Revolutionizing Automotive Performance with Advanced Aluminum Alloys
The automotive industry is undergoing a profound transformation driven by stringent emissions standards, rising demand for fuel efficiency, and the rapid proliferation of electric and hybrid vehicles. As manufacturers strive to reduce vehicle weight without compromising safety or performance, aluminum alloys have emerged as a cornerstone of innovation. Their favorable strength-to-weight ratios, excellent corrosion and fatigue resistance, and adaptability to advanced manufacturing processes position them as indispensable in body structures, chassis systems, engine components, and interior applications. Concurrently, advancements in alloy design-ranging from high-pressure die casting of cast aluminum to heat-treatable and non-heat-treatable grades-are expanding the material’s performance envelope. Furthermore, the push toward sustainability has catalyzed the development of hybrid alloys and recycling programs, underscoring aluminum’s role in a circular economy. In this dynamic environment, stakeholders across the value chain-from alloy producers and automotive OEMs to regulators and Tier 1 suppliers-must navigate evolving technical requirements, shifting trade policies, and regional market dynamics. This executive overview explores the critical shifts reshaping aluminum alloy adoption in automobiles, evaluates the impact of forthcoming U.S. tariffs, delves into segmentation and regional trends, profiles leading participants, and offers targeted recommendations for industry leaders.
Transformative Shifts in the Aluminum Alloy Automotive Landscape
Recent years have witnessed a convergence of technological breakthroughs and market forces that are redefining how aluminum alloys are specified and deployed in automotive applications. Electrification has accelerated the imperative for lightweighting, driving OEMs to replace traditional steel components with high-strength and heat-treatable aluminum grades capable of meeting rigorous safety standards. Simultaneously, digital design tools and simulation platforms enable rapid alloy formulation and virtual testing, reducing development timelines and allowing for optimized geometries in components such as door structures and chassis beams. Additive manufacturing and high-pressure die casting processes are unlocking complex shapes and thin-walled sections, while advanced surface treatments enhance abrasion and corrosion resistance. On the sustainability front, hybrid alloys-blending aluminum with elements like magnesium and silicon-are delivering performance gains while facilitating recycling. Moreover, the integration of the Internet of Things into manufacturing lines is yielding predictive maintenance and real-time quality control, ensuring consistent yield in rolled, extruded, and forged products. As global supply chains evolve, partnerships between alloy suppliers and Tier 1 integrators are intensifying, enabling co-development of tailor-made solutions for electric, luxury, passenger, and commercial vehicle segments. Together, these transformative shifts are charting a new course for the automotive materials landscape.
Cumulative Impact of United States Tariffs 2025 on Automotive Aluminum
In 2025, the cumulative effects of U.S. tariff adjustments on aluminum imports will exert a profound influence on raw material costs, sourcing strategies, and production footprints across the automotive sector. Elevated duties on primary and fabricated aluminum have triggered price volatility, prompting OEMs and suppliers to reassess supply contracts and inventory buffers. In response, domestic smelters and fabricators are scaling capacity, leveraging integrated roasting and casting facilities to capture higher margins. At the same time, some manufacturers are diversifying procurement to Europe, Middle East & Africa and Asia-Pacific hubs where duty structures are more favorable, albeit at the expense of extended logistics lead times. Tariff-induced cost pressures are also intensifying collaboration on alloy optimization to achieve weight targets with reduced material volumes, thereby offsetting unit price escalations. Furthermore, the reshoring of certain value-added processing steps-such as precision machining and extrusions-underscores a strategic pivot toward regional supply chain resilience. As a result, manufacturers that proactively implement hedging mechanisms, strategic partnerships, and localized production models will emerge better positioned to manage the tariff headwinds and maintain competitive cost structures.
Critical Insights Across Aluminum Alloy Market Segments
A granular view of market segmentation reveals the diverse demands placed on aluminum alloys across the automotive ecosystem. When considering alloy grade, cast aluminum variants-including high-pressure die casts-compete with heat-treatable and non-heat-treatable compositions, while high-strength automotive-grade alloys meet structural and crashworthiness requirements. Performance characteristics further dictate material choice: corrosion resistance remains critical for exterior and underbody components, fatigue resistance under cyclic load prolongs service life in suspension and engine parts, and impact plus wear resistance safeguard safety and longevity in high-stress zones. Application areas span body structures with door components as key weight-optimization targets, chassis structures, engine components where thermal and mechanical stability is essential, and interior fittings that balance aesthetics and durability. On the manufacturing front, cast processes such as high-pressure die casting operate alongside extrusion, forging, machining, and rolling techniques to meet varying production volumes and tolerances. Innovation drivers-cost effectiveness, light weighting through the integration of hybrid alloys, and sustainability goals-steer alloy development toward eco-efficient formulations. Finally, vehicle specifications from commercial and passenger to luxury and electric platforms impose unique performance thresholds, underscoring the need for tailored alloy solutions that align with differentiated end-use criteria.
