The Automobile OEM In-plant Logistics Market size was estimated at USD 15.22 billion in 2024 and expected to reach USD 16.32 billion in 2025, at a CAGR 7.53% to reach USD 23.54 billion by 2030.

Setting the Stage for Next-Generation In-Plant Logistics
In an era defined by rapid technological evolution and intensifying competitive pressures, automobile manufacturers face unprecedented challenges in optimizing in-plant logistics. Production efficiency, inventory accuracy, and seamless material flow have become nonnegotiable elements in the pursuit of operational excellence. As vehicle complexity escalates and customer expectations shift toward personalized configurations, in-plant logistics emerges as a vital determinant of profitability and time-to-market. This executive summary establishes the foundational context for understanding how digitization, automation, and strategic alignment catalyze transformative improvements within automotive manufacturing campuses.
By exploring core trends, tariff implications, market segments, regional dynamics, and leading players, we deliver a holistic view of the in-plant logistics landscape. Our objective is to equip industry leaders, plant managers, and supply chain executives with the analytical frameworks and practical recommendations necessary to navigate uncertainty, harness emerging opportunities, and future-proof their logistical operations.
Emerging Forces Reshaping In-Plant Logistics Dynamics
The in-plant logistics arena is undergoing a paradigm shift propelled by several converging forces. Intelligent automation now transcends simple mechanization as robotics and autonomous guided vehicles collaborate with warehouse management software to eliminate manual bottlenecks and optimize material handling pathways. Concurrently, the Internet of Things (IoT) infuses real-time visibility into every pallet and component, enabling predictive maintenance of conveyors and dynamic slotting of high-velocity parts. Artificial intelligence and machine learning algorithms continuously refine routing and scheduling, offering a agility once reserved for research labs.
Sustainability mandates and circular economy principles further drive innovation as OEMs seek recyclable packaging, energy-efficient handling equipment, and digital twin simulations to reduce waste. At the same time, cross-functional integration of planning, production, and logistics teams accelerates decision cycles and fosters a culture of continuous improvement. Together, these developments are rewriting the rules of engagement, elevating in-plant logistics from a cost center to a strategic enabler of resilience and responsiveness.
Assessing the Ripple Effects of 2025 US Tariffs on In-Plant Logistics
The introduction of new United States tariffs in 2025 reverberates across global supply chains, significantly altering cost structures and sourcing strategies within automobile in-plant logistics. Tariff escalations on steel and aluminum imports have increased raw material expenses, prompting OEMs to renegotiate contracts and explore alternative suppliers. In turn, this has elevated the importance of logistics agility as plants adjust inbound shipments to mitigate buffer stock while preserving just-in-time workflows.
Beyond raw materials, import duties on electronic subassemblies have pressured pricing for sensors, control units, and WMS hardware, compelling logistics teams to reengineer inventory policies. Some manufacturers have relocated low-value, high-footprint operations back to domestic facilities to sidestep tariffs, amplifying the need for robust in-plant systems capable of absorbing variable volumes. These shifts underscore the critical role of data-driven forecasting and scenario modeling in maintaining throughput and avoiding costly disruptions.
Deep Dives into Key Segmentation Insights
A nuanced comprehension of market segments reveals where investments and performance gains are most impactful. When examining components, hardware equipment such as automated guided vehicles, automated storage and retrieval systems, conveyor lines, cranes and hoists, forklifts and pallet jacks, robotic arms and dedicated warehouse management system hardware form the backbone of mechanized material flow. Complementary software solutions and professional services ensure seamless integration, real-time monitoring and continuous optimization of these assets.
Service models span inventory management through just-in-time delivery orchestration, material handling and transportation services, packaging and labelling operations, returnable packaging management solutions, and warehousing and storage support. Each service layer enhances precision in stock levels, minimizes lead times, and sustains high utilization rates on the shop floor.
Levels of automation range from fully automated logistics environments, where end-to-end processes occur with minimal human intervention, to semi-automated facilities that blend manual oversight with mechanized assistance, and purely manual logistics setups where human operatives handle primary material movement. This spectrum captures the progressive journey toward increased throughput and reduced error rates.
Logistics modes distinguish inbound flows of raw materials and components, internal logistics that shuttle parts between production cells and assembly lines, and outbound logistics responsible for finished-vehicle dispatch. Optimizing each mode requires tailored layouts, handling equipment and orchestrated handoffs across functional boundaries.
Automotive component types such as body parts, electrical systems, engine modules, interior assemblies, suspension systems, transmission components, and wheels and tires each carry distinct handling requirements. Temperature sensitivities, weight tolerances and batch sizes influence the design of storage and transport processes within the plant.
