The Automatic Lubrication Systems Market size was estimated at USD 1.21 billion in 2024 and expected to reach USD 1.29 billion in 2025, at a CAGR 6.06% to reach USD 1.73 billion by 2030.

Setting the Stage for Automated Lubrication Excellence
Automated lubrication systems have emerged as critical enablers of operational excellence across a wide span of heavy industries and precision manufacturing environments. By delivering precisely metered lubricant to bearings, gears, chains, and other moving parts, these systems reduce friction losses, prevent unscheduled downtime, and extend equipment lifespan. As capital investments intensify in advanced machinery, the demand for reliable lubrication infrastructure has become more pronounced than ever.
With ongoing pressures to optimize asset utilization and meet stringent productivity targets, manufacturers and plant operators are shifting away from manual greasing routines toward fully integrated lubrication solutions. These systems harness sensors, controllers, and network connectivity to deliver tailored lubrication regimens that adapt in real time to thermal loads, rotational speeds, and contamination levels. The result is a fundamental transformation in how maintenance teams manage reliability programs, leveraging data-driven protocols to anticipate lubrication-related failures and to orchestrate interventions with surgical precision.
This executive summary distills the latest market intelligence on automatic lubrication systems, capturing core growth drivers, evolving technological paradigms, and the competitive dynamics shaping this space. By mapping key segmentation frameworks, analyzing regional growth pockets, and spotlighting leading innovators, this report offers decision-makers the clarity needed to formulate resilient supply strategies, invest in the right solution profiles, and unlock new avenues for operational differentiation.
Emerging Forces Redefining Lubrication Technologies
The landscape of automatic lubrication solutions is undergoing a profound evolution driven by digitalization and an increasing emphasis on sustainability. Industry 4.0 initiatives are propelling the integration of smart sensors and edge computing within lubrication networks, enabling continuous performance monitoring and adaptive control. This shift from fixed-cycle lubrication to condition-based dispensing marks a leap forward in maintenance philosophy, where teams leverage real-time insights to optimize lubrication volumes and intervals, thereby minimizing waste and environmental impact.
Simultaneously, the proliferation of Internet of Things platforms has facilitated seamless connectivity between lubrication controllers, enterprise asset management systems, and maintenance dashboards. This convergence is empowering maintenance engineers to visualize lubrication health across distributed asset fleets, orchestrate remote parameter adjustments, and trigger automated alerts when deviations arise. As a result, lubrication programs are no longer siloed tasks but integral elements of holistic reliability strategies that encompass predictive analytics, root cause diagnostics, and continuous process improvement.
Beyond digital convergence, material science advances are yielding new lubricant formulations that offer superior thermal stability, extended service intervals, and compatibility with diverse substrate materials. When paired with next-generation dispensing technologies, these developments are unlocking new performance thresholds in high-load, high-temperature, and corrosive operating environments. Taken together, these transformative shifts are redefining the value proposition of lubrication systems, transitioning them from ancillary utilities to strategic enablers of operational resilience and sustainable growth.
Reassessing Supply Chains Amid U.S. Tariff Reforms
In 2025, the imposition of revised United States tariffs on critical components and finished lubrication equipment has imparted far-reaching consequences for global supply chains. Manufacturers reliant on imported pumps, sensors, fittings, and lubricant formulations have confronted increased landed costs, prompting many to reevaluate sourcing strategies and renegotiate supplier contracts. This reconfiguration has compelled original equipment manufacturers and distributors to absorb margin pressures, adjust pricing structures, or in certain cases, explore nearshore manufacturing alternatives to mitigate tariff burdens.
As cost structures recalibrate, end users face the dual reality of higher capital expenditures for new installations and elevated operating expenses for retrofit projects. Organizations with aggressive reliability goals must now weigh the economics of extending existing manual lubrication programs against the long-term benefits of condition-based automation. In parallel, procurement teams are diversifying their supplier portfolios to include domestic fabricators and regional distributors capable of providing turnkey assemblies at more favorable duty rates.
