Introduction to the Automatic Metallographic Abrasive Cutter Industry Landscape
Automatic metallographic abrasive cutters serve as the cornerstone of sample preparation in laboratories and manufacturing environments. By delivering precise, reproducible cuts, these instruments enhance the reliability of microscopy and material analysis workflows. As researchers and quality assurance teams demand ever-greater levels of consistency, the shift toward automation has accelerated, positioning advanced abrasive cutters at the forefront of metallographic practices.
This summary examines the underlying drivers, emerging shifts and strategic considerations shaping the current landscape. It outlines how technological advances, regulatory factors and supply chain dynamics are influencing equipment selection and deployment. Additionally, it highlights key segmentation perspectives, regional dynamics and leading vendors whose innovations are redefining operational benchmarks.
With industrial research and development departments, academic institutions and production facilities all leveraging these cutting solutions, decision-makers face a complex matrix of options. Understanding segmentation nuances, tariff implications and regional differences can inform more targeted investments in cutting technology. Furthermore, the integration of digital controls and IoT connectivity is reshaping expectations around remote monitoring and predictive maintenance, fueling demand for next-generation abrasive cutting systems. Stakeholders must evaluate the adaptability of their workflows, the compatibility with diverse material types and the scalability of equipment portfolios. This executive briefing synthesizes these critical factors to provide a comprehensive overview for experts and decision-makers alike.
Transformative Shifts Redefining the Metallographic Abrasive Cutter Sector
Over the past decade, the metallographic abrasive cutter sector has transformed through advances in automation, digitalization and materials science. Fully automated systems are replacing manual techniques in high-volume laboratories, delivering unprecedented throughput and consistency, while semi-automatic configurations balance operator control with operational flexibility in mid-scale facilities.
Digital controls and advanced software have reshaped expectations for data traceability and workflow standardization. Real-time monitoring of cutting parameters and predictive maintenance alerts enable technical teams to minimize downtime and ensure reproducibility. The integration of embedded systems and IoT connectivity now supports remote diagnostics and performance benchmarking across global sites.
Material science breakthroughs have also driven innovation. Cubic boron nitride and synthetic diamond blades extend tool life and improve cut quality in demanding applications. Concurrently, compact high-precision units address specialized needs in sectors such as aerospace and electronics, where microstructural integrity is critical.
Consequently, equipment providers are prioritizing modular architectures that support customization, scalability and future upgrades. This holistic evolution reflects a broader industry pivot toward integrated, data-driven solutions that prioritize consistency, efficiency and adaptability in metallographic sample preparation.
Assessing the Cumulative Impact of 2025 U.S. Tariffs on the Cutter Market
Since early 2025, the United States government implemented tariffs on imported metals and precision machinery components that directly affect metallographic abrasive cutters. These levies have raised the landed cost of critical parts such as motor assemblies, control electronics and blade substrates. In response, OEMs and laboratory equipment suppliers have reevaluated their sourcing strategies, expanding relationships with domestic component manufacturers and exploring alternative international partners.
Tariff-induced cost pressures have translated into pricing adjustments across the supply chain. Distributors and end-users have observed higher unit prices, prompting engineering teams to seek efficiency gains through optimized cutting protocols and extended blade lifecycles. Some laboratories have revisited equipment maintenance schedules to offset incremental expenses. At the same time, strategic inventory management has emerged as a priority, with several organizations increasing buffer stocks of essential spare parts to mitigate future tariff escalations.
Furthermore, the tariff landscape has accelerated conversations around localized manufacturing. By investing in regional assembly operations, certain suppliers aim to circumvent import duties and reduce logistical complexities. This approach also aligns with a broader emphasis on supply chain resilience, as disruptions in global shipping routes and raw material shortages intensify.
Moreover, research laboratories engaged in advanced materials characterization are weighing the trade-off between blade selection and frequency of tool replacement to limit tariff pass-through. Equipment providers are investing in research and development to engineer lower-cost components without sacrificing precision, leveraging alternative alloys and streamlined manufacturing techniques.
Looking ahead, equipment providers and research institutions must navigate this evolving policy environment by balancing cost containment with performance requirements. Collaborative partnerships between cutter manufacturers and component suppliers will be crucial in engineering cost-effective, high-precision solutions that maintain cutting standards without compromise.
Key Segmentation Insights for the Metallographic Abrasive Cutter Market
An in-depth segmentation analysis reveals multiple dimensions for strategic positioning. The Product Type classification distinguishes fully automatic, manual and semi-automatic cutters, each addressing different workflow preferences. Cutting Capacity spans small tabletop units for low-volume research, medium systems for moderate throughput and large platforms tailored to heavy-duty industrial needs. Application Areas include academic research agendas, industrial R&D programs, material testing laboratories, mass production facilities and specialized research institutes.
End-User Industries cover the aerospace sector, where ultra-precise sectioning is mandatory; the automotive field emphasizing component durability testing; the electronics and electrical industry requiring contamination-free cuts; and the metallurgical industry relying on consistent sample preparation for process optimization. Technology segmentation differentiates analog systems, digital controllers offering programmable processes and solutions integrating embedded systems and IoT connectivity for remote monitoring and data analytics.
