Introduction to Articulated Robot Welding Solutions
Articulated robots have revolutionized welding processes by delivering precision, speed, and flexibility that surpass traditional manual or fixed automation methods. As manufacturers strive for higher throughput and consistent quality, these multi-jointed machines adapt seamlessly to complex geometries and high-mix production environments. The melding of advanced motion control, integrated vision systems, and real-time data analytics empowers weld cells to self-optimize, minimizing downtime and reducing scrap rates.
In this dynamic landscape, both established industrial players and emerging innovators leverage robotics to drive operational excellence. Articulated robots integrate with peripheral equipment-such as part feeders, positioners, and safety enclosures-creating cohesive, scalable production lines. This synergy fosters lean manufacturing principles, enabling rapid changeovers and enabling manufacturers to address fluctuating demand without sacrificing quality or cost-effectiveness.
Looking ahead, the convergence of artificial intelligence, adaptive welding algorithms, and collaborative frameworks heralds a new era of autonomous welding cells. Industry leaders that embrace these advancements will unlock productivity gains, enhance workforce safety through human-robot collaboration, and secure a competitive edge in a global marketplace increasingly defined by agility and precision. This introduction sets the stage for a deep dive into the forces reshaping articulated welding robots and the strategies that decision-makers must adopt to thrive.
Navigating Transformative Shifts in Welding Automation Landscape
Over the past decade, automation in welding has undergone transformative shifts driven by the confluence of digitalization and evolving production demands. Initially, robotic welding centered on heavy, six-axis industrial arms executing repetitive bead runs in high-volume assembly lines. Today, we witness a fundamental shift: collaborative robots engineered with power and force limiting algorithms now operate safely alongside human operators, enabling manual guidance and accelerated programming workflows.
Meanwhile, the rise of adaptive welding technologies-such as real-time joint tracking and closed-loop feedback-has elevated process reliability. Machine vision systems equipped with laser profilometry inspect joint geometry on-the-fly, while AI-driven control software dynamically adjusts parameters to maintain optimal penetration and minimize spatter. This fusion of hardware and software intelligence underscores a broader industry trend toward self-optimizing manufacturing cells.
Additionally, the adoption of offline and online programming platforms has streamlined deployment. Engineers can simulate complex gantry or Cartesian robot paths virtually, validating collision-free trajectories before commissioning. When integrated with predictive maintenance algorithms, these platforms leverage sensor data-tracking torque signatures, vibration patterns, and thermal cycles-to forecast component wear and schedule proactive service.
Finally, sustainability considerations are gaining prominence. Manufacturers are optimizing arc efficiency and gas consumption, selecting titanium or advanced alloys only where performance demands justify cost. These combined shifts illustrate a welding automation landscape that is more intelligent, flexible, and resource-efficient than ever before.
Cumulative Impact of United States Tariffs in 2025
The introduction of United States tariffs in 2025 has reshaped global supply chains for articulated welding robots and their components. Following adjustments in import duties on motors, gearboxes, and electronic controllers, many OEMs experienced increased unit costs. These higher tariffs prompted a strategic realignment: some manufacturers pivoted sourcing to tariff-exempt regions, while others negotiated long-term contracts to lock in favorable pricing before duty escalations.
Consequently, assembly facilities located in the Americas reexamined their component mix. Sourcing critical modules domestically or within nearshore markets reduced exposure to import tariffs and shortened lead times, but it also required investments in local supplier development and quality assurance. In parallel, companies with vertically integrated manufacturing capabilities leveraged internal production of robot arms and end effectors to mitigate cost volatility.
On the other hand, certain end-users accepted modest price increases by absorbing tariff surcharges, viewing the tradeoff as necessary to maintain supply continuity and automation schedules. Others deferred capital expenditures, opting for leasing or rental arrangements that spread cost impacts over longer horizons.
Ultimately, the 2025 tariff landscape accelerated diversification in both supplier networks and business models. Organizations that proactively restructured procurement strategies emerged more resilient, while those that hesitated faced longer lead times and higher landed costs, underscoring the critical need for agile supply chain planning in a geopolitically complex environment.
Key Insights from Market Segmentation
A granular examination of market segmentation reveals nuanced adoption patterns across the welding robot ecosystem. When analyzed by type, Cartesian configurations excel in high-precision, small-parts welding applications, while collaborative robots offering safety-rated monitored stops and speed-and-separation monitoring features thrive in mixed-model production lines. Gantry systems underpin large-scale fabrications, particularly in automotive body shops, whereas six-axis industrial robots continue to dominate arc and spot welding tasks that require intricate joint accessibility.
Payload capacity serves as a critical discriminator. Heavy payload solutions exceeding 50 kilograms support multi-torch setups for structural assembly, whereas light payload robots under 5 kilograms enable fine laser or seam welding on delicate components. Medium-capacity robots balance flexibility and reach for general-purpose applications, allowing integrators to optimize throughput without significant infrastructure overhaul.
