The Aluminum Parts Gravity Die Casting Market size was estimated at USD 7.38 billion in 2024 and expected to reach USD 7.90 billion in 2025, at a CAGR 6.72% to reach USD 10.91 billion by 2030.

Setting the Stage for Aluminum Gravity Die Casting Growth
Aluminum parts gravity die casting plays a pivotal role in modern manufacturing ecosystems, offering a blend of dimensional accuracy, high production rates, and cost efficiency. As end markets from automotive to aerospace and medical continue to demand lighter, more complex components, gravity die casting has emerged as a strategic enabler for achieving weight reduction without compromising performance. The interplay of material science advancements and process innovations has propelled this sector to new heights, driving manufacturers to optimize alloy compositions and refine mold designs to unlock previously unattainable shapes and tolerances.
At the heart of this sector’s momentum lies the convergence of sustainability mandates and digital transformation initiatives. Environmental regulations and customer demands are driving a shift toward alloys and processes that reduce waste and energy consumption. Full process modeling and digital twin platforms are enabling foundries to predict casting outcomes with unprecedented accuracy, minimizing trials and speeding product development cycles. As supply chains face growing disruptions, resilience strategies such as localizing production and diversifying raw material sources have become imperative.
This executive summary distills these dynamics into a coherent narrative, guiding stakeholders through the critical themes that will define success in the coming years. By weaving together macroeconomic considerations, policy developments, market segmentation analysis, and strategic company profiles, this document equips executives with the insights needed to make informed investment and operational decisions.
Revolutionary Forces Redefining Casting Operations
Digitalization and Industry 4.0 adoption are redefining gravity die casting operations at an unprecedented pace. Advanced process simulation tools now enable foundries to model metal flow, solidification, and thermal profiles in virtual environments, drastically reducing trial runs and accelerating time to market. Meanwhile, robotics and automated handling systems are streamlining mold loading, pouring, and knock-out processes, increasing throughput while enhancing safety and consistency.
Concurrent with these technological advances, sustainability imperatives are reshaping material choices and energy management strategies. High-efficiency furnaces and closed-loop cooling circuits are cutting carbon footprints, while emergent recycling systems are reclaiming scrap and reducing reliance on primary aluminum. Furthermore, the rise of electric vehicles has shifted design priorities toward thinner wall sections and lighter structural components, spurring alloy development in areas such as Al Si Mg grades with superior strength-to-weight ratios. As global competition intensifies, manufacturers that integrate digital tools with sustainable practices will redefine benchmarks for quality, cost, and environmental stewardship.
Tariff Dynamics Reshaping U.S. Casting Economics
The United States tariff revisions slated for 2025 stand to alter the economics of aluminum parts gravity die casting across multiple dimensions. By imposing additional duties on selected imports, supply chains will face immediate cost pressures, prompting buyers to reassess sourcing strategies. Foundries reliant on imported dies, tooling, or castings may see landed costs rise, driving some to invest in domestic mold production or seek alternate trade lanes. These shifts are likely to accelerate nearshoring initiatives, as manufacturers aim to protect margins and ensure uninterrupted supply.
Beyond direct cost implications, redrawn tariff boundaries could reshape global trade flows. Countries previously advantaged by preferential rates may lose market share in the U.S., while exporters from non-tariffed regions could fill gaps, fostering new partnerships. This reallocation of trade volumes will hinge on logistical agility and the ability to meet stringent quality specifications. As suppliers recalibrate their footprints, consolidation among midsize foundries could intensify, further altering competitive dynamics.
In the long run, these tariff changes may trigger investment in advanced manufacturing hubs within the United States, bolstering local capability for high-precision components used in automotive, aerospace, and industrial machinery. Companies that proactively adapt by diversifying their supplier base, expanding domestic capacity, and leveraging digital procurement platforms will be better positioned to navigate the evolving tariff landscape and capture emerging opportunities.