This comprehensive research report categorizes the Aluminum Alloys for Automobiles market into clearly defined segments, providing a detailed analysis of emerging trends and precise revenue forecasts to support strategic decision-making.
- Alloy Grade
- Performance Characteristics
- Application Areas
- Manufacturing Processes
- Innovation Drivers
- Vehicle Specifications
Key Regional Trends in the Aluminum Alloy Automotive Market
Geographic dynamics are shaping the trajectory of aluminum alloy adoption in distinct ways. In the Americas, established automotive hubs are leveraging domestic raw material availability and accelerated investments in recycling infrastructure to mitigate the impact of import tariffs, with electric vehicle manufacturers driving demand for lightweight battery housings and chassis components. Europe, Middle East & Africa face stringent CO₂ reduction mandates, prompting OEMs to integrate advanced aluminum solutions in lightweight body structures and modular platforms, supported by a strong network of smelters and secondary processors. In Asia-Pacific, rapid expansion of passenger and electric vehicle production-particularly in China, Japan, South Korea, and India-has created a competitive environment where manufacturers optimize high-strength alloys in door assemblies, engine brackets, and interior trim, while scaling extruded and rolled products to achieve cost efficiencies. Across these regions, localized partnerships between alloy suppliers and automakers are essential for navigating regulatory frameworks, ensuring consistent quality standards, and delivering on sustainability commitments.
This comprehensive research report examines key regions that drive the evolution of the Aluminum Alloys for Automobiles market, offering deep insights into regional trends, growth factors, and industry developments that are influencing market performance.
- Americas
- Asia-Pacific
- Europe, Middle East & Africa
Competitive Landscape of Leading Aluminum Alloy Manufacturers
The competitive landscape is populated by a range of specialized and diversified alloy suppliers, each contributing unique capabilities. AeroAuto Alloys and Alloy Advance Corp have established leadership in high-strength automotive-grade material formulations, whereas Alloy Dynamics Ltd and Alpha Alloys LLC excel in heat-treatable solutions for structural applications. AlumaCore Industries and AluminaTech Inc focus on developing hybrid alloys that balance light weighting with enhanced fatigue life. Aluminum Dynamics and Apex Alloy Engineering drive innovation in corrosion-resistant and impact-resistant grades, while AutoAlloy Solutions LLC and CarAlloy Industries lead in high-pressure die casting expertise. Dynamic Alloys Inc and EcoLight Metals Inc prioritize sustainable sourcing and closed-loop recycling programs. Elite Alloy Engineering and Fortitude Metals Inc deliver precision extruded and rolled profiles to meet tight tolerances. FusionMetal Technologies and Innovative Alloy Systems are at the forefront of integrating additive manufacturing and advanced machining methods. Meanwhile, Metallurgical Solutions Inc. and MetroAlloy Corporation support custom alloy design with robust R&D platforms. NextGen Alloys Inc. and OmniAluminum Corp leverage Industry 4.0 digital process controls, and Pinnacle Metals Limited alongside Precision Metals Corporation optimize forging and stamping capabilities. ProAlloy Manufacturing and Riveted Alloys Inc serve critical chassis and engine component needs, while Summit Aluminum Alloys and Superior Alloys Group concentrate on abrasion and wear resistance enhancements. Titan Alloys Group and UltraAlloy Technologies specialize in ultra-high-strength grades for crash-relevant parts, and Urban Alloy Solutions together with Vertex Alloys invest heavily in sustainable, lightweight materials to align with net-zero goals.
This comprehensive research report delivers an in-depth overview of the principal market players in the Aluminum Alloys for Automobiles market, evaluating their market share, strategic initiatives, and competitive positioning to illuminate the factors shaping the competitive landscape.
- AeroAuto Alloys
- Alloy Advance Corp
- Alloy Dynamics Ltd
- Alpha Alloys LLC
- AlumaCore Industries
- AluminaTech Inc
- Aluminum Dynamics
- Apex Alloy Engineering
- AutoAlloy Solutions LLC
- CarAlloy Industries
- Dynamic Alloys Inc
- EcoLight Metals Inc
- Elite Alloy Engineering
- Fortitude Metals Inc
- FusionMetal Technologies
- Innovative Alloy Systems
- Metallurgical Solutions Inc.