End-user industry segmentation further underscores differentiated requirements. In aerospace, articulated robots facilitate aircraft body assembly and jet engine manufacturing with strict process traceability and material handling precision. The automotive sector leverages welding automation across assembly, body shop, and paint shop environments to achieve consistent weld quality at high volumes. Electronics manufacturers employ compact welding cells for battery packs and delicate housings, prioritizing repeatability and minimal heat input.
Application-driven segmentation highlights specialized process capabilities. Arc welding applications, including gas metal arc welding (GMAW) and gas tungsten arc welding (GTAW), remain staples for structural joins, while laser and spot welding gain traction for thin-gauge materials. Seam welding finds use in seal-critical industries such as HVAC and appliance manufacturing.
From a component perspective, robust controllers with intuitive human-machine interfaces underpin flexible cell configurations; end effectors range from grippers to specialized welding torches; sensors monitor arc stability and seam deviation; and robot arms with optimized kinematics deliver the precision demanded by advanced alloys. Offline programming software accelerates engineering setup, whereas online programming platforms allow in-process adjustments. Material-focused segmentation distinguishes between steel, aluminum, titanium, and emerging advanced alloys, each necessitating tailored heat input control and gas shielding strategies. Functionality offers fully automated systems alongside semi-automated or manual-override options for niche applications. Diverse business models, including leasing, purchase, and rental, cater to budget constraints and project timelines, while maintenance strategies-corrective, predictive, and preventive-determine total cost of ownership and uptime metrics.
This comprehensive research report categorizes the Articulated Robot for Welding market into clearly defined segments, providing a detailed analysis of emerging trends and precise revenue forecasts to support strategic decision-making.
- Type
- Payload Capacity
- End-User Industry
- Application
- Component
- Technology
- Material Type To Be Welded
- Functionality
- Business Model
- Maintenance
Regional Insights Shaping the Welding Robot Market
Regional dynamics play a pivotal role in the adoption and evolution of articulated welding robots. In the Americas, proximity to major automotive and aerospace manufacturers drives demand for both turnkey robotic cells and retrofitting solutions. This region emphasizes reshoring initiatives, with local integrators capitalizing on tariff-induced supply chain realignment to strengthen domestic manufacturing capabilities.
Across Europe, the Middle East & Africa, regulatory frameworks and environmental standards push manufacturers toward energy-efficient welding processes. Collaborative deployments have gained traction in EMEA, supported by government incentives for digital transformation and workforce upskilling. Concurrently, a growing network of specialist system integrators in the Middle East targets oil and gas applications, while Africa’s nascent automotive and electronics sectors adopt entry-level robot packages to establish pilot automation lines.
In Asia-Pacific, a diversified landscape reflects the breadth of end-user industries. Mature markets such as Japan and South Korea pioneer advanced robotics technologies, investing heavily in compact, high-speed laser welding cells for electronics assembly. China’s massive production footprint in automotive and consumer goods drives demand for high-throughput arc and spot welding solutions, with local vendors rapidly scaling both hardware and software offerings. Meanwhile, Southeast Asia emerges as a low-cost manufacturing hub for medium-payload robot deployment, attracting capital expenditure from global OEMs seeking operational flexibility and cost optimization.
This comprehensive research report examines key regions that drive the evolution of the Articulated Robot for Welding market, offering deep insights into regional trends, growth factors, and industry developments that are influencing market performance.
- Americas
- Asia-Pacific
- Europe, Middle East & Africa
Key Company Strategies and Competitive Landscape
Leading original equipment manufacturers and technology providers continually refine strategies to capture market share in the articulated welding segment. ABB Ltd. focuses on integrated digital platforms that unify robot control, vision, and analytics, offering customers end-to-end visibility into process health. Cloos Welding Technology delivers modular welding cells tailored to spot and seam welding, emphasizing quick-change end effectors for production agility.
Comau SpA leverages its strong presence in European automotive to offer turnkey arc welding lines, while Daihen Corporation integrates industry-specific software for enhanced joint tracking accuracy. Fanuc Corporation’s extensive robot portfolio ranges from micro-payload collaborative arms to heavy-duty four-axis units, complemented by its proprietary programming language that reduces cycle times.
HITACHI LTD. and Hyundai Robotics collaborate on smart factory architectures, embedding predictive maintenance algorithms into controllers to maximize uptime. Kawasaki Heavy Industries, Ltd. and KUKA AG invest in open-architecture control systems, enabling seamless integration with third-party components and ERP platforms. Miller Electric Mfg. LLC and The Lincoln Electric Company, each with deep expertise in welding power sources, bundle power source–robot combinations that optimize arc characteristics for diverse materials.
Nachi-Fujikoshi Corp. develops high-speed, high-acceleration robots suited for compact welding cells, whereas Omron Corporation emphasizes AI-driven vision systems for seam detection. Panasonic Corporation’s focus on laser welding technology dovetails with its robust sensor suite, allowing for ultra-precise, low-heat welds. Yaskawa Electric Corporation differentiates through user-friendly HMI interfaces and collaborative payload options, targeting small-batch, high-mix production environments.
