Introduction: Shaping the Future of Automated Wafer Bonding
The rapid evolution of semiconductor manufacturing has elevated automated wafer bonders from niche tools to essential enablers of advanced packaging, MEMS fabrication, and photonics integration. As device geometries shrink and performance demands intensify, precision alignment and robust bonding processes have become critical differentiators for industry leaders. In response, equipment providers and end users alike are investing in automation, closed-loop monitoring, and high-throughput strategies to minimize cycle times and maximize yield. Moreover, the convergence of materials science, process engineering, and digital analytics is unlocking new possibilities for heterogeneous integration, unlocking next-generation applications in automotive electronics, telecommunications, and medical devices. This introduction outlines the foundational drivers reshaping the automated wafer bonder landscape, setting the stage for a deeper exploration of market shifts, tariff impacts, segmentation insights, and strategic imperatives. By surveying recent technological breakthroughs, supply chain dynamics, and regulatory influences, we frame the critical context that decision-makers and technical experts need to navigate an increasingly complex environment. Ultimately, this summary equips stakeholders with a clear understanding of how automation, material innovation, and policy changes converge to redefine wafer bonding in the years ahead.
Transformative Shifts in the Automated Wafer Bonder Landscape
Over the past decade, the automated wafer bonder landscape has undergone transformative shifts driven by escalating demand for miniaturization, multi-chip modules, and heterogeneous integration. Advanced packaging approaches, such as 3D stacking, have compelled equipment manufacturers to integrate in situ metrology and alignment feedback loops, ensuring sub-micron accuracy. Furthermore, thermocompression and direct bonding techniques have matured to accommodate sensitive CMOS image sensors and MEMS devices, facilitating cost-effective production at scale. Concurrently, adhesive and anodic bonding variants have evolved, with direct and indirect anodic methods enabling glass-to-silicon interfaces for photonic applications. These innovations coincide with the proliferation of fully automatic wafer bonders, which deliver enhanced throughput for high-volume semiconductor fabs, alongside semi-automatic and manual systems that maintain flexibility for R&D labs and niche production runs. In addition, the convergence of digital twin simulations and machine learning algorithms now allows predictive maintenance and process optimization, reducing unplanned downtime. These combined shifts underscore a dynamic market where technological advancement, process integration, and data-driven controls establish new benchmarks for quality and efficiency.
Cumulative Impact of United States Tariffs 2025 on Wafer Bonding
In 2025, the imposition of new U.S. tariffs on wafer bonder equipment and key bonding materials has prompted a reevaluation of global supply chains and sourcing strategies. By raising duties on imported components-including precision alignment optics and specialty alloys-manufacturers have seen input costs climb, pressuring margins and triggering cost-pass-through measures. As a result, leading semiconductor foundries and packaging houses have diversified their supplier base, seeking tariff-exempt local production in allied regions to mitigate exposure. Meanwhile, some equipment vendors have reclassified product categories to avoid higher tariff brackets, while others have absorbed duties to maintain competitive pricing. The ripple effects extend beyond direct costs: logistics providers recalibrated shipment routes, and customs brokers deepened collaborations to expedite tariff classification appeals. Furthermore, the tariff landscape accelerated conversations around reshoring critical wafer bonder subassemblies, leveraging domestic manufacturing incentives and tax credits. Collectively, these actions reflect a strategic pivot from lowest-cost sourcing to a resilience-oriented model, where duty considerations influence facility placement, partner selection, and long-term capital investment decisions.
Key Segmentation Insights Driving Market Dynamics
Detailed segmentation reveals diverse growth vectors and risk profiles across the automated wafer bonder market. When examined by wafer size, production for 200 mm platforms remains stable in legacy MEMS and CMOS sensor lines, while 300 mm systems drive volume in mainstream semiconductor and photonic sectors; emerging 450 mm initiatives stay in pilot phases due to infrastructure costs. Bonding technology segmentation highlights adhesive bonding’s popularity for flexible substrates, whereas anodic bonding-including both direct and indirect approaches-addresses glass-to-silicon interfaces critical for photonics and microfluidics; direct and thermocompression bonding dominate high-precision 3D integration. Application-based segmentation underscores automotive electronics and consumer devices as high-volume markets, medical devices demanding biocompatible materials, and MEMS production split between actuators and sensors; photonics and telecommunications leverage fiber-optic and wireless device integration. Across end-user industries, aerospace & defense, communication & IT, and healthcare adopt wafer bonding for mission-critical reliability, while semiconductor fabs lean on R&D labs-spanning educational and technical institutes-for process innovation. Material type analysis contrasts glass and glass-ceramic for optical clarity with silicon’s thermal performance. Equipment type segmentation differentiates fully automatic bonders for mass production, semi-automatic units for flexible batch sizes, and manual systems for lab experiments. Finally, device type segmentation covers 3D integration modules, CMOS image sensors, LED packages, and memory stacks, each demanding tailored bonding precision and throughput.
