Introduction: Antistatic Corrosion Resistant Coating Overview
Antistatic corrosion resistant coatings represent the fusion of two critical surface protection strategies: preventing electrostatic discharge and enhancing resistance against corrosive elements. As industries demand materials that safeguard sensitive electronics, structural components, and consumer goods, these coatings have achieved a pivotal role in extending asset lifespans and preserving operational integrity. Innovation in formulation chemistry has enabled multifunctional coatings that not only deflect moisture and chemicals but also dissipate or shield against electrostatic buildup, addressing safety and reliability concerns in high-stakes environments.
The growing emphasis on sustainability, combined with the need for lightweight and high-performance materials, continues to drive research into next-generation antistatic corrosion resistant solutions. Regulatory bodies worldwide are tightening standards around corrosive emissions and electrostatic hazards, compelling manufacturers to adopt coatings that comply with stringent certifications. Stakeholders-from aerospace engineers to medical device designers-are prioritizing surfaces that deliver consistent anti-corrosive protection alongside reliable static control. This introduction establishes the foundational context for understanding why antistatic corrosion resistant coatings are evolving from niche applications into mainstream requirements across multiple sectors.
Transformative Shifts in the Antistatic Coating Landscape
The landscape of antistatic corrosion resistant coatings has undergone transformative shifts propelled by technological breakthroughs and market demands. Advanced formulations incorporating nanomaterials, such as graphene and metal oxides, now deliver superior barrier performance and tunable conductivity. Integration of smart coating technology-where sensors embedded within the coating matrix provide real-time integrity data-has elevated predictive maintenance capabilities, reducing downtime and labor costs.
Simultaneously, sustainability goals are reshaping raw material selection and application processes. Adoption of low-VOC chemistries and waterborne systems has gained traction, minimizing environmental impact without compromising performance. In parallel, global supply chain realignments are responding to geopolitical tensions and evolving trade policies, prompting companies to diversify sourcing and establish regional production hubs.
Market dynamics have also shifted as end-users demand multifunctionality. Manufacturers increasingly blend antistatic efficacy with corrosion protection and thermal stability to meet the strict criteria of sectors like electric mobility and industrial electronics. These transformative shifts underscore a clear trend: multifunctional coatings that balance environmental compliance, cost efficiency, and uncompromised performance are set to define the future of surface protection.
Cumulative Impact of U.S. Tariffs in 2025 on Coating Dynamics
The introduction of new U.S. tariffs in 2025 has generated a cumulative impact on the antistatic corrosion resistant coating market, influencing raw material costs and competitive positioning. Tariffs on imported specialty polymers and metal oxides have increased input expenses for formulators, compelling many to reengineer supply chains or source alternative domestic materials. This recalibration has elevated overall production costs by an estimated mid-single-digit percentage, prompting manufacturers to seek efficiencies in process engineering and scale benefits through consolidated order volumes.
End-users in sectors such as automotive and industrial manufacturing are feeling the ripple effects, with procurement teams renegotiating contracts and exploring local suppliers to offset price volatility. Meanwhile, providers with vertically integrated operations or regional manufacturing footprints have gained a competitive edge, minimizing exposure to cross-border levies. The net result is a more regionally focused landscape, where cost containment strategies and supply chain resilience are paramount. In this context, businesses that proactively adapt to tariff-driven challenges-through diversified sourcing, tariff engineering, or strategic partnerships-will secure long-term stability and market leadership.
Key Segmentation Insights
Understanding the market’s complexity requires a close examination of key segmentation pillars. Based on industry application, coatings tailored for aerospace and defense emphasize extreme environmental resilience, while those for the automotive sector distinguish between electric vehicles and internal combustion vehicles, reflecting divergent requirements for weight, thermal management, and electrical conductivity. Consumer goods demand protective layers that combine aesthetic finish with static dissipation, whereas electronics coatings bifurcate into consumer electronics and industrial electronics to address differences in usage cycles and operating environments. Industrial applications focus on large-scale corrosion mitigation and machinery protection, and the medical segment prioritizes biocompatibility alongside sterilization resistance.
When evaluating product type, customized solutions offer tailored performance specifications, multilayer coatings integrate adhesion promoters and barrier layers for enhanced durability, pre-engineered coatings deliver consistency across batches, and single layer coatings provide streamlined application. Within material composition, ceramic-based and metal-based coatings offer unparalleled hardness and thermal resistance, composite materials strike a balance between flexibility and strength, and polymer-based variants-split into polyurethane and silicone formulations-excel in adaptability and ease of repair.
