Introduction to the Automotive Bracket Market Landscape
The automotive bracket sector forms a critical backbone within vehicle manufacturing, enabling the secure attachment of components ranging from engine assemblies to passenger safety mechanisms. As global supply chains continue to evolve and vehicle architectures grow more complex, brackets have transitioned from simple fastening elements to precision-engineered parts that influence performance, weight distribution, and safety compliance. This executive summary delivers an insightful overview of the market’s current dynamics, exploring the interplay of regulatory changes, material innovations, and emerging production techniques. It illuminates how these factors converge to redefine product design, sourcing strategies, and competitive positioning. By synthesizing critical market intelligence, this introduction sets the stage for deep-dive analysis, ensuring decision-makers gain a clear understanding of the forces shaping the future of automotive bracket solutions.
Transformative Shifts Redefining Design, Materials, and Production
Recent years have witnessed profound shifts within automotive manufacturing, driven by electrification, autonomous driving development, and stringent environmental regulations. The pivot toward electric vehicles has elevated thermal management demands, prompting bracket designs that integrate cooling channels and withstand higher operating temperatures. Concurrently, lightweighting initiatives have accelerated adoption of advanced composite materials, while digital twin simulations refine load distribution and vibration resistance. Additionally, additive manufacturing has advanced from prototyping to flexible production runs, enabling custom configurations and rapid iteration. The convergence of modular vehicle architectures and over-the-air software updates has compelled OEMs and suppliers to reimagine mounting solutions for sensors, batteries, and wiring harnesses. As a result, bracket suppliers must not only meet traditional durability and safety criteria but also adapt to dynamic production volumes and collaborative design processes. These transformative shifts are reshaping cost structures, time-to-market benchmarks, and competitive differentiation within the bracket ecosystem.
Analyzing the Cumulative Impact of U.S. Tariffs in 2025 on Cost and Supply Chains
The imposition of new United States tariffs in 2025 underscores the geopolitical dimension influencing automotive component sourcing. Tariffs on imported metals and certain advanced composites have elevated input costs for aluminum alloy brackets and glass fiber composites, prompting manufacturers to reassess supply networks. In response, many tier-one suppliers are diversifying procurement by securing authorized distributors and forging direct partnerships with domestic mills. Meanwhile, high-density plastic and engineered plastic compositions, previously cost-competitive, face margin pressures as raw material prices climb. The need to balance compliance with cost optimization has intensified collaboration between quality assurance teams and logistics networks, ensuring that materials align with industry standards without compromising throughput. On the export side, after-market alliances have become invaluable, facilitating smoother cross-border flows through established customs protocols. Ultimately, the cumulative impact of U.S. tariffs in 2025 will be measured not only in adjusted price points but in the strategic realignment of global value chains toward resilience and regional self-reliance.
Key Segmentation Insights Across Applications, Materials, and Manufacturing
Insight into product application reveals critical distinctions among mounting solutions, safety equipment, structural support including heavy load support and light weight support, and thermal management. Each category demands precise engineering and material compatibility. When examining material composition, bracket solutions span composite materials-incorporating carbon composite and glass fiber-metal based options such as aluminum alloy and steel grade, and plastic based parts including engineered plastic and high density plastic, with each subcategory offering unique strength-to-weight profiles. Manufacturing techniques further diversify the market, from additive manufacturing enabling bespoke designs to injection molding, machining processes, and precision casting suited for high-volume runs. End use classification underscores the varied requirements across commercial vehicles, electric vehicles, heavy duty vehicles, and passenger vehicles, each segment imposing distinct loading and environmental constraints. Design attributes such as custom configurations-with adjustable parameters and fit for specific needs-ergonomic design, and modular structure influence both aftermarket adaptability and OEM integration. Performance criteria range from durability testing and load efficiency to thermal resistance and vibration resistance, while industry standards enforcement via compliance verification, quality assurance, and safety certification ensures regulatory alignment. Finally, supply chain integration through after market alliances, logistics networks, and OEM collaboration-leveraging authorized distributors and direct partnerships-governs reliability and speed of delivery.