Material Types encompass hard ceramics, a range of thermoplastics and thermoset plastics, diverse metals and general-purpose plastics. Blade Type selection influences performance, with abrasive wheels for general purpose, cubic boron nitride blades for extended life in aggressive conditions and diamond blades for ultra-fine finishes. Mode of Operation considerations range from dry cutting to wet cutting with water-based or oil-based coolant systems. Distribution Channels include direct sales relationships, networks of distributors and dealers, and expanding online platforms, while Customer Type segmentation spans commercial enterprises, small and large enterprises, individual users and industrial users each with distinct procurement criteria. Aligning product development and marketing strategies with these segmentation criteria enables more targeted engagement and competitive differentiation.
This comprehensive research report categorizes the Automatic Metallographic Abrasive Cutter market into clearly defined segments, providing a detailed analysis of emerging trends and precise revenue forecasts to support strategic decision-making.
- Product Type
- Cutting Capacity
- Application Areas
- End-User Industries
- Technology
- Material Types
- Blade Type
- Mode Of Operation
- Distribution Channel
- Customer Type
Regional Dynamics Shaping the Cutter Industry Across Global Markets
Regional dynamics critically influence equipment adoption and investment trends. In the Americas, a robust industrial R&D ecosystem and stringent quality standards have fueled widespread deployment of automated abrasive cutters, supported by strong partnerships between equipment suppliers and leading universities. North American laboratories benefit from advanced service networks and localized technical support, which accelerate equipment uptime and lifecycle management.
In Europe, Middle East and Africa, diverse regulatory frameworks and varied infrastructure maturity create a mosaic of opportunities. Western European markets emphasize digital integration and sustainability, driving demand for energy-efficient cutting systems with minimal coolant waste. Meanwhile, emerging economies in the Middle East and Africa prioritize cost-effective solutions and aftermarket support, presenting growth avenues for suppliers adept at flexible financing models and turnkey service offerings.
Asia-Pacific remains the fastest-evolving region, characterized by significant investments in semiconductor manufacturing, automotive assembly and aerospace engineering. Countries such as China, Japan, South Korea and India are expanding metallographic research capabilities, prompting suppliers to introduce compact, high-precision cutters optimized for space-constrained labs. Strategic alliances with local agents and region-tailored training programs have become key success factors in this dynamic market.
This comprehensive research report examines key regions that drive the evolution of the Automatic Metallographic Abrasive Cutter market, offering deep insights into regional trends, growth factors, and industry developments that are influencing market performance.
- Americas
- Asia-Pacific
- Europe, Middle East & Africa
Leading Players Driving Innovation in the Metallographic Abrasive Cutter Space
Industry leadership in metallographic abrasive cutting is shaped by a mix of global conglomerates and specialized innovators. Aka-Pi Sp. z o.o. has established a reputation for bespoke automation platforms that meet niche laboratory requirements, while Allied High Tech Products, Inc. offers modular sample-preparation systems that adapt to evolving workflow demands. ATM GmbH (Qness GmbH) specializes in space-efficient, fully automated cutters designed for continuous operation in high-throughput environments, and Buehler (a division of Illinois Tool Works Inc.) leverages integrated workflows combining cutting, mounting and polishing for end-to-end efficiency.
Extec Corp and Femi Tools SpA focus on precision blade engineering, delivering abrasive wheels that extend life cycles and improve cut quality. Forcipol Instruments Inc. and Kemet International Ltd excel in abrasive consumables, supplying a broad range of cutting products. Laizhou Weiyi Experiment Machinery Manufacturing Co., Ltd. and LECO Corporation provide cost-effective platforms and global service networks, while Metkon Instruments Inc. and Micracut Manufacturing Company develop advanced diamond and fine-grain abrasive cutting solutions. Struers A/S leads with software-driven, connected systems that enable data capture and quality control across diverse laboratory settings. Together, these companies drive continuous progress through targeted R&D, strategic collaborations and a commitment to elevating precision and productivity in metallographic sample preparation.
This comprehensive research report delivers an in-depth overview of the principal market players in the Automatic Metallographic Abrasive Cutter market, evaluating their market share, strategic initiatives, and competitive positioning to illuminate the factors shaping the competitive landscape.
- Aka-Pi Sp. z o.o.
- Allied High Tech Products, Inc.
- ATM GmbH (Qness GmbH)
- Buehler (a division of Illinois Tool Works Inc.)
- Extec Corp
- Femi Tools SpA
- Forcipol Instruments Inc.
- Kemet International Ltd
- Laizhou Weiyi Experiment Machinery Manufacturing Co., Ltd.
- LECO Corporation
- Metkon Instruments Inc.
- Micracut Manufacturing Company
- Struers A/S
Actionable Recommendations for Industry Leadership and Growth
To navigate the evolving landscape of metallographic abrasive cutting and secure a competitive edge, industry leaders should consider the following strategic actions:
Prioritize digital integration by evaluating current equipment portfolios for compatibility with advanced controls, IoT connectivity and predictive maintenance capabilities. Upgrading to systems that support remote monitoring can reduce unplanned downtime and enhance data-driven decision making.
