Introduction to Alumina Porous Ceramic Vacuum Chucks in Semiconductor Manufacturing
Alumina porous ceramic vacuum chucks have emerged as indispensable tools in the semiconductor wafer-handling process, providing unparalleled precision, thermal stability, and chemical resistance. These specialized chucks, engineered with interconnected pore structures, enable uniform vacuum distribution across the wafer surface, minimizing surface stress and enhancing yield in high-volume manufacturing environments. As wafer diameters grow and device architectures become more complex, the demand for chucks that can maintain tight tolerances under extreme conditions has never been higher.
In recent years, the evolution of semiconductor fabrication-from sub-7nm logic nodes to advanced packaging techniques-has placed new demands on chuck performance. Manufacturers seek materials that withstand rapid thermal cycling in front-end processes, endure corrosive etchants in back-end applications, and maintain vacuum integrity during wafer-level packaging. Porous alumina ceramics address these challenges by combining high porosity-to-strength ratios with excellent electrical insulation and dimensional stability.
Moreover, innovative fabrication methods have broadened the design possibilities for chuck geometries and porosity gradients, enabling custom solutions for consumer electronics, automotive chips, and aerospace sensors alike. With ongoing investment in semiconductor R&D and the push toward near-zero defect processes, alumina porous ceramic chucks stand at the forefront of evolving wafer-handling strategies. This introduction outlines the core value proposition of these advanced materials and sets the stage for a deeper exploration of market dynamics, regulatory shifts, and competitive positioning.
Key Transformative Shifts Redefining the Vacuum Chuck Landscape
Over the past decade, the vacuum chuck landscape has undergone transformative shifts driven by technological, economic, and regulatory forces. First, the rapid integration of additive manufacturing techniques, such as 3D printing, has revolutionized fabrication methods for porous structures. This shift has unlocked complex pore architectures that optimize vacuum flow and thermal management while reducing lead times and material waste.
Simultaneously, semiconductor industry roadmaps have prompted a migration from standard porosity chucks to high-porosity and variable porosity designs with controlled flow rate capabilities. This progression responds to the intensifying requirements of next-generation front-end and back-end processes, where uniform heat dissipation and contamination control are paramount. As a result, device makers now demand chucks that adapt dynamically to process variations and wafer geometries.
In tandem, global supply chain realignments have encouraged manufacturers to diversify raw material sources and forge strategic partnerships across regions. Emerging markets in Asia-Pacific have scaled production capacity, compelling established suppliers in the Americas and EMEA to enhance their value propositions through material innovation and service excellence. Finally, rising sustainability standards have propelled a gradual shift toward energy-efficient sintering methods and recyclable material streams in chuck production.
These converging trends underscore a market in flux, where agility and technological leadership define competitive advantage. The following sections delve into how regulatory changes and market segmentation further shape this dynamic environment.
Cumulative Impact of United States Tariffs 2025 on Ceramic Vacuum Chuck Supply Chains
The imposition of new United States tariffs in 2025 on imported ceramic materials and precision components has reverberated across semiconductor vacuum chuck supply chains. Import duties on high-purity alumina powders and finished chuck assemblies have increased landed costs, prompting equipment manufacturers and end users to reassess their sourcing strategies. Firms previously reliant on cost-effective imports from Asia have begun reallocating orders toward domestic and nearshore suppliers to mitigate duty exposures.
In response, several global chuck producers have accelerated investments in localized manufacturing hubs within North America. These facilities leverage advanced fabrication methods-including pressure assisted sintering and cold isostatic pressing-to circumvent tariffs on imported sintered parts. At the same time, alliances with specialty material providers have expanded, enabling technology transfers that preserve technical performance while optimizing total delivered cost.
On the demand side, semiconductor fabrication centers have adjusted inventory policies, building strategic buffer stocks of both raw alumina feedstock and finished chucks to smooth production planning. Equipment OEMs are renegotiating long-term contracts to share tariff risks, incorporating price adjustment clauses tied to duty rates and currency fluctuations. This collaborative approach has softened the immediate impact on wafer fabrication operations and accelerates joint advocacy for tariff relief through industry associations.
While the new duties present short-term cost pressures, they also catalyze supply chain resilience and foster technology innovation in domestic markets. Companies that proactively adapt sourcing models and deepen partnerships across the value chain will be best positioned to sustain operational continuity and margin integrity in a post-tariff environment.
Key Segmentation Insights Shaping Market Dynamics
A nuanced understanding of market segmentation reveals how diverse product, application, and end-user requirements shape competitive dynamics. Alumina porous ceramic chucks span multiple material types, from composite alumina formulations optimized for thermal conduction to doped alumina grades tailored for electrical insulation, as well as ultra-high-purity and conventionally sintered alumina offerings. These variations address distinct performance metrics across process steps.
Within electronic device manufacturing, chucks serve in consumer electronics assembly and heavy-duty industrial electronics, while research and development laboratories leverage custom porous ceramic samples for process validation. Semiconductor fabrication further segments into front-end processes that demand tight thermal uniformity, back-end processes where chemical resistance is critical, and wafer-level packaging that requires minimal particulate generation.