This comprehensive research report categorizes the Automotive Bracket market into clearly defined segments, providing a detailed analysis of emerging trends and precise revenue forecasts to support strategic decision-making.
- Product Application
- Material Composition
- Manufacturing Technique
- End Use Classification
- Design Attributes
- Performance Criteria
- Industry Standards
- Supply Chain Integration
Key Regional Insights Illustrating Diverse Market Drivers
The Americas region has maintained leadership, driven by strong automotive production in the United States and Mexico, buoyed by nearshoring trends and robust aftermarket networks. Europe, Middle East & Africa exhibits a dynamic duality: western European markets prioritize electrification and lightweight solutions, while emerging economies in the Middle East and Africa invest in reliability and ruggedization for commercial fleets. In the Asia-Pacific, rapid urbanization and government incentives for electric vehicles propel demand for advanced thermal management brackets and modular mounting solutions. Cross-regional logistics networks and strategic OEM collaboration are shaping distribution strategies, with regional regulatory environments influencing material certification processes and safety approval timelines. Collectively, these regional patterns highlight the importance of tailored design strategies, localized manufacturing capabilities, and adaptive supply chain models.
This comprehensive research report examines key regions that drive the evolution of the Automotive Bracket market, offering deep insights into regional trends, growth factors, and industry developments that are influencing market performance.
- Americas
- Asia-Pacific
- Europe, Middle East & Africa
Key Company Insights: Leading Innovators and Strategic Collaborators
Within this competitive landscape, a cohort of leading suppliers drives innovation and market penetration. Aisin Seiki Co., Ltd. has advanced mounting solutions with integrated vibration resistance modules, while Aptiv PLC excels in sensor bracketry for autonomous systems. Autoliv Inc. differentiates through safety equipment brackets designed for rapid deployment across passenger vehicles. Benteler International AG focuses on structural support components, optimizing heavy load support for commercial fleets. BMW AG and Ford Motor Company leverage in-house bracket design to streamline production lines. Brose Fahrzeugteile GmbH & Co. KG integrates modular structures into door and seat mounting frameworks. Continental AG and Delphi Technologies PLC enhance thermal management brackets for high-power electric drivetrains. Daimler AG and General Motors Company collaborate with after market alliances to ensure part availability. Denso Corporation and Mahle GmbH concentrate on high-density plastic and engineered plastic compositions. Eaton Corporation plc and Faurecia S.E. pioneer precision casting and machining processes for lightweight chassis components. Gestamp Automoción, S.A. and Magna International Inc. harness high-strength steel grades for load-bearing supports. Hyundai Mobis Co., Ltd. and Nissan Motor Co., Ltd. develop custom configurations for ergonomic assembly. Johnson Controls International plc and Lear Corporation focus on compliance verification and quality assurance. NSK Ltd. and Robert Bosch GmbH deliver brackets with enhanced thermal resistance. Schaeffler Technologies AG & Co. KG and Sumitomo Electric Industries, Ltd. support direct partnerships with OEMs. Toyota Boshoku Corporation, Valeo SA, Valeo Siemens eAutomotive GmbH, Volkswagen AG, and ZF Friedrichshafen AG round out an ecosystem defined by advanced materials, industry-leading safety certification, and integrated supply chain models.
This comprehensive research report delivers an in-depth overview of the principal market players in the Automotive Bracket market, evaluating their market share, strategic initiatives, and competitive positioning to illuminate the factors shaping the competitive landscape.
- Aisin Seiki Co., Ltd.
- Aptiv PLC
- Autoliv Inc.
- Benteler International AG
- BMW AG
- Brose Fahrzeugteile GmbH & Co. KG
- Continental AG
- Daimler AG
- Delphi Technologies PLC
- Denso Corporation
- Eaton Corporation plc
- Faurecia S.E.
- Ford Motor Company
- General Motors Company
- Gestamp Automoción, S.A.
- Hyundai Mobis Co., Ltd.
- Johnson Controls International plc
- Lear Corporation
- Magna International Inc.
- Mahle GmbH
- Nissan Motor Co., Ltd.
