Introduction to Automatic Welding Carriage Solutions
Automatic welding carriages have emerged as vital enablers of precision, consistency and throughput across modern fabrication environments. These self-propelled platforms guide welding torches or heads along predefined paths, reducing operator fatigue, minimizing dimensional errors and unlocking repeatable high-quality joints. As manufacturing demands evolve under pressures of cost containment, skilled labor shortages and stringent quality requirements, welding carriages provide a compelling solution. They bridge the gap between manual flexibility and full robotic automation, making them indispensable in industries ranging from automotive and aerospace to heavy machinery and shipbuilding. By unifying motion control, sensing and power delivery into a compact, mobile unit, these carriages drive productivity gains while ensuring regulatory compliance and operator safety. This introduction sets the stage for an in-depth exploration of the market dynamics, technological innovations and strategic imperatives shaping the future of automatic welding carriages.
Transformative Shifts in the Automatic Welding Carriage Landscape
The landscape of automatic welding carriages is undergoing transformative shifts driven by convergence of Industry 4.0, advanced materials and environmental mandates. First, digital integration has become ubiquitous: real-time data acquisition, cloud connectivity and AI-assisted defect detection are redefining process control. Closed-loop feedback systems now adjust welding parameters on the fly, responding to seam irregularities or material variations with precision. Concurrently, collaborative robotics have extended carriage versatility, enabling seamless handoffs between human operators and automated systems for complex or intermittent welds.
Second, material science breakthroughs-such as high-strength alloys and composite reinforcements-have spurred the need for specialized carriage hardware capable of multi-axis articulation, adaptive torch angles and force compensation. Manufacturers are leveraging compact actuators and lightweight carbon-fiber frames to maintain rigidity while enhancing portability.
Third, sustainability mandates are reshaping energy profiles: carriages equipped with regenerative braking, low-loss drives and smart sleep modes can now deliver up to 30 percent higher energy efficiency in continuous operation. This aligns with broader corporate ESG objectives and delivers cost savings in high-throughput environments.
Together, these shifts underscore a broader ecosystem transition in which automatic welding carriages no longer serve as mere fixtures but as intelligent, connected nodes within a digitally orchestrated production line.
Cumulative Impact of U.S. Tariffs 2025 on Automatic Welding Carriage
The cumulative impact of U.S. tariffs effective 2025 is reshaping sourcing strategies, component costs and competitive positioning for automatic welding carriage providers. Steel, aluminum extrusions, precision sensors and electronic controllers-all critical inputs-now incur elevated import duties, introducing a complex cost premium. As a result, companies are diversifying supply bases, shifting to regional suppliers in North America or near-shoring key machining and assembly operations to mitigate exposure.
This tariff environment has also accelerated local content requirements, compelling OEMs to embed greater domestic value in their solutions. Some manufacturers are negotiating consortia or joint ventures to secure preferential tariff treatment under trade agreements into which regional partners hold equity stakes. Parallel to procurement tactics, R&D road maps have pivoted to emphasize modular designs that can accommodate alternative materials or locally sourced subsystems without sacrificing performance.
In parallel, end users are conducting total cost of ownership analyses that internalize tariff-driven price fluctuations. As capital budgets realign, providers offering robust service networks and retrofit packages for existing carriages gain an edge in a market increasingly sensitive to acquisition costs and long-term maintenance outlays.
Key Segmentation Insights for the Automatic Welding Carriage Market
Deconstructing the market through segmentation reveals nuanced adoption patterns and technology preferences. When evaluated by carriage mechanism, systems offering automatic adjustment command premium insights due to their closed-loop controls, while manual override variants retain appeal in low-volume, high-flexibility scenarios and precision positioning models dominate highly regulated sectors. Examining the welding process dimension underscores a bifurcation: arc welding remains the workhorse-further refined into MIG and TIG configurations-whereas friction stir, laser and resistance welding (inclusive of seam and spot modalities) serve niche applications that demand specialized carriage rigidity and thermal management.
A manufacturing sector lens highlights that aerospace exploits high-precision carriages with multi-axis articulation, automotive emphasizes cycle time reduction via integrated robotics, construction machinery leverages robustness to manage heavy-gauge steel, and shipbuilding prioritizes extended travel lengths and corrosion-resilient materials. Control system segmentation uncovers that advanced sensing solutions enable adaptive path correction, human-machine interfaces improve operator oversight and programmable logic controllers deliver deterministic cycle execution.
Turning to energy efficiency, high-throughput configurations achieve rapid weld sequences with optimized power draws, low energy consumption variants focus on minimal heat-affected zones, and sustainable operation packages integrate renewable energy compatibility and carbon monitoring. Finally, equipment integration trends favor modular platforms that scale with line capacity and robotic integration models that facilitate seamless handoffs between fixed robots and mobile carriages. These layered insights inform tailored go-to-market strategies and pinpoint investment priorities.
