Introduction to the Aluminum Alloy Distributed Bracket Market
The aluminum alloy distributed bracket market stands at a pivotal juncture, driven by evolving industrial applications, regulatory dynamics, and technological innovation. As industries seek lightweight, high-strength components for critical structures, these brackets have emerged as indispensable elements in aerospace assemblies, automotive subframes, and advanced building systems. This introduction outlines the core drivers shaping demand, highlights emerging materials and design trends, and frames the broader context in which manufacturers and end users operate.
Recent advancements in alloy formulation and processing techniques have significantly enhanced mechanical performance, corrosion resistance, and manufacturability. Concurrently, sustainability imperatives and lightweighting initiatives are spurring designers to optimize bracket geometry and material selection, accelerating adoption across multiple sectors. From rapid growth in electric vehicle platforms to heightened requirements for modular construction, the market’s trajectory reflects both macroeconomic forces and sector-specific innovations.
Moreover, shifting trade policies and supply chain realignment underscore the importance of agility for producers and purchasers alike. Understanding the interplay of these factors is crucial for stakeholders aiming to capture value and mitigate risk. This executive summary provides a structured overview of key market forces, segmentation insights, regional trends, and strategic imperatives to inform decision-making in this dynamic landscape.
Transformative Shifts in the Aluminum Alloy Distributed Bracket Landscape
The landscape of aluminum alloy distributed brackets has undergone transformative shifts in recent years, reshaping competitive dynamics and value chains. Accelerated digitalization in manufacturing, including additive and automated processes, has enabled more precise bracket geometries and reduced material waste. At the same time, the proliferation of Industry 4.0 solutions has fostered greater transparency and agility across production lines, allowing rapid scale-up and customization to meet exacting specifications.
Concurrently, the push for electrification in automotive and aerospace sectors has elevated thermal management and weight reduction as top priorities, prompting novel alloy series and surface treatments to gain traction. Regulatory standards targeting carbon emissions and energy efficiency have further catalyzed lightweighting strategies, driving engineers to incorporate distributed brackets with optimized load paths and reduced material footprints.
Supply chain resilience has emerged as another critical pivot point. Geopolitical tensions and raw material volatility have led manufacturers to diversify sources, invest in localized processing capabilities, and establish strategic buffer inventories. These adaptive measures, alongside collaborative partnerships spanning raw material suppliers, tier-one integrators, and OEMs, are setting new benchmarks for speed to market and cost containment. Together, these shifts redefine competitive advantage in the aluminum bracket arena.
Assessing the Cumulative Impact of 2025 U.S. Tariffs
The imposition of new United States tariffs in 2025 has compounded existing trade frictions, reshaping supply chains for aluminum alloy distributed brackets. By escalating duties on both primary aluminum and value-added products, these measures have prompted immediate cost implications for imports, catalyzed sourcing diversification, and reignited conversations around domestic production capacity.
Producers reliant on foreign ingots or semi-finished goods have faced upward pressure on raw material costs, leading some fabricators to renegotiate contracts or explore alternative alloy series with more accessible feedstocks. In response, a number of integrated manufacturers have accelerated investments in local smelting and recycling operations, aiming to internalize value and insulate against further tariff escalations.
Meanwhile, end users have adjusted procurement strategies by broadening supplier portfolios and revalidating bracket designs for alternative material specifications. Collaborative product development agreements now emphasize flexibility, enabling rapid substitution between cast and wrought alloys as cost inputs fluctuate. This strategic agility helps maintain production continuity and preserves margin integrity in the face of evolving trade policies.
The cumulative impact of these tariffs will continue to ripple through the value chain, making proactive risk management and strategic sourcing pivotal for competitiveness.
Key Segmentation Insights Across Type, Series, Application, and More
A nuanced view of market segmentation reveals distinct drivers and adoption patterns across multiple dimensions. Based on Type, demand differentiates between cast aluminum alloys, prized for complex shapes and cost efficiency, and wrought aluminum alloys, which offer superior mechanical properties and tighter tolerances. The Alloy Series dimension underscores the significance of Series 1xxx for chemical applications, Series 2xxx for aerospace structures, Series 3xxx for corrosion resistance, Series 4xxx for weldability, Series 5xxx for marine and transportation, Series 6xxx for general structural uses, Series 7xxx for high-strength aerospace fittings, and Series 8xxx for specialty electrical and packaging needs.
Application segmentation further highlights aerospace, where weight constraints drive high-performance alloy uptake; automotive, where lightweight brackets support fuel economy and electrification; building and construction, where structural aesthetics and durability are paramount; consumer products, where miniaturization and design flexibility matter; electrical and electronics, where thermal management is critical; and industrial sectors requiring robustness under heavy loads.
