Unveiling the Strategic Importance of Inline Capping in Modern Manufacturing
In an era where packaging efficiency can make or break supply chain performance, inline capping machines have emerged as linchpins of modern manufacturing. This report delivers a comprehensive examination of the technological advancements, operational efficiencies, and strategic imperatives that define the current market environment for automatic inline capping machines. By synthesizing insights from industry experts, engineering leaders, and end users, the analysis sheds light on how automated capping solutions are streamlining production lines, reducing downtime, and enhancing product integrity across diverse industries.
The narrative unfolds by exploring the convergence of mechanical precision and digital intelligence within capping operations. It offers an authoritative perspective on the drivers propelling demand for inline capping technology, including the imperative for high-speed throughput, the pursuit of zero-defect production, and the integration of real-time quality control. Through detailed discussion of market dynamics and user requirements, this introduction sets the stage for an in-depth exploration of transformative trends, regulatory influences, and strategic recommendations that follow.
The scope of this analysis spans the full value chain, covering design innovations, materials compatibility, and service models that support long-term equipment performance. Readers will gain a nuanced understanding of how inline capping machines are evolving to meet the exacting standards of pharmaceutical aseptic filling, high-viscosity chemical containment, and the rapid pace of beverage bottling. By laying out the foundational landscape, this introduction primes decision-makers for actionable insights on capitalizing on emerging opportunities and navigating potential challenges.
Revolutionary Forces Redefining the Inline Capping Ecosystem
The inline capping market is undergoing a profound transformation driven by a convergence of technological breakthroughs and shifting operational priorities. Digitization has enabled the integration of intelligent sensors with mechanical capping heads, offering predictive maintenance capabilities that minimize unplanned downtime and optimize performance. At the same time, the advent of advanced robotics and machine vision is elevating precision, ensuring uniform torque application and defect detection at unprecedented speeds.
Environmental stewardship has also reshaped the competitive landscape, prompting manufacturers to embrace eco-friendly materials and energy-efficient designs. This shift is paralleled by evolving consumer expectations for sustainable packaging and traceability throughout the supply chain. As a result, inline capping solutions now incorporate modular frameworks that facilitate rapid changeovers and support a wide array of cap styles and materials, from metal screw caps to snap-on plastics.
Labor market dynamics are further reinforcing automation’s appeal, as skilled technician shortages and rising labor costs drive investment toward self-calibrating systems that require minimal human intervention. In concert with regulatory demands for stringent quality control, these forces are redefining how stakeholders approach equipment selection, deployment, and lifecycle management, ushering in a new era of operational excellence.
Assessing the Ripple Effects of U.S. Tariff Changes on Capping Solutions
Looking ahead to 2025, changes in United States tariff policy are poised to exert a lasting influence on the sourcing and pricing of inline capping equipment. Manufacturers that rely heavily on imported components are reassessing their global supply chains, exploring alternative suppliers in low-tariff jurisdictions to mitigate cost pressures. As tariff rates on mechanical assemblies and precision subcomponents rise, the total cost of ownership for foreign-made systems may increase significantly, prompting a strategic shift toward domestic fabrication or nearshoring.
This realignment is stirring collaborative ventures between equipment OEMs and local machine shops to localize assembly operations and minimize exposure to import duties. Companies are also accelerating efforts to redesign key components for compatibility with regionally available materials, thereby reducing the need for cross-border shipments. Alongside these supply-side adjustments, end users are renegotiating service contracts to reflect new cost structures, emphasizing preventative maintenance and spare-parts stockpiles to avoid tariff-induced lead times.
The cumulative effect of these trends is a marketplace characterized by heightened resilience and flexibility. Stakeholders who proactively adapt their procurement strategies will preserve their competitive advantage, while those who delay risk facing elevated capital expenditures and operational bottlenecks.
Deep Dive into Core Market Segmentation for Inline Capping Machines
In examining automation type, the market encompasses fully automatic solutions that deliver high throughput without manual intervention, semi automatic machines that blend human oversight with mechanized processes, and manual systems that remain in use where capital constraints or batch sizes favor simpler setups. When considering capping type, press on designs offer rapid engagement for lightweight closures, while screw cap mechanisms cover continuous thread configurations optimized for resealable bottles and lug cap variants suited to thicker closures. ROPP capping systems handle aluminum and tin closures with precision roll-forming heads, and snap cap equipment delivers clean engagement for plastic and composite materials.
Analysis of machine type reveals that chuck-style systems provide versatile gripping for various container profiles, rotary machines cater to high-speed production lines, and inline formats streamline integration with upstream and downstream modules. Within the inline category, double arch designs support higher throughput with synchronized capping heads, whereas single arch configurations offer compact footprints ideal for space-constrained facilities. Container material segmentation highlights the need for specialized torque profiles when handling glass bottles versus metal drums or lightweight plastic containers.