This comprehensive research report categorizes the Automated Wafer Bonder market into clearly defined segments, providing a detailed analysis of emerging trends and precise revenue forecasts to support strategic decision-making.
- Wafer Size
- Bonding Technology
- Application
- End-User Industry
- Material Type
- Equipment Type
- Device Type
Regional Perspectives: Americas, EMEA, and Asia-Pacific
Regional dynamics significantly influence the adoption and deployment of automated wafer bonders. In the Americas, strong domestic semiconductor manufacturing policies and reshoring incentives have stimulated investments in advanced packaging lines and local supplier development, reinforcing North American fabs’ preference for fully automatic bonders with integrated metrology. Transitioning to Europe, Middle East & Africa, regulatory focus on data sovereignty and sustainable manufacturing practices has motivated investment in low-waste bonding adhesives and energy-efficient thermocompression systems, particularly within German and French semiconductor clusters. Meanwhile, the Asia-Pacific region leads in capacity expansion, driven by aggressive wafer foundry growth in Taiwan, South Korea, and China; here, high-throughput direct and adhesive bonding solutions scale to meet consumer electronics and telecommunications demand. Additionally, government subsidies in Japan and Singapore accelerate R&D adoption of next-generation anodic bonding for photonic integration, while India’s emerging semiconductor policy encourages local assembly of wafer bonding modules. These regional perspectives underscore how policy, infrastructure maturity, and application mix determine both technology priorities and supplier selection.
This comprehensive research report examines key regions that drive the evolution of the Automated Wafer Bonder market, offering deep insights into regional trends, growth factors, and industry developments that are influencing market performance.
- Americas
- Asia-Pacific
- Europe, Middle East & Africa
Strategic Moves by Leading Automated Wafer Bonder Providers
Leading equipment and material suppliers are actively shaping the automated wafer bonder ecosystem. Applied Materials, Inc. continues to refine precision alignment systems that seamlessly integrate with back-end process flows, while Atotech Deutschland GmbH advances adhesive formulations tailored for high-temperature thermocompression. Brewer Science, Inc. invests in nanostructured interface layers to enhance bond strength in silicon-glass assemblies. DISCO Corporation differentiates through wafer thinning and dicing capabilities that dovetail with bonding modules, creating end-to-end solutions. EV Group expands its collaborative bonding platforms, incorporating in-line metrology to guarantee sub-micron accuracy. Indium Corporation develops specialized solder preforms and alloys that streamline hybrid bonding for CMOS image sensors. KLA Corporation integrates inspection and defect-review tools into bonder platforms, enabling real-time quality control. Kulicke & Soffa Industries, Inc. leverages its packaging expertise to introduce flip-chip bonding enhancements. Lam Research Corporation synchronizes etch processes with bonding cycles for improved interface cleanliness. Mattson Technology, Inc. focuses on thermal uniformity in vacuum bonders. ON Semiconductor Corporation pioneers sensor-ready bonded wafer stacks optimized for automotive applications. SHENZHEN QT MICROELECTRONICS TECHNOLOGY CO., LTD. accelerates local manufacturing of manual and semi-automatic systems in China. SUSS MicroTec SE refines wafer handling robotics, while Tokyo Electron Limited and Tokyo Ohka Kogyo Co., Ltd. collaborate on interface materials that maximize yield. Ultratech, Inc. (a division of Veeco) leverages high-precision lithography alignment to boost throughput in 3D integration devices.
This comprehensive research report delivers an in-depth overview of the principal market players in the Automated Wafer Bonder market, evaluating their market share, strategic initiatives, and competitive positioning to illuminate the factors shaping the competitive landscape.
- Amat (Applied Materials, Inc.)
- Atotech Deutschland GmbH
- Brewer Science, Inc.
- DISCO Corporation
- EV Group (EVG)
- Indium Corporation
- KLA Corporation
- Kulicke & Soffa Industries, Inc.