End-user industry requirements underscore divergent priorities: aerospace and defense programs, including space exploration missions, prioritize extreme temperature resilience; automotive semiconductor fabs focus on high throughput; healthcare and biomedical manufacturers emphasize contamination control; and the broader semiconductor and electronics sector, encompassing display technology, integrated circuit manufacturing, and photovoltaic energy modules, balances cost-effectiveness with precision handling.
Product type differentiation ranges from electrostatic chucks-offered in both Coulomb-type and Johnsen-Rahbek configurations-to magnetic, mechanical vacuum, and negative pressure chucks. Porosity functionality also varies across high, standard, and variable porosity categories, the latter introducing controlled flow rate features that adapt to wafer geometry. Production methods include 3D printed prototypes, CNC machined substrates, cold isostatic pressing techniques, and pressure assisted sintering, each enabling specific porosity and mechanical properties. Usage environments cover corrosive chemical resistance, contaminant resistance, high-temperature operations, and room-temperature applications. Surface topologies extend from patterned and polished finishes to textured surfaces, while attachment mechanisms incorporate alignment guides, clamp-based systems, rotary devices, and traditional vacuum sealing.
This comprehensive research report categorizes the Alumina Porous Ceramic Vacuum Chucks for Semiconductor Wafers market into clearly defined segments, providing a detailed analysis of emerging trends and precise revenue forecasts to support strategic decision-making.
- Material Type
- Application
- End-User Industry
- Product Type
- Functionality
- Fabrication Method
- Usage Environment
- Surface Type
- Attachment Mechanism
Regional Dynamics Driving Market Growth and Adoption
Regional divergence in semiconductor vacuum chuck adoption reflects distinct technological priorities and policy frameworks across the Americas, Europe, Middle East & Africa, and Asia-Pacific. In the Americas, robust domestic fab expansions and government incentives have driven local demand for high-performance chucks, motivating suppliers to invest in state-of-the-art production facilities to meet lead time and customization requirements.
Meanwhile, European and Middle Eastern semiconductor clusters, buoyed by national initiatives, emphasize sustainable manufacturing and stringent environmental regulations. Suppliers serving these markets have adapted by enhancing energy-efficient sintering processes and offering comprehensive lifecycle services. Africa’s nascent semiconductor efforts, though smaller in scale, present early-stage opportunities for research partnerships and proof-of-concept installations.
In contrast, the Asia-Pacific region, led by major fabrication hubs in China, Taiwan, South Korea, and Japan, accounts for the lion’s share of global wafer production. High-volume fabs in this region demand scalable chuck solutions with rapid replenishment cycles and localized technical support. To align with these expectations, chuck manufacturers have established regional R&D centers and joint ventures, accelerating innovation in porosity control and material composition.
Looking ahead, trade policies, infrastructure investments, and cross-border collaborations will continue to redefine regional demand patterns. Suppliers that tailor product portfolios and service models to each region’s regulatory environment and process roadmaps will capture greater market share and strengthen long-term partnerships.
This comprehensive research report examines key regions that drive the evolution of the Alumina Porous Ceramic Vacuum Chucks for Semiconductor Wafers market, offering deep insights into regional trends, growth factors, and industry developments that are influencing market performance.
- Americas
- Asia-Pacific
- Europe, Middle East & Africa
Competitive Landscape: Leading Companies and Strategic Positioning
Competition in the alumina porous ceramic vacuum chuck market is shaped by a blend of global leaders and specialized niche players. BNG Industries has distinguished itself through advanced cold isostatic pressing techniques, while Carborundum Universal Limited leverages its integrated alumina production to offer cost-competitive solutions. CeramTec GmbH and CoorsTek, Inc. focus on high-purity ceramic innovations and modular chuck assemblies.
Ferrotec Corporation and Kyocera Corporation excel in producing electrostatic chuck variants, with Ferrotec emphasizing Johnsen-Rahbek structures and Kyocera achieving scale in Coulomb-type designs. Morgan Advanced Materials plc and Murata Manufacturing Co., Ltd. maintain expansive R&D pipelines, developing novel doped alumina grades and process-specific surface treatments. NGK Insulators, Ltd. and Noritake Co., Limited integrate their core ceramics expertise to tailor chucks for both front-end and wafer-level packaging applications.
Rauschert GmbH and Saint-Gobain S.A. have strengthened their portfolios with negative pressure and mechanical vacuum chucks that address unique attachment challenges. Meanwhile, SCHOTT AG has invested in pressure assisted sintering capabilities that yield high-strength, variable porosity chucks for high-temperature resistant applications. Across this competitive landscape, companies differentiate by enhancing customization options, expanding technical support networks, and pursuing sustainability initiatives to meet evolving industry demands.
This comprehensive research report delivers an in-depth overview of the principal market players in the Alumina Porous Ceramic Vacuum Chucks for Semiconductor Wafers market, evaluating their market share, strategic initiatives, and competitive positioning to illuminate the factors shaping the competitive landscape.
- BNG Industries
- Carborundum Universal Limited
- CeramTec GmbH
- CoorsTek, Inc.
