Introduction to Aluminum Forgings in Automotive Suspension
The automotive suspension system has undergone a profound transformation in recent years, driven by a relentless pursuit of lighter, stronger, and more durable components. Aluminum forgings have emerged as a cornerstone of this evolution, offering an optimal balance of high strength-to-weight ratio, fatigue resistance, and corrosion performance. As electric and hybrid vehicles gain traction alongside traditional internal combustion platforms, the demand for suspension parts that contribute to overall efficiency and handling precision has never been greater.
Automakers are under increasing regulatory pressure to reduce vehicle mass in order to meet stringent emission targets and enhance battery range in electrified models. At the same time, consumer expectations for ride comfort, safety, and longevity require suspension systems capable of withstanding complex loading cycles over extended service lifetimes. Aluminum forging technology addresses these dual imperatives by enabling the production of intricately shaped control arms, knuckles, torsion bars, and linkages with minimal material waste and superior mechanical properties.
This introduction sets the stage for a comprehensive examination of the aluminum forging market for automotive suspension applications. It highlights the core drivers shaping supplier strategies, outlines the competitive landscape, and provides a foundation for understanding how technological, geopolitical, and regulatory forces are converging to reshape industry dynamics.
Transformative Shifts Reshaping the Aluminum Forging Landscape
Over the past decade, the aluminum forging landscape has been remapped by several transformative shifts. Rapid growth in vehicle electrification has redirected R&D funding toward advanced alloys that can endure higher operating temperatures without sacrificing ductility. In parallel, the rise of digital manufacturing platforms and predictive analytics has optimized forging process parameters, slashing lead times and scrap rates while enabling just-in-time delivery to assembly lines.
Material science breakthroughs have produced high-performance aluminum alloys in the 8000 and 9000 series, which deliver tensile strengths previously achieved only by heavier steel variants. These alloys have unlocked new design possibilities for control arms and subframes, where weight savings translate directly into improved energy efficiency and handling responsiveness. Meanwhile, closed die and counterblow forging methods have become more widely adopted for their ability to generate near-net shapes with tight tolerances, reducing secondary machining operations and overall production costs.
Environmental sustainability has also taken center stage, with manufacturers integrating closed-loop recycling systems and adopting low-carbon smelting techniques to lower the cradle-to-gate footprint of forged components. As a result, supplier networks are evolving to incorporate cross-functional teams of metallurgists, process engineers, and digital specialists who collaborate on continuous improvement initiatives. These converging trends are redefining the competitive frontier, forcing traditional forging houses to embrace agile, data-driven production models or risk ceding ground to more innovative entrants.
Cumulative Impact of United States Tariffs in 2025
The introduction of new tariffs in 2025 targeting specific aluminum products has sent ripples through the automotive forging supply chain. Imposed under national security and trade remedy statutes, these levies have increased landed costs for imported die forgings, particularly those originating from major exporters with previously preferential access. As a direct consequence, domestic forging facilities have experienced heightened demand but must rapidly scale capacity to manage longer lead times and avoid production bottlenecks.
Automotive OEMs have responded by diversifying sourcing strategies, forging partnerships with regional suppliers in North America while renegotiating contracts to include tariff-adjustment clauses. Some international suppliers have shifted final forging and machining steps to tariff-exempt jurisdictions, creating hybrid supply networks that blend cost-efficiency with compliance. Meanwhile, downstream tier-one integrators are adopting dual-sourcing policies to mitigate single-region dependencies and strengthen resilience against future policy shifts.
Though the short-term impact has been an uptick in unit costs for suspension knuckles and control arms, the longer-term effect is a realignment of the forging ecosystem toward near-shoring and higher domestic content. This change incentivizes greater investment in automation, digital quality assurance, and continuous heat-treatment capabilities within local plants. As a result, lead times are gradually stabilizing even as capacity expansions ramp up, setting the stage for a more robust, tariff-resilient network of aluminum forging operations.
Key Segmentation Insights for Forging Methods and Alloy Selection
Analysis of forging methods reveals that closed die forging remains the backbone of suspension component production, prized for its ability to deliver complex geometries with exceptional dimensional accuracy and repeatable mechanical properties. Counterblow forging is gaining traction where near-net shapes and reduced flash generation are paramount, particularly for lightweight knuckles and links that demand both rigidity and impact resistance. Open die forging continues to serve large-scale structural elements and prototypes, offering flexibility in shaping and heat treatment for bespoke applications, while roll forging addresses the need for uniform cross-sectional profiles in shafts and long-link assemblies.