Deep Dive into Market Segmentation Trends
An examination of product type reveals that cylinder heads and engine blocks continue to command the largest share of aluminum gravity die castings, driven by stringent engine weight reduction goals and thermal performance requirements. Housings and valve bodies are experiencing steady growth as consumer electronics and medical device manufacturers demand intricate geometries with tight tolerances. End use industry patterns indicate that automotive remains the premier application, with commercial vehicles, electric vehicles, and passenger cars each exhibiting unique design and alloy preferences. Aerospace pursues the lightest possible castings, while industrial machinery’s heavy machinery and pumps & compressors sectors rely on robust components, and the medical equipment segment values biocompatibility and precision.
Alloy segmentation underscores the predominance of Al Si grades, specifically A380 and A383, which offer balanced castability and mechanical performance. Al Si Cu variants deliver enhanced thermal stability for high-temperature applications, and Al Si Mg alloys such as A356 and A357 are favored for their superior strength and corrosion resistance in structural parts. Weight categories highlight that components weighing between one and five kilograms form the backbone of the market, while sub-kilogram parts are gaining traction in electronics and medical fields, and heavier castings above five kilograms cater to specialized industrial uses. Sales channel analysis shows original equipment manufacturers leading in large-volume, high-precision contracts, whereas the aftermarket demands flexibility and rapid turnaround to meet diverse replacement and upgrade requirements.
This comprehensive research report categorizes the Aluminum Parts Gravity Die Casting market into clearly defined segments, providing a detailed analysis of emerging trends and precise revenue forecasts to support strategic decision-making.
- Product Type
- End Use Industry
- Alloy
- Weight
- Sales Channel
Regional Market Profiles and Strategic Hotspots
In the Americas, a mature automotive and aerospace casting base is complemented by strong industrial machinery clusters, with foundries increasingly investing in process automation and sustainability measures. The region’s emphasis on regulatory compliance and environmental stewardship drives continuous improvement in alloy selection and energy efficiency.
Europe, Middle East & Africa presents a diverse landscape where established automotive hubs in Germany and France coexist with emerging markets in the Middle East. Stringent emissions and safety regulations are propelling innovation in lightweight casting solutions, and industrial machinery demands remain robust within EMEA’s manufacturing heartlands. In the Asia-Pacific region, rapid growth is fueled by China’s expansive automotive and heavy industry sectors, India’s burgeoning infrastructure investments, and Southeast Asia’s rising consumer electronics output. Japan and South Korea continue to lead in high-precision casting techniques, underscoring the region’s technological prowess.
This comprehensive research report examines key regions that drive the evolution of the Aluminum Parts Gravity Die Casting market, offering deep insights into regional trends, growth factors, and industry developments that are influencing market performance.
- Americas
- Europe, Middle East & Africa
- Asia-Pacific
Leading Players Driving Innovation and Scale
Global leaders are strengthening their positions through capacity expansions, technology partnerships, and targeted R&D investments. Some companies have inaugurated new casting facilities with integrated digital workflow systems, while others are collaborating with universities and research institutes to pioneer novel alloy formulations. Mergers and acquisitions among midsize foundries are streamlining supply chains and enabling scale economies necessary to invest in advanced automation and sustainability initiatives.
Strategic alliances between casting specialists and OEMs are also redefining value delivery. By embedding engineering teams within customer design centers, top players ensure early alignment on part geometries, material specifications, and process parameters. This proactive engagement reduces iteration cycles and fosters long-term relationships, securing a steady flow of high-value orders in sectors such as electric vehicles, aerospace, and precision medical components.
This comprehensive research report delivers an in-depth overview of the principal market players in the Aluminum Parts Gravity Die Casting market, evaluating their market share, strategic initiatives, and competitive positioning to illuminate the factors shaping the competitive landscape.
- Nemak, S.A.B. de C.V.
- Georg Fischer AG
- Barnes Group Inc.
- Constellium SE
- Shiloh Industries, Inc.
- Signicast Investment Corp.
- Delta-Tech Industries, Inc.
- WKK Technology Ltd.
- Mercury Castings, Inc.
- Yizumi Precision Machinery Limited
Strategic Paths for Competitive Advantage
Industry leaders should prioritize the deployment of digital twin platforms to simulate and optimize casting processes, reducing trial costs and accelerating new product introductions. Simultaneously, diversifying alloy portfolios-particularly by expanding offerings in Al Si Mg grades-can address emerging structural and corrosion-resistant requirements across electric vehicles and medical devices.