Despite these headwinds, forward-looking maintenance teams are leveraging the tariff-driven shakeout as an opportunity to optimize total cost of ownership. By adopting modular lubrication platforms with standardized interfaces, businesses can reduce dependency on proprietary components subject to punitive tariffs. Furthermore, strategic stockpiling of high-turnover parts and the consolidation of lubricant inventories have emerged as effective short-term countermeasures. In this context, the tariff environment is compelling the industry to embrace leaner, more resilient procurement and deployment models, thereby setting new benchmarks for supply chain agility.
Unveiling Market Segments Driving Lubrication Demand
A comprehensive view of the automatic lubrication systems market reveals nuanced demand patterns across multiple segmentation dimensions. When end users in the automotive, construction, energy & power, manufacturing, and mining sectors evaluate lubrication strategies, they prioritize solution profiles uniquely suited to their operational risk factors and asset criticality. Within the automotive space, OEM production lines and aftermarket service centers require distinct configurations to accommodate high-volume chassis assembly lines versus maintenance bays, while residential and non-residential construction projects call for portable grease systems capable of withstanding variable site conditions.
In the energy & power domain, conventional thermal plants demand heavy-grease dispensers for high-load bearings, whereas renewable installations are increasingly adopting oil mist systems to meet environmental compliance standards. Discrete manufacturing floors leverage programmable controllers to synchronize lubrication pulses with robotic arms, whereas continuous process industries favor closed-loop oil circulation systems to ensure homogeneous lubricant quality throughout extended production runs. Surface and underground mining operations contend with extreme dust, moisture, and shock loads that favor sealed, sensor-based pumps with robust filtration capabilities.
The choice of lubricant type further refines purchasing decisions, as calcium-based greases are widely used in heavy equipment joints while lithium-based formulations offer enhanced thermal performance for industrial machines. Mineral oils remain a cost-effective option for general-purpose circulation systems, whereas synthetic oils command a premium in applications requiring extended change intervals and superior oxidation resistance. Component-level segmentation highlights the critical roles of fittings and connectors in maintaining system integrity, gear and piston pumps in modulating flow rates, and flow and pressure sensors in enabling data-driven maintenance. Valve selection-spanning ball, check, and solenoid variants-determines responsiveness and reliability under dynamic load cycles.
Distribution channels mirror the market’s complexity: direct sales teams service large global accounts with customized turnkey packages, distributors provide regional support and aftermarket spares, and online portals offer rapid access to off-the-shelf components and lubricant consumables. Together, these segmentation insights equip stakeholders with a granular understanding of the factors shaping product specifications, supplier evaluations, and go-to-market strategies in the automatic lubrication ecosystem.
This comprehensive research report categorizes the Automatic Lubrication Systems market into clearly defined segments, providing a detailed analysis of emerging trends and precise revenue forecasts to support strategic decision-making.
- End User Industry
- System Type
- Application
- Distribution Channel
- Lubricant Type
- Component
Regional Dynamics Shaping Lubrication Adoption Worldwide
Regional growth trajectories for automatic lubrication systems diverge significantly across the Americas, Europe, Middle East & Africa, and Asia-Pacific, reflecting differential industrial priorities and investment climates. In the Americas, the automotive and mining sectors have been strong adopters of advanced lubrication platforms, driven by a combination of regulatory incentives for emissions reduction and a growing focus on machine reliability. The presence of major equipment manufacturers has also spurred collaborative pilot projects that showcase the operational benefits of condition-based systems in heavy-duty applications.
Across Europe, Middle East & Africa, stringent environmental regulations are accelerating the transition toward oil mist and synthetic lubricant solutions that minimize waste and support circular economy objectives. Renewable energy installations in Northern and Western Europe frequently incorporate integrated lubrication and monitoring packages to ensure high availability of turbines and auxiliary equipment. In the Middle East, rapid infrastructure development has generated demand for robust, dust-resistant lubrication units in construction and power generation, while Africa’s mining projects increasingly rely on turnkey greasing systems to maximize uptime in remote locations.
Asia-Pacific stands out for its diverse manufacturing landscape, where discrete electronics production and capital-intensive process industries coexist with expansive mining operations. China and India, in particular, are witnessing heightened investments in automated assembly lines and predictive maintenance platforms, fostering a vibrant market for networked lubrication solutions. Japan and South Korea continue to innovate in micro-lubrication and precision dispensing technologies, addressing the needs of high-speed machinery in semiconductor and automotive component fabrication. These regional dynamics underscore the importance of localized value propositions and service models to capitalize on evolving industrial priorities.