- NSK Ltd.
- Robert Bosch GmbH
- Schaeffler Technologies AG & Co. KG
- Sumitomo Electric Industries, Ltd.
- Toyota Boshoku Corporation
- Valeo SA
- Valeo Siemens eAutomotive GmbH
- Volkswagen AG
- ZF Friedrichshafen AG
Actionable Recommendations for Industry Leaders to Drive Growth and Resilience
To secure competitive advantage, industry leaders must pursue a multifaceted strategy. First, invest in cross-functional R&D that bridges material sciences and digital manufacturing, accelerating the adoption of carbon composite and additive manufacturing for lightweight, high-precision brackets. Second, reinforce supply chain agility by establishing direct partnerships with domestic material suppliers and leveraging authorized distributors to mitigate tariff impact. Third, integrate advanced analytics within logistics networks to forecast component demand and optimize inventory levels across regional hubs. Fourth, align product development with evolving industry standards by embedding compliance verification and safety certification processes early in design sprints. Fifth, cultivate aftermarket alliances in growth regions to capitalize on service revenue streams and bolster brand loyalty. Sixth, differentiate through ergonomic and modular design attributes, enabling rapid customization for electric and autonomous vehicle platforms. Lastly, foster collaborative ecosystems that unite OEMs, suppliers, and end-use providers around shared objectives of sustainability, cost efficiency, and regulatory compliance.
Explore AI-driven insights for the Automotive Bracket market with ResearchAI on our online platform, providing deeper, data-backed market analysis.
Ask ResearchAI anything
World's First Innovative Al for Market Research
Conclusion: Navigating Complexity with Innovation and Strategic Alignment
In conclusion, the automotive bracket market stands at a pivotal juncture where material innovation, regulatory shifts, and evolving vehicle architectures converge. Success will hinge on suppliers’ ability to navigate tariff-induced cost pressures, harness advanced manufacturing techniques, and embed stringent quality assurance protocols from concept through certification. By leveraging regional strengths, strategic partnerships, and data-driven supply chain management, organizations can transform challenges into opportunities for differentiation and long-term value creation. The insights detailed herein offer a roadmap for decision-makers seeking to optimize their product portfolios, reinforce operational resilience, and maintain competitive leadership in an increasingly complex market environment.
This section provides a structured overview of the report, outlining key chapters and topics covered for easy reference in our Automotive Bracket market comprehensive research report.
- Preface
- Research Methodology
- Executive Summary
- Market Overview
- Market Dynamics
- Market Insights
- Cumulative Impact of United States Tariffs 2025
- Automotive Bracket Market, by Product Application
- Automotive Bracket Market, by Material Composition
- Automotive Bracket Market, by Manufacturing Technique
- Automotive Bracket Market, by End Use Classification
- Automotive Bracket Market, by Design Attributes
- Automotive Bracket Market, by Performance Criteria
- Automotive Bracket Market, by Industry Standards
- Automotive Bracket Market, by Supply Chain Integration
- Americas Automotive Bracket Market
- Asia-Pacific Automotive Bracket Market
- Europe, Middle East & Africa Automotive Bracket Market
- Competitive Landscape
- ResearchAI
- ResearchStatistics
- ResearchContacts
- ResearchArticles
- Appendix
- List of Figures [Total: 32]
- List of Tables [Total: 639 ]
Call to Action: Engage with Ketan Rohom for Customized Market Intelligence
For decision-makers ready to delve deeper into these insights and access comprehensive market analysis, contact Ketan Rohom, Associate Director, Sales & Marketing. He will guide you through tailored research packages, address your specific needs, and facilitate procurement of the full market research report to support your strategic planning and execution efforts.
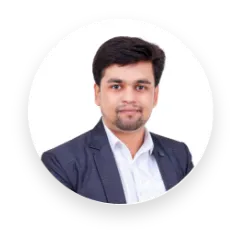
- When do I get the report?
- In what format does this report get delivered to me?
- How long has 360iResearch been around?
- What if I have a question about your reports?
- Can I share this report with my team?
- Can I use your research in my presentation?