Setting the Stage for Automated Lithium Cell Production
As global demand for energy storage and electric mobility accelerates, the automotive and electronics industries are turning to advanced assembly technologies to ensure consistency, safety, and efficiency in lithium battery cell production. This shift toward automation is not merely a technological upgrade but a strategic imperative. Manufacturers face mounting pressure to optimize throughput, minimize costs, and guarantee the highest quality standards as geopolitical dynamics and resource constraints tighten.
The transition from manual and semi-automated processes to fully automated assembly lines marks a transformative period in the lithium battery landscape. Automation solutions, ranging from precision stacking machines to integrated inspection and testing systems, offer unprecedented control over production variables. These systems not only reduce the risks of human error but also enable real-time monitoring and adaptive process adjustments. Consequently, stakeholders across the value chain-from equipment suppliers to cell manufacturers and end users-must align their strategies to harness these technological gains.
This executive summary delivers a concise yet comprehensive overview of the factors reshaping the industry, including emerging tariff policies, segmentation insights, regional dynamics, and leading players. Through a balanced lens of rigorous analysis and practical foresight, this report equips decision-makers with the knowledge to navigate a rapidly evolving marketplace and capitalize on the next wave of growth.
Navigating the Technological Tide of Automation and Integration
In recent years, the lithium battery cell assembly sector has experienced a series of transformative shifts fueled by advancements in robotics, machine learning, and systems integration. Industry 4.0 paradigms now underpin end-to-end production workflows, enabling manufacturers to leverage data analytics, predictive maintenance, and digital twins. With robotic stacking machines achieving micrometer-level precision and fully integrated inspection systems identifying defects instantaneously, the era of reactive quality control is giving way to proactive process optimization.
Concurrently, supply chain resilience has emerged as a strategic priority. Companies are reexamining their sourcing strategies, localizing critical components, and forging partnerships to mitigate disruption risks. This focus on supply chain agility has driven a surge in demand for formation and aging systems that can adapt to variable cell chemistries and batch sizes without compromising throughput.
Moreover, the rapid electrification of transportation and expansion of energy storage applications have compelled OEMs and battery manufacturers to accelerate capacity expansions. They are investing in modular, scalable automation platforms that can be tailored to diverse cell formats-cylindrical, pouch, and prismatic-while maintaining high levels of flexibility. As competition intensifies, the ability to rapidly reconfigure production lines for new chemistries and form factors is now a decisive differentiator.
Assessing the 2025 U.S. Tariff Impact on Automation Investments
As of 2025, the recalibration of U.S. trade policy has introduced a new layer of complexity to the global lithium battery equipment market. Tariffs levied on imported machinery and critical components have the potential to reshape sourcing decisions and production footprints. Equipment suppliers face increased cost pressures when exporting to the United States, leading some manufacturers to reconsider their supply chains and evaluate onshore assembly options.
The cost impact of these tariffs is multifaceted. Higher import duties translate into elevated capital expenditure, prompting companies to seek alternative procurement channels or domestic partnerships. To offset these added expenses, some stakeholders have accelerated investments in higher throughput lines and advanced process automation, striving for economies of scale that can absorb the incremental tariff-driven costs.
Meanwhile, battery cell makers in the United States are exploring sourcing equipment from regional suppliers in Asia-Pacific and Europe, or repatriating production through greenfield facility developments. Policymakers are supporting these moves with incentives aimed at bolstering domestic manufacturing capabilities and security of supply. As a result, the competitive landscape is evolving rapidly, with tariff dynamics serving as both a barrier and a catalyst for strategic realignment.
Unpacking Multidimensional Market Segmentation
A granular view of the market’s structure reveals critical insights across multiple segmentation dimensions. When analyzed by equipment type, the landscape comprises electrolyte filling systems, formation and aging systems, inspection and testing systems, packaging and labeling systems, stacking machines, winding machines, and welding machines subdivided into laser welding and resistance welding variants. Each equipment category exhibits unique automation requirements, precision tolerances, and throughput targets, underscoring the importance of tailored integration strategies.
Examining cell format segmentation, cylindrical, pouch, and prismatic cell types drive distinct line architectures. Cylindrical cells often demand continuous winding and precision packing flows, whereas pouch cells necessitate advanced stacking, sealing, and formation processes. Prismatic formats combine aspects of both, requiring hybrid solutions. Production strategies must accommodate rapid changeovers and inline inspection capabilities to maintain quality across diverse cell designs.
End-use segmentation highlights varied performance parameters and regulatory constraints. Consumer electronics applications span laptops, tablets, smartphones, and wearables, prioritizing compact form factors and high cycle life. Electric vehicles encompass commercial and passenger vehicles, where energy density, safety, and fast charge capabilities dominate equipment specifications. Energy storage systems across commercial, residential, and utility-scale installations emphasize long-term reliability and cost efficiency, while power tools focus on durability and peak discharge rates.