End-users segment into aftermarket parts and accessories manufacturers, commercial vehicle OEMs and passenger vehicle OEMs. Aftermarket operations demand rapid replenishment cycles and multiple SKU variants, while large-volume commercial and passenger vehicle assembly plants prioritize standardized flow paths and high-velocity throughput. Understanding these segment dynamics guides capital allocation and technology adoption strategies.
This comprehensive research report categorizes the Automobile OEM In-plant Logistics market into clearly defined segments, providing a detailed analysis of emerging trends and precise revenue forecasts to support strategic decision-making.
- Component
- Service Model Type
- Level of Automation
- Logistics Mode
- Automotive Component Type
- End-Users
Regional Dynamics Steering In-Plant Logistics Evolution
Geography shapes the contours of in-plant logistics performance and investment priorities. In the Americas, a strong emphasis on lean manufacturing principles converges with increasing automation adoption. Domestic production and nearshoring trends bolster investment in warehouse management systems and autonomous material transport solutions, particularly in regions with emerging EV manufacturing hubs. Localized supply chains benefit from shorter transit distances, allowing just-in-time strategies to flourish within sprawling assembly plants.
Within Europe, Middle East and Africa, regulatory initiatives targeting carbon emissions in manufacturing drives demand for energy-efficient equipment and circular packaging solutions. OEMs navigate complex cross-border trade regulations while harmonizing digital standards across multiple facilities. High labor costs in Western European plants accelerate the shift toward robotic arms and automated guided vehicles that enhance throughput without compromising ergonomic safety.
Asia-Pacific represents a diverse landscape, where some markets still rely heavily on manual handling while others leapfrog to fully automated logistics ecosystems. Rapid industrialization and infrastructure modernization fuel expansion of greenfield facilities optimized for vertical integration of production and logistics. The region’s competitive labor market, coupled with government incentives for smart manufacturing, propels both domestic and multinational OEMs to invest in sophisticated material flow networks.
This comprehensive research report examines key regions that drive the evolution of the Automobile OEM In-plant Logistics market, offering deep insights into regional trends, growth factors, and industry developments that are influencing market performance.
- Americas
- Europe, Middle East & Africa
- Asia-Pacific
Leading Industry Players Driving Logistics Innovations
A select group of technology providers and integrators are pioneering advanced solutions that redefine operational norms. Leading robotics manufacturers continuously refine their AGV fleets, offering modular platforms capable of navigating changing plant layouts and integrating seamlessly with vision systems and digital twins. Warehouse management system vendors leverage cloud-based architectures to deliver scalable, secure data environments that support remote monitoring and analytics.
Systems integrators blend domain expertise in automotive production with deep technical know-how, enabling end-to-end deployment of orchestrated material flow networks. They collaborate closely with OEM IT departments to align on cybersecurity, data governance and enterprise resource planning interfaces. Service providers are expanding their portfolios to include outcome-based contracts, aligning their compensation with tangible improvements in throughput, inventory accuracy and downtime reduction. This evolution blurs the lines between capital expenditure and operational expenditure models, offering greater financial flexibility to manufacturing organizations.
This comprehensive research report delivers an in-depth overview of the principal market players in the Automobile OEM In-plant Logistics market, evaluating their market share, strategic initiatives, and competitive positioning to illuminate the factors shaping the competitive landscape.
- Accenture PLC
- AIT Worldwide Logistics, Inc.
- BLG LOGISTICS GROUP AG & Co. KG
- BR Williams Trucking, Inc.
- CEVA Logistics SA
- Daifuku Co., Ltd.
- DHL Group
- DP World Limited
- DSV A/S
- GXO Logistics, Inc.
- Handling Specialty Manufacturing Ltd.
- Hellmann Worldwide Logistics SE & Co. KG
- Hyster-Yale Materials Handling, Inc.
- John Bean Technologies Corporation
- Joloda Hydraroll Limited
- Kintetsu World Express, Inc.
- Kion Group AG
- Kuka AG
- Kühne + Nagel Group
- LTIMindtree Limited
- Penske Truck Leasing Co., L.P.
- Rhenus SE & Co. KG
- Rudolph and Hellmann Automotive
- Ryder System, Inc
- Schnellecke Logistics SE
- SEKO Worldwide, LLC
- SF Holding Co., Ltd.
- Sinotrans Limited
- SSI SCHÄFER GmbH & Co KG
- TCI Supply Chain Solutions
- Tech Mahindra Limited
- Toyota Industries Corporation
Strategic Actions to Future-Proof Logistics Operations
To thrive amid mounting complexity, industry leaders must adopt a multifaceted strategic agenda. They should begin by mapping end-to-end material flows with digital twins, identifying choke points and validating optimization scenarios before committing to capital investments. Investing in modular hardware platforms that can be repurposed across lines mitigates the risk of technology obsolescence as product portfolios evolve.