Furthermore, establishing regional centers of excellence close to key OEM and end-use clusters will mitigate tariff risks and logistical disruptions. Collaborative ventures with raw material suppliers can secure preferential access to recycled aluminum streams, boosting sustainability credentials. Investing in workforce upskilling programs ensures that operators and engineers can harness advanced automation and data analytics tools, cementing competitive advantage in a rapidly evolving marketplace.
Rigorous Framework Underpinning Our Analysis
This analysis integrates a robust research framework combining extensive secondary research with primary interviews and rigorous validation protocols. Initially, comprehensive literature reviews and industry publications informed a foundational understanding of aluminum gravity die casting technologies, market drivers, and regulatory landscapes. Subsequently, in-depth interviews with C-suite executives, plant managers, and materials scientists provided real-world perspectives on operational challenges and strategic priorities.
Data triangulation was conducted through cross-referencing company filings, trade association reports, and customs databases to ensure accuracy and consistency. Findings were subjected to an expert panel review, comprising seasoned engineers and supply chain analysts, to reconcile divergent viewpoints and refine key insights. Throughout the process, quality controls including peer reviews and methodological audits upheld the integrity and reliability of the research outcomes.
Explore AI-driven insights for the Aluminum Parts Gravity Die Casting market with ResearchAI on our online platform, providing deeper, data-backed market analysis.
Ask ResearchAI anything
World's First Innovative Al for Market Research
Converging Insights and Future Outlook
This executive summary has illuminated the multifaceted forces shaping the aluminum parts gravity die casting market, from the transformative impact of digitalization and sustainability mandates to the strategic implications of upcoming tariffs. Detailed segmentation analysis revealed critical trends across product types, end use industries, alloy compositions, weight categories, and sales channels, while regional profiling highlighted the unique dynamics of the Americas, Europe, Middle East & Africa, and Asia-Pacific.
Leading companies are responding with investments in advanced process controls, collaborative engineering models, and supply chain diversification. By aligning strategies with these emerging paradigms, industry stakeholders can capitalize on growth opportunities and mitigate risks. The convergence of technology, policy, and market demand underscores a pivotal moment for gravity die castings; organizations that embrace innovation and resilience will thrive in the evolving competitive landscape.
This section provides a structured overview of the report, outlining key chapters and topics covered for easy reference in our Aluminum Parts Gravity Die Casting market comprehensive research report.
- Preface
- Research Methodology
- Executive Summary
- Market Overview
- Market Dynamics
- Market Insights
- Cumulative Impact of United States Tariffs 2025
- Aluminum Parts Gravity Die Casting Market, by Product Type
- Aluminum Parts Gravity Die Casting Market, by End Use Industry
- Aluminum Parts Gravity Die Casting Market, by Alloy
- Aluminum Parts Gravity Die Casting Market, by Weight
- Aluminum Parts Gravity Die Casting Market, by Sales Channel
- Americas Aluminum Parts Gravity Die Casting Market
- Europe, Middle East & Africa Aluminum Parts Gravity Die Casting Market
- Asia-Pacific Aluminum Parts Gravity Die Casting Market
- Competitive Landscape
- ResearchAI
- ResearchStatistics
- ResearchContacts
- ResearchArticles
- Appendix
- List of Figures [Total: 26]
- List of Tables [Total: 415 ]
Secure Access to Expert Market Intelligence Today
For exclusive access to the full market research report and personalized insights, please contact Ketan Rohom, Associate Director of Sales & Marketing at 360iResearch. Secure your copy today to stay ahead in the dynamic aluminum parts gravity die casting market and empower your organization with actionable intelligence.
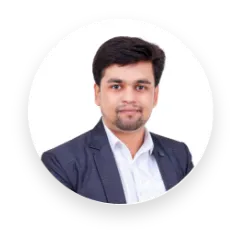
- How big is the Aluminum Parts Gravity Die Casting Market?
- What is the Aluminum Parts Gravity Die Casting Market growth?
- When do I get the report?
- In what format does this report get delivered to me?
- How long has 360iResearch been around?
- What if I have a question about your reports?
- Can I share this report with my team?
- Can I use your research in my presentation?