Assessing performance attributes reveals categories such as abrasion resistance for wear-intensive scenarios, antistatic efficacy subdivided into electrostatic shielding and static dissipative properties, chemical resistance for exposure to aggressive agents, corrosion protection to extend substrate life, and thermal stability for high-temperature operations. Manufacturing processes span chemical vapor deposition, dip coating, electrocoating, physical vapor deposition, and spray coating methods, the latter further delineated into air assisted and airless systems. Certification standards play a critical role, with ASTM benchmarks, ISO compliance, RoHS directives, and UL approvals ensuring reliability and regulatory adherence. Finally, technological innovation showcases advanced formulations, nanotechnology integration, self-healing mechanisms, and smart coating technology, while distribution channels range from dealer networks and direct sales to online platforms and wholesale distribution, each offering distinct advantages in reach and customer engagement.
This comprehensive research report categorizes the Antistatic Corrosion Resistant Coating market into clearly defined segments, providing a detailed analysis of emerging trends and precise revenue forecasts to support strategic decision-making.
- Industry Application
- Product Type
- Material Composition
- Performance Attributes
- Manufacturing Process
- Quality And Certification
- Technological Innovation
- Distribution Channel
Key Regional Insights
Regional dynamics further shape market priorities and competitive strategies. In the Americas, demand is driven by automotive production hubs in North America and industrial refurbishment projects in South America, reinforced by domestic raw material availability that cushions against tariff shocks. Europe, the Middle East & Africa exhibits robust interest in sustainable coating systems, spurred by stringent environmental regulations in the EU and rapid infrastructure growth in the Gulf Cooperation Council countries. Africa’s nascent yet emerging manufacturing sectors are beginning to adopt advanced coatings to support mining and energy applications.
The Asia-Pacific region commands a significant share of production capacity, fueled by large electronics and automotive manufacturing bases in countries such as China, Japan, South Korea, and India. Here, local coating formulators leverage cost-efficient labor and scale economies to compete globally. At the same time, regional governments are incentivizing research into low-emission processes and advanced materials, bolstering innovation clusters in key economic centers. The net effect is a diversified regional landscape where end-users benefit from regional specialization and localized support services, enhancing responsiveness and total cost of ownership.
This comprehensive research report examines key regions that drive the evolution of the Antistatic Corrosion Resistant Coating market, offering deep insights into regional trends, growth factors, and industry developments that are influencing market performance.
- Americas
- Asia-Pacific
- Europe, Middle East & Africa
Key Companies Insights
The competitive landscape features a diverse array of established global players and specialized innovators. 3M Company and AkzoNobel N.V. leverage extensive research and development capabilities to introduce multifunctional systems, while Allnex Global BV and Archline Coatings Ltd. focus on specialty polymers and niche applications. Axalta Coating Systems Ltd. and BASF Corporation offer end-to-end solutions spanning formulation to application equipment, complemented by Benjamin Moore & Co. and Carboline Company, Inc., which maintain strong dealer networks for industrial maintenance markets.
Chemetall GmbH and China Coatings Holdings Ltd. are prominent in surface treatment solutions, whereas Covestro AG, Dow Inc., and DuPont de Nemours, Inc. drive innovation in polymer chemistry. EPR Industries, Inc. and Hempel A/S serve maritime and offshore sectors, and Henkel AG & Co. KGaA and Huntsman Corporation apply adhesives technology to coating systems. Jotun Group and Kansai Paint Co., Ltd. have established leadership in protective coatings for construction and infrastructure, while Masco Corporation, Nippon Paint Holdings Co., Ltd., PPG Industries, Inc., and PPG Protective Coatings maintain broad portfolios across raw material and applicator segments. Royal DSM N.V. and RPM International Inc. specialize in sustainable materials, and Sherwin-Williams Company, SigmaKalon Industries Ltd., Sika AG, Tremco Incorporated, and Valspar Corporation deliver regional focus with local manufacturing and service support.
This comprehensive research report delivers an in-depth overview of the principal market players in the Antistatic Corrosion Resistant Coating market, evaluating their market share, strategic initiatives, and competitive positioning to illuminate the factors shaping the competitive landscape.
- 3M Company
- AkzoNobel N.V.
- Allnex Global BV
- Archline Coatings Ltd.
- Axalta Coating Systems Ltd.
- BASF Corporation
- Benjamin Moore & Co.
- Carboline Company, Inc.
- Chemetall GmbH
- China Coatings Holdings Ltd.
- Covestro AG
- Dow Inc.
- DuPont de Nemours, Inc.