- Ferrotec Corporation
- Kyocera Corporation
- Morgan Advanced Materials plc
- Murata Manufacturing Co., Ltd.
- NGK Insulators, Ltd.
- Noritake Co., Limited
- Rauschert GmbH
- Saint-Gobain S.A.
- SCHOTT AG
Actionable Recommendations for Industry Leaders to Navigate Market Challenges
To secure a leadership position in semiconductor chuck manufacturing, companies should prioritize investments in advanced fabrication techniques such as pressure assisted sintering and 3D printing to achieve tighter porosity control and faster prototyping cycles. Diversifying raw material partnerships will buffer against tariff fluctuations and supply disruptions while enabling access to specialized alumina formulations.
Engaging in joint development agreements with wafer fabs and equipment OEMs can accelerate the co-creation of bespoke chuck solutions optimized for emerging process nodes and packaging formats. Additionally, establishing regional service hubs staffed with application engineers will enhance responsiveness to local manufacturing needs and strengthen customer relationships.
Adopting digital twins and predictive maintenance tools will reduce unplanned downtime and extend chuck lifecycles, translating into tangible cost savings for end users. Finally, integrating sustainability metrics-such as energy consumption per sintering cycle and recyclable ceramic recyclate rates-will align product roadmaps with environmental regulations and corporate responsibility goals, further differentiating offerings in a competitive marketplace.
Explore AI-driven insights for the Alumina Porous Ceramic Vacuum Chucks for Semiconductor Wafers market with ResearchAI on our online platform, providing deeper, data-backed market analysis.
Ask ResearchAI anything
World's First Innovative Al for Market Research
Conclusion: Strategic Imperatives for Future-Proofing Vacuum Chuck Investments
As the semiconductor industry advances toward increasingly complex device architectures, alumina porous ceramic vacuum chucks will remain integral to precision wafer handling. Strategic focus on material innovation, supply chain resilience, and collaborative partnerships will determine which suppliers can meet the evolving needs of semiconductor manufacturers.
By aligning product development with regional policy incentives and tariff landscapes, companies can optimize cost structures and accelerate market penetration. Furthermore, embracing customization-whether through modular chuck platforms or variable porosity designs-will address the unique performance requirements of aerospace, automotive, healthcare, and consumer electronics applications.
Ultimately, the ability to deliver end-to-end service excellence, from rapid prototyping to post-sale technical support, will be the hallmark of sustainable competitive advantage. Firms that balance rigorous R&D investment with operational agility will drive the next wave of innovation in vacuum chuck technology and secure long-term growth.
This section provides a structured overview of the report, outlining key chapters and topics covered for easy reference in our Alumina Porous Ceramic Vacuum Chucks for Semiconductor Wafers market comprehensive research report.
- Preface
- Research Methodology
- Executive Summary
- Market Overview
- Market Dynamics
- Market Insights
- Cumulative Impact of United States Tariffs 2025
- Alumina Porous Ceramic Vacuum Chucks for Semiconductor Wafers Market, by Material Type
- Alumina Porous Ceramic Vacuum Chucks for Semiconductor Wafers Market, by Application
- Alumina Porous Ceramic Vacuum Chucks for Semiconductor Wafers Market, by End-User Industry
- Alumina Porous Ceramic Vacuum Chucks for Semiconductor Wafers Market, by Product Type
- Alumina Porous Ceramic Vacuum Chucks for Semiconductor Wafers Market, by Functionality
- Alumina Porous Ceramic Vacuum Chucks for Semiconductor Wafers Market, by Fabrication Method
- Alumina Porous Ceramic Vacuum Chucks for Semiconductor Wafers Market, by Usage Environment
- Alumina Porous Ceramic Vacuum Chucks for Semiconductor Wafers Market, by Surface Type
- Alumina Porous Ceramic Vacuum Chucks for Semiconductor Wafers Market, by Attachment Mechanism
- Americas Alumina Porous Ceramic Vacuum Chucks for Semiconductor Wafers Market
- Asia-Pacific Alumina Porous Ceramic Vacuum Chucks for Semiconductor Wafers Market
- Europe, Middle East & Africa Alumina Porous Ceramic Vacuum Chucks for Semiconductor Wafers Market
- Competitive Landscape
- ResearchAI
- ResearchStatistics
- ResearchContacts
- ResearchArticles
- Appendix
- List of Figures [Total: 34]
- List of Tables [Total: 729 ]
Take the Next Step: Engage with Ketan Rohom to Access Comprehensive Research
Reach out to Ketan Rohom, Associate Director of Sales & Marketing, to access the full market research report and gain the insights needed to inform strategic decisions and drive process excellence.
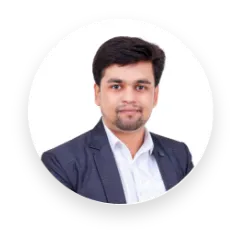
- When do I get the report?
- In what format does this report get delivered to me?
- How long has 360iResearch been around?
- What if I have a question about your reports?
- Can I share this report with my team?
- Can I use your research in my presentation?