- MetroAlloy Corporation
- NextGen Alloys Inc.
- OmniAluminum Corp
- Pinnacle Metals Limited
- Precision Metals Corporation
- ProAlloy Manufacturing
- Riveted Alloys Inc
- Summit Aluminum Alloys
- Superior Alloys Group
- Titan Alloys Group
- UltraAlloy Technologies
- Urban Alloy Solutions
- Vertex Alloys
Actionable Strategies for Automotive Industry Leaders
To thrive in a rapidly changing environment, automotive stakeholders should prioritize the following actionable strategies. First, invest in collaborative R&D partnerships to accelerate the development of hybrid and high-strength alloy systems, ensuring alignment with evolving performance and safety standards. Next, diversify supply chains by establishing multi-regional sourcing agreements and nearshoring key processing steps, thereby reducing exposure to tariff volatility and logistics disruptions. Embrace digital manufacturing solutions-such as real-time metallurgical monitoring and AI-driven process optimization-to enhance yield and quality across casting, extruding, forging, machining, and rolling operations. Simultaneously, integrate sustainability metrics into alloy selection and lifecycle assessments to meet regulatory and consumer-driven environmental targets. Engage in joint ventures with recyclers to secure a stable pipeline of secondary aluminum and reinforce circular economy initiatives. Collaborate closely with OEMs to co-design components, leveraging simulation tools that optimize material distribution and minimize waste. Finally, maintain agility by continuously monitoring policy shifts and emerging material science breakthroughs, enabling rapid recalibration of sourcing, production, and product portfolios.
Explore AI-driven insights for the Aluminum Alloys for Automobiles market with ResearchAI on our online platform, providing deeper, data-backed market analysis.
Ask ResearchAI anything
World's First Innovative Al for Market Research
Concluding Perspectives on Aluminum Alloy Advancements
Aluminum alloys have transcended their traditional role to become pivotal enablers of automotive innovation. As regulatory pressures tighten and consumer preferences shift toward sustainable mobility, the demand for optimized material solutions will only intensify. The ability to navigate trade policy dynamics, harness emerging manufacturing technologies, and tailor alloys to specific performance and application requirements will distinguish market leaders. Collaboration across the supply chain-from raw material producers to OEM design teams-will drive efficiencies, foster technical breakthroughs, and unlock new application avenues. By embedding sustainability and digitalization at the core of alloy strategies, stakeholders can future-proof their operations and capture value in an increasingly competitive landscape.
This section provides a structured overview of the report, outlining key chapters and topics covered for easy reference in our Aluminum Alloys for Automobiles market comprehensive research report.
- Preface
- Research Methodology
- Executive Summary
- Market Overview
- Market Dynamics
- Market Insights
- Cumulative Impact of United States Tariffs 2025
- Aluminum Alloys for Automobiles Market, by Alloy Grade
- Aluminum Alloys for Automobiles Market, by Performance Characteristics
- Aluminum Alloys for Automobiles Market, by Application Areas
- Aluminum Alloys for Automobiles Market, by Manufacturing Processes
- Aluminum Alloys for Automobiles Market, by Innovation Drivers
- Aluminum Alloys for Automobiles Market, by Vehicle Specifications
- Americas Aluminum Alloys for Automobiles Market
- Asia-Pacific Aluminum Alloys for Automobiles Market
- Europe, Middle East & Africa Aluminum Alloys for Automobiles Market
- Competitive Landscape
- ResearchAI
- ResearchStatistics
- ResearchContacts
- ResearchArticles
- Appendix
- List of Figures [Total: 28]
- List of Tables [Total: 545 ]
Connect with Ketan Rohom to Access Comprehensive Market Research
Elevate your strategic decision-making by securing the full market research report today. Contact Ketan Rohom, Associate Director, Sales & Marketing, to gain in-depth insights, detailed segmentation analysis, and expert recommendations that will empower your organization to capitalize on aluminum alloy opportunities in the evolving automotive sector.
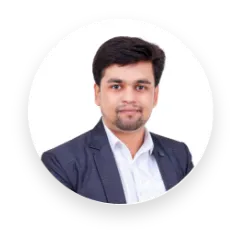
- When do I get the report?
- In what format does this report get delivered to me?
- How long has 360iResearch been around?
- What if I have a question about your reports?
- Can I share this report with my team?
- Can I use your research in my presentation?