End-Use Industry analysis delineates building and construction into commercial, infrastructure, and residential subsegments; transportation into aerospace, automotive, marine, and rail subcategories; and aerospace further subdivided into commercial aircraft, military aircraft, and spacecraft, while automotive spans commercial vehicles and passenger cars. Manufacturing Process segmentation covers casting, extrusion, forging, and rolling, each influencing bracket geometry, surface finish, and unit cost. Finally, Temper segmentation distinguishes strain-hardened, annealed, thermally treated, and solution heat-treated conditions, which determine mechanical performance and post-processing requirements.
This comprehensive research report categorizes the Aluminum Alloy Distributed Bracket market into clearly defined segments, providing a detailed analysis of emerging trends and precise revenue forecasts to support strategic decision-making.
- Type
- Alloy Series
- Application
- End-Use Industry
- Manufacturing Process
- Temper
Key Regional Insights: Americas, EMEA, and Asia-Pacific Dynamics
Regional dynamics shape growth trajectories and competitive positioning in profound ways. In the Americas, a robust infrastructure pipeline and resurgence of domestic aluminum smelting have bolstered local supply, catering to strong demand from automotive OEMs and aerospace platforms. Trade tensions have incentivized nearshoring, with production clusters emerging in the United States, Canada, and Mexico to minimize exposure to cross-border duties and logistical disruptions.
Across Europe, the Middle East, and Africa, stringent environmental regulations and ambitious carbon reduction targets have spurred investments in low-carbon aluminum production and recycled feedstock. Europe’s well-established aerospace and automotive sectors continue to drive demand for high-strength Series 2xxx and 7xxx brackets, while Middle Eastern construction megaprojects create opportunities for Architecturally focused cast alloys. In Africa, nascent industrialization presents long-term growth potential, especially where value-added extrusion and forging capabilities expand.
In the Asia-Pacific region, rapid urbanization, electrification of transport, and heavy industrial activity underpin sustained bracket consumption. China’s dominance in primary aluminum output continues to influence global pricing, while domestic policy measures aim to balance production intensity with environmental stewardship. Southeast Asia and India are poised to gain share as manufacturing hubs, offering cost competitiveness and strategic access to growing end-use markets.
This comprehensive research report examines key regions that drive the evolution of the Aluminum Alloy Distributed Bracket market, offering deep insights into regional trends, growth factors, and industry developments that are influencing market performance.
- Americas
- Asia-Pacific
- Europe, Middle East & Africa
Key Competitive Landscape: Leading Players and Strategic Positions
The competitive landscape features a diverse array of integrated smelters, recyclers, and fabricators, each pursuing distinct growth strategies. Alcoa Corporation remains a trailblazer in primary aluminum production and advanced casting, while Aleris Corporation focuses on high-performance rolled products for aerospace and defense customers. Aluar Aluminio Argentino S.A.I.C leverages regional resource advantages in South America, whereas AMAG Austria Metall AG emphasizes sustainable extrusion technologies and downstream partnerships.
Arconic Inc. continues to innovate in additive manufacturing and near-net-shape forging, and BALCO (Bharat Aluminium Company Limited) strengthens its position through government-backed expansion of domestic smelting. Century Aluminum Company and China Hongqiao Group Limited prioritize capacity growth to capitalize on global demand swings, while Constellium SE integrates specialized surface treatments for premium applications. ElvalHalcor Hellenic Copper and Aluminium Industry S.A. and Erbslöh Aluminium GmbH differentiate through niche alloys tailored to architectural and industrial sectors.
Hindalco Industries and JW Aluminum focus on sustainability credentials and strategic alliances. Kaiser Aluminum and Norsk Hydro ASA maintain balanced portfolios across extrusion, rolling, and smelting. Novelis Inc. leads in aluminium recycling and high-recycled-content products, PT Timah (Persero) Tbk leverages tin-aluminum synergies, Rio Tinto integrates upstream operations, UACJ Corporation secures Japanese automotive and electronics business, and Vedanta Resources Limited invests in greenfield capacity to meet rising local demand.
This comprehensive research report delivers an in-depth overview of the principal market players in the Aluminum Alloy Distributed Bracket market, evaluating their market share, strategic initiatives, and competitive positioning to illuminate the factors shaping the competitive landscape.
- Alcoa Corporation
- Aleris Corporation
- Aluar Aluminio Argentino S.A.I.C
- AMAG Austria Metall AG
- Arconic Inc.
- BALCO (Bharat Aluminium Company Limited)
- Century Aluminum Company
- China Hongqiao Group Limited
- Constellium SE
- ElvalHalcor Hellenic Copper and Aluminium Industry S.A.
