Setting the Stage for the Aluminum Extrusion Revolution
During the past decade, aluminum extrusion has emerged as a pivotal manufacturing process across multiple industries. By forcing aluminum billets through precisely engineered dies, extrusion generates profiles with tight tolerances, exceptional strength-to-weight ratios, and outstanding surface finishes. This unique combination of properties has positioned aluminum extrusion as a preferred solution for applications ranging from automotive components and building facades to consumer electronics and machinery parts.
This executive summary distills the key trends, market drivers, and strategic insights shaping the global aluminum extrusion industry. It explores how rapid technological innovation, evolving regulatory landscapes, and shifting supply chain dynamics are influencing stakeholder decisions. Designed to inform C-suite executives, industry analysts, and strategic decision-makers, the report highlights transformative shifts, tariff impacts, segmentation nuances, regional variations, leading company strategies, and actionable recommendations. By synthesizing rigorous primary research, expert interviews, and comprehensive secondary data, this summary offers a concise yet thorough overview to guide investment, expansion, and innovation initiatives.
Redefining the Aluminum Extrusion Arena Through Innovation and Sustainability
The aluminum extrusion landscape is undergoing a profound metamorphosis driven by digitalization, sustainability imperatives, and precision engineering. Advanced process control systems now integrate real-time data analytics and closed-loop feedback, enabling manufacturers to optimize billet temperature, extrusion speed, and die design with unprecedented accuracy. As a result, variability has declined and throughput has increased, creating opportunities for higher-value, custom profiles that address specialized end-use requirements.
Simultaneously, sustainability has shifted from a peripheral concern to a core strategic priority. Companies are investing in recycled aluminum streams and closed-loop scrap management to reduce carbon footprints and comply with stricter environmental regulations. Innovations in alloy development further support lightweighting initiatives, with emerging compositions delivering enhanced fatigue resistance and corrosion protection. Against this backdrop, the convergence of Industry 4.0 capabilities and green manufacturing principles is redefining the competitive frontier, urging industry stakeholders to adopt integrated, agile production models.
Navigating the Ripple Effects of 2025 US Tariff Measures
In 2025, the cumulative effect of layered tariff measures imposed on aluminum imports into the United States has introduced significant cost pressures across the value chain. Tariffs levied on primary and semi-finished aluminum have increased landed costs for extruders reliant on overseas feedstock, prompting many to reevaluate their sourcing strategies. Domestic producers have experienced improved margins but face heightened scrutiny over capacity constraints and raw material availability.
The tariff environment has also triggered ripple effects in downstream sectors. Automotive manufacturers and construction firms are contending with fluctuating input prices, leading to volatile procurement cycles and contractual renegotiations. To mitigate exposure, some extruders have diversified into recycled aluminum and sought strategic partnerships with regional smelters. While these adaptive measures offer partial relief, the uncertain trade policy outlook continues to influence capital investment decisions and long-term capacity planning.
Unpacking Market Dynamics Across Diverse Aluminum Extrusion Segments
A nuanced understanding of market segments is essential for identifying growth pockets within the aluminum extrusion industry. The analysis begins with alloy selection, spanning the high-purity compositions in the 1000 series through copper-reinforced 2000 series, manganese-based 3000 series, silicon-enriched 4000 series, magnesium-alloyed 5000 series, the versatile 6000 series, high-strength zinc alloys in the 7000 series, and specialized miscellaneous alloys in the 8000 series. Each family delivers distinct mechanical, thermal, and surface characteristics suited to specific performance requirements.
Feedstock source further differentiates market behavior, as primary aluminum emphasizes supply security and consistent composition, while recycled aluminum addresses sustainability goals and cost sensitivity. Process variations-cold, hot, and warm extrusion-offer trade-offs between dimensional precision, mechanical strength, and production throughput. The diversity of product shapes, from structural angles, bars, rods, channels, I-beams, rails, T-profiles, tees, tubes, pipes, and Z-profiles, supports an array of end-use configurations.
Enterprise size influences strategic priorities, with large-scale manufacturers leveraging economies of scale and integrated operations, and small and medium enterprises focusing on niche capabilities and rapid customization. Cross-section types range from hollow and semi-hollow to solid, enabling lightweight designs or high structural integrity. Profiles vary in complexity, from custom and large profiles to medium and small stock shapes. End-use applications encompass automotive chassis, frames, drive shafts, heat exchangers, and internal panels; building and construction elements such as curtain walls, railings, fences, structural members, and windows and doors; electrical and electronics components including cable ducts, enclosures, and heat sinks; and machinery and equipment platforms demanding rigorous performance standards.