- EPR Industries, Inc.
- Hempel A/S
- Henkel AG & Co. KGaA
- Huntsman Corporation
- Jotun Group
- Kansai Paint Co., Ltd.
- Masco Corporation
- Nippon Paint Holdings Co., Ltd.
- PPG Industries, Inc.
- PPG Protective Coatings
- Royal DSM N.V.
- RPM International Inc.
- Sherwin-Williams Company
- SigmaKalon Industries Ltd.
- Sika AG
- Tremco Incorporated
- Valspar Corporation
Actionable Recommendations for Industry Leaders
To thrive in a shifting market, industry leaders should adopt a proactive, integrated approach:
Focus investment in research on multifunctional formulations that pair antistatic performance with high corrosion resistance, leveraging nanotechnology and smart sensing to differentiate offerings. Enhance supply chain resilience by diversifying raw material sourcing across regions and exploring alternative feedstocks to mitigate tariff impacts. Establish regional production or partnership agreements in key markets to reduce logistics costs and strengthen customer service capabilities. Prioritize sustainability through low-VOC and waterborne systems, achieving ASTM, ISO, RoHS, and UL certifications to meet evolving regulatory expectations and end-user requirements. Implement digital tools such as AI-driven quality control and real-time monitoring to optimize manufacturing processes, reduce waste, and accelerate time to market. Develop specialized training and support programs for applicators and end-users, deepening technical engagement and ensuring proper application practices. Finally, cultivate strategic alliances with equipment providers and end-use industries to co-develop solutions that address specific sector challenges in aerospace, automotive, electronics, and industrial maintenance.
Explore AI-driven insights for the Antistatic Corrosion Resistant Coating market with ResearchAI on our online platform, providing deeper, data-backed market analysis.
Ask ResearchAI anything
World's First Innovative Al for Market Research
Conclusion
Antistatic corrosion resistant coatings are poised to play an indispensable role in safeguarding assets and enhancing safety across diverse industries. The confluence of technological advancements, regulatory drivers, and shifting global trade dynamics has created both challenges and opportunities for coating formulators, applicators, and end-users. By understanding intricate segmentation layers, regional nuances, and the competitive landscape, stakeholders can make informed strategic decisions that balance performance, cost efficiency, and sustainability.
Looking ahead, success will belong to those who integrate smart technologies, optimize supply chains against tariff disruptions, and embrace rigorous quality standards. Collaborative innovation with downstream industries and strategic market alignment will ensure that antistatic corrosion resistant coatings not only meet existing demands but also anticipate future requirements, driving long-term growth and resilience.
This section provides a structured overview of the report, outlining key chapters and topics covered for easy reference in our Antistatic Corrosion Resistant Coating market comprehensive research report.
- Preface
- Research Methodology
- Executive Summary
- Market Overview
- Market Dynamics
- Market Insights
- Cumulative Impact of United States Tariffs 2025
- Antistatic Corrosion Resistant Coating Market, by Industry Application
- Antistatic Corrosion Resistant Coating Market, by Product Type
- Antistatic Corrosion Resistant Coating Market, by Material Composition
- Antistatic Corrosion Resistant Coating Market, by Performance Attributes
- Antistatic Corrosion Resistant Coating Market, by Manufacturing Process
- Antistatic Corrosion Resistant Coating Market, by Quality And Certification
- Antistatic Corrosion Resistant Coating Market, by Technological Innovation
- Antistatic Corrosion Resistant Coating Market, by Distribution Channel
- Americas Antistatic Corrosion Resistant Coating Market
- Asia-Pacific Antistatic Corrosion Resistant Coating Market
- Europe, Middle East & Africa Antistatic Corrosion Resistant Coating Market
- Competitive Landscape
- ResearchAI
- ResearchStatistics
- ResearchContacts
- ResearchArticles
- Appendix
- List of Figures [Total: 32]
- List of Tables [Total: 647 ]
Call-To-Action
Contact Ketan Rohom, Associate Director, Sales & Marketing, to acquire the comprehensive market research report and gain actionable insights that will inform strategic plans and accelerate your leadership in the antistatic corrosion resistant coating arena.
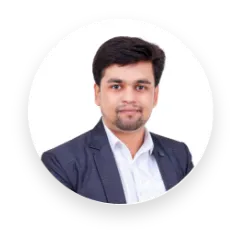
- When do I get the report?
- In what format does this report get delivered to me?
- How long has 360iResearch been around?
- What if I have a question about your reports?
- Can I share this report with my team?
- Can I use your research in my presentation?