Europe, Middle East & Africa region combines stringent REACH-compliance standards with robust aerospace and defense manufacturing hubs. In this landscape, high-purity aluminium oxide and cerium oxide slurries find application in high-value optical component and wafer fabrication segments. Concurrently, regional distributors and direct sales teams emphasize technical training and local inventory holdings to minimize lead times and uphold performance guarantees.
Asia-Pacific presents a mosaic of mature semiconductor centers in East Asia and rapidly growing electronics assembly corridors in Southeast Asia. Manufacturers in this region prioritize cost-effective, high-throughput slurry formulations while navigating variable import duties and logistic challenges. Partnerships between global slurry suppliers and regional equipment OEMs mitigate tariff exposure and provide tailored solutions for consumer electronics, automotive, and industrial end-markets alike.
This comprehensive research report examines key regions that drive the evolution of the Alumina Polishing Slurry market, offering deep insights into regional trends, growth factors, and industry developments that are influencing market performance.
- Americas
- Asia-Pacific
- Europe, Middle East & Africa
Competitive Landscape: Strategic Profiles of Leading Alumina Polishing Slurry Providers
Leading global suppliers exhibit differentiated strategies to capture share in the alumina polishing slurry market. Air Products and Chemicals, Inc. leverages its gas and chemical portfolio to deliver integrated slurry packages, while Asahi Glass Co., Ltd. emphasizes advanced ceramic coating expertise for next-generation optical applications. BASF SE remains a frontrunner in sustainable formulation development, pioneering water-based dispersions that reduce environmental impact.
Cabot Microelectronics Corporation continues to expand its footprint in semiconductor CMP slurries, deploying localized application labs in major wafer fabrication clusters. CMC Materials KMG Corporation and Dow Chemical Company focus on R&D collaborations to enhance particle stability and throughput efficiency. DuPont Electronics & Imaging and Ebara Corporation offer turnkey polishing systems bundled with proprietary slurries, reducing system integration complexity.
Fujimi Incorporated and Hitachi Chemical Co., Ltd. sustain competitive advantage through specialty cerium oxide variants tailored for bespoke optical finishes. JSR Corporation, NanoMaterials Ltd., and Rodel Holdings Inc. target niche markets by optimizing particle size distributions for sub-micron surface treatments. Saint-Gobain Ceramics & Plastics, Inc. and Versum Materials, Inc. concentrate on strategic partnerships with OEMs to co-develop slurries that meet evolving performance benchmarks across aerospace, automotive, and electronics segments.
This comprehensive research report delivers an in-depth overview of the principal market players in the Alumina Polishing Slurry market, evaluating their market share, strategic initiatives, and competitive positioning to illuminate the factors shaping the competitive landscape.
- Air Products and Chemicals, Inc.
- Asahi Glass Co., Ltd.
- BASF SE
- Cabot Microelectronics Corporation
- CMC Materials KMG Corporation
- Dow Chemical Company
- DuPont Electronics & Imaging
- Ebara Corporation
- Fujimi Incorporated
- Hitachi Chemical Co., Ltd.
- JSR Corporation
- NanoMaterials Ltd.
- Rodel Holdings Inc.
- Saint-Gobain Ceramics & Plastics, Inc.
- Versum Materials, Inc.
Actionable Recommendations for Industry Leaders to Capitalize on Emerging Opportunities
Industry leaders should prioritize continuous innovation in slurry formulation by allocating resources to advanced particle engineering and environmentally compliant chemistries. Establishing cross-functional teams that integrate material scientists with process engineers will streamline the translation of lab-scale breakthroughs into production-ready solutions. To mitigate tariff pressures, companies can diversify raw material sourcing through multi-regional partnerships and consider backward integration for critical powder feedstocks.
Enhancing digital connectivity across supply chains enables real-time inventory management, predictive maintenance scheduling, and process optimization. By deploying smart sensors and data analytics, organizations can reduce excess slurry consumption and prolong polishing pad lifespans. Additionally, tailoring distribution strategies-balancing direct sales, distributor networks, and e-commerce portals-will expand market reach while providing local service support.
Engaging end-users through collaborative pilot programs and application workshops fosters deeper insights into emerging requirements, from ultra-low surface roughness in optical fibers to high throughput in semiconductor fabs. Finally, committing to sustainability goals-such as transitioning to water-based formulations and minimizing process waste-will strengthen brand reputation and ensure compliance with tightening environmental regulations.
Explore AI-driven insights for the Alumina Polishing Slurry market with ResearchAI on our online platform, providing deeper, data-backed market analysis.
Ask ResearchAI anything
World's First Innovative Al for Market Research
Conclusion: Synthesizing Insights for Strategic Decision-Making
Alumina polishing slurry stands at the intersection of advanced manufacturing demands and sustainability imperatives. Strategic investments in particle morphology control, formulation safety, and digital process integration will define the next phase of market leadership. Regional dynamics and tariff environments will continue to shape supply chain decisions and partnerships, whereas targeted collaboration with end users will unlock new application frontiers. By embracing these insights and aligning organizational capabilities, stakeholders can secure competitive advantage and drive long-term resilience.
This section provides a structured overview of the report, outlining key chapters and topics covered for easy reference in our Alumina Polishing Slurry market comprehensive research report.
- Preface
- Research Methodology
- Executive Summary
- Market Overview
- Market Dynamics
- Market Insights
- Cumulative Impact of United States Tariffs 2025
- Alumina Polishing Slurry Market, by Application
- Alumina Polishing Slurry Market, by Formulation Type
- Alumina Polishing Slurry Market, by End-User Industry
- Alumina Polishing Slurry Market, by Concentration Level
- Alumina Polishing Slurry Market, by Material Type
- Alumina Polishing Slurry Market, by Particle Size
- Alumina Polishing Slurry Market, by Technology Used
- Alumina Polishing Slurry Market, by Distribution Channel
- Americas Alumina Polishing Slurry Market
- Asia-Pacific Alumina Polishing Slurry Market
- Europe, Middle East & Africa Alumina Polishing Slurry Market
- Competitive Landscape
- ResearchAI
- ResearchStatistics
- ResearchContacts
- ResearchArticles
- Appendix
- List of Figures [Total: 32]
- List of Tables [Total: 676 ]
Call to Action: Connect with Ketan Rohom to Access the Comprehensive Market Report
To gain comprehensive visibility into market dynamics, segmentation nuances, and competitive strategies for alumina polishing slurry, reach out to Ketan Rohom, Associate Director of Sales & Marketing, to purchase the full research report and inform your strategic roadmap.
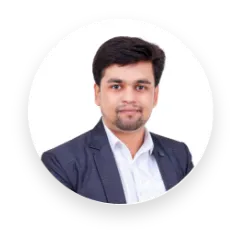
- When do I get the report?
- In what format does this report get delivered to me?
- How long has 360iResearch been around?
- What if I have a question about your reports?
- Can I share this report with my team?
- Can I use your research in my presentation?