- Erbslöh Aluminium GmbH
- Hindalco Industries
- JW Aluminum
- Kaiser Aluminum
- Norsk Hydro ASA
- Novelis Inc.
- PT Timah (Persero) Tbk
- Rio Tinto
- UACJ Corporation
- Vedanta Resources Limited
Actionable Recommendations for Industry Leaders
Industry leaders must adopt forward-looking strategies to navigate evolving market conditions. First, diversify raw material sourcing by establishing qualified supplier networks across geographies and alloy series, ensuring supply continuity and cost optimization. Second, invest in advanced manufacturing technologies, such as high-precision extrusion and additive processes, to deliver differentiated bracket designs with tighter tolerances and reduced lead times. Third, prioritize sustainability by increasing recycled aluminum content, pursuing certified low-carbon production, and transparently reporting environmental metrics to meet tightening regulatory standards and customer expectations.
Additionally, foster collaborative R&D partnerships with end users to co-develop alloys and bracket architectures tailored to specific load cases, thermal management requirements, and weight targets. Embrace digital transformation across the value chain by integrating real-time quality monitoring, predictive maintenance, and blockchain-enabled traceability to enhance transparency and operational resilience. Finally, cultivate talent and skills through targeted training programs in materials science, additive manufacturing, and compliance management to maintain competitive advantage amid technological and regulatory shifts.
Explore AI-driven insights for the Aluminum Alloy Distributed Bracket market with ResearchAI on our online platform, providing deeper, data-backed market analysis.
Ask ResearchAI anything
World's First Innovative Al for Market Research
Conclusion: Navigating the Future of Aluminum Alloy Distributed Brackets
The aluminum alloy distributed bracket market is poised for sustained expansion, fueled by sectoral electrification, regulatory momentum toward carbon reduction, and ongoing supply chain realignment. Stakeholders that proactively adapt through technological innovation, diversified sourcing, and sustainability leadership will capture disproportionate value. Conversely, firms that rely on legacy processes or centralized supply networks risk margin erosion and market share loss.
Rigorous attention to segmentation nuances-whether optimizing bracket properties by series and temper or aligning capacity with regional demand dynamics-will differentiate winners from laggards. As trade policies shift and raw material costs fluctuate, agile procurement frameworks and strategic inventory buffers become vital. Moreover, forging deep customer partnerships to co-innovate brackets for next-generation platforms will reinforce long-term supplier relationships and create barriers to entry.
Ultimately, the market’s trajectory hinges on the ability of industry participants to balance cost competitiveness with quality, sustainability, and speed to market. By embracing a holistic, data-driven approach, companies can thrive amid uncertainty and secure leadership in this critical segment of the lightweight materials ecosystem.
This section provides a structured overview of the report, outlining key chapters and topics covered for easy reference in our Aluminum Alloy Distributed Bracket market comprehensive research report.
- Preface
- Research Methodology
- Executive Summary
- Market Overview
- Market Dynamics
- Market Insights
- Cumulative Impact of United States Tariffs 2025
- Aluminum Alloy Distributed Bracket Market, by Type
- Aluminum Alloy Distributed Bracket Market, by Alloy Series
- Aluminum Alloy Distributed Bracket Market, by Application
- Aluminum Alloy Distributed Bracket Market, by End-Use Industry
- Aluminum Alloy Distributed Bracket Market, by Manufacturing Process
- Aluminum Alloy Distributed Bracket Market, by Temper
- Americas Aluminum Alloy Distributed Bracket Market
- Asia-Pacific Aluminum Alloy Distributed Bracket Market
- Europe, Middle East & Africa Aluminum Alloy Distributed Bracket Market
- Competitive Landscape
- ResearchAI
- ResearchStatistics
- ResearchContacts
- ResearchArticles
- Appendix
- List of Figures [Total: 28]
- List of Tables [Total: 472 ]
Take the Next Step: Secure Your Full Market Research Report
To capitalize on the insights and strategic imperatives outlined, we invite you to secure the comprehensive market research report by contacting Ketan Rohom (Associate Director, Sales & Marketing at 360iResearch). This in-depth analysis offers granular data, actionable forecasts, and tailored recommendations to inform your growth strategy and operational planning. Reach out today to unlock a full suite of intelligence that will empower your organization to lead with confidence in the evolving aluminum alloy distributed bracket market.
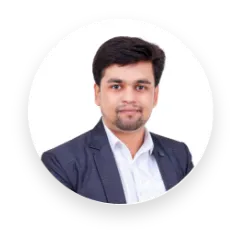
- When do I get the report?
- In what format does this report get delivered to me?
- How long has 360iResearch been around?
- What if I have a question about your reports?
- Can I share this report with my team?
- Can I use your research in my presentation?