On the alloy front, custom aluminum variants are being tailored to specific suspension performance envelopes, blending elements like magnesium, silicon, and zinc to achieve enhanced fatigue life under cyclic loading. High-performance aluminum alloys in the 8000 series combine elevated strength and conductivity benefits for emerging electric vehicle substructures, and the 9000 series is breaking new ground in ultra-high-strength forgings. Standard aluminum alloys-namely those in the 6000 and 7000 series-remain widely used for their cost-effectiveness, balanced machinability, and proven track record in mid-range vehicle platforms. This multilayered segmentation underscores the importance of aligning forging method and alloy selection with vehicle architecture, regulatory requirements, and production scale.
This comprehensive research report categorizes the Aluminum Forgings for Automotive Suspension market into clearly defined segments, providing a detailed analysis of emerging trends and precise revenue forecasts to support strategic decision-making.
- Type of Forging
- Material Type
Key Regional Dynamics Influencing Supply and Demand
In the Americas, a confluence of government incentives and reshoring initiatives has invigorated forging capacity in the United States and Mexico, turning North America into a hotbed for aluminum forging investment. Vehicle manufacturers are increasingly localizing suspension component production to reduce exposure to currency fluctuations and international logistics disruptions. South America’s forging sector, though smaller in scale, is benefiting from renewed interest in lightweighting as OEMs seek to meet regional fuel-efficiency mandates.
Europe, the Middle East, and Africa are navigating a complex mosaic of sustainability targets and industrial policies. In Western Europe, stringent carbon-emission regulations have accelerated the adoption of low-embodied-energy aluminum, prompting forging houses to retrofit smelters with renewable-energy inputs. Central and Eastern European nations are emerging as competitive hubs for mid-tier forging, offering favorable labor rates and proximity to key automotive clusters. In the Middle East, sovereign-backed industrial parks are laying the groundwork for integrated aluminum-to-forging supply chains, while Africa’s nascent market is primed for growth as infrastructure projects boost demand for lightweight, high-strength components.
Asia-Pacific continues to dominate global aluminum forging volumes, propelled by China’s expansive manufacturing base and aggressive capacity expansion plans. Japan and South Korea remain leaders in high-precision, specialty alloy forgings, supplying premium OEMs worldwide. India is carving out a strategic position through policy-driven incentives and joint ventures that fuse local forging expertise with advanced alloy know-how. Across the region, investments in automation and Industry 4.0 frameworks are elevating process efficiency and product consistency to meet global quality benchmarks.
This comprehensive research report examines key regions that drive the evolution of the Aluminum Forgings for Automotive Suspension market, offering deep insights into regional trends, growth factors, and industry developments that are influencing market performance.
- Americas
- Asia-Pacific
- Europe, Middle East & Africa
Key Company Strategies and Competitive Positioning
AAM has solidified its status through strategic acquisitions and joint-development agreements, leveraging its deep expertise in closed die processes to win long-term suspension contracts with major automakers. Alcoa Corporation has advanced its position by integrating low-carbon aluminum production with specialized forging operations, creating a vertically aligned model that appeals to sustainability-focused OEMs. AMAG Austria Metall AG has distinguished itself by expanding green forging facilities in Europe, tapping renewable energy to power its presses and reduce overall CO₂ intensity.
Arconic Inc. continues to push the envelope in high-speed forging and precision machining, while ATI has broadened its high-performance alloy portfolio to address the stringent mechanical requirements of electric vehicle frames. Bharat Forge Ltd. has capitalized on its cost-competitive manufacturing footprint and forged partnerships with both domestic and international vehicle platforms. Constellium has invested heavily in the research and development of advanced 8000 series alloys, whereas Hitachi Metals, Ltd. has focused on specialty alloy formulations that enhance thermal stability under continuous dynamic loading.
Kaiser Aluminum Corporation has fortified its supply chain resilience by establishing multiple regional forgings, and Kobe Steel, Ltd. has doubled down on R&D to deliver ultra-high-strength forgings for performance vehicles. Metaldyne Performance Group has optimized plant footprints in North America and Europe to reduce lead times, while Nippon Steel Corporation exploits synergies between its steel and aluminum divisions to broaden its forging portfolio. Norsk Hydro ASA has demonstrated leadership in low-carbon aluminum, Precision Castparts Corp. has integrated forging capabilities to create seamless manufacturing flows, and Simpson Strong-Tie Company Inc. has diversified into suspension substructures, expanding its footprint beyond traditional fastening systems.
This comprehensive research report delivers an in-depth overview of the principal market players in the Aluminum Forgings for Automotive Suspension market, evaluating their market share, strategic initiatives, and competitive positioning to illuminate the factors shaping the competitive landscape.
- AAM (American Axle & Manufacturing)
- Alcoa Corporation
- AMAG Austria Metall AG
- Arconic Inc.
- ATI (Allegheny Technologies Incorporated)
- Bharat Forge Ltd.
- Constellium
- Hitachi Metals, Ltd.