This comprehensive research report categorizes the Aluminum Extrusion market into clearly defined segments, providing a detailed analysis of emerging trends and precise revenue forecasts to support strategic decision-making.
- Aluminum Type
- Source Type
- Manufacturing Process
- Product Shape
- Enterprise Size
- Cross-Section Type
- Profile Type
- Application
Regional Forces Shaping the Global Aluminum Extrusion Market
Regional trends exert a powerful influence on the global aluminum extrusion market. In the Americas, robust automotive production hubs and steady infrastructure investment fuel demand for both standard and high-performance profiles. Recycling initiatives and renewable energy integration are gaining momentum, encouraging extruders to collaborate with smelters to secure sustainable feedstock streams and achieve circular economy goals.
Europe, the Middle East, and Africa collectively present a complex regulatory mosaic. Stricter emissions targets and green building standards have elevated demand for low-carbon aluminum solutions. Manufacturers in these regions are pioneering advanced extrusion techniques that reduce waste and energy consumption, while forging alliances to strengthen supply chain resilience against geopolitical uncertainties.
Asia-Pacific remains the epicenter of capacity expansion, driven by aggressive infrastructure rollouts, consumer electronics growth, and automotive electrification. High throughput extrusion lines in key manufacturing economies are scaling rapidly, with investments in automation and digital twins enhancing predictive maintenance and quality assurance. As regional players diversify applications and prioritize value-added services, the competitive dynamics continue to evolve at a remarkable pace.
This comprehensive research report examines key regions that drive the evolution of the Aluminum Extrusion market, offering deep insights into regional trends, growth factors, and industry developments that are influencing market performance.
- United Arab Emirates
- Saudi Arabia
- Qatar
- Egypt
- Turkey
- Israel
- Bahrain
- Kuwait
- Oman
Competitive Landscape and Strategic Moves of Leading Extrusion Players
The competitive landscape is characterized by strategic investments, capacity expansions, and technology-driven differentiation. Leading extrusion companies have pursued vertical integration to secure raw material supply and optimize downstream capabilities. Joint ventures and strategic alliances are increasingly common, as players seek to share R&D costs for next-generation alloys and advanced die designs.
Market leaders have differentiated their offerings by integrating Industry 4.0 solutions, enabling remote monitoring, predictive maintenance, and digital quality control. Sustainability credentials have emerged as a key competitive lever, with top firms committing to science-based targets, renewable energy adoption, and closed-loop recycling systems. At the same time, regional champions are capitalizing on local expertise and cost advantages to address specific market niches, forging partnerships with component manufacturers and OEMs to co-develop tailored extrusion profiles.
In this environment, agility and innovation are paramount. Companies investing in flexible manufacturing platforms and advanced analytics are best positioned to respond to evolving customer demands, navigate trade policy fluctuations, and capture emerging opportunities in high-growth end markets.
This comprehensive research report delivers an in-depth overview of the principal market players in the Aluminum Extrusion market, evaluating their market share, strategic initiatives, and competitive positioning to illuminate the factors shaping the competitive landscape.
- ALJAS METAL ASSOCIATES
- Al Salam Aluminium Co. LLC
- Al Taiseer Aluminium Company
- Aluminium and Light Industries Company Limited (ALICO)
- ALUPROF
- ALUPCO
- ALUTECH
- Arabian Extrusions Factory LLC (AREXCO)
- Balexco Bahrain Aluminium Extrusion Company B.S.C.
- Emirates Extrusion Factory LLC
- Gulf Extrusions Co. LLC
- Hussain Aluminium Co. LLC
- Midal Cables B.S.C.
- Modern Aluminium Industries Co. Ltd.
- National Aluminium Products Company SAOG (NAPCO)
- Qatar Aluminium Extrusion Company
- Taiba Aluminium Company
- White Aluminium Enterprises LLC
Strategic Imperatives to Capitalize on Emerging Opportunities in Extrusion
To thrive amid technological upheaval and policy uncertainty, industry leaders should prioritize digital transformation initiatives that streamline process control and enhance real-time decision making. Deploying advanced sensing technologies and analytics platforms will unlock productivity gains, reduce defect rates, and enable rapid customization of complex profiles.
Supply chain resilience demands diversification of feedstock sources, including strategic partnerships for recycled aluminum procurement and near-shoring of billet production. Investing in alloy development and proprietary die technologies will create a sustainable competitive edge, while aligning with increasingly stringent environmental regulations. Collaboration with customers to co-innovate tailored solutions can deepen relationships and drive higher margin opportunities.