Automation level further segments the market into fully automatic and semi-automatic systems. Fully automatic lines deliver unparalleled throughput and consistency but require higher initial capital investment and sophisticated control architectures. Semi-automatic solutions offer lower entry costs and flexible layouts, often serving as pilot or niche production lines. Production capacity criteria distinguish large-scale facilities processing millions of cells annually from medium-scale plants with mid-tier volumes and small-scale operations catering to specialized or early-stage applications. Finally, sales channels comprise aftermarket support, direct sales agreements, and OEM partnerships, each presenting different lifecycle value propositions and service models.
This comprehensive research report categorizes the Automatic Assembly Line for Lithium Battery Cell market into clearly defined segments, providing a detailed analysis of emerging trends and precise revenue forecasts to support strategic decision-making.
- Equipment Type
- Cell Format
- End Use
- Automation Level
- Production Capacity
- Sales Channel
Decoding Regional Dynamics Influencing Automation Demand
Regional analysis underscores the varied dynamics shaping equipment demand across the globe. In the Americas, strong government incentives for electric vehicles and energy storage projects have spurred demand for high-speed formation and aging systems as well as advanced inspection technologies to ensure compliance with rigorous safety standards. The region’s focus on onshore manufacturing capacity has also bolstered interest in modular automation architectures that can be rapidly deployed.
Over in Europe, Middle East & Africa, regulatory frameworks targeting carbon neutrality and renewable integration are driving significant investments in utility-scale energy storage and electric mobility infrastructure. Manufacturers in this region are prioritizing fully automatic stacking and welding lines that maximize yield while adhering to strict environmental and safety guidelines. Strategic partnerships and joint ventures between regional players and global automation suppliers are proliferating, facilitating technology transfer and local value creation.
Asia-Pacific remains the largest and most diverse market, with leading cell producers in China, South Korea, and Japan advancing both scale and sophistication. The region’s emphasis on cost efficiency has catalyzed the adoption of semi-automatic and fully automatic packaging and labeling systems tailored for high-volume pouch and cylindrical cell formats. Meanwhile, emerging markets within Asia-Pacific are exploring small-scale production platforms as they develop domestic battery manufacturing ecosystems.
This comprehensive research report examines key regions that drive the evolution of the Automatic Assembly Line for Lithium Battery Cell market, offering deep insights into regional trends, growth factors, and industry developments that are influencing market performance.
- Americas
- Europe, Middle East & Africa
- Asia-Pacific
Profiling Leading Automation Innovators and Collaborations
Key companies are redefining the competitive landscape through differentiated automation portfolios and strategic alliances. Leading system integrators are leveraging proprietary robotics and vision systems to deliver turnkey assembly lines that seamlessly integrate filling, stacking, welding, and inspection modules. These vendors emphasize end-to-end traceability and digital connectivity, enabling manufacturers to harness real-time process analytics for continuous improvement.
Equipment manufacturers specializing in formation and aging platforms are collaborating with software providers to embed AI-driven process optimization engines, reducing cycle times and energy consumption. Inspection and testing technology leaders are unveiling advanced machine vision solutions that detect sub-micrometer defects and monitor electrode integrity without interrupting production flows. Simultaneously, packaging and labeling specialists are focusing on flexible, high-speed lines that accommodate rapid format changeovers and comply with evolving safety regulations.
Strategic OEM partnerships are increasingly common, as cell producers seek to co-develop bespoke automation systems that align closely with proprietary cell chemistries and form factors. These collaborations often involve joint R&D efforts, pilot line deployments, and shared service agreements to accelerate time to market. Additionally, aftermarket service providers are expanding global support networks to offer predictive maintenance, remote diagnostics, and operator training, ensuring maximum uptime and operational excellence.
This comprehensive research report delivers an in-depth overview of the principal market players in the Automatic Assembly Line for Lithium Battery Cell market, evaluating their market share, strategic initiatives, and competitive positioning to illuminate the factors shaping the competitive landscape.
- Manz Aktiengesellschaft
- Komax Holding AG
- Applied Materials, Inc.
- JBT Corporation
- ABB Ltd.
- Dürr Aktiengesellschaft
- KUKA Aktiengesellschaft
- Panasonic Factory Solutions Co., Ltd.
- Mitsubishi Electric Corporation
- Bosch Rexroth AG
Blueprint for Operational Excellence in Automated Assembly
To thrive in this competitive environment, industry leaders must adopt a multifaceted strategy that balances technological agility with operational resilience. First, it is imperative to invest in modular automation platforms that can be reconfigured rapidly to support new cell formats and chemistries. Such platforms allow manufacturers to respond to shifting market demands without the prohibitive costs of purpose-built lines.
Second, forging strategic partnerships with system integrators and software providers will accelerate access to cutting-edge robotics, AI-driven optimization engines, and comprehensive digital twins. These alliances should extend beyond procurement to include co-development initiatives and joint pilot programs, creating a shared roadmap for innovation.