This comprehensive research report examines key regions that drive the evolution of the Automatic Lubrication Systems market, offering deep insights into regional trends, growth factors, and industry developments that are influencing market performance.
- Americas
- Europe, Middle East & Africa
- Asia-Pacific
Competitive Landscape and Strategic Player Profiles
The competitive landscape for automatic lubrication systems is populated by established engineering giants and specialized technology challengers, each leveraging distinct strengths to capture market share. Leading pump and dispenser manufacturers have broadened their portfolios through targeted acquisitions, integrating sensor and control capabilities into legacy mechanical platforms. These moves have solidified their positions in key verticals such as mining, automotive OEMs, and energy infrastructure, where comprehensive service networks and global footprint remain critical decision factors.
Simultaneously, emerging automation firms are partnering with lubricant formulators and IoT providers to deliver turnkey solutions that combine hardware, software, and data analytics under a unified service contract. These integrators emphasize subscription-based models that lower upfront capital requirements and align maintenance spend with actual equipment usage. Their agility in software development and cloud connectivity contrasts with the more conservative upgrade cycles favored by incumbent players, yielding a bifurcation in go-to-market approaches.
Several companies have introduced machine learning engines that analyze historical lubrication and equipment data to predict component wear and recommend proactive interventions. Meanwhile, alliances between component specialists and industrial distributors have broadened channel reach, enabling faster deployment of spare parts and retrofit kits. Competitive differentiation increasingly hinges on the ability to provide end-to-end lifecycle management, combining reliability engineering services, remote monitoring, and performance benchmarking to demonstrate measurable operational savings. As market demands intensify for integrated, outcome-driven offerings, organizations that bridge the hardware-software divide will command a decisive advantage.
This comprehensive research report delivers an in-depth overview of the principal market players in the Automatic Lubrication Systems market, evaluating their market share, strategic initiatives, and competitive positioning to illuminate the factors shaping the competitive landscape.
- Aktiebolaget SKF
- Graco Inc.
- Lincoln Electric Holdings, Inc.
- Groeneveld Group B.V.
- Bijur Delimon International, Inc.
- Alemite Corporation
- Parker Hannifin Corporation
- Yuken Kogyo Co., Ltd.
- Lubrication Engineers, Inc.
- NSK Ltd.
Strategic Imperatives for Next-Generation Lubrication Leaders
To thrive in the evolving lubrication ecosystem, industry leaders must adopt a multifaceted strategy that prioritizes digital integration, partnerships, and sustainability. First, embedding smart sensors and wireless connectivity into lubrication loops enables real-time performance feedback and seamless integration with existing asset management systems. Decision-makers should pilot condition-based lubrication initiatives on critical equipment to quantify return on investment and build internal advocacy for broader rollouts.
Second, forging partnerships across the value chain accelerates innovation and reduces time to market. Collaborating with lubricant suppliers, IoT platform vendors, and machine tool OEMs creates synergistic ecosystems that deliver comprehensive solutions bundled with predictive analytics and expert support. Cross-industry alliances can unlock new use cases, such as remote service delivery to off-grid mining operations or cloud-based monitoring for distributed manufacturing cells.
Third, embracing sustainable lubricant chemistries and recycling programs not only mitigates environmental risk but also aligns with corporate responsibility goals and increasingly stringent regulations. Leaders should evaluate the lifecycle footprint of grease and oil products, opting for formulations with extended drain intervals and lower volatility. Finally, enhancing organizational readiness through targeted skill development is crucial. Investing in training programs for maintenance personnel on data interpretation, sensor calibration, and digital troubleshooting builds a foundation for continuous improvement and ensures that technology investments translate into tangible throughput gains.
A Rigorous Framework Underpinning Our Market Analysis
The insights presented in this report derive from a rigorous, multi-phased research methodology designed to ensure data accuracy and relevance. Primary research included in-depth interviews with maintenance executives, reliability engineers, and procurement leaders across key end-user industries. These discussions illuminated evolving pain points, investment drivers, and adoption barriers specific to automated lubrication deployments.