Leadership teams must also embed sustainability into core operations, targeting energy efficiency improvements, carbon reduction roadmaps, and circular economy frameworks. By adopting a proactive stance on emissions reporting and resource stewardship, organizations will satisfy stakeholder expectations and secure access to green finance instruments. Finally, continuous talent development and cross-functional knowledge sharing will ensure that the workforce remains equipped to implement strategic initiatives and maintain operational excellence.
Rigorous Approach Underpinning Comprehensive Market Analysis
This analysis is grounded in a rigorous, multi-tiered methodology. Extensive primary research entailed interviews with industry executives, OEM procurement specialists, technology vendors, and trade association representatives to capture first-hand perspectives on evolving market conditions. Secondary research incorporated company reports, regulatory filings, technical papers, and reputable industry publications to validate trends and quantify strategic imperatives.
Data triangulation ensured accuracy by cross-referencing insights from diverse sources, while expert panels provided peer review and methodological validation. Segmentation frameworks were constructed based on aluminum alloy types, source classifications, process variations, product geometries, enterprise scales, cross-section profiles, and end-use applications. Competitive intelligence mapping and supply chain analyses were integrated to reveal strategic positioning and capability gaps.
Qualitative insights were complemented by quantitative trend analysis, tracking historical developments and policy shifts. The final deliverable synthesizes these inputs into actionable findings, ensuring that recommendations are both evidence-based and aligned with stakeholder needs.
Explore AI-driven insights for the Aluminum Extrusion market with ResearchAI on our online platform, providing deeper, data-backed market analysis.
Ask ResearchAI anything
World's First Innovative Al for Market Research
Charting the Future Trajectory of Aluminum Extrusion
The aluminum extrusion industry stands at an inflection point where innovation, regulation, and global trade intersect to shape its future trajectory. Technological advancements in process automation and materials science are unlocking new performance thresholds, while sustainability imperatives are redefining value propositions. Trade policy developments continue to ripple through supply chains, prompting adaptive strategies and diversification efforts.
By examining segmentation dynamics, regional variations, and competitive strategies in tandem, this summary has highlighted the critical drivers and emerging opportunities that will guide investment and operational decisions. The recommendations presented offer a pathway for industry leaders to harness digital tools, strengthen supply chains, and embed sustainability at the core of their business models. As the market evolves, those who combine strategic foresight with agile execution will be best positioned to capture growth and deliver differentiated value.
This section provides a structured overview of the report, outlining key chapters and topics covered for easy reference in our Aluminum Extrusion market comprehensive research report.
- Preface
- Research Methodology
- Executive Summary
- Market Overview
- Market Dynamics
- Market Insights
- Cumulative Impact of United States Tariffs 2025
- Aluminum Extrusion Market, by Aluminum Type
- Aluminum Extrusion Market, by Source Type
- Aluminum Extrusion Market, by Manufacturing Process
- Aluminum Extrusion Market, by Product Shape
- Aluminum Extrusion Market, by Enterprise Size
- Aluminum Extrusion Market, by Cross-Section Type
- Aluminum Extrusion Market, by Profile Type
- Aluminum Extrusion Market, by Application
- United Arab Emirates Aluminum Extrusion Market
- Saudi Arabia Aluminum Extrusion Market
- Qatar Aluminum Extrusion Market
- Egypt Aluminum Extrusion Market
- Turkey Aluminum Extrusion Market
- Israel Aluminum Extrusion Market
- Bahrain Aluminum Extrusion Market
- Kuwait Aluminum Extrusion Market
- Oman Aluminum Extrusion Market
- Competitive Landscape
- ResearchAI
- ResearchStatistics
- ResearchContacts
- ResearchArticles
- Appendix
- List of Figures [Total: 22]
- List of Tables [Total: 161 ]
Secure Your Comprehensive Aluminum Extrusion Market Report Today
Ready to elevate your strategic positioning in the aluminum extrusion market? Reach out to Ketan Rohom (Associate Director, Sales & Marketing) to secure your comprehensive market research report. Gain exclusive insights into emerging trends, tariff implications, and competitive dynamics that will empower your organization to stay ahead of market shifts.
Connect directly to explore customized research packages, receive detailed pricing information, and schedule a one-on-one briefing. Take this opportunity to transform data into action and unlock the full potential of the aluminum extrusion landscape.
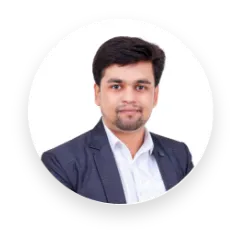
- When do I get the report?
- In what format does this report get delivered to me?
- How long has 360iResearch been around?
- What if I have a question about your reports?
- Can I share this report with my team?
- Can I use your research in my presentation?