Third, enhancing supply chain transparency through integrated data capture and analytics will mitigate tariff risks and raw material volatility. By deploying end-to-end tracking solutions, companies can shift from reactive purchasing decisions to proactive, scenario-based planning.
Fourth, upskilling the workforce is essential. As automation complexity grows, organizations must invest in training programs that equip operators and engineers with the skills to manage advanced control systems, interpret process data, and perform predictive maintenance. Cross-functional teams that blend automation expertise with cell chemistry and quality management knowledge will be critical to sustaining continuous improvement.
Finally, embedding sustainability metrics into automation roadmaps will future-proof operations. Energy-efficient process designs, closed-loop coolant and gas management, and waste reduction initiatives not only reduce environmental impact but also contribute to lower total cost of ownership over the equipment lifecycle.
Ensuring Rigor Through Integrated Qualitative and Quantitative Analysis
This research employs a robust, multi-pronged methodology to ensure accuracy and reliability. Primary data was gathered through in-depth interviews with key executives and technical experts across equipment suppliers, cell manufacturers, and end-use customers. These qualitative insights were complemented by on-site visits to operational facilities, enabling firsthand observations of automation workflows and process integration.
Secondary sources included trade publications, regulatory filings, patent databases, and corporate financial reports. These materials provided a comprehensive view of technology trends, market dynamics, and competitive positioning. Quantitative data was analyzed using advanced statistical techniques to uncover correlations between automation deployment, throughput, and quality metrics.
A structured segmentation framework was applied to dissect the market across equipment type, cell format, end use, automation level, production capacity, and sales channel dimensions. Regional analyses were conducted to capture local regulatory influences, incentive programs, and supply chain configurations. All findings were validated through expert panels and iterative feedback loops to ensure practical relevance and strategic clarity.
Explore AI-driven insights for the Automatic Assembly Line for Lithium Battery Cell market with ResearchAI on our online platform, providing deeper, data-backed market analysis.
Ask ResearchAI anything
World's First Innovative Al for Market Research
Summarizing Strategic Pathways in Battery Cell Automation
The automatic assembly line for lithium battery cells is at the forefront of industrial innovation, where incremental improvements yield significant competitive advantages. As automation technologies evolve, stakeholders must remain vigilant to the interplay of regulatory shifts, tariff dynamics, and segmentation nuances that shape demand.
By understanding the multifaceted nature of this market-from equipment specialization and cell format diversity to regional incentives and key partnerships-industry players can craft targeted strategies that drive efficiency, quality, and growth. The insights and recommendations presented herein provide a strategic compass for navigating the opportunities and challenges of automated lithium cell production.
This section provides a structured overview of the report, outlining key chapters and topics covered for easy reference in our Automatic Assembly Line for Lithium Battery Cell market comprehensive research report.
- Preface
- Research Methodology
- Executive Summary
- Market Overview
- Market Dynamics
- Market Insights
- Cumulative Impact of United States Tariffs 2025
- Automatic Assembly Line for Lithium Battery Cell Market, by Equipment Type
- Automatic Assembly Line for Lithium Battery Cell Market, by Cell Format
- Automatic Assembly Line for Lithium Battery Cell Market, by End Use
- Automatic Assembly Line for Lithium Battery Cell Market, by Automation Level
- Automatic Assembly Line for Lithium Battery Cell Market, by Production Capacity
- Automatic Assembly Line for Lithium Battery Cell Market, by Sales Channel
- Americas Automatic Assembly Line for Lithium Battery Cell Market
- Europe, Middle East & Africa Automatic Assembly Line for Lithium Battery Cell Market
- Asia-Pacific Automatic Assembly Line for Lithium Battery Cell Market
- Competitive Landscape
- ResearchAI
- ResearchStatistics
- ResearchContacts
- ResearchArticles
- Appendix
- List of Figures [Total: 28]
- List of Tables [Total: 463 ]
Engage with Our Associate Director to Secure Your Comprehensive Market Report
Are you ready to elevate your strategic planning with comprehensive insights into the automatic assembly line for lithium battery cells? Reach out to Ketan Rohom, Associate Director, Sales & Marketing at 360iResearch, to secure your copy of the full market research report. Gain exclusive access to detailed analyses, actionable recommendations, and future-proof strategies that will empower your organization to thrive in this dynamic, high-growth sector. Connect with Ketan today to discover how this report can become the cornerstone of your competitive advantage
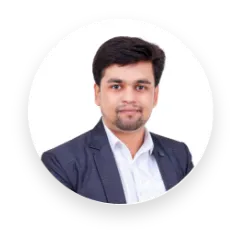
- When do I get the report?
- In what format does this report get delivered to me?
- How long has 360iResearch been around?
- What if I have a question about your reports?
- Can I share this report with my team?
- Can I use your research in my presentation?