This comprehensive research report categorizes the Automatic Welding Carriage market into clearly defined segments, providing a detailed analysis of emerging trends and precise revenue forecasts to support strategic decision-making.
- Carriage Mechanism
- Welding Process
- Manufacturing Sector
- Control System
- Energy Efficiency
- Equipment Integration
Key Regional Insights for Automatic Welding Carriage Adoption
Regional dynamics play a pivotal role in adoption trajectories and value perceptions. In the Americas, a robust automotive and aerospace supply chain fuels demand for automated welding carriages that can integrate easily with existing assembly lines and meet stringent safety and quality standards; service networks concentrated in the United States and Mexico further lower downtime risks. Moving eastward to Europe, Middle East & Africa, varied regulatory regimes and a strong shipbuilding base in countries like Germany and Turkey emphasize corrosion-resistant carriage materials, while emerging manufacturers in the Gulf Cooperation Council pursue cost-competitive systems calibrated for high temperatures.
Across Asia-Pacific, the region’s expansive electronics, automotive and general manufacturing hubs drive significant scale. Providers tailor lightweight, precision positioning carriages for Japanese and South Korean factories, while Chinese integrators favor automated adjustment platforms that can be locally assembled under aggressive cost targets. Moreover, Australia and Southeast Asia are witnessing increased uptake of modular platforms and energy-efficient variants as mining, infrastructure and renewable energy projects seek reliable on-site welding solutions. Understanding these regional nuances allows suppliers to craft differentiated value propositions and align channel investments.
This comprehensive research report examines key regions that drive the evolution of the Automatic Welding Carriage market, offering deep insights into regional trends, growth factors, and industry developments that are influencing market performance.
- Americas
- Asia-Pacific
- Europe, Middle East & Africa
Key Company Insights Driving the Automatic Welding Carriage Market
Leading enterprises are shaping the competitive landscape through continuous product innovation, strategic partnerships and expanded service portfolios. ABB Ltd. and Siemens Welding Systems GmbH continue to pioneer advanced sensing integration and digital twin calibration, while KUKA AG and Yaskawa Electric Corporation emphasize collaborative robotic integration that merges carriage mobility with articulated arm flexibility. Bosch Welding Technologies and Trumpf Group Welding Systems leverage their systems engineering prowess to deliver turnkey solutions, and Fronius International GmbH and Panasonic Welding Solutions Inc. focus on energy recovery and pulse-waveform optimization.
Specialized players such as Adarc Welding Innovations Ltd., Advanced Weld Carriage Systems Inc. and Elite Weld Solutions differentiate through modular carriage platforms and bespoke automation packages, whereas Comau Welding Systems, Robotic Weld Solutions Inc. and Universal Robotic Welding Inc. embed human-machine interfaces to streamline operator interactions. Global Weld Systems and Precision Automation Welders excel in retrofitting legacy equipment, and Innovative Weld Solutions and NEXTGEN Weld Automation specialize in tailor-made workflows for high-mix, low-volume producers.
On the consumables and accessory front, ESAB Corporation, Lincoln Electric Holdings, Inc. and Hobart Brothers LLC lead in service network density and welding wire optimization, while Miller Electric Manufacturing and Lincoln Tech Welding Solutions support rapid deployment with standardized control libraries. Meanwhile, Mitsubishi Electric Welding Solutions and Kawasaki Robotics Welding Solutions offer comprehensive control system integration, and Cameron Welding and Automation, Fastenal Welding Systems and OTC Global LLC provide extensive distribution and aftermarket support. Additional entrants like Gibson Welding Corporation, Global Weld Systems, Mecademic Robotics Welding, Mazak Corporation Welding Solutions, NIL Welding Automation, Precision Weld Tech Inc. and Toyota Welding Technologies underscore the increasing fragmentation and specialization in niche applications-from shipbuilding to aerospace. These collective efforts drive innovation cycles, expand use cases and elevate service expectations across the automatic welding carriage market.
This comprehensive research report delivers an in-depth overview of the principal market players in the Automatic Welding Carriage market, evaluating their market share, strategic initiatives, and competitive positioning to illuminate the factors shaping the competitive landscape.
- ABB Ltd.
- Adarc Welding Innovations Ltd.
- Advanced Weld Carriage Systems Inc.
- Amazon Welding Technology Solutions
- Bosch Welding Technologies
- Cameron Welding and Automation
- Comau Welding Systems
- Danfoss Welding Automation
- Elite Weld Solutions
- ESAB Corporation
- EWM AG Welding Solutions
- Fastenal Welding Systems
- Fronius International GmbH
- Gibson Welding Corporation
- Global Weld Systems
- Hobart Brothers LLC
- Innovative Weld Solutions
- Kawasaki Robotics Welding Solutions
- KUKA AG
- Lincoln Electric Holdings, Inc.