This comprehensive research report delivers an in-depth overview of the principal market players in the Articulated Robot for Welding market, evaluating their market share, strategic initiatives, and competitive positioning to illuminate the factors shaping the competitive landscape.
- ABB Ltd.
- Cloos Welding Technology
- Comau SpA
- Daihen Corporation
- Fanuc Corporation
- HITACHI LTD.
- Hyundai Robotics
- Kawasaki Heavy Industries, Ltd.
- KUKA AG
- Miller Electric Mfg. LLC
- Nachi-Fujikoshi Corp.
- Omron Corporation
- Panasonic Corporation
- The Lincoln Electric Company
- Yaskawa Electric Corporation
Actionable Recommendations for Industry Leaders
Leaders in welding automation should prioritize cross-functional collaboration between engineering, operations, and procurement teams to drive holistic technology adoption. Establishing a center of excellence for robotics deployment can consolidate best practices and accelerate knowledge transfer. Equally important is the integration of digital twins: simulating robotic cells virtually not only validates process parameters but also identifies potential bottlenecks before physical installation.
To future-proof investments, organizations must negotiate flexible supplier agreements that account for geopolitical uncertainties, including tariff fluctuations and shipping disruptions. This entails diversifying the supplier base across multiple regions and fostering strategic partnerships with component manufacturers for co-development of customized solutions.
Investing in workforce readiness is critical. Upskilling technicians on both offline programming tools and advanced maintenance platforms-especially those leveraging machine learning to predict component wear-ensures that teams can maximize system availability and respond swiftly to process anomalies.
Finally, sustainability should be embedded into automation roadmaps. Optimizing arc efficiency, reclaiming inert gas, and designing for energy recovery amplify environmental stewardship while supporting long-term cost savings. Regularly benchmarking key performance indicators-such as cycle time, first-pass quality, and mean time between failures-creates a feedback loop that drives continuous improvement across welding cells.
Explore AI-driven insights for the Articulated Robot for Welding market with ResearchAI on our online platform, providing deeper, data-backed market analysis.
Ask ResearchAI anything
World's First Innovative Al for Market Research
Conclusion: Steering the Future of Automated Welding
Articulated robots for welding stand at the intersection of precision engineering and digital innovation. As the market evolves through collaborative frameworks, adaptive welding technologies, and diversified business models, manufacturers that embrace agility will outpace competition. Strategic supply chain realignment in response to tariff shifts, combined with a commitment to sustainability and workforce development, forms the bedrock of resilient automation initiatives.
By leveraging advanced segmentation insights, organizations can tailor solutions to specific payload requirements, end-user applications, and functionality demands, ensuring that each installation maximizes return on investment. Regional nuances further inform deployment strategies, guiding decisions on local partnerships and system customization.
The landscape continues to advance as leading companies expand their offerings with integrated power sources, AI-enabled vision systems, and open architecture controls. These developments underscore an era in which welding cells are not merely tools but intelligent, interconnected production nodes capable of self-optimization and data-driven adaptation.
This section provides a structured overview of the report, outlining key chapters and topics covered for easy reference in our Articulated Robot for Welding market comprehensive research report.
- Preface
- Research Methodology
- Executive Summary
- Market Overview
- Market Dynamics
- Market Insights
- Cumulative Impact of United States Tariffs 2025
- Articulated Robot for Welding Market, by Type
- Articulated Robot for Welding Market, by Payload Capacity
- Articulated Robot for Welding Market, by End-User Industry
- Articulated Robot for Welding Market, by Application
- Articulated Robot for Welding Market, by Component
- Articulated Robot for Welding Market, by Technology
- Articulated Robot for Welding Market, by Material Type To Be Welded
- Articulated Robot for Welding Market, by Functionality
- Articulated Robot for Welding Market, by Business Model
- Articulated Robot for Welding Market, by Maintenance
- Americas Articulated Robot for Welding Market
- Asia-Pacific Articulated Robot for Welding Market
- Europe, Middle East & Africa Articulated Robot for Welding Market
- Competitive Landscape
- ResearchAI
- ResearchStatistics
- ResearchContacts
- ResearchArticles
- Appendix
- List of Figures [Total: 36]
- List of Tables [Total: 860 ]
Call to Action: Partner with Ketan Rohom for Advanced Market Insights
To gain comprehensive insights and strategic guidance tailored to your organization’s welding automation initiatives, connect with Ketan Rohom (Associate Director, Sales & Marketing) to secure the full market research report. Empower your team with actionable data, in-depth competitive analysis, and expert recommendations to lead with confidence.
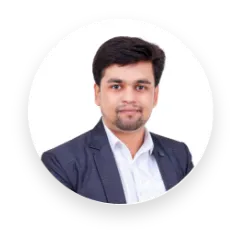
- When do I get the report?
- In what format does this report get delivered to me?
- How long has 360iResearch been around?
- What if I have a question about your reports?
- Can I share this report with my team?
- Can I use your research in my presentation?