Secondary research encompassed comprehensive reviews of industry publications, patent filings, regulatory frameworks, and company financial disclosures. Proprietary databases were leveraged to track historical product launches, partnership announcements, and tariff developments. Data triangulation techniques validated quantitative findings against multiple sources, while expert advisory panels provided contextual interpretation and scenario analysis.
Global coverage spanned all major regions, with bespoke analysis for North America, Europe, Middle East & Africa, and Asia-Pacific. The segmentation framework integrated end-user industry, system type, application, distribution channel, lubricant chemistry, and component architecture. Market dynamics were assessed through qualitative scoring, benchmarking of competitive offerings, and evaluation of emerging technological trends. The methodological rigor ensures that conclusions and recommendations reflect a holistic understanding of the current state and future trajectory of automatic lubrication systems.
Explore AI-driven insights for the Automatic Lubrication Systems market with ResearchAI on our online platform, providing deeper, data-backed market analysis.
Ask ResearchAI anything
World's First Innovative Al for Market Research
Concluding Perspectives on Lubrication Market Trajectories
The journey through the automatic lubrication market reveals a sector at the cusp of transformative growth, propelled by digital innovation and reshaped by external policy forces. As systems evolve from passive dispensers to intelligent platforms, the opportunity to enhance asset reliability and reduce lifecycle costs has never been clearer. Stakeholders equipped with granular segmentation insights and regional intelligence are better positioned to tailor offerings that resonate with end-user priorities.
Competitive dynamics underscore the pivotal role of integrated solutions that blend hardware, software, and expert services. Companies that harness data analytics and foster collaborative ecosystems will set new standards for performance transparency and operational agility. In parallel, the imperative to navigate tariff fluctuations and embrace sustainable lubrication chemistries will define resilience in an increasingly complex global supply environment.
Ultimately, the path forward hinges on strategic investments in smart technologies, distribution agility, and talent development. By leveraging the actionable recommendations in this report, industry participants can chart a course toward sustainable growth and operational excellence within the dynamic landscape of automatic lubrication systems.
This section provides a structured overview of the report, outlining key chapters and topics covered for easy reference in our Automatic Lubrication Systems market comprehensive research report.
- Preface
- Research Methodology
- Executive Summary
- Market Overview
- Market Dynamics
- Market Insights
- Cumulative Impact of United States Tariffs 2025
- Automatic Lubrication Systems Market, by End User Industry
- Automatic Lubrication Systems Market, by System Type
- Automatic Lubrication Systems Market, by Application
- Automatic Lubrication Systems Market, by Distribution Channel
- Automatic Lubrication Systems Market, by Lubricant Type
- Automatic Lubrication Systems Market, by Component
- Americas Automatic Lubrication Systems Market
- Europe, Middle East & Africa Automatic Lubrication Systems Market
- Asia-Pacific Automatic Lubrication Systems Market
- Competitive Landscape
- ResearchAI
- ResearchStatistics
- ResearchContacts
- ResearchArticles
- Appendix
- List of Figures [Total: 28]
- List of Tables [Total: 995 ]
Unlock In-Depth Insights with Ketan Rohom
For a deeper exploration of the trends, opportunities, and strategic imperatives outlined in this report, reach out to Ketan Rohom, Associate Director, Sales & Marketing. Ketan will guide you through tailored packages and complementary insights designed to support your decision making with precision and confidence. Secure your access to the definitive market research on automatic lubrication systems to stay ahead of evolving technologies and maximize operational performance.
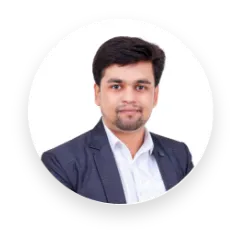
- How big is the Automatic Lubrication Systems Market?
- What is the Automatic Lubrication Systems Market growth?
- When do I get the report?
- In what format does this report get delivered to me?
- How long has 360iResearch been around?
- What if I have a question about your reports?
- Can I share this report with my team?
- Can I use your research in my presentation?