- Lam Research Corporation
- Mattson Technology, Inc.
- ON Semiconductor Corporation
- SHENZHEN QT MICROELECTRONICS TECHNOLOGY CO., LTD.
- SUSS MicroTec SE
- Tokyo Electron Limited
- Tokyo Ohka Kogyo Co., Ltd.
- Ultratech, Inc. (A division of Veeco)
Actionable Recommendations for Industry Leaders
To maintain competitive advantage and resilience, industry leaders should pursue several strategic initiatives. First, they must deepen collaboration with materials innovators to co-develop bonding adhesives, interface alloys, and process chemistries that address emerging device requirements. Second, firms should integrate digital twins and AI-driven analytics into automation platforms to enable predictive maintenance, adaptive process control, and rapid root-cause identification. Third, companies ought to diversify supply chains by qualifying multiple sources for critical subassemblies, thereby insulating operations from tariff fluctuations and logistical disruptions. Fourth, engaging with government incentives and regional consortia can secure funding for R&D pilots in advanced packaging and photonics applications. Fifth, cross-industry partnerships-linking semiconductor players with automotive, healthcare, and aerospace customers-will accelerate the adoption of heterogeneous integration solutions. Finally, investing in workforce upskilling ensures that technicians and engineers possess the multidisciplinary expertise required to operate next-generation fully automatic and semi-automatic bonders. By executing these actions, organizations can optimize yield, control costs, and drive systemic innovation in wafer bonding.
Explore AI-driven insights for the Automated Wafer Bonder market with ResearchAI on our online platform, providing deeper, data-backed market analysis.
Ask ResearchAI anything
World's First Innovative Al for Market Research
Conclusion: Seizing Opportunities in Wafer Bonding
The automated wafer bonder market stands at a crossroads of technological innovation and strategic realignment. As devices become more complex and global supply chains face geopolitical headwinds, precision bonding processes will determine competitive positioning. Manufacturers that harness advanced alignment techniques, robust material interfaces, and data-driven automation will unlock superior performance and reliability across high-value applications in MEMS, photonics, and advanced packaging. Concurrently, a proactive stance on tariff mitigation, regional diversification, and collaborative R&D will foster operational resilience and strategic flexibility. Ultimately, this landscape rewards those who balance rigorous process control with agile adaptation to policy shifts and evolving customer needs. By synthesizing segmentation insights, regional perspectives, and company strategies, decision-makers can chart a clear path through uncertainty, ensuring that automated wafer bonders remain pivotal in powering next-generation electronic systems.
This section provides a structured overview of the report, outlining key chapters and topics covered for easy reference in our Automated Wafer Bonder market comprehensive research report.
- Preface
- Research Methodology
- Executive Summary
- Market Overview
- Market Dynamics
- Market Insights
- Cumulative Impact of United States Tariffs 2025
- Automated Wafer Bonder Market, by Wafer Size
- Automated Wafer Bonder Market, by Bonding Technology
- Automated Wafer Bonder Market, by Application
- Automated Wafer Bonder Market, by End-User Industry
- Automated Wafer Bonder Market, by Material Type
- Automated Wafer Bonder Market, by Equipment Type
- Automated Wafer Bonder Market, by Device Type
- Americas Automated Wafer Bonder Market
- Asia-Pacific Automated Wafer Bonder Market
- Europe, Middle East & Africa Automated Wafer Bonder Market
- Competitive Landscape
- ResearchAI
- ResearchStatistics
- ResearchContacts
- ResearchArticles
- Appendix
- List of Figures [Total: 30]
- List of Tables [Total: 509 ]
Take the Next Step: Secure Your Market Insights
For a comprehensive understanding of these insights and to guide your strategic roadmap, connect with Ketan Rohom, Associate Director, Sales & Marketing. He can provide detailed analyses, customized data excerpts, and advisory support tailored to your organization’s needs. Reach out to schedule a consultation and secure access to the full market research report, equipping your team with the intelligence required to capitalize on emerging trends and technology advances in automated wafer bonding.
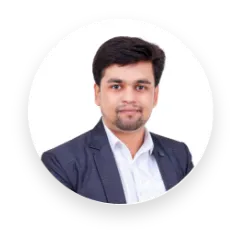
- When do I get the report?
- In what format does this report get delivered to me?
- How long has 360iResearch been around?
- What if I have a question about your reports?
- Can I share this report with my team?
- Can I use your research in my presentation?