Turning to end use industry insights, chemical applications often demand corrosion-resistant components and custom torque control, while cosmetics and personal care lines prioritize hygiene and changeover speed. In food and beverage operations, beverage bottling requires gentle handling for glass returnables and high-speed PET lines for single-use containers. Pharmaceutical sectors necessitate precise torque monitoring for liquid dosage vials and robust capping integrity for solid dosage containers to meet stringent regulatory standards.
This comprehensive research report categorizes the Automatic Inline Capping Machine market into clearly defined segments, providing a detailed analysis of emerging trends and precise revenue forecasts to support strategic decision-making.
- Automation Type
- Capping Type
- Machine Type
- Container Material
- End Use Industry
Regional Dynamics Shaping the Global Inline Capping Market
Across the Americas, demand is fueled by manufacturers in North and South America seeking high-performance capping solutions for established food and beverage, pharmaceutical, and chemicals industries. Innovation hubs in the United States and Brazil are driving rapid adoption of smart capping systems that integrate seamlessly with digital quality control platforms. Capital investments in Mexico’s growing packaging sector are also contributing to regional growth, as enterprises look to nearshore production amid global supply chain realignment.
Within Europe, Middle East & Africa, established markets in Western Europe emphasize customization and sustainability, with regulatory frameworks in the EU accelerating the uptake of energy-efficient equipment. In the Middle East, large-scale petrochemical and beverage operations require robust capping machines capable of handling aggressive industrial environments. African markets, while emerging more gradually, are seeing nascent demand in pharmaceutical fill-finish and personal care segments, supported by international aid programs and local investments.
The Asia-Pacific arena stands out for its dynamic expansion, driven by rapid industrialization in China and India, burgeoning consumer markets in Southeast Asia, and government incentives to modernize manufacturing infrastructure. Key sectors such as cosmetics, food processing, and specialty chemicals are adopting inline capping machines with enhanced automation and remote monitoring capabilities, positioning the region as a major growth engine for global equipment vendors.
This comprehensive research report examines key regions that drive the evolution of the Automatic Inline Capping Machine market, offering deep insights into regional trends, growth factors, and industry developments that are influencing market performance.
- Americas
- Europe, Middle East & Africa
- Asia-Pacific
Competitive Landscape Spotlight on Leading Inline Capping Innovators
Leading players are establishing competitive differentiation through advanced product portfolios, high-efficiency designs, and comprehensive service networks. Longstanding equipment manufacturers are leveraging deep engineering expertise to introduce modular platforms that accommodate diverse cap styles, automation levels, and production throughput requirements. These incumbents maintain strong aftermarket relationships by offering performance contracts, remote diagnostics, and tailored maintenance plans that drive customer loyalty.
Simultaneously, emerging companies are capturing niche opportunities by focusing on specialized segments such as aseptic pharmaceutical capping or sustainable packaging applications. These agile challengers deploy lightweight materials science innovations, low-energy drive systems, and cloud-based analytics that resonate with customers seeking both operational excellence and environmental compliance. Strategic partnerships and targeted acquisitions are facilitating rapid capability expansion, as both established and newer entrants aim to broaden their global footprint and service offerings.
The competitive landscape is further characterized by ongoing R&D investment in digital twin simulations, IIoT connectivity, and AI-driven quality inspection. By integrating these capabilities into inline capping solutions, market leaders are enhancing predictability, reducing changeover times, and achieving consistent torque accuracy, thereby raising the bar for performance standards across the industry.
This comprehensive research report delivers an in-depth overview of the principal market players in the Automatic Inline Capping Machine market, evaluating their market share, strategic initiatives, and competitive positioning to illuminate the factors shaping the competitive landscape.
- Krones Aktiengesellschaft
- Tetra Pak International S.A.
- Sidel S.A.
- KHS GmbH
- Syntegon Technology GmbH
- Coesia S.p.A.
- IMA S.p.A.
- JBT Corporation
- GEA Group AG
- Ronchi Mario S.p.A.
Strategic Actions to Drive Growth in the Inline Capping Sector
To harness the full potential of inline capping technology, industry leaders should prioritize investment in modular, scalable machine architectures that facilitate rapid changeovers and support a broad spectrum of cap types and materials. Augmenting these platforms with real-time data acquisition and AI-driven analytics will enable predictive maintenance and continuous optimization of torque application, minimizing unplanned downtime and ensuring consistent product quality.
Cultivating strategic partnerships with component suppliers and local service providers can bolster supply chain resilience in the face of tariff fluctuations. By co-developing localized assembly networks and standardized subcomponent designs, organizations can reduce exposure to import duties and compress lead times. Concurrently, integrating sustainability criteria into procurement decisions-such as evaluating energy consumption, carbon footprint, and recyclability-will help align capping operations with broader corporate environmental objectives.