- Kaiser Aluminum Corporation
- Kobe Steel, Ltd.
- Metaldyne Performance Group (MPG)
- Nippon Steel Corporation
- Norsk Hydro ASA
- Precision Castparts Corp.
- Simpson Strong-Tie Company Inc.
Actionable Recommendations for Industry Leaders
To maintain leadership in a rapidly evolving forging landscape, industry participants should prioritize several strategic initiatives:
-
Establish comprehensive alloy development partnerships with research institutions and OEMs to accelerate the qualification of next-generation 9000 series alloys, enabling quicker market entry and performance differentiation.
-
Invest in advanced digital twins and real-time process monitoring across forging lines to optimize die design iterations, minimize scrap rates, and ensure consistent mechanical properties in high-volume production.
-
Pursue modular expansion strategies for forging capacity in tariff-compliant regions, balancing near-shore operations with export-oriented plants to maximize market access while mitigating geopolitical risk.
-
Implement circular economy principles through closed-loop recycling of aluminum scrap and adoption of low-carbon smelting technologies, thereby enhancing supplier appeal to sustainability-driven OEM procurement teams.
-
Enhance collaborative platforms that integrate metallurgists, data scientists, and manufacturing engineers to drive cross-functional innovation, reduce time-to-market, and respond swiftly to emerging suspension system requirements.
-
Leverage predictive maintenance and AI-powered quality control to reduce unplanned downtime, extend die life, and optimize maintenance schedules, ensuring high uptime in 24/7 production environments.
By acting on these recommendations, forging suppliers and automakers can create a resilient, agile ecosystem capable of delivering superior aluminum suspension components under evolving market and regulatory pressures.
Explore AI-driven insights for the Aluminum Forgings for Automotive Suspension market with ResearchAI on our online platform, providing deeper, data-backed market analysis.
Ask ResearchAI anything
World's First Innovative Al for Market Research
Conclusion and Strategic Takeaways
In summary, aluminum forgings stand at the intersection of performance, sustainability, and supply chain resilience for modern automotive suspension systems. The industry’s trajectory is defined by a race to develop lighter, stronger alloys and to integrate digital manufacturing tools that drive efficiency and quality. Geopolitical shifts, such as the recent tariff changes, have accelerated the trend toward regional supply networks, while regulatory and consumer pressures on vehicle emissions continue to prioritize lightweight materials.
Segmentation analysis underscores the need to tailor forging methods and alloy choices to specific suspension applications, whether that involves high-precision closed die parts forged from 9000 series alloys or bulk open die components produced in 6000 series materials. Regional insights highlight the dynamic interplay between policy incentives, labor economics, and technological capabilities across the Americas, EMEA, and Asia-Pacific.
Leading companies are differentiating themselves through strategic vertical integration, green manufacturing initiatives, and targeted R&D. As the market continues to evolve, forging suppliers and automakers must collaborate closely to align product roadmaps with emerging vehicle architectures, ensuring the next generation of suspension systems meets both performance and sustainability benchmarks.
This section provides a structured overview of the report, outlining key chapters and topics covered for easy reference in our Aluminum Forgings for Automotive Suspension market comprehensive research report.
- Preface
- Research Methodology
- Executive Summary
- Market Overview
- Market Dynamics
- Market Insights
- Cumulative Impact of United States Tariffs 2025
- Aluminum Forgings for Automotive Suspension Market, by Type of Forging
- Aluminum Forgings for Automotive Suspension Market, by Material Type
- Americas Aluminum Forgings for Automotive Suspension Market
- Asia-Pacific Aluminum Forgings for Automotive Suspension Market
- Europe, Middle East & Africa Aluminum Forgings for Automotive Suspension Market
- Competitive Landscape
- ResearchAI
- ResearchStatistics
- ResearchContacts
- ResearchArticles
- Appendix
- List of Figures [Total: 20]
- List of Tables [Total: 190 ]
Call-to-Action: Engage with Ketan Rohom for Exclusive Market Insights
For a deeper dive into the aluminum forging market, tailored guidance on navigating tariff complexities, and granular insights into alloy development strategies, connect with Ketan Rohom, Associate Director, Sales & Marketing. Whether you need customized segmentation analysis or detailed competitive benchmarking, a market research report will equip you with the intelligence to make informed decisions and secure a competitive edge. Reach out today to unlock the full potential of aluminum for your suspension product portfolio.
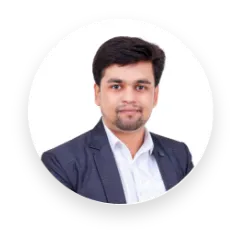
- When do I get the report?
- In what format does this report get delivered to me?
- How long has 360iResearch been around?
- What if I have a question about your reports?
- Can I share this report with my team?
- Can I use your research in my presentation?