Diversify supply chain partnerships in light of tariff fluctuations and material shortages by establishing relationships with multiple component suppliers-domestic and international-to ensure continuity of part availability and cost stability. Nearshore or onshore manufacturing collaborations can mitigate import duties.
Leverage segmentation insights by tailoring product development and marketing initiatives to specific use cases, from high-precision diamond blade solutions for aerospace applications to cost-effective manual cutters for academic research. Segment-driven strategies can unlock new revenue opportunities and strengthen brand positioning.
Expand regional footprint strategically: in the Americas, deepen service capabilities and technical support networks; in Europe, Middle East and Africa, emphasize sustainable, energy-efficient systems; in Asia-Pacific, partner with local agents and offer training programs to accelerate adoption.
Invest in R&D for sustainable practices by developing cutting processes that minimize coolant consumption and optimize blade lifecycles, addressing both cost and environmental considerations. Explore alternative materials and resource-efficient manufacturing techniques.
Foster cross-industry collaborations by engaging end-users in automotive, electronics and metallurgical sectors to co-innovate custom solutions that integrate sample preparation with broader quality control systems.
Monitor policy developments proactively by establishing an internal task force to track regulatory changes, tariff schedules and trade agreements that may affect import costs or compliance requirements. Proactive policy intelligence enables timely adjustments to pricing and sourcing strategies.
Enhance customer engagement through educational resources, application workshops and virtual demonstrations to showcase system capabilities and best practices. A strong customer training program reduces onboarding time and fosters long-term loyalty.
Explore AI-driven insights for the Automatic Metallographic Abrasive Cutter market with ResearchAI on our online platform, providing deeper, data-backed market analysis.
Ask ResearchAI anything
World's First Innovative Al for Market Research
Conclusion and Strategic Takeaways for Stakeholders
Metallographic abrasive cutters have evolved into sophisticated, integrated systems that underpin critical research and quality assurance initiatives across multiple industries. Technological advances in automation, digital controls and material science have redefined expectations for precision, consistency and operational efficiency. At the same time, policy shifts such as U.S. tariffs and regional demand differentials underscore the need for resilient supply chains and tailored market strategies.
By leveraging granular segmentation insights, understanding regional dynamics and engaging with leading solution providers, stakeholders can make informed decisions that align with both immediate requirements and long-term objectives. The recommendations outlined in this briefing offer a roadmap for equipment selection, supply chain optimization and strategic partnerships. As the industry continues to innovate, proactive leaders will be best positioned to harness emerging opportunities and maintain a competitive advantage in metallographic sample preparation.
This section provides a structured overview of the report, outlining key chapters and topics covered for easy reference in our Automatic Metallographic Abrasive Cutter market comprehensive research report.
- Preface
- Research Methodology
- Executive Summary
- Market Overview
- Market Dynamics
- Market Insights
- Cumulative Impact of United States Tariffs 2025
- Automatic Metallographic Abrasive Cutter Market, by Product Type
- Automatic Metallographic Abrasive Cutter Market, by Cutting Capacity
- Automatic Metallographic Abrasive Cutter Market, by Application Areas
- Automatic Metallographic Abrasive Cutter Market, by End-User Industries
- Automatic Metallographic Abrasive Cutter Market, by Technology
- Automatic Metallographic Abrasive Cutter Market, by Material Types
- Automatic Metallographic Abrasive Cutter Market, by Blade Type
- Automatic Metallographic Abrasive Cutter Market, by Mode Of Operation
- Automatic Metallographic Abrasive Cutter Market, by Distribution Channel
- Automatic Metallographic Abrasive Cutter Market, by Customer Type
- Americas Automatic Metallographic Abrasive Cutter Market
- Asia-Pacific Automatic Metallographic Abrasive Cutter Market
- Europe, Middle East & Africa Automatic Metallographic Abrasive Cutter Market
- Competitive Landscape
- ResearchAI
- ResearchStatistics
- ResearchContacts
- ResearchArticles
- Appendix
- List of Figures [Total: 36]
- List of Tables [Total: 465 ]
Connect with Ketan Rohom to Acquire the Comprehensive Market Report
To access the full market research report and gain deeper insights into strategic opportunities, reach out to Ketan Rohom, Associate Director, Sales & Marketing. He can guide you through customized research packages and subscription options tailored to your organization’s needs. Connect now to secure comprehensive analysis that will inform your strategic planning and investment decisions in the automatic metallographic abrasive cutter market.
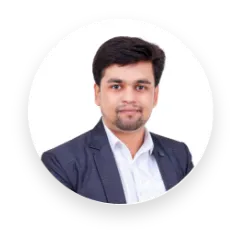
- When do I get the report?
- In what format does this report get delivered to me?
- How long has 360iResearch been around?
- What if I have a question about your reports?
- Can I share this report with my team?
- Can I use your research in my presentation?