Finally, companies should invest in workforce development programs that enhance operator proficiency with digital instrumentation and machine learning tools. Providing targeted training on advanced troubleshooting, system parameter tuning, and data interpretation will empower teams to extract maximum value from automated capping systems, driving long-term operational efficiency and competitive advantage.
Robust Research Framework Ensuring Credible Market Insights
The research methodology underpinning this analysis combines extensive secondary data collection with structured primary interviews to validate findings and ensure robustness. Industry publications, regulatory filings, patent databases, and corporate reports formed the foundational research layer, while in-depth discussions with equipment manufacturers, packaging line operators, and technology providers enriched the study with real-world perspectives.
A rigorous data triangulation process reconciled information from diverse sources, ensuring consistency across market dynamics, segmentation definitions, and regional outlooks. Key assumptions were cross-verified with engineering experts and financial analysts to confirm technical feasibility and commercial relevance. Quality control measures, including peer reviews and expert panel validation, were implemented at each research phase to maintain the highest standards of accuracy and reliability.
Segmentation mapping was performed to align market observations with automation type, capping style, machine configuration, material compatibility, and end use industry. Regional analysis incorporated trade flow assessments, regulatory environments, and infrastructure considerations. The result is a comprehensive framework that underpins actionable insights and strategic recommendations for stakeholders across the inline capping ecosystem.
Explore AI-driven insights for the Automatic Inline Capping Machine market with ResearchAI on our online platform, providing deeper, data-backed market analysis.
Ask ResearchAI anything
World's First Innovative Al for Market Research
Consolidated Perspectives on the Inline Capping Machine Market Journey
This executive summary has revealed how inline capping machines stand at the intersection of mechanical innovation and digital transformation. The convergence of intelligent automation, sustainability imperatives, and evolving trade policies is reshaping market dynamics, compelling stakeholders to adapt their strategies across sourcing, product development, and service models.
Key segmentation and regional analyses demonstrate the imperative for flexible, modular equipment architectures capable of handling diverse cap types, container materials, and industry requirements. Competitive benchmarking highlights the importance of integrating IIoT connectivity, predictive maintenance, and rapid changeover capabilities to secure operational excellence and customer satisfaction.
By embracing the actionable recommendations outlined herein-ranging from modular machine designs and localized supply chains to workforce development and sustainability integration-industry leaders can unlock significant value. This report serves as a strategic compass, guiding decision-makers through the complexities of an increasingly dynamic marketplace and empowering them to capitalize on emerging opportunities.
This section provides a structured overview of the report, outlining key chapters and topics covered for easy reference in our Automatic Inline Capping Machine market comprehensive research report.
- Preface
- Research Methodology
- Executive Summary
- Market Overview
- Market Dynamics
- Market Insights
- Cumulative Impact of United States Tariffs 2025
- Automatic Inline Capping Machine Market, by Automation Type
- Automatic Inline Capping Machine Market, by Capping Type
- Automatic Inline Capping Machine Market, by Machine Type
- Automatic Inline Capping Machine Market, by Container Material
- Automatic Inline Capping Machine Market, by End Use Industry
- Americas Automatic Inline Capping Machine Market
- Europe, Middle East & Africa Automatic Inline Capping Machine Market
- Asia-Pacific Automatic Inline Capping Machine Market
- Competitive Landscape
- ResearchAI
- ResearchStatistics
- ResearchContacts
- ResearchArticles
- Appendix
- List of Figures [Total: 26]
- List of Tables [Total: 458 ]
Secure Your Comprehensive Report by Connecting with Ketan Rohom Today
For an in-depth exploration of the automatic inline capping machine market, reach out to Ketan Rohom, Associate Director, Sales & Marketing at 360iResearch. Engage directly to secure the comprehensive report that delivers rigorous analysis, strategic insights, and actionable recommendations tailored to your organizational goals. Whether you seek to benchmark your machine capabilities, understand emerging regulatory implications, or identify high-potential regions and segments, this report equips you with the critical intelligence needed to make informed decisions. Contact Ketan Rohom today to elevate your market position, accelerate innovation, and drive sustainable growth with the definitive resource on inline capping technology.
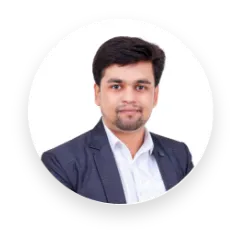
- When do I get the report?
- In what format does this report get delivered to me?
- How long has 360iResearch been around?
- What if I have a question about your reports?
- Can I share this report with my team?
- Can I use your research in my presentation?