Cultivating cross-functional teams that unite logistics, production, quality and IT fosters a holistic mindset and accelerates continuous improvement cycles. Embedding predictive analytics into routine maintenance schedules ensures equipment uptime and alerts stakeholders to emerging anomalies. It is also critical to reassess supplier partnerships, favoring those that offer bundled services encompassing packaging, labelling and returnable packaging management to simplify coordination.
Finally, executives should establish a governance structure that tracks key performance indicators tied to throughput gains, cost per move, and carbon emissions. By aligning incentive structures with sustainability and efficiency goals, organizations can sustain momentum and secure executive buy-in for successive improvement waves.
Robust Research Methodology Underpinning Our Analysis
Our analysis draws on a rigorous methodology combining primary and secondary research. Interviews were conducted with plant managers, supply chain directors, and technology specialists across leading OEMs to validate market needs, pain points, and adoption barriers. Data from industry associations, regulatory bodies, and trade publications provided contextual background on tariff changes, standards, and regional investment trends.
We examined case studies of greenfield and brownfield implementations, analyzing quantitative results on throughput improvements, error rate reductions, and total cost of ownership metrics. Technology roadmaps and product briefs from major hardware and software suppliers were assessed to identify emerging capabilities and maturity curves. Statistical triangulation ensured forecasted trends aligned with both qualitative insights and macroeconomic indicators.
A dedicated peer review panel of automotive logistics experts evaluated our findings, offering feedback that refined segmentation frameworks, regional analyses and actionable recommendations. This iterative process ensures the insights presented are robust, objective and tailored to the strategic imperatives of in-plant logistics stakeholders.
Explore AI-driven insights for the Automobile OEM In-plant Logistics market with ResearchAI on our online platform, providing deeper, data-backed market analysis.
Ask ResearchAI anything
World's First Innovative Al for Market Research
Synthesis and Path Forward in In-Plant Logistics
In-plant logistics stands at the intersection of traditional material handling and cutting-edge digital transformation. The evolving landscape demands that OEMs embrace automation, data visibility and process integration to remain competitive. Our exploration of tariffs, segmentation dynamics, regional distinctions and leading technology providers confirms that strategic alignment across functions is essential.
The cumulative evidence underscores the importance of a measured yet ambitious approach: optimize existing systems through data-driven improvements while selectively investing in next-generation hardware and software. By doing so, manufacturers can achieve short-term cost efficiencies and build a foundation for sustained agility amid shifting trade policies, evolving regulatory requirements and market demands.
The path forward lies in continuous experimentation, cross-disciplinary collaboration, and unwavering commitment to performance metrics that balance productivity, quality and sustainability. Organizations that navigate this journey effectively will unlock new levels of operational excellence and secure a competitive edge.
This section provides a structured overview of the report, outlining key chapters and topics covered for easy reference in our Automobile OEM In-plant Logistics market comprehensive research report.
- Preface
- Research Methodology
- Executive Summary
- Market Overview
- Market Dynamics
- Market Insights
- Cumulative Impact of United States Tariffs 2025
- Automobile OEM In-plant Logistics Market, by Component
- Automobile OEM In-plant Logistics Market, by Service Model Type
- Automobile OEM In-plant Logistics Market, by Level of Automation
- Automobile OEM In-plant Logistics Market, by Logistics Mode
- Automobile OEM In-plant Logistics Market, by Automotive Component Type
- Automobile OEM In-plant Logistics Market, by End-Users
- Americas Automobile OEM In-plant Logistics Market
- Europe, Middle East & Africa Automobile OEM In-plant Logistics Market
- Asia-Pacific Automobile OEM In-plant Logistics Market
- Competitive Landscape
- ResearchAI
- ResearchStatistics
- ResearchContacts
- ResearchArticles
- Appendix
- List of Figures [Total: 28]
- List of Tables [Total: 337 ]
Acquire the Full In-Plant Logistics Market Report Today
Elevate your strategic decision-making by accessing the comprehensive in-plant logistics market report designed to illuminate critical trends, benchmark leading practices, and uncover actionable insights. Engage with Ketan Rohom, Associate Director, Sales & Marketing at 360i, to secure this authoritative resource and propel your organization ahead of the competition.
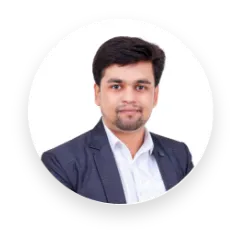
- How big is the Automobile OEM In-plant Logistics Market?
- What is the Automobile OEM In-plant Logistics Market growth?
- When do I get the report?
- In what format does this report get delivered to me?
- How long has 360iResearch been around?
- What if I have a question about your reports?
- Can I share this report with my team?
- Can I use your research in my presentation?