- Lincoln Tech Welding Solutions
- Mazak Corporation Welding Solutions
- Mecademic Robotics Welding
- Miller Electric Manufacturing
- Mitsubishi Electric Welding Solutions
- NextGen Weld Automation
- NIL Welding Automation
- OTC Global LLC
- Panasonic Welding Solutions Inc.
- Precision Automation Welders
- Precision Weld Tech Inc.
- Robotic Weld Solutions Inc.
- SIEMENS Welding Systems GmbH
- Toyota Welding Technologies
- Trumpf Group Welding Systems
- Universal Robotic Welding Inc.
- Yaskawa Electric Corporation
Actionable Recommendations for Industry Leaders
To remain competitive and resilient, industry leaders should adopt a proactive, multi-pronged strategy. First, prioritize R&D investments in adaptive control algorithms and advanced sensing modules that enable real-time weld quality optimization. Second, develop flexible supply chains by forging partnerships with regional component manufacturers, thereby reducing tariff exposure and ensuring continuity of critical parts. Third, offer modular upgrade paths for legacy carriages-encompassing energy efficiency packages and digital connectivity retrofits-to capture aftermarket revenue and deepen customer relationships.
Fourth, collaborate with system integrators and end users to pilot robotic integration frameworks, demonstrating seamless orchestration between fixed and mobile assets. Fifth, design service agreements that bundle predictive maintenance, remote diagnostics and operator training to mitigate downtime and strengthen long-term contracts. Finally, align product road maps with sustainability targets by incorporating low-emission power supplies and recyclable materials, thereby addressing both regulatory compliance and corporate ESG goals.
Explore AI-driven insights for the Automatic Welding Carriage market with ResearchAI on our online platform, providing deeper, data-backed market analysis.
Ask ResearchAI anything
World's First Innovative Al for Market Research
Conclusion: Navigating the Future of Welding Carriage Automation
Automatic welding carriages are evolving from standalone devices into intelligent, networked components of advanced manufacturing cells. Technological convergence in digitalization, materials and energy management is driving unprecedented gains in precision, throughput and cost efficiency. Meanwhile, external factors such as U.S. tariffs, regional market nuances and intensifying competition among specialized and diversified suppliers are reshaping strategic imperatives. By leveraging granular segmentation insights-spanning carriage mechanism, welding process, sector application, control architecture, energy profile and integration modality-manufacturers can tailor offerings to distinct customer needs.
Simultaneously, understanding regional adoption patterns across the Americas, Europe, Middle East & Africa and Asia-Pacific allows for optimized channel deployment and localized service models. A clear-eyed analysis of leading companies highlights best practices in modular design, robotic integration, aftermarket services and sustainability. Armed with these insights, executives can make informed decisions about product road maps, partnerships and operational investments that drive differentiation in a rapidly shifting competitive arena.
This section provides a structured overview of the report, outlining key chapters and topics covered for easy reference in our Automatic Welding Carriage market comprehensive research report.
- Preface
- Research Methodology
- Executive Summary
- Market Overview
- Market Dynamics
- Market Insights
- Cumulative Impact of United States Tariffs 2025
- Automatic Welding Carriage Market, by Carriage Mechanism
- Automatic Welding Carriage Market, by Welding Process
- Automatic Welding Carriage Market, by Manufacturing Sector
- Automatic Welding Carriage Market, by Control System
- Automatic Welding Carriage Market, by Energy Efficiency
- Automatic Welding Carriage Market, by Equipment Integration
- Americas Automatic Welding Carriage Market
- Asia-Pacific Automatic Welding Carriage Market
- Europe, Middle East & Africa Automatic Welding Carriage Market
- Competitive Landscape
- ResearchAI
- ResearchStatistics
- ResearchContacts
- ResearchArticles
- Appendix
- List of Figures [Total: 28]
- List of Tables [Total: 370 ]
Call to Action: Secure Your In-Depth Market Research Report
Ready to capitalize on these insights and gain a competitive edge? Contact Ketan Rohom, Associate Director, Sales & Marketing, to purchase the comprehensive market research report and unlock detailed analyses, proprietary data and strategic guidance tailored to your business objectives.
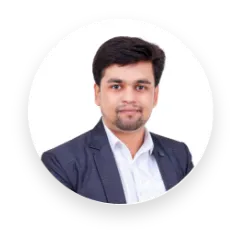
- When do I get the report?
- In what format does this report get delivered to me?
- How long has 360iResearch been around?
- What if I have a question about your reports?
- Can I share this report with my team?